A checkweigher system is a precision tool used on high-speed production lines to verify product weight accuracy. It dynamically weighs items using conveyor belts and strain-gauge load cells, converting force into electrical signals. The control unit compares these measurements against preset tolerances, classifying products as underweight, acceptable, or overweight. Non-compliant items are rejected via mechanisms like pneumatic pushers. Real-time data aids process optimization. Exploring further unveils deeper insights into its diverse applications and benefits.
Key Takeaways
- A checkweigher system ensures product weight consistency on production lines through dynamic weighing.
- It compares weights to preset tolerances for quality and compliance.
- Products are classified as underweight, acceptable, or overweight using conveyor-based load cells.
- Non-compliant items are removed via rejection mechanisms like pushers or air jets.
- Real-time data from checkweighers optimizes processes and enhances efficiency.
Understanding Checkweigher Systems
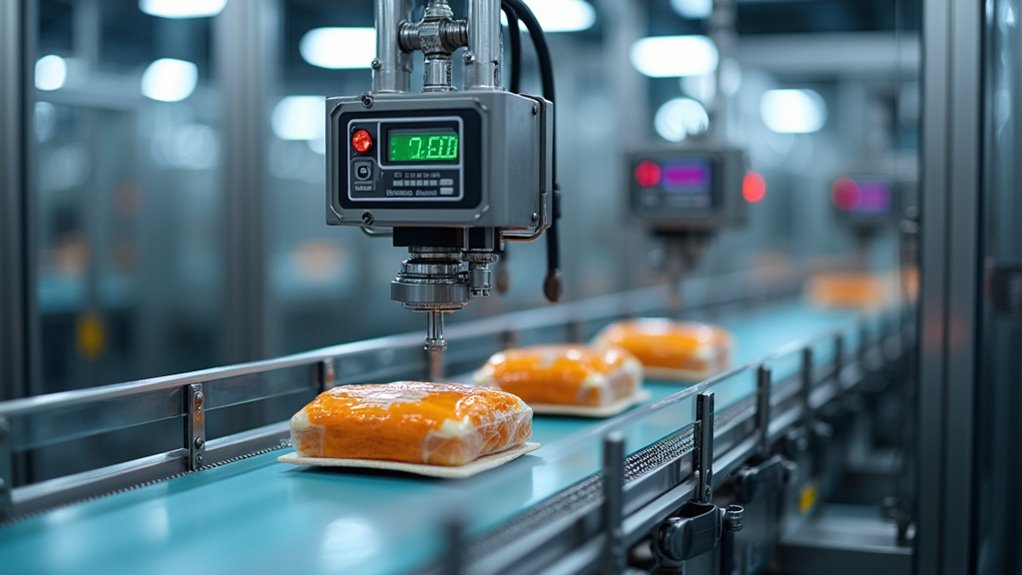
How do manufacturers ensure consistent product weight on high-speed production lines? They rely on checkweigher systems, automated machines designed for dynamic weighing of products as they move along conveyors. These systems compare measured weights against pre-set tolerances stored in memory, ensuring compliance with quality and regulatory standards. By classifying items into zones such as underweight, acceptable, or overweight, they maintain uniformity and minimize product giveaway or underfilling risks.
The evolution history of checkweighers traces back to manual scales, progressing to sophisticated, high-speed systems with advanced data processing for process optimization. They play a critical role in industries like food and pharmaceuticals, supporting legal net content requirements and traceability through detailed weight records. Additionally, checkweighers enhance productivity by automating the weighing process at high speeds, reducing manual errors. automating the weighing process
Looking at future trends, advancements in automation and data analytics are expected to enhance precision and integration, driving efficiency and predictive maintenance in production environments with minimal human intervention.
Core Components of a Checkweigher
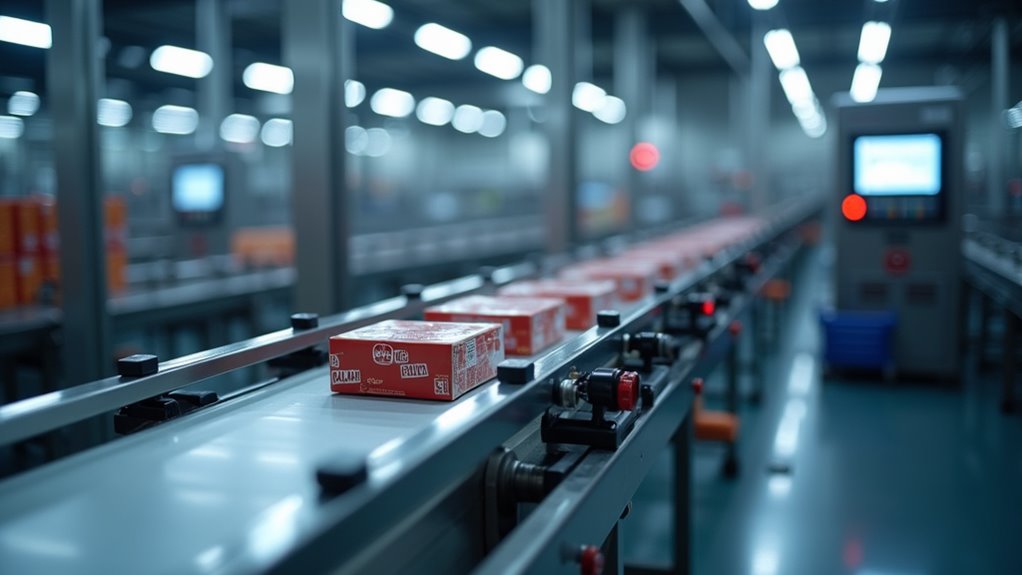
Building on the broader understanding of checkweigher systems, attention now shifts to the fundamental elements that enable their functionality. A checkweigher comprises several critical components, starting with the conveyor system, which includes infeed, weigh, and outfeed/reject belts, designed to ensure precise spacing and minimal interference. The weighing element, typically a strain-gauge load cell, converts force into electrical signals with high sensitivity, demanding robust protection. The rejection mechanism, such as pneumatic pushers or air jets, efficiently removes non-conforming items based on predefined tolerances.
The control unit, equipped with an HMI, processes data and manages operations, while the frame provides structural integrity tailored to environmental demands. To maintain accuracy, Component Upgrades, such as advanced load cells, enhance performance, and adherence to strict Maintenance Schedules prevents downtime and ensures reliability. These core elements collectively underpin the precision and efficiency of checkweigher systems in industrial applications.
How Checkweighers Function in Production
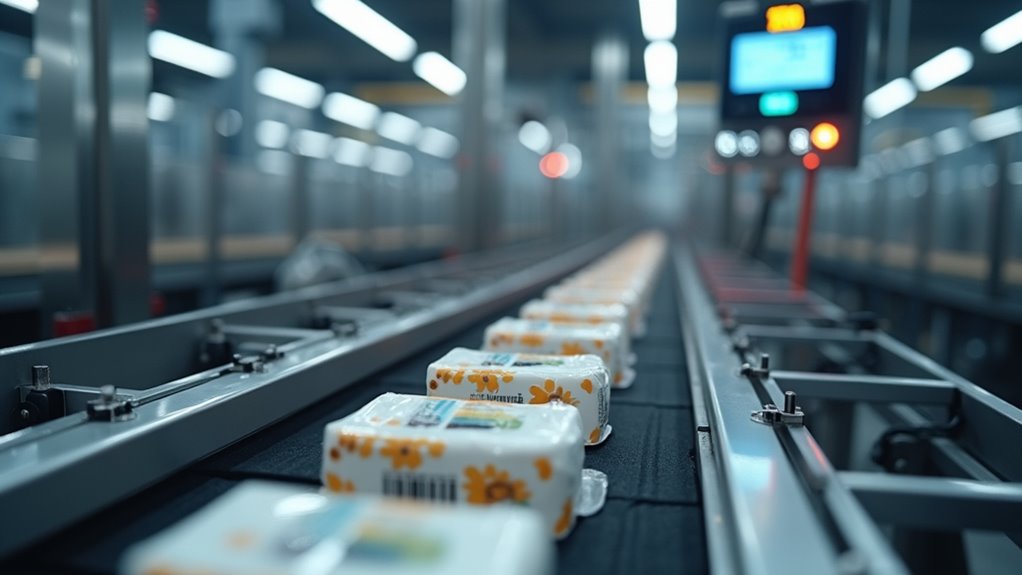
Why are checkweighers indispensable in modern production lines? These precision systems ensure product weight compliance by seamlessly integrating at critical stages like pre-production, packaging, or end-of-line. Positioned adjacent to equipment such as fillers and labelers, they weigh 100% of items in motion via conveyors and load cells, converting weight into electrical signals for analysis. The controller compares these against preset targets, classifying items as underweight, acceptable, or overweight, and triggers rejection mechanisms for non-compliant products using pushers or air blasts.
Beyond quality control, checkweighers enhance Safety Measures by preventing hazardous overfills or underfills that could compromise product integrity. They also contribute to Energy Efficiency by providing real-time data for process optimization, enabling feedback to upstream equipment for automatic adjustments, reducing waste, and minimizing energy use. Through detailed data collection on weights and rejects, they support analytical insights, ensuring only compliant products advance in production flows.
Different Types of Checkweigher Equipment
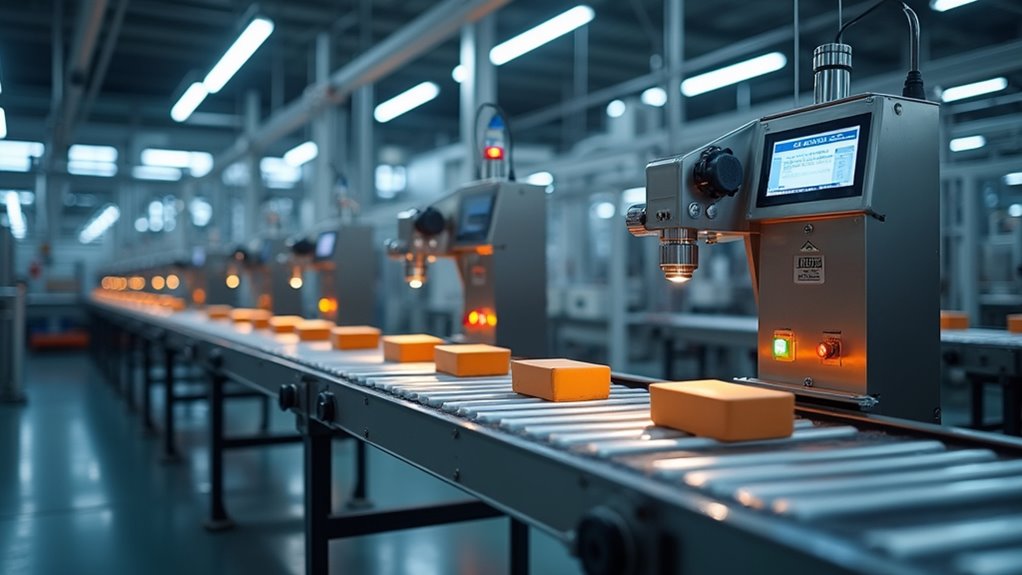
Various types of checkweigher equipment cater to diverse production needs, ensuring precision and compliance across industries. In a Types Comparison, static checkweighers, used for manual weighing of stationary items like raw meats, contrast with in-motion checkweighers, which dynamically weigh products on conveyor lines at high speeds, often exceeding 500 items per minute. Multi-head checkweighers, with multiple scoops, enable rapid target weight assembly in automated setups.
In a Variants Exploration, combination checkweighers integrate with metal detectors or X-ray systems for comprehensive quality control, saving space. Specialized checkweighers, tailored for harsh environments or specific tasks like pharmaceutical or heavy-load weighing, offer features such as multi-lane processing and real-time data monitoring via Statistical Process Control. Each type addresses unique operational demands, from manual spot-checking to high-speed automation, ensuring accurate weight verification and adherence to stringent industry standards across diverse production environments.
Key Benefits and Applications of Checkweighers
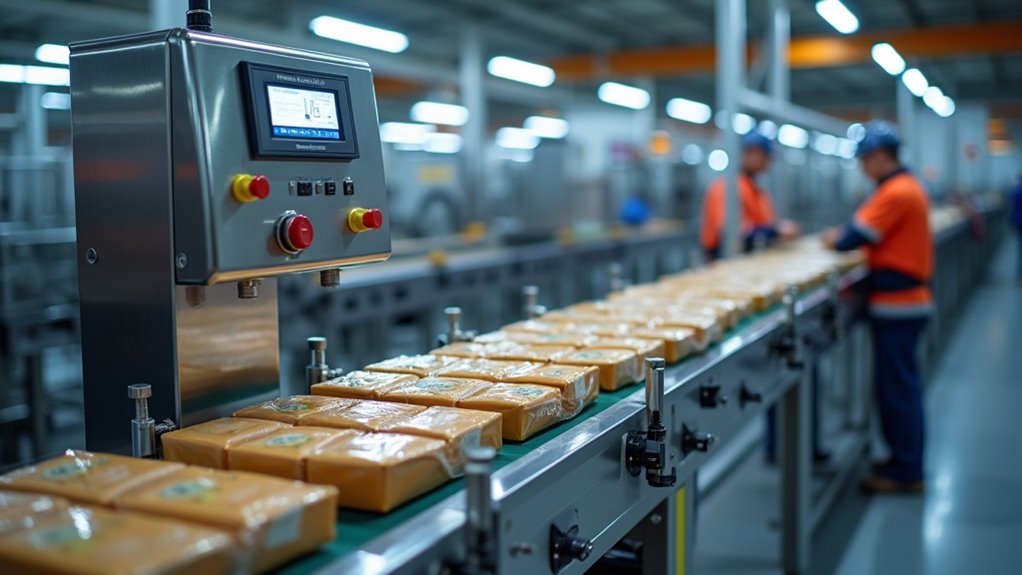
Checkweighers play a critical role in modern production environments by delivering precise weight verification and ensuring operational excellence. These systems enhance quality control by detecting weight deviations, rejecting non-conforming products, and maintaining consistency, thus safeguarding brand reputation. They boost efficiency through automation, achieving high-speed weighing up to 350 ppm, minimizing labor needs, and optimizing throughput. Significant Cost Benefits arise from reducing product giveaway, minimizing waste, and avoiding fines for regulatory non-compliance with standards like FDA or OIML, while also cutting rework expenses.
From an Application Insights perspective, checkweighers serve diverse industries. In food and beverage, they ensure accurate portioning; in pharmaceuticals, they verify dosages for safety; and in logistics, they confirm shipping weights. Their versatility extends to automotive and cosmetics, supporting quality control and compliance. By integrating precision and adaptability, checkweighers remain indispensable for maintaining standards across varied production landscapes.