High speed checkweighers are precision instruments used for dynamic weight verification in fast-paced production lines across industries like food and pharmaceuticals. They employ infeed conveyors, synchronized belts, and load cells or magnetic force restoration technology to capture accurate weight data. Real-time digital signal processing filters noise, while centralized controllers manage tolerances and high-speed reject mechanisms divert non-conforming items. Their robust design ensures reliability. Explore further to uncover additional insights into their advanced capabilities.
Key Takeaways
- High-speed checkweighers are precision tools for weight verification in fast-paced production settings.
- They ensure accuracy with error margins as low as +/-20g at 2 Sigma.
- They use load cells and digital signal processing to measure weights dynamically.
- Synchronized conveyors and reject mechanisms divert non-conforming products swiftly.
- They enhance efficiency and compliance across food, pharmaceutical, and industrial sectors.
Understanding High Speed Checkweighers
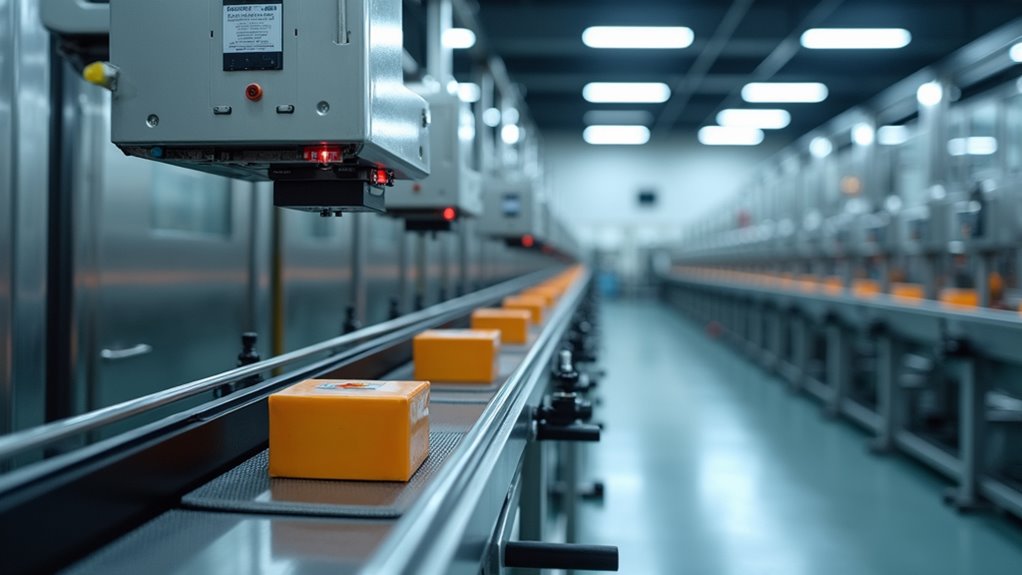
High speed checkweighers are precision instruments designed to ensure accurate weight verification in dynamic production environments across a diverse range of industries. These systems cater to sectors like food and beverage, pharmaceuticals, and heavy industries, offering rugged designs and modular configurations for applications from bulk materials to multilane setups. Their high-speed accuracy, with error margins as low as +/-20g at 2 Sigma, supports compliance with stringent regulatory standards. Additionally, their durable hardware built for longevity ensures minimal need for frequent upgrades or replacements, maximizing production uptime.
Critical to their performance are rigorous calibration procedures, which must be conducted regularly to maintain precision across varying throughput rates, from 50 to 650 packages per minute. Equally important are structured maintenance schedules to uphold durability, especially for IP69K-rated systems in harsh wash-down environments or corrosive settings. By integrating stainless steel construction and dynamic weighing technology, these checkweighers ensure reliable operation in compact, space-efficient layouts, meeting the demands of modern production facilities with consistent accuracy and efficiency.
Operational Mechanisms of Checkweighers
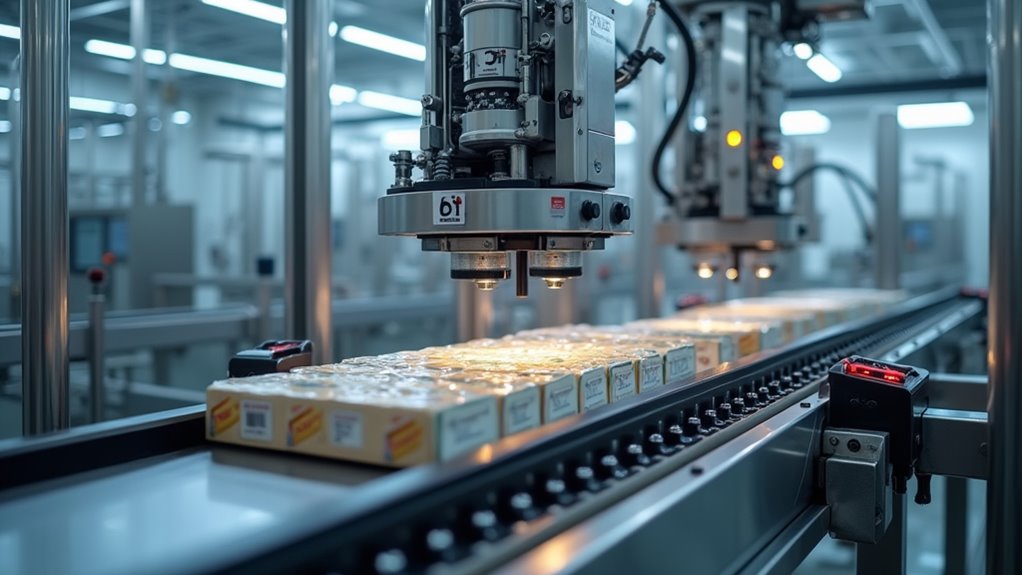
Delving into the operational mechanisms of checkweighers reveals a sophisticated interplay of mechanical, electronic, and software components designed for precision and efficiency in dynamic production settings. At the core, infeed conveyor belts and synchronized belt systems ensure optimal product spacing and speed, while weigh belts equipped with strain-gauge load cells or magnetic force restoration technology capture accurate weight data through sensor integration. These systems rely on dynamic signal processing to filter noise and stabilize readings under high-speed conditions.
Centralized controllers process real-time data, supported by software parameterization for setting tolerances. Component calibration, facilitated by auto-calibration routines, maintains measurement accuracy despite environmental variables like temperature or vibration, mitigated by isolation mounts. High-speed reject mechanisms, driven by precision actuation, divert non-conforming items via air jets or actuators. Advanced algorithms and fieldbus integration further optimize throughput, ensuring seamless operation within automated production lines through meticulous design and control.
Benefits and Applications of Checkweighing Systems
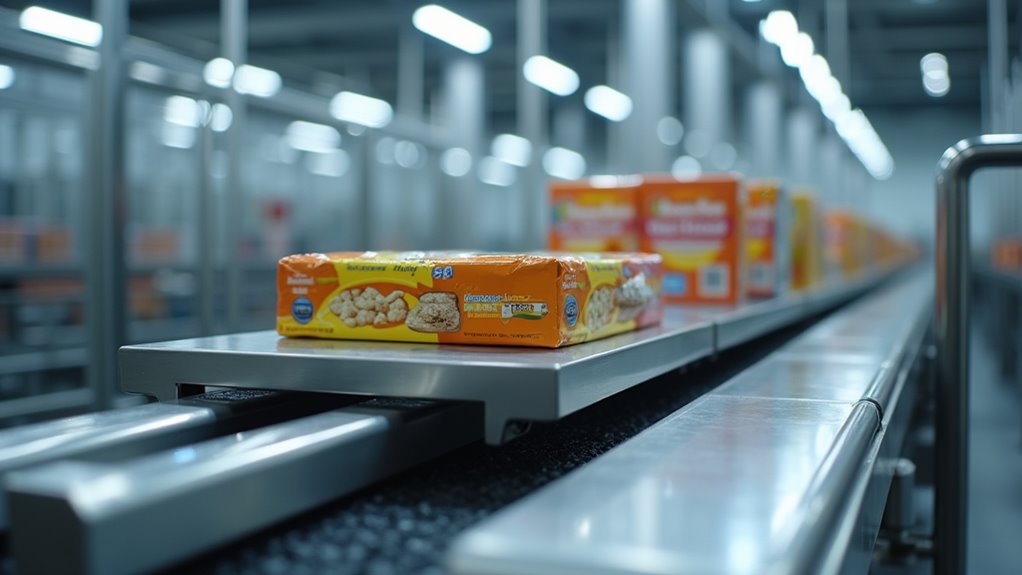
Building on the intricate workings of checkweighers, their value becomes evident in the wide-ranging benefits and applications they offer across industries. From a historical overview, these systems have evolved from manual scales to automated precision tools, ensuring regulatory compliance and operational efficiency. They safeguard consumer trust by maintaining consistent product weights and protect brands through early defect detection in sectors like food, pharmaceuticals, and automotive.
Checkweighers have transformed from manual scales to automated tools, ensuring compliance, efficiency, and consumer trust across food, pharmaceutical, and automotive industries.
Key advantages include:
- Regulatory Adherence: Automated 100% weight inspections prevent legal penalties under acts like the Fair Packaging Act.
- Cost Efficiency: Real-time adjustments reduce material waste and labor costs by minimizing rework.
- Industry-Specific Precision: Customization options allow tailored solutions for dosing accuracy in pharmaceuticals or portion control in food safety.
Additionally, integration with modern production lines enhances data tracking and process control. Customization options further enable seamless adaptation to unique industry needs, maximizing quality assurance and minimizing consumer complaints.