For businesses seeking the best food labeling machines in 2025, top picks include the Sirius MK6 for high-speed precision at 300 products per minute, the budget-friendly Sirius 100 with easy changeovers, and the versatile RF150 for shrink sleeve labeling. Security-focused DF100 offers tamper-evident solutions, while Herma systems excel in premium self-adhesive automation. Manual models suit small operations, and quick-integration machines boost efficiency. Explore further to uncover detailed insights on optimizing your production line.
Key Takeaways
- Advanced automated labeling machines offer IoT integration and AI-driven quality control for enhanced compliance and accuracy.
- Modular solutions provide scalable designs and interchangeable applicators for adapting to various container shapes.
- Sirius MK6 delivers high-speed precision, labeling up to 300 products per minute with versatile configurations.
- Cost-effective Sirius 100 features tool-free changeovers and durable stainless steel frames for easy maintenance.
- Specialized systems like RF150 handle shrink sleeve labeling for diverse shapes at 250 products per minute.
Top Pick: Sirius MK6 for High-Speed Precision
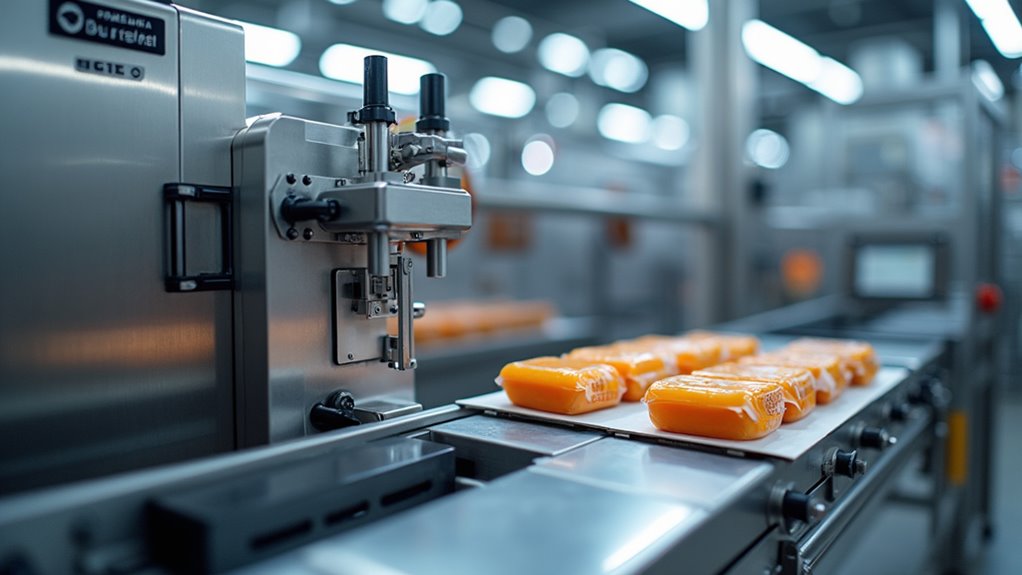
The Sirius MK6 stands out as a premier choice for high-speed precision in food labeling, boasting an impressive capability to handle up to 300 products per minute, depending on label and product dimensions. Its advanced applicators, compatible with Comet series, ensure precise label placement across diverse configurations like front, back, and wrap labeling. This machine supports Label Durability through consistent application, vital for food industry standards, even under high-volume demands.
Engineered for robustness, the Sirius MK6 features a compact, heavy-duty design that integrates seamlessly into existing production lines. Its smart HMI interface, with self-diagnostic alerts and remote monitoring, simplifies Machine Calibration for optimal performance. Tool-free adjustments enable rapid changeovers, minimizing downtime, while preventive maintenance alerts ensure reliability. With a label width range of 0.4 mm to 305 mm, it offers unmatched versatility for pharmaceuticals, food, and industrial packaging, meeting stringent precision requirements efficiently. Additionally, its worldwide support network ensures reliable ongoing assistance for businesses globally.
Budget-Friendly Choice: Sirius 100 With Easy Changeovers
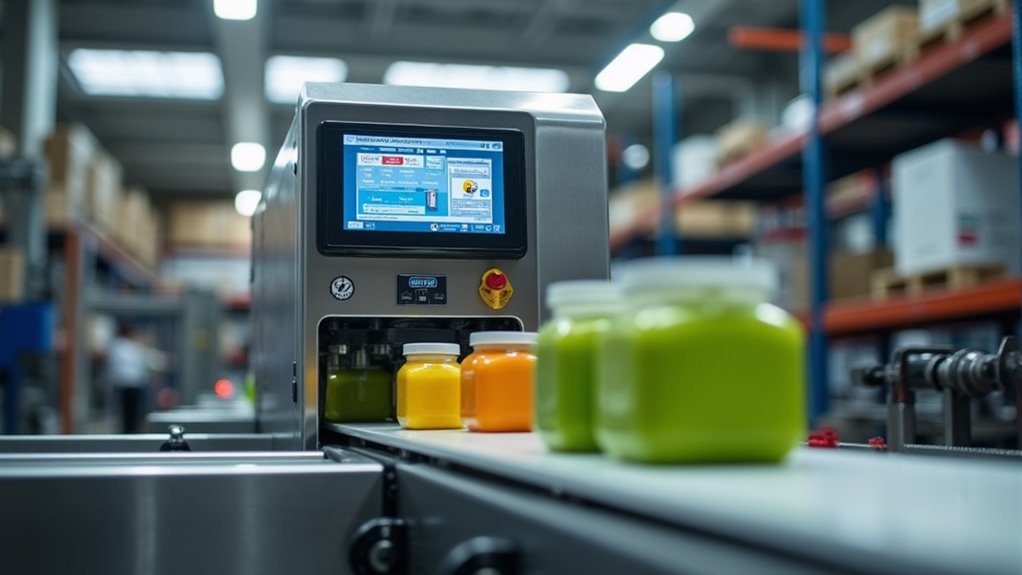
The Sirius 100 emerges as an affordable labeling solution within the food industry, offering cost efficiency through its customizable single or twin-head options and high-speed technology. Its design prioritizes swift setup adjustments with toolless changeovers, significantly reducing downtime during production shifts. This system ensures operational continuity while maintaining precision, making it a practical choice for budget-conscious manufacturers.
Affordable Labeling Solution
While navigating budget constraints in food labeling, manufacturers can find a reliable solution in the Sirius 100, a cost-effective machine designed for efficiency and easy changeovers. Its rugged stainless steel frame ensures product durability, while flexible handling supports material compatibility across diverse food, pharmaceutical, and personal care items. Servo-driven axes enhance precision, minimizing waste.
Key features are highlighted below:
Feature | Benefit |
---|---|
Single/Twin-Head Options | Affordable scalability |
Modular Design | Integrates with existing lines |
Energy-Efficient Servos | Reduces power consumption |
This machine’s compact footprint and reduced tooling lower operational costs, making it ideal for budget-conscious businesses. With compliance to industry standards and support for specialty containers, the Sirius 100 delivers value without compromising quality or performance.
Swift Setup Adjustments
How can food manufacturers achieve rapid production shifts without sacrificing efficiency? The Sirius 100, a budget-friendly choice, offers swift setup adjustments with its toolless changeover system, minimizing downtime and material waste. This enhances production efficiency while maintaining profit margins through rapid batch changes, ideal for contract packaging. Its precision servo technology ensures consistent labeling accuracy across varied product sizes, supporting front, back, and wrap applications without compromising product aesthetics. The modular design integrates seamlessly into existing lines, adapting to diverse shapes and high-speed environments. With competitive machinery pricing, the Sirius 100 also features a smart interface for intuitive control and real-time maintenance alerts, reducing operator training time and ensuring continuous operation in food manufacturing settings.
Versatile Design: RF150 for Shrink Sleeve Labeling
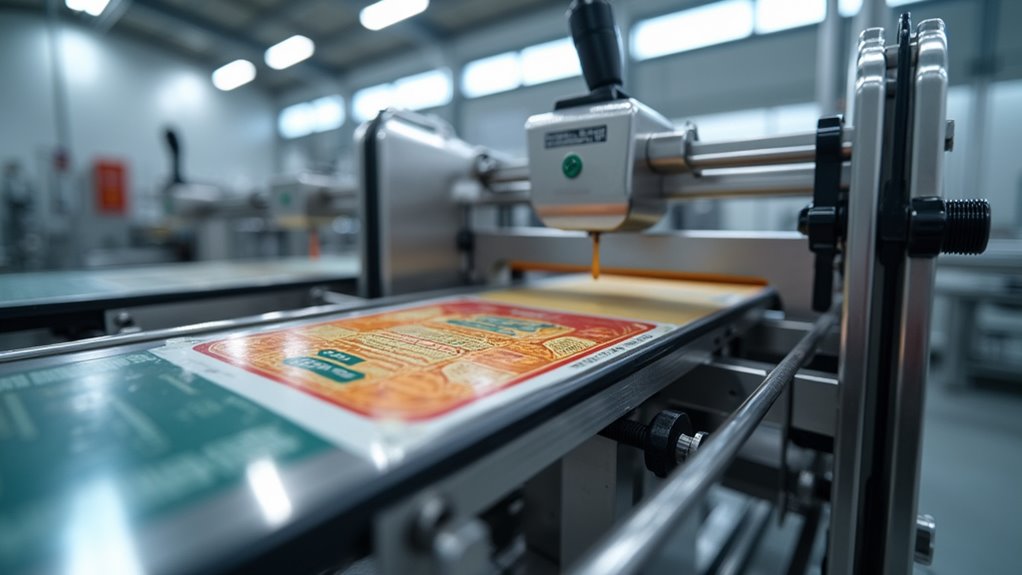
Innovative engineering defines the RF150 shrink sleeve labeling machine, crafted for exceptional versatility in food packaging applications. Designed to handle diverse container materials such as plastic, glass, and metal, it accommodates oval, round, or square shapes with diameters from 25 mm to 210 mm. The RF150 ensures labeling accuracy through variable sleeve positioning systems, supporting sleeve lengths of 25 mm to 300 mm and materials like PVC, PETG, and PLA with thicknesses of 40–70 microns.
Capable of processing up to 250 products per minute, it maintains consistent speed for high-volume lines. Its modular design adapts to various product orientations, while motor-driven adjustments enable rapid setup changes. With a compact footprint of 350 kg, integrated PLC controls, and tool-free change parts, the RF150 minimizes downtime. Compatible with optional shrink tunnels and meeting food-safe hygiene standards, it offers precision and efficiency for mid-to-large-scale operations.
Security Focused: DF100 for Tamper-Evident Solutions
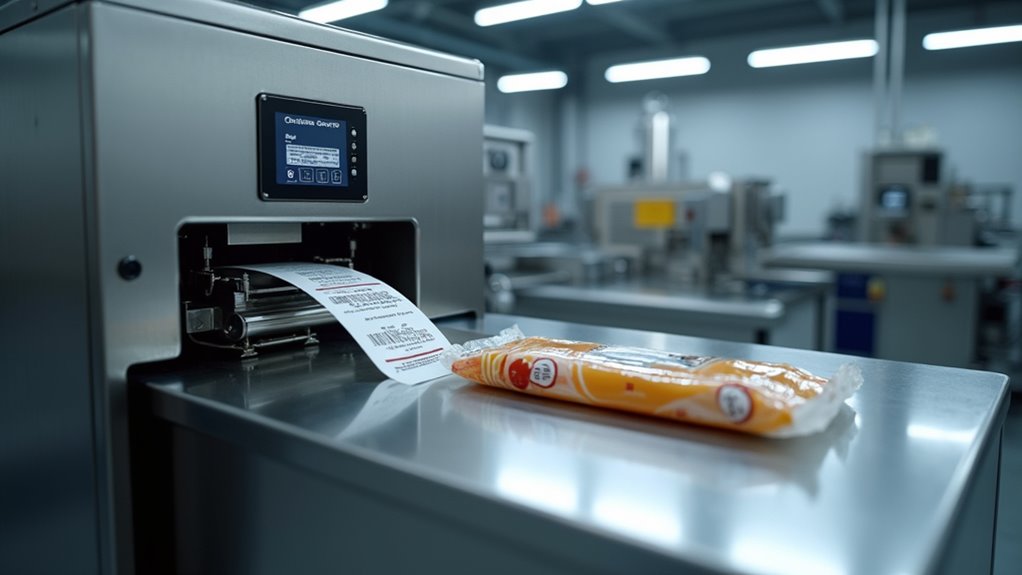
The DF100 shrink sleeve labeling machine stands as a specialized solution for tamper-evident applications in food packaging. Designed for security enhancement, it ensures tamper evidence by applying precise shrink sleeves at speeds up to 100 containers per minute. It supports a range of materials like PETG, PVC, and PLA films with thicknesses of 40-70 microns, achieving optimal shrinkage for container diameters from 30mm to 125mm.
Its compact footprint and conveyor height adjustability (900-1000mm) allow seamless integration into existing lines, while compatibility with hot air and IR heat tunnels ensures consistent sleeve application. The DF100’s dual functionality handles both unprinted tamper-evident sleeves and printed designs, catering to food, beverage, and pharmaceutical sectors. With a user-friendly interface, quick changeovers, and robust 250 kg build, it minimizes downtime and operator strain. This machine delivers reliable output consistency, reinforcing product integrity through advanced tamper evidence and security enhancement features.
Premium Performance: Herma Self-Adhesive Systems
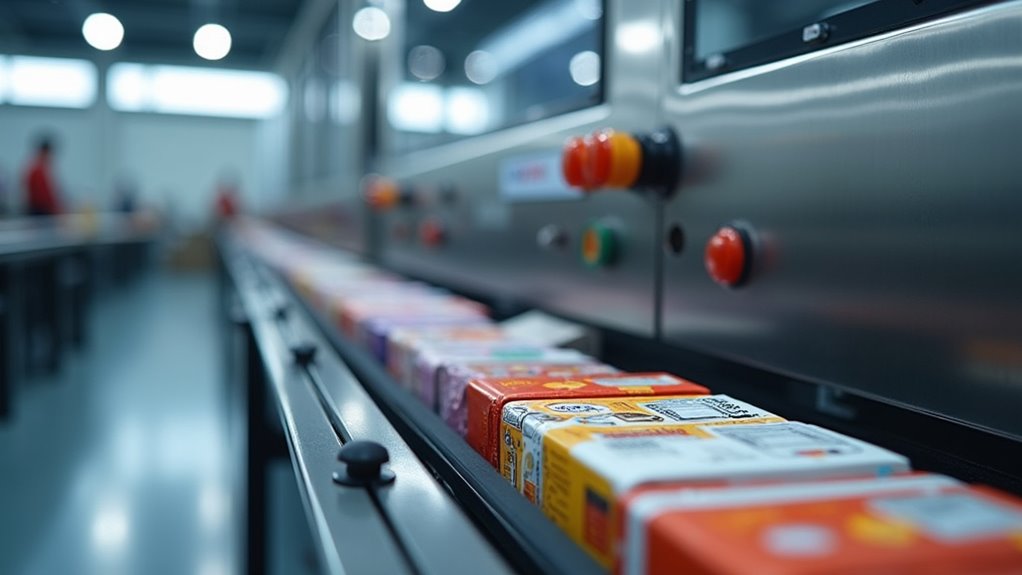
Building on the focus of secure packaging solutions, attention now shifts to the exceptional capabilities of Herma Self-Adhesive Systems in delivering premium labeling performance. With over 110 years of manufacturing expertise, Herma excels in high-performance machinery tailored for the food, pharmaceutical, and OEM industries. Their systems achieve dispensing rates of 200 meters per minute, applying up to 2000 labels per minute with precision via advanced motorized winders and dispensing beaks.
Herma’s seamless production-line compatibility ensures reliability in high-volume food environments, supported by connectivity features for modern factory automation. This includes options for remote monitoring to track performance and robotic integration for automated label application, enhancing operational precision. Additionally, their customizable, FSC-certified materials and bespoke labeling solutions, such as barcode labels, meet specific industrial needs. Backed by global support and consultation services, Herma guarantees quality through integrated end-to-end solutions for safety-critical applications.
Efficiency Boost: Machines With Quick Integration Features
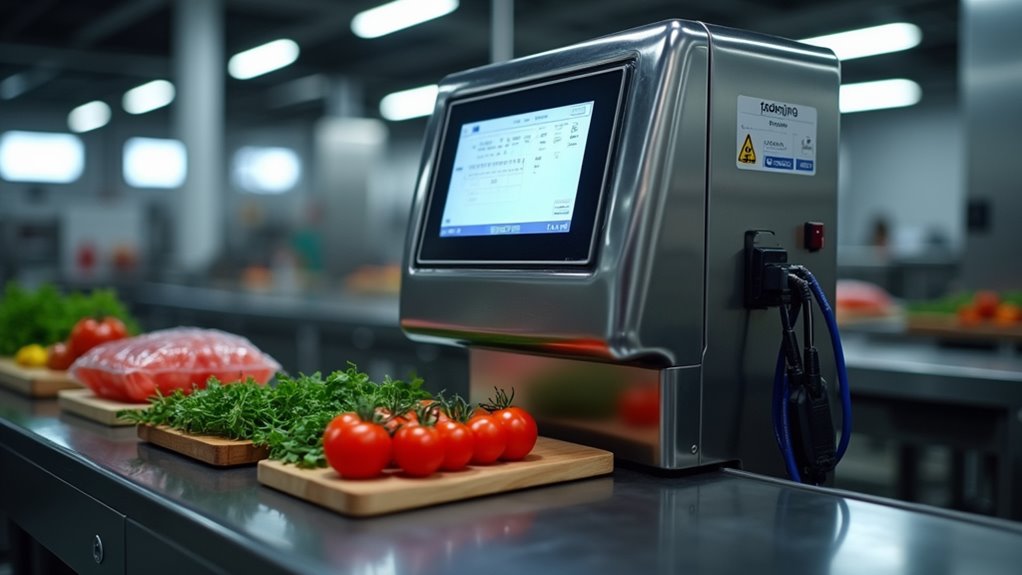
How can food labeling processes keep pace with the demands of modern production environments? The answer lies in machines with quick integration features that streamline operations through advanced tech integration. These systems seamlessly connect to existing production lines and data networks, ensuring compatibility with barcode scanners and ERP software via standardized protocols. IoT sensor connectivity further enhances compliance by linking to environmental monitoring tools, while cloud-linked databases enable real-time label customization with dynamic data like batch codes.
Moreover, process automation is elevated through AI-driven quality control, scanning labels for defects instantly, and automated reordering alerts for low stock. Plug-and-play setups and pre-programmable templates minimize downtime, allowing rapid deployment. Modular designs support scalable configurations, adapting to varying container shapes with interchangeable applicators. Such innovations ensure efficiency, reduce operational disruptions, and meet the high-speed demands of modern food labeling with precision and reliability.
Sustainable Option: Manual Models for Small Operations
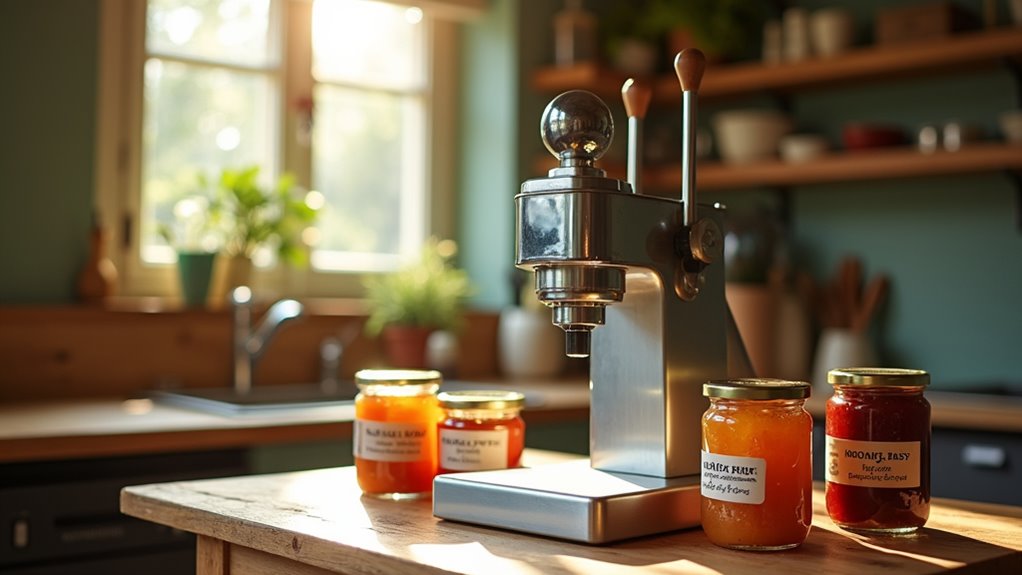
Manual labeling machines present a sustainable and cost-effective solution for small-scale food operations, offering significant benefits over automated systems. Their design supports small batch production with low upfront costs, minimal maintenance, and zero electricity usage, making them ideal for startups or mobile setups. Additionally, these machines ensure precise label application and adaptability to various container sizes, enhancing operational flexibility for limited production runs.
Benefits of Manual Models
Why should small-scale operations consider manual food labeling machines? These systems offer a cost-effective solution for businesses with low-volume production needs. With a significantly lower upfront investment compared to automated alternatives, they mitigate the automation challenges faced by smaller enterprises lacking capital for high-tech equipment. Additionally, they reduce long-term operational costs, as they require minimal maintenance and repairs, ensuring reliability without ongoing expenses.
Manual models are particularly suitable for seasonal or occasional packaging demands, providing flexibility without the burden of complex systems. While they necessitate basic workforce training to ensure accurate labeling, this is often less intensive than managing automated setups. For small operations, manual labeling machines present a sustainable, economical choice tailored to limited production scales.
Ideal for Small Batches
Small-scale food producers often find manual labeling machines to be an optimal solution for handling small batches with efficiency and sustainability. Devices like tabletop manual applicators and handheld applicators offer precision alignment with a ±0.2mm tolerance, ensuring batch consistency across micro-batches. Their design minimizes material waste and supports low energy consumption, aligning with eco-friendly practices.
Additionally, these machines boast equipment durability through robust construction, extending lifespan and reducing replacement frequency. They accommodate irregular container shapes and customizable label sizes, providing versatility for diverse products. With easy maintenance and minimal electronic components, they further lower e-waste. Capable of labeling up to 50 bottles per minute, manual models deliver reliable performance for small operations seeking sustainable, cost-effective solutions.