Belt weigh feeders are sophisticated devices used in material handling to precisely control the flow of bulk materials. They integrate weighing and conveying functions, utilizing load cells to measure material weight and speed sensors to monitor conveyor speed, thereby ensuring accurate feed rates. Calibration is essential for their performance, involving adjustments for factors like belt tension and material properties. Their application across various industries enhances process efficiency and product quality. Understanding their mechanics reveals their critical role in modern manufacturing.
Key Takeaways
- Belt weigh feeders are essential in industries for precise material handling and flow measurement.
- They comprise load cells, speed sensors, conveyor systems, and controllers for accurate control.
- Load cells convert material weight into electrical signals, and speed sensors measure conveyor speed.
- Controllers process these signals to adjust feed rates, ensuring the desired accuracy.
- They are calibrated using test materials and static weights to maintain optimal performance and reliability.
Understanding Belt Weigh Feeders
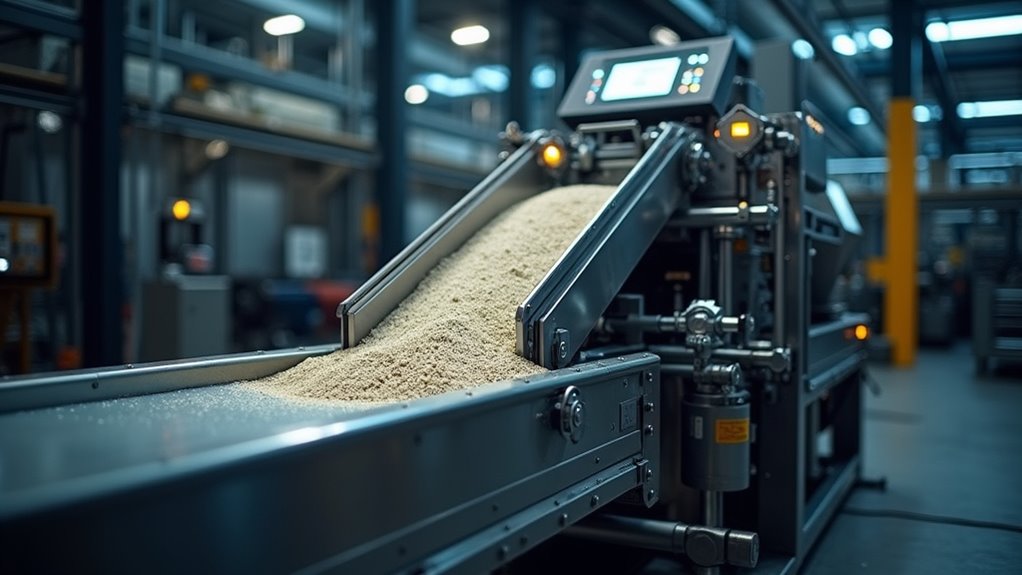
Belt weigh feeders are integral components in material handling systems, serving as specialized flow meters for granular or powdered solids. These feeders are designed to provide continuous, accurate, and controlled delivery of bulk materials into processes, ensuring consistency in mixtures based on specific formulations. Checkweighers are also widely used in industries to verify the weight of packaged goods during production. Belt weigh feeders operate by adjusting conveyor speed to maintain a constant flow rate, with a load cell continuously weighing a section of the conveyor and a speed sensor measuring belt speed. Accurate material blending is critical in industries like cement production, where precise ratios of raw materials are required for high-quality final products.
Key Components and Their Functions
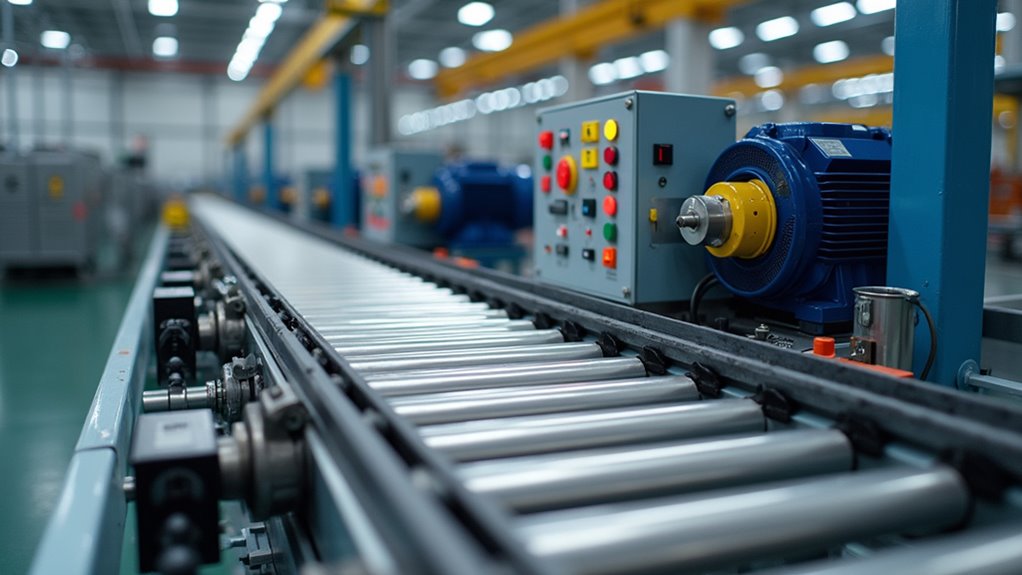
At the core of a belt weigh feeder’s operation are several key components, each with a distinct role in ensuring precise and consistent material handling.
Load cells, located beneath the conveyor belt, convert material weight into electrical signals, which are then sent to the controller.
Load cells: The bridge between material weight and electrical signals, enabling precise control and measurement in belt feeder operations.
Speed sensors, typically associated with a non-driven pulley, measure belt speed, providing the data needed to calculate mass flow rate.
The conveyor system, consisting of the belt, idlers, and drive mechanism, facilitates stable material transport, while the controller processes signals from the load cells and speed sensors to adjust the feed rate, maintaining the desired throughput with high accuracy.
How Belt Weigh Feeders Work
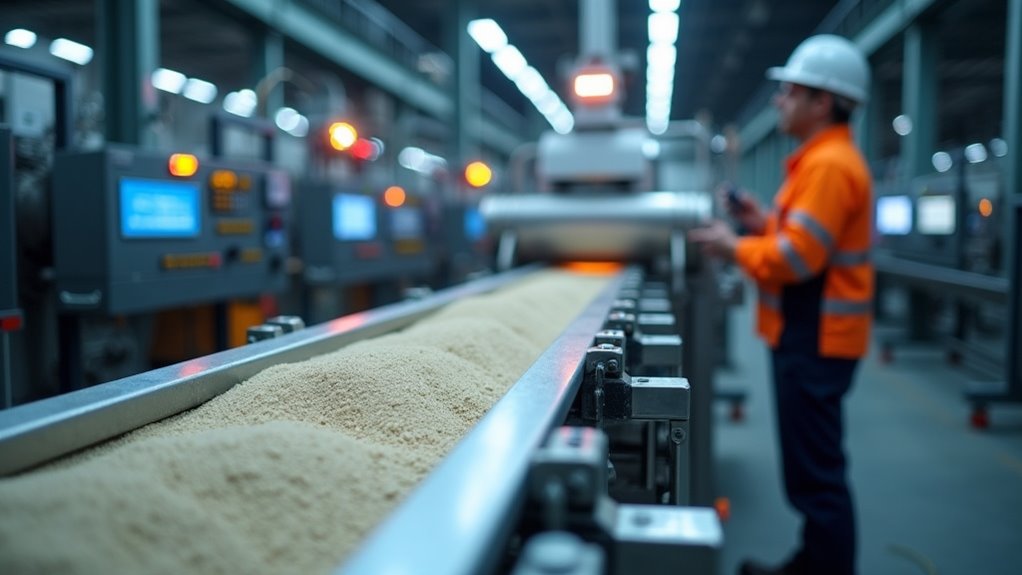
The material handling process in belt weigh feeders begins with the controlled release of material from a hopper or pre-feeder onto the conveyor belt.
The control system’s function involves continuously measuring the weight of material on a specific belt section using load cells and determining belt speed using a tachometer or optical encoder.
The controller then calculates the mass flow rate by multiplying the weight per unit length by the belt speed, adjusting the belt speed as needed to maintain the desired flow rate setpoint.
Material Handling Process
Material handling in industrial processes often relies on belt weigh feeders to ensure precision and efficiency. These feeders are designed to handle a wide range of bulk materials, from fine powders to large, abrasive lumps.
The feeding methods employed by belt weigh feeders ensure consistent and accurate material delivery to downstream processes. Bulk materials are typically introduced into the feeder via a hopper or chute, with an adjustable gate creating a uniform material profile on the conveyor belt.
The material is then continuously weighed as it travels along a specific section of the conveyor, supported by a weighbridge structure equipped with precision load sensors. This allows the feeder to calculate the mass flow rate of the material, ensuring precise control over the feed rate.
Control System Function
Belt weigh feeders rely on sophisticated control systems to ensure accurate and consistent material flow.
These systems use advanced control algorithms and feedback mechanisms to maintain precise mass flow rates. Load cells and speed sensors provide continuous measurements of material weight and conveyor speed, respectively. A microcontroller or PLC processes these inputs, calculating the instantaneous flow rate and comparing it to a predefined setpoint.
Using a PID control loop, the system generates adjustment outputs to regulate conveyor speed through a Variable Frequency Drive (VFD). This closed-loop control ensures that any variations in material density or input feed rate are compensated for, achieving a stable and reliable material flow.
Calibration and Accuracy in Belt Weigh Feeders
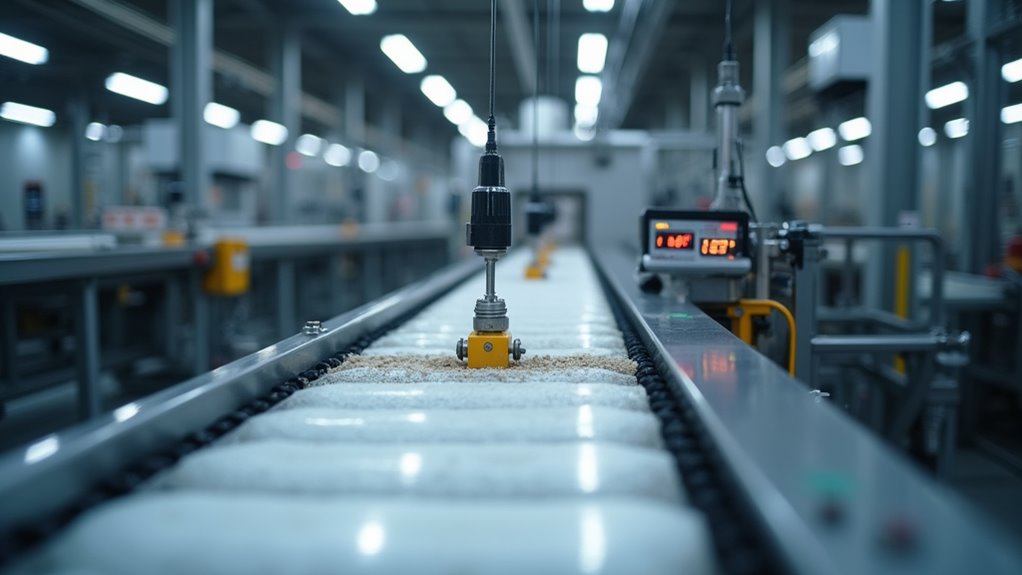
Calibration and accuracy in belt weigh feeders are critical to ensuring optimal performance and reliable material feed rates.
Various calibration methods, including material testing, static weight testing, and roller chain testing, are used to verify and maintain accuracy.
Key factors such as belt tension, material properties, and regular calibration processes significantly influence the overall accuracy of the feeder.
Calibration Techniques
Understanding calibration techniques for belt weigh feeders is crucial to ensuring accurate and reliable weighing of bulk materials.
Two primary calibration methods exist: zero calibration, establishing a baseline for an empty conveyor, which should be performed daily or weekly, and span calibration, adjusting the measurement to match a known load, which should be conducted monthly.
Static test weight calibration is the most common method, involving the placement of known weights on the weighbridge to simulate load conditions. This method is relatively inexpensive and provides a repeatable calibration check.
Proper calibration is essential to maintaining system accuracy and ensuring optimal belt weigh feeder performance.
Maintaining Accuracy
Maintaining the accuracy of belt weigh feeders is an ongoing process that requires attention to detail and a comprehensive approach. Regular inspections and adherence to maintenance practices are essential to address accuracy challenges such as belt tension inconsistencies, misaligned rollers, and load cell performance.
Mechanical integrity must be maintained through regular checks for wear, ensuring components like belts and rollers are clean and functioning properly. Additionally, maintaining consistent material flow and properly handling material properties, including temperature and abrasiveness, is critical for sustained accuracy.
Protecting load cells from environmental factors and carefully managing material layer consistency further contribute to the reliable operation of belt weigh feeders.
Applications and Industries Using Belt Weigh Feeder Systems
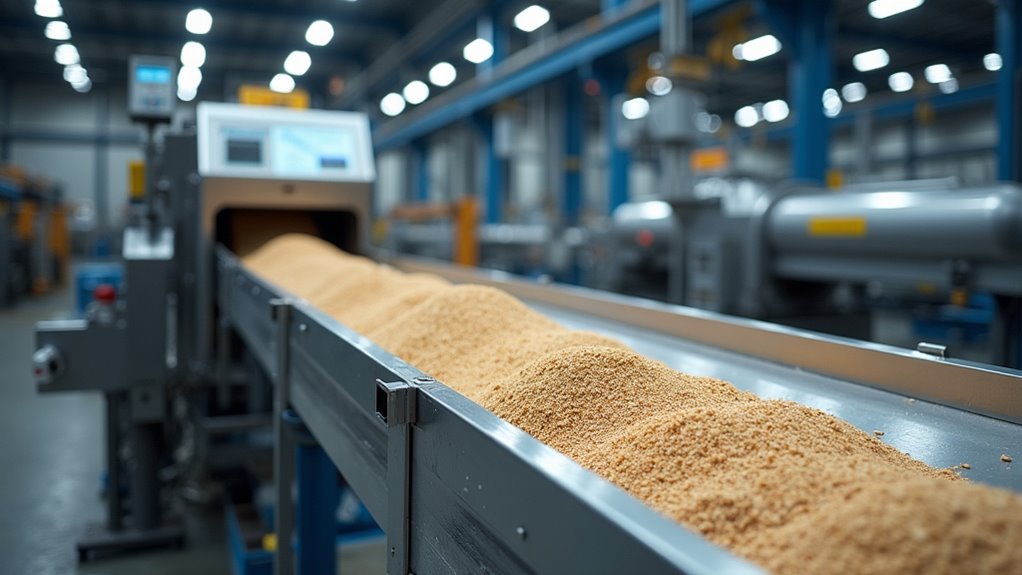
While the importance of belt weigh feeders in industrial applications is widely recognized, their role in ensuring precision and efficiency across various sectors cannot be overstated.
These devices play a critical role in maintaining product quality and process efficiency by controlling the flow of bulk materials with unmatched precision.
Belt weigh feeders: Guardians of product quality and process efficiency, mastering the flow of bulk materials with unparalleled precision.
- Mining and Mineral Processing: Ensuring consistent material feed for ore processing and coal handling.
- Cement and Construction Materials: Regulating flow in raw material feeding and clinker production.
- Food Processing and Agriculture: Maintaining product consistency in ingredient dosing and grain handling.
- Chemicals and Pharmaceuticals: Enabling precise measurement of additives and resin production.
- Environmental Control: Supporting waste management and recycling processes.
Furthermore, the adoption of advanced technologies, such as real-time analytics, enables improved monitoring and optimization across various applications.
The application benefits of belt weigh feeders include enhanced process control, reduced material waste, and improved product quality, making them indispensable across a wide range of industries.
Benefits of Using Belt Weigh Feeders in Material Handling
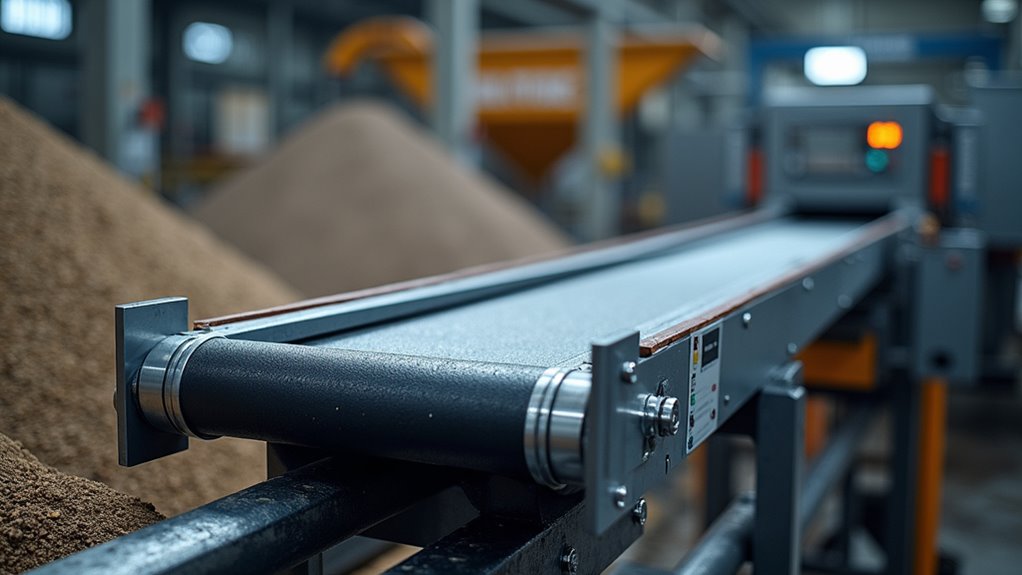
Belt weigh feeders offer numerous advantages in material handling operations, leveraging their widespread applications across various industries.
These devices provide high-accuracy material flow measurements, achieving accuracies of around ±0.5%, which is critical for processes with stringent quality standards. Improved accuracy minimizes errors in inventory management and enables precise dosing and blending of materials, ensuring product quality and consistency.
Moreover, belt weigh feeders contribute to cost efficiency by reducing material waste, minimizing energy consumption, and lowering operational costs through enhanced automation. Their ability to optimize conveyor speed and feed rates further enhances efficiency and productivity in industrial environments.