A checkweigher conveyor is an industrial device designed to verify the weight of packaged goods during high-speed production. It operates by transporting items on an infeed belt for proper spacing, then onto a weigh belt where load cell sensors capture precise weight data. The system compares weights against preset tolerances, rejecting non-compliant items via mechanisms like pushers. Controllers ensure real-time monitoring. Explore further to uncover deeper insights into its advanced applications and benefits.
Key Takeaways
- A checkweigher conveyor is an industrial device that verifies the weight of packaged goods during production.
- It weighs items in motion, achieving speeds over 500 items per minute for efficiency.
- Products pass over a weigh belt with load cells to capture precise weight data.
- The system compares weights to preset tolerances, rejecting non-compliant items via mechanisms like pushers.
- It ensures accuracy and compliance in industries like food, pharmaceuticals, and logistics.
Understanding the Basics of a Checkweigher Conveyor
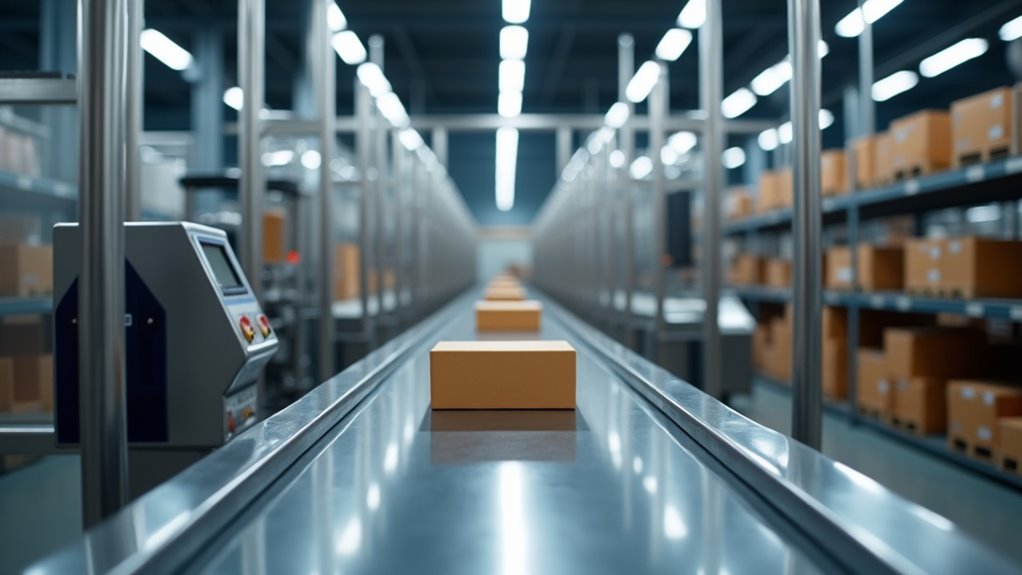
While modern production lines demand precision and efficiency, a checkweigher conveyor serves as a critical industrial measuring device designed to verify the weight of packaged commodities. Positioned typically at the end of packaging lines, this automated system, also termed a belt weigher or dynamic scale, ensures products meet specified weight tolerances without manual intervention. It weighs items in motion, comparing results against preset ranges, and either accepts or rejects based on compliance, achieving speeds exceeding 500 items per minute. Additionally, these systems are designed to handle a wide variety of container types and package designs, ensuring accurate product delivery across diverse industries.
In the Historical Context, checkweigher conveyors evolved from manual weighing practices to sophisticated inline systems, driven by industrial automation needs since the mid-20th century. Their development reflects a shift toward precision in quality control. Looking at Innovation Prospects, advancements in sensor technology and data analytics promise enhanced accuracy and integration with smart manufacturing systems, paving the way for even greater efficiency and reliability in future production environments.
Key Components and Their Functions
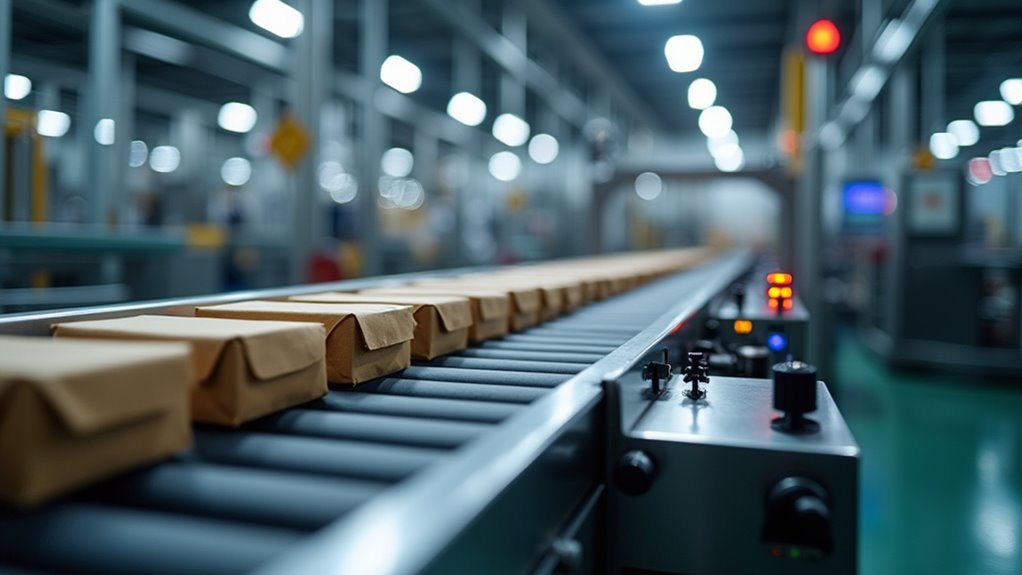
A checkweigher conveyor relies on a sophisticated assembly of components, each engineered to perform specific functions that ensure accurate weight verification and seamless operation. The conveyor frame, often constructed from stainless steel or anodized aluminum, provides essential Frame Stability, supporting belts, rollers, and motors under dynamic loads. The infeed belt manages product spacing, while the weigh belt, mounted on a load cell, captures precise weight data. This load cell, critical for Cell Accuracy, converts force into electrical signals, with high-precision options like electromagnetic force compensation offering superior results over standard strain-gauge types.
Additionally, the rejection system identifies and diverts out-of-tolerance items using mechanisms like pushers or air blasts, maintaining quality control. The control system, paired with an HMI, processes weight data and allows parameter adjustments. Drive mechanisms, including motors and rollers, ensure consistent belt movement, collectively enabling the checkweigher conveyor to uphold stringent industrial standards.
Operational Process and Workflow
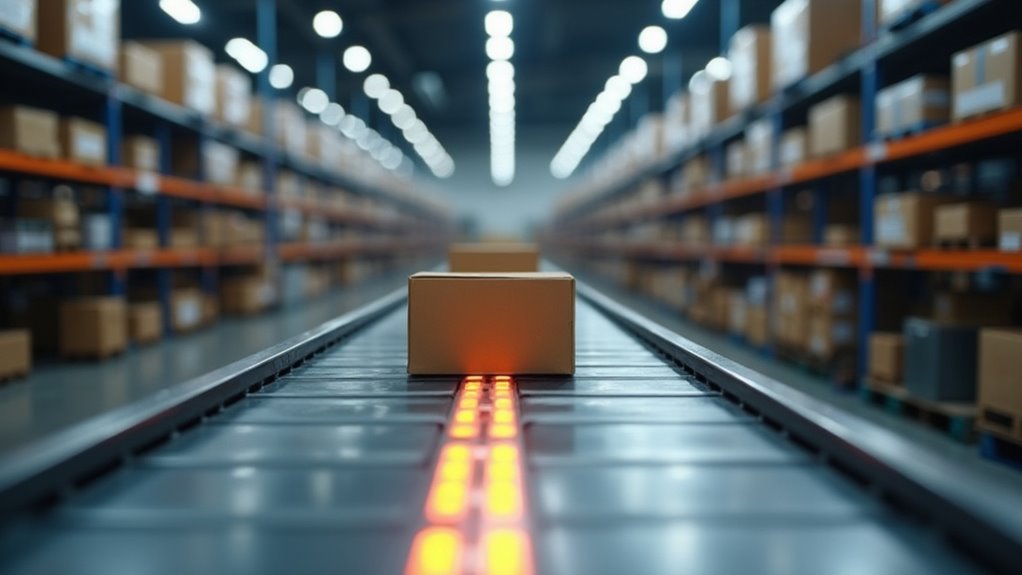
The operational process of a checkweigher conveyor unfolds through a meticulously coordinated sequence of stages designed to ensure precise weight verification and efficient workflow. Initially, products enter via an infeed conveyor, where speed adjustments and acceleration sections maintain proper spacing for individual weighing. Photoelectric sensors detect entry to the weighing platform, enabling dynamic weight measurement via load cell sensors. These sensors convert deformation into electrical signals, processed by a controller for accurate weight determination.
Subsequently, the system compares measured weights against preset tolerances, classifying products as acceptable or non-compliant. Workflow Integration ensures seamless transition from weighing to sorting, where reject mechanisms like pushers or air blasts divert unqualified items. Process Monitoring is critical, with controllers and visual indicators providing real-time feedback on weight classifications. This systematic approach, completed in seconds per product, guarantees precision and efficiency in high-speed production environments through rigorous coordination of each operational phase.
Benefits and Applications Across Industries
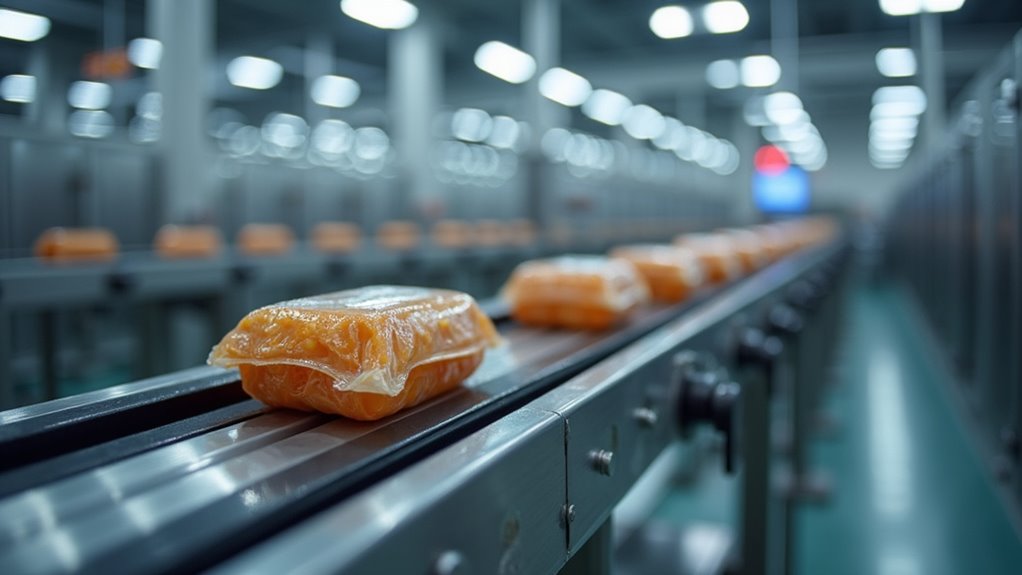
Numerous industries rely on checkweigher conveyors to deliver critical advantages in quality assurance and operational efficiency. These systems ensure product weight accuracy, uphold compliance with Global Regulations such as MID and USDA/FSIS, and enhance productivity by automating inspections. They also offer Sustainability Benefits by minimizing overfilling and reducing material waste, aligning with eco-conscious manufacturing goals. Their precision supports diverse sectors, from food and beverage to pharmaceuticals, ensuring safety and consistency.
Applications are vast, as illustrated by these scenarios:
- Food Industry: Verifying package weights for ready meals to prevent customer complaints.
- Pharmaceuticals: Ensuring dosage accuracy in pill packaging for patient safety.
- Logistics: Confirming shipment weights to meet regulatory and client standards.
- Consumer Goods: Maintaining fill level consistency in cosmetics for brand trust.