Investing in flat bottle labeling machines enhances production efficiency and output capacity, ensuring precise label placement to boost brand consistency. These machines offer versatile labeling options, reduce labor costs, and minimize product waste. Seamless integration with existing production lines enhances product aesthetics. Adopting this technology leads to significant operational improvements, hinting at even greater benefits within reach.
Key Takeaways
- Enhanced production efficiency with high-speed labeling technology, handling up to 500 products per minute.
- Improved brand consistency through precise label placement and advanced alignment technology.
- Cost-effective operations and reduced labor costs due to automation and minimal manual intervention.
- Versatile labeling options, including wrap-around and corner labels, supporting diverse packaging needs.
- Seamless integration with existing production lines, enhancing workflow efficiency and productivity.
Enhanced Production Efficiency
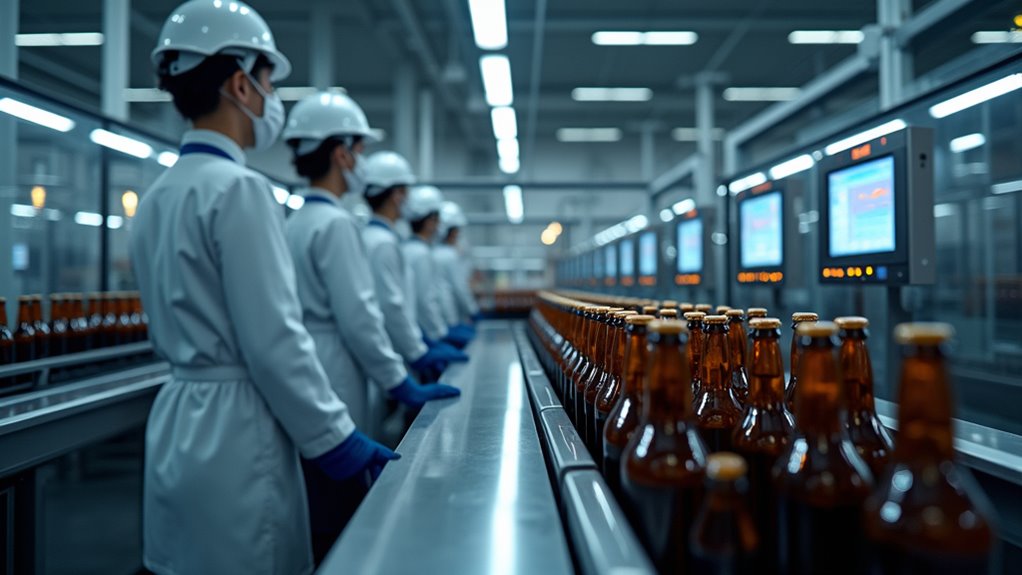
As the demand for efficient production processes grows, flat bottle labeling machines have become critical assets in enhancing production efficiency.
These automated systems offer significant advancements in quality assurance and operational scalability. By integrating with existing production lines, these machines facilitate smoother, more continuous workflows, reducing production time and accelerating inventory turnover. Additionally, many systems, such as the Krones Modular Labeler, leverage AI and IoT technology to enhance labeling processes.
High-speed capabilities, some reaching up to 500 products per minute, combined with minimal downtime for changeovers, enable businesses to meet rising consumer demand and shorten production cycles. This scalability is crucial for industries facing fluctuating market demands.
High-speed labeling machines, handling up to 500 products per minute with minimal changeover downtime, enable businesses to meet rising consumer demand and adapt to fluctuating market needs.
Thus, flat bottle labeling machines are indispensable for companies seeking to maintain a competitive edge in today’s fast-paced market environment.
Precise Label Placement
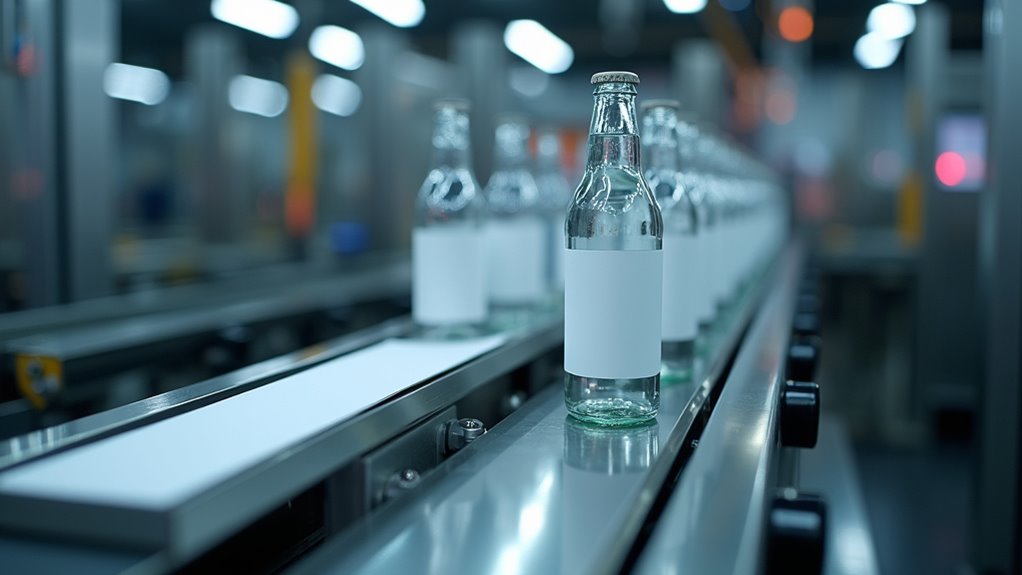
Accurate label placement is a critical factor in the packaging industry, significantly impacting both brand perception and regulatory compliance.
Modern flat bottle labeling machines utilize advanced label alignment technology to ensure each label is applied with the highest precision. These systems adhere strictly to label accuracy standards, preventing costly errors and maintaining consistency across all products.
The use of servo-controlled applicators, synchronized conveyors, and sensor-based inspection systems allows these machines to handle various bottle sizes and label dimensions while achieving precise placement every time. Such accuracy is vital for building consumer trust, differentiating products on shelves, and avoiding regulatory issues. Additionally, these machines enhance efficiency akin to automation in warehouse management systems, significantly reducing labor costs and minimizing human error.
Increased Output Capacity
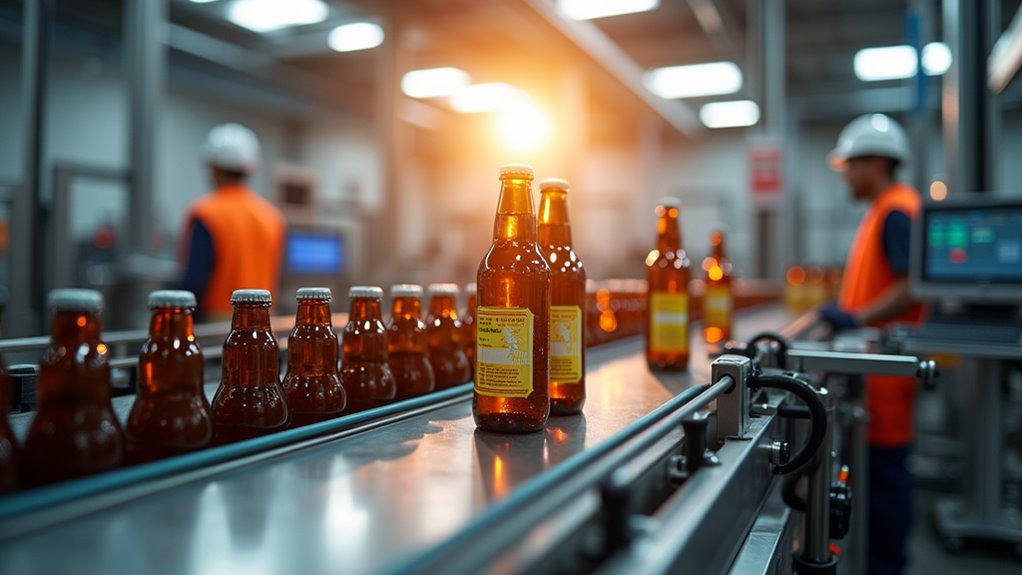
Flat bottle labeling machines significantly increase output capacity through high-speed labeling capabilities, with some models handling up to 300 bottles per minute. These systems minimize downtime between production runs with quick-change features and robust construction, ensuring continuous operation. Additionally, they often include high-capacity systems designed to maintain accuracy and efficiency even in demanding production environments.
High-Speed Labeling
High-speed labeling machines significantly boost production output by automating the labeling process, resulting in increased capacity for businesses. Utilizing advanced labeling technology and automation trends, these machines can label up to 300 bottles per minute, a key advantage for high-volume industries like pharmaceuticals and cosmetics. The integration of servo-controlled systems and high-precision sensors ensures accurate label placement at high speeds, significantly reducing errors and rework. This automation efficiency not only meets growing market demands but also enables scalable production, making these machines indispensable in modern manufacturing environments.
Feature | Benefit |
---|---|
Servo-Controlled Systems | Fast, precise application |
Advanced Sensors | Compensates for label misalignment |
Automatic Feeding | Efficient bottle handling |
Minimal Downtime
Minimal downtime is a key advantage of advanced flat bottle labeling machines, directly contributing to increased output capacity. These machines incorporate automated control systems such as automatic label length detection and synchronized speed control, eliminating the need for manual input and ensuring consistent label placement.
Real-time monitoring enables machines to perform automatic adjustments, maintaining optimal performance and reducing the likelihood of downtime due to inconsistencies. Additionally, features like quick-adjustment wheels, minimal changeover components, and recipe storage in HMIs facilitate rapid changeovers between product runs, minimizing unproductive time.
The robust mechanical construction of these machines also enhances reliability, ensuring fewer maintenance-related interruptions. Through efficient monitoring and automatic adjustments, these systems significantly improve productivity by keeping production lines running smoothly and consistently.
Increased Throughput
Automated flat bottle labeling machines significantly enhance throughput, a critical factor in meeting the demands of high-volume production environments. This capacity increase is achieved through several key features:
- High-Speed Application: Machines can label up to 300 bottles per minute, depending on size, without compromising accuracy, thanks to advanced servo systems ensuring precise label placement even at high speeds.
- Automated Labeling Process: Eliminating manual labor not only speeds up production but also minimizes errors. Automated feeding and labeling systems position and process bottles in sequence, enhancing bottle stability and enabling continuous flow.
- Integration and Synchronization: Seamless integration with other packaging equipment and synchronized conveyor speeds stabilize bottles during labeling, allowing for higher operational speeds. This streamlined process eliminates bottlenecks, ensuring a more efficient production line.
Cost-Effective Operations
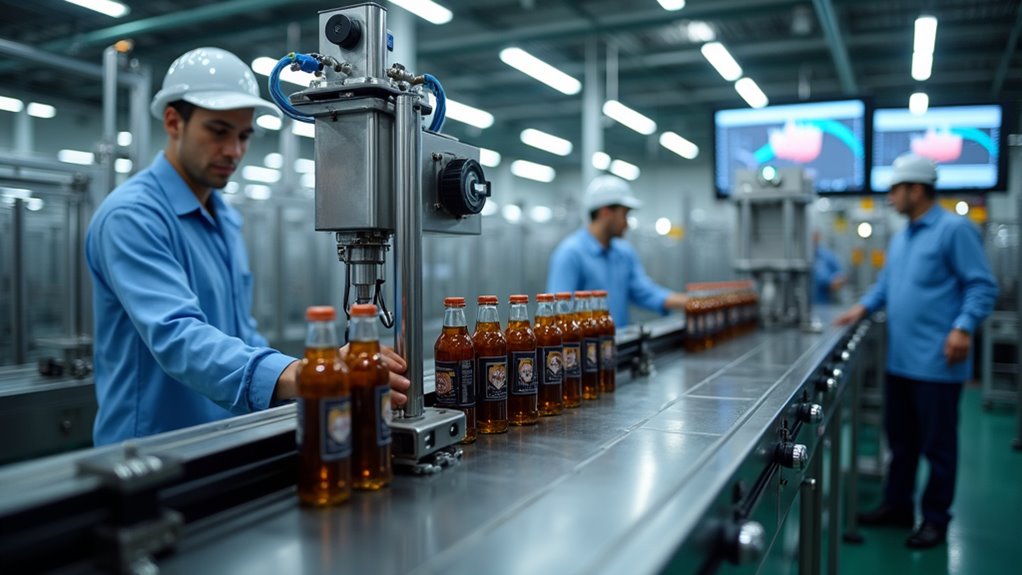
Investing in flat bottle labeling machines offers opportunities for cost-effective operations, a critical aspect for businesses aiming to optimize their production processes. These machines not only reduce labor costs but also enhance production sustainability. Automating the labeling process significantly reduces the need for manual labor, thereby lowering costs related to wages, training, and human error. Moreover, the high-speed labeling capabilities of these machines increase operational efficiency, ensuring production targets are met without compromising quality. Additionally, features like advanced IoT integration enable improved compliance and accuracy in labeling operations.
Benefit | Impact |
---|---|
Reduced Labor Costs | Lower wage and training expenses |
Increased Efficiency | Higher production output |
Minimized Material Waste | Reduced material costs |
Long-Term ROI | Increased profitability over time |
Lower Operating Costs | Reduced energy and maintenance expenses |
Versatile Labeling Options
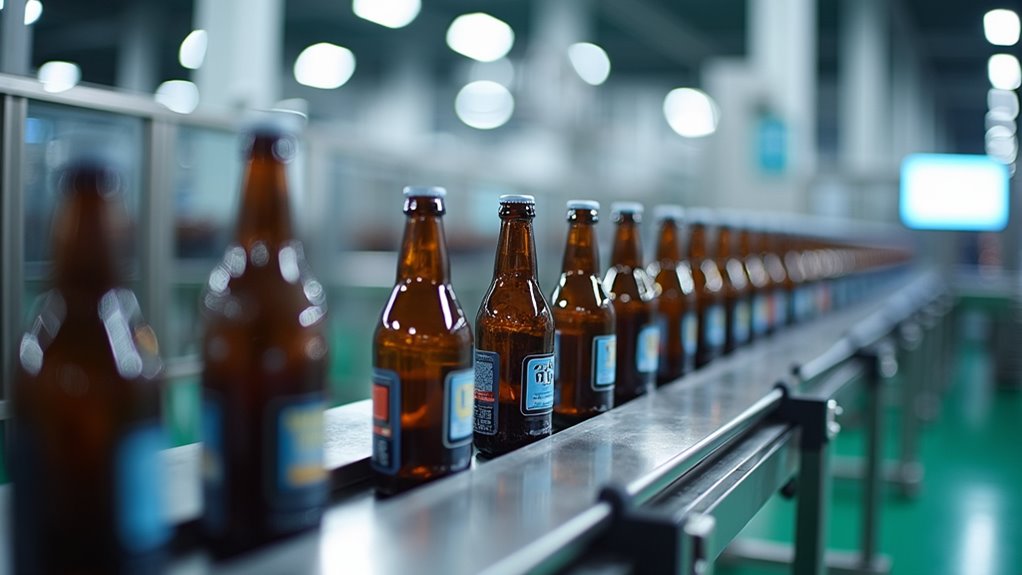
Flat bottle labeling machines offer a wide range of versatile labeling options, making them essential assets for businesses seeking to diversify their product presentation. These machines encompass various labeling techniques and application methods to meet specific packaging requirements.
Versatile in their options, flat bottle labeling machines are critical for businesses aiming to diversify product presentation, meeting a wide range of packaging requirements with precision and flexibility.
- Diverse Label Application Methods: From single-side to wrap-around and corner labeling, these machines ensure precise label placement across various container shapes and sizes.
- Compatibility with Multiple Bottle Types: They are designed to handle not only flat-sided bottles but also oval and round bottles, offering flexibility in product packaging options.
- Flexible Material and Label Size Handling: With the ability to work with various materials and label sizes, these machines provide extensive customization options for brand display and product information.
Improved Brand Consistency
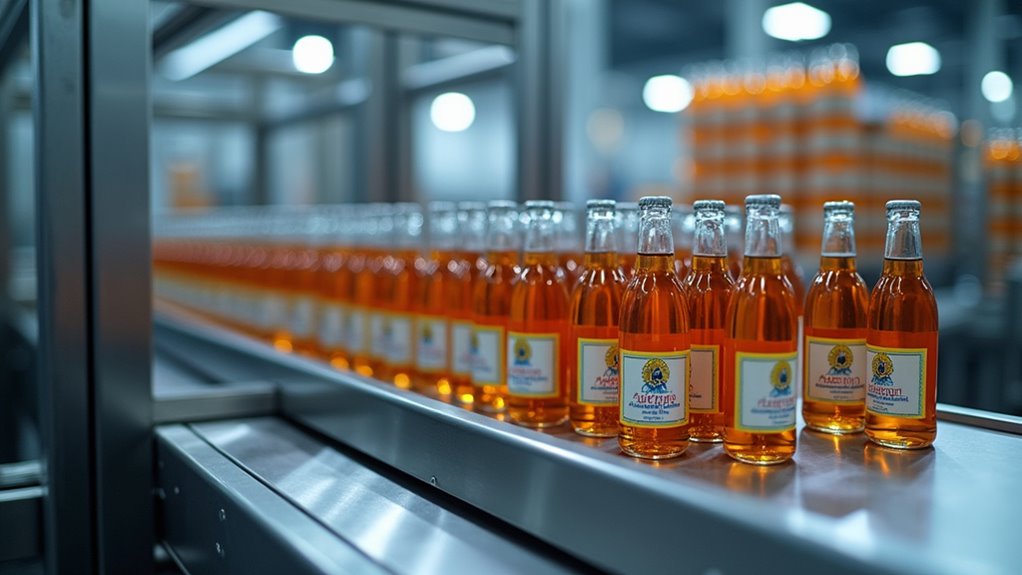
Accurate labeling is crucial for maintaining brand consistency, and flat bottle labeling machines ensure this with unparalleled precision.
These machines guarantee that each label is placed correctly on every bottle, reinforcing brand recognition and making it instantly recognizable to consumers. Equipped with advanced technology like sensors and programmable settings, they minimize errors and ensure flawless label placement, contributing to a professional appearance that reflects quality and attention to detail.
Consistency in labeling not only builds consumer trust but also fosters loyalty, as customers are more likely to repurchase from a brand that presents a reliable and cohesive image.
Reduced Labor Costs
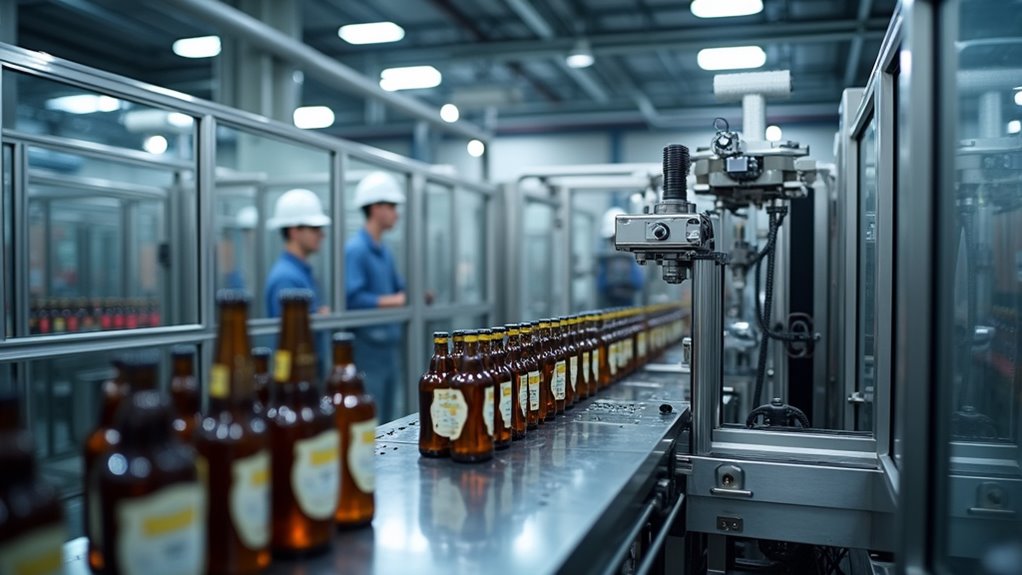
Although the initial investment in flat bottle labeling machines may seem substantial, the significant reduction in labor costs quickly justifies this expense.
By automating the labeling process, these machines provide:
- Labor Optimization: Eliminating the need for manual labeling allows for a reduced workforce, directly lowering wage costs.
- Flexible Staff Allocation: Employees can be reassigned from repetitive labeling tasks to higher-value activities, enhancing overall operational efficiency.
- Minimized Human Intervention: With the ability to operate with minimal supervision, these machines reduce costs associated with labor-intensive tasks and management.
Integrating flat bottle labeling machines not only simplifies the production process but also delivers substantial savings in labor-related costs, providing a compelling return on investment.
Minimized Product Waste
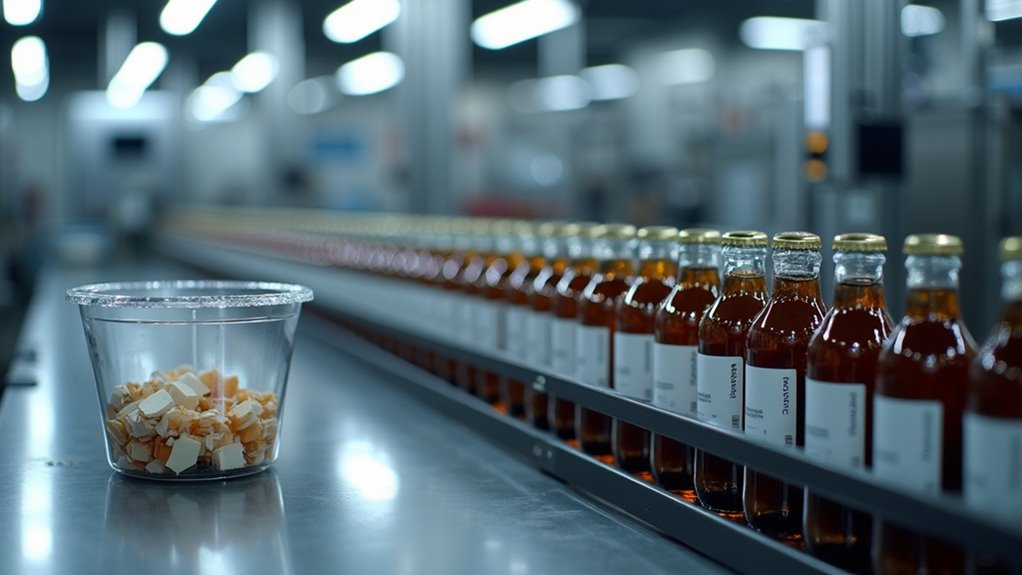
Beyond labor-related advantages, flat bottle labeling machines significantly contribute to minimizing product waste. These machines ensure precise label placement, reducing errors such as misaligned or wrinkled labels, which are common in manual operations.
This accuracy, coupled with automated verification processes, significantly lowers the likelihood of mislabeling or errors, thereby avoiding the need to discard otherwise viable products. Furthermore, the integration of vision inspection systems enables real-time quality assurance, detecting and rejecting defective labeled products before they reach the market.
Sustainable practices in labeling operations not only enhance brand integrity but also significantly reduce material waste and support lean manufacturing principles.
Seamless Integration with Existing Lines
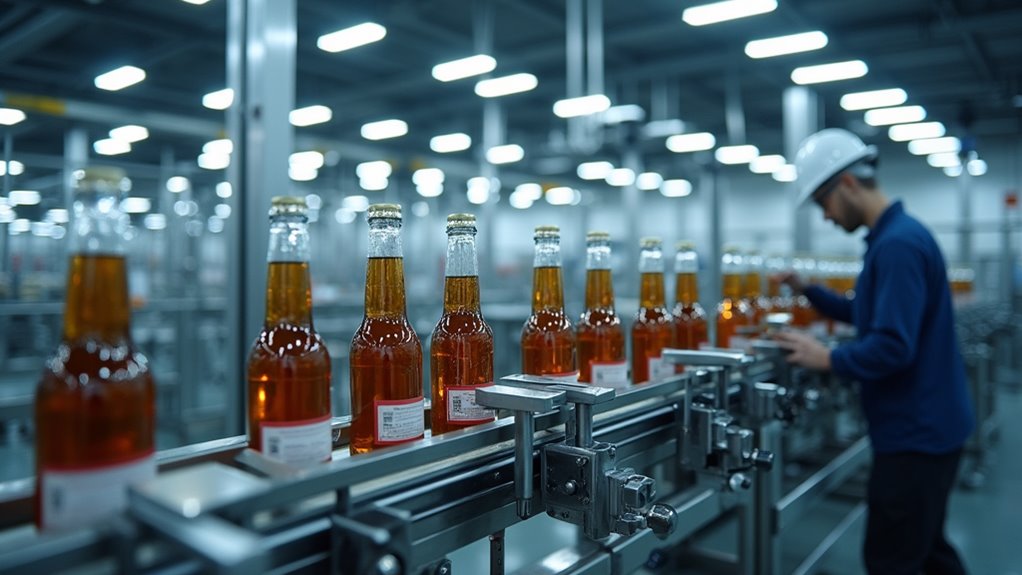
Flat bottle labeling machines offer seamless integration into existing production lines, enhancing operational efficiency and productivity.
These machines are equipped with advanced features that ensure:
- Streamlined Workflow: They are designed to synchronize easily with other automated machinery like filling and capping machines, establishing a continuous and efficient packaging process.
- Flexible Configuration: With modular designs, they offer setup flexibility and allow the addition of modules as production needs expand, minimizing the need for multiple machines.
- Automation Features: Equipped with intuitive touchscreen control panels and PLC systems, these machines enable easy adjustment of various operational parameters, allowing quick and consistent setup for different products.
Enhanced Product Aesthetics
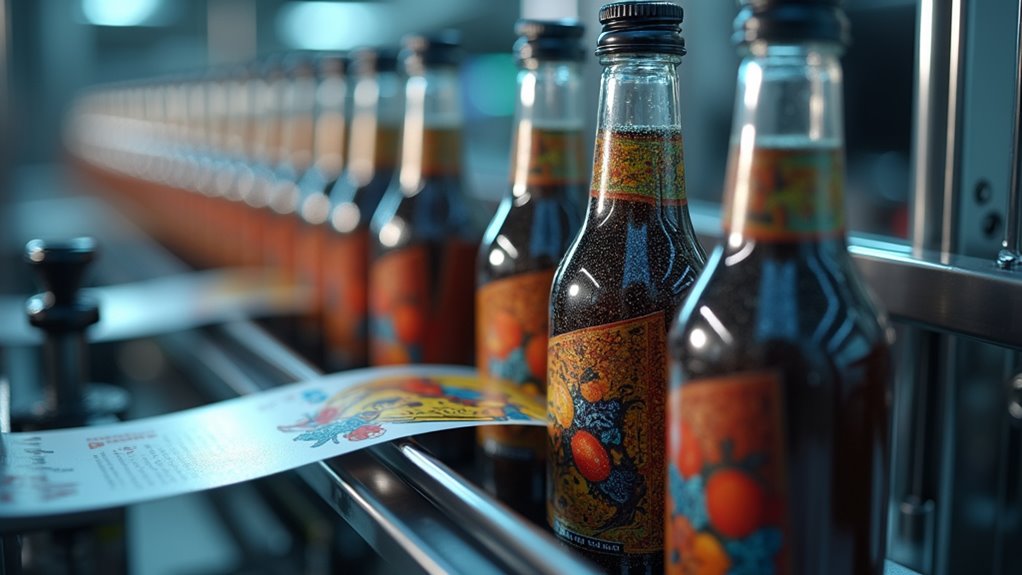
In the competitive packaging industry, enhanced product aesthetics is a critical factor, and flat bottle labeling machines play a pivotal role in achieving this goal.
These machines ensure flawless label application, eliminating wrinkles, bubbles, and misalignment that detract from a professional appearance.
Flawless label application, free of wrinkles, bubbles, and misalignment, is essential for a professional appearance.
Precise placement and advanced sensor technology maintain consistent and uniform labeling, crucial for cohesive brand identity.
The ability to handle various label materials and designs, including intricate shapes and premium finishes, enables enhanced design freedom.
This freedom is vital for leveraging color psychology in label design, ultimately boosting brand recognition and shelf appeal.