For businesses seeking efficiency, the top seven automatic bottle labeling machines excel in precision and speed. These include advanced wrap-around labelers achieving ±1mm accuracy for cylindrical bottles, high-speed rotary systems handling up to 500 units per minute, and versatile front-back labelers for diverse shapes. Top-bottom and pressure-sensitive models ensure flawless application on flat or varied materials, while shrink sleeve and tube labelers offer specialized branding and precision. Explore further to uncover detailed insights on each solution.
Key Takeaways
- High-speed rotary labeling machines achieve up to 500 bottles per minute with ±1mm accuracy for cylindrical containers.
- Versatile shape labeling systems handle diverse forms like round, square, and oval at speeds of 60-240 bottles per minute.
- Top and bottom labeling machines offer dual-head application with ±0.5mm accuracy and speeds up to 300 products per minute.
- Heat tunnel technology ensures uniform sleeve shrinkage and distortion-free results for tamper-evident packaging.
- Tube labeling systems reach 1800 vials per hour with automation for precision and reduced labor costs.
Top Wrap-Around Labeler for Cylindrical Bottles
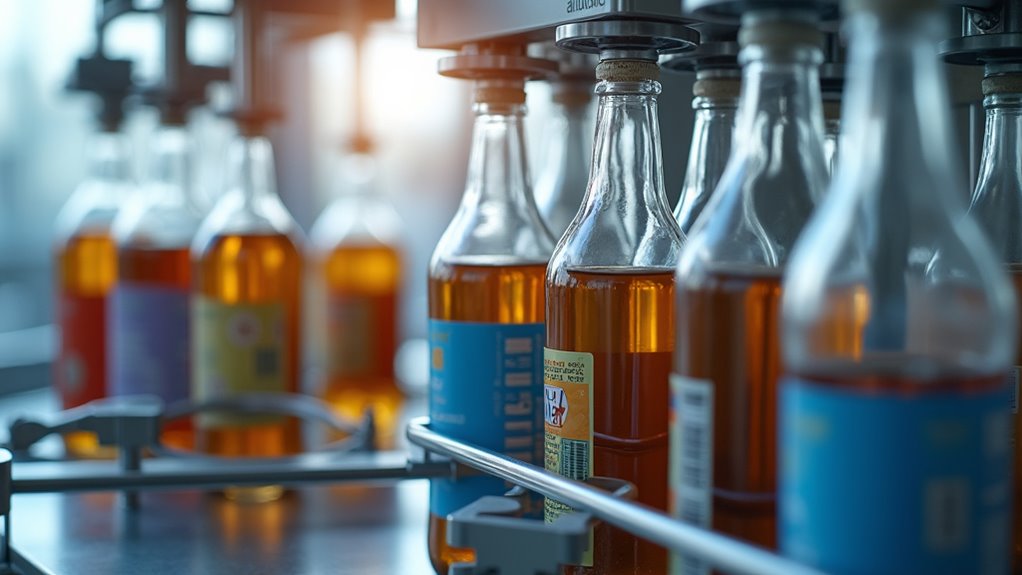
Precision defines the top wrap-around labeler for cylindrical bottles, a specialized machine engineered to apply pressure-sensitive labels with exceptional accuracy to a variety of container types, including bottles, jars, tubes, and cans. Designed for industries like food, pharmaceuticals, and cosmetics, it handles diverse materials such as glass, plastic, and metal, with labeling accuracy often within ±1mm. Its automatic operation, powered by stepper or servo motors, ensures consistent placement at speeds up to 400 products per minute. This labeler also offers flexibility, as it easily adjusts for container sizes, accommodating a wide range of products from small vials to larger bottles.
The Setup Process is streamlined through user-friendly interfaces like touchscreens and patented software, enabling quick configuration for varying container sizes (0.5″ to 8″ diameter). Integrated conveyors and sensors enhance precision during operation. For longevity, Maintenance Tips include regular cleaning of the stainless steel frame to prevent residue buildup, inspecting sensors for optimal detection, and lubricating moving parts to minimize wear, ensuring sustained performance in demanding production environments.
Leading Front and Back Labeler for Versatile Shapes
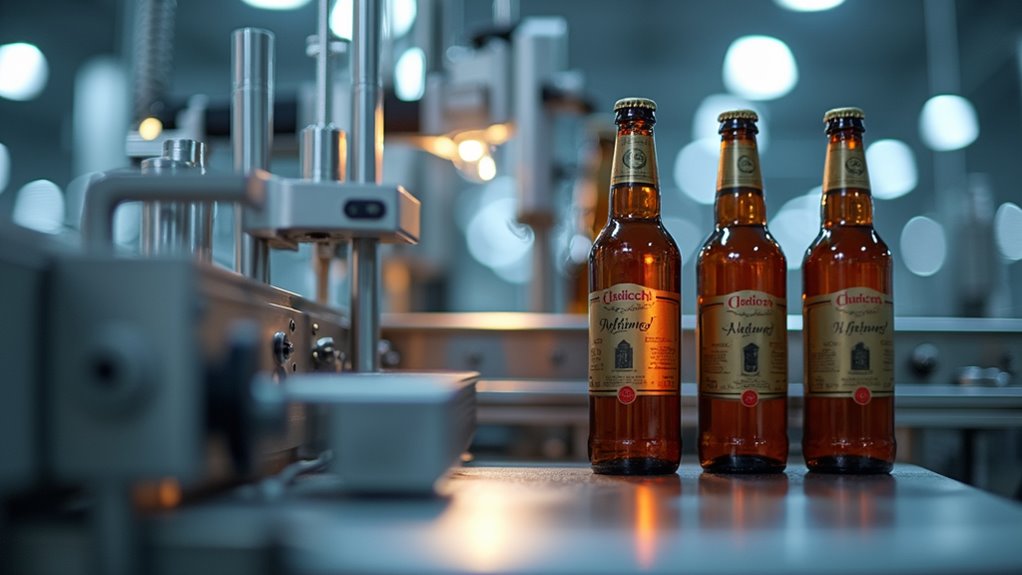
Front and back labelers for versatile shapes are engineered to handle a broad spectrum of container geometries, including flat, oval, square, and rectangular forms, ensuring compatibility across diverse product lines. These systems are equipped with dual labeling heads that operate in synchronization to achieve precise placement of pressure-sensitive labels on both sides of a container simultaneously. This capability, supported by advanced alignment mechanisms, guarantees accuracy and consistency even on non-cylindrical surfaces.
Versatile Shape Compatibility
Innovative automatic bottle labeling machines demonstrate remarkable adaptability in handling a wide array of container shapes through advanced engineering. These systems excel in managing Bottle Variety, from standard round and square to complex tapered and hexagonal forms, ensuring Form Compatibility across diverse industries like food, beverage, and cosmetics. Equipped with adjustable bases, flexible guiding mechanisms, and stabilizing systems, they align varied profiles with precision. Advanced sensors and microprocessor controls enable quick shape changeovers, while servo-driven applicators ensure accurate label placement on non-uniform surfaces. Rotary systems and optional attachments like wrap-around mechanisms further enhance versatility for irregular containers. With minimal changeover times and speeds of 60-240 bottles per minute, these machines optimize efficiency for varying container sizes and materials.
Dual Label Precision
Building on the adaptability of automatic bottle labeling machines for diverse container shapes, attention now shifts to their capability in achieving dual label precision for front and back applications. These systems employ servo motors and sensors to ensure meticulous Label Timing, detecting bottle positions for exact release and placement with tolerances as tight as +/- 0.1mm. Bottle Stability is maintained through top hold-down belts and dual guiding chains, preventing movement during simultaneous label application from opposing heads. Advanced PLC controls and high-frequency encoders further enhance accuracy, while proper setup and maintenance are critical for consistent results. Such precision ensures flawless alignment on versatile shapes, meeting stringent business demands for quality and efficiency in labeling operations.
High-Speed Rotary Labeler for Complex Applications
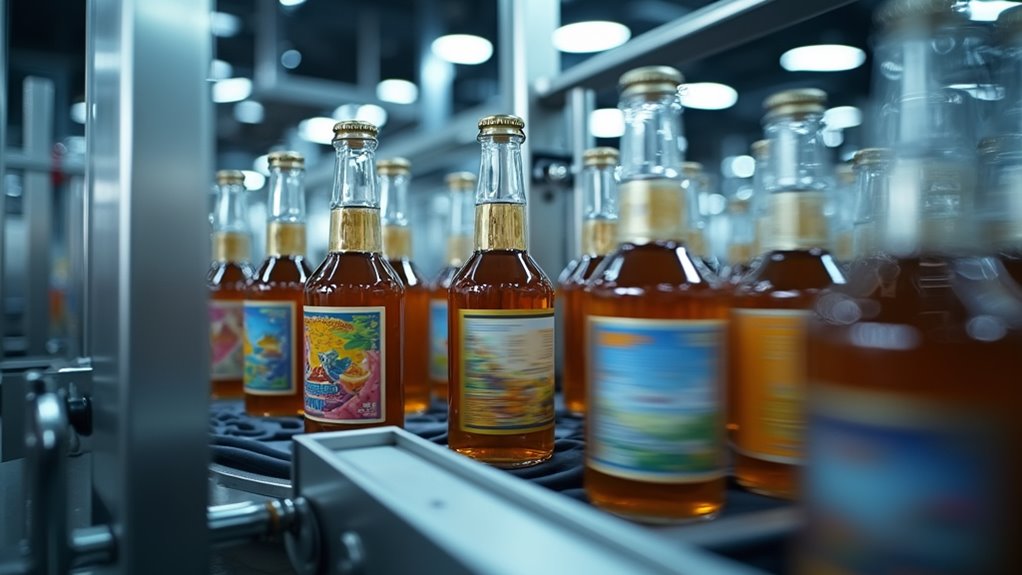
High-speed rotary labelers stand as a pinnacle of efficiency in the realm of automated bottle labeling, specifically engineered for complex applications. These machines, a testament to Rotary Innovation, achieve remarkable speeds of up to 500 bottles per minute, leveraging continuous rotary platforms and servo-driven controls for precise label placement. They adeptly address Application Challenges by managing diverse container shapes—round, square, oval, or conical—and applying multiple label types like front, back, and tamper-evident seals without misalignment or wrinkles.
Their flexibility shines in handling various materials and sizes with minimal part changes, while camera-based orientation ensures accuracy. Integration into production lines is seamless, with features like automatic speed synchronization and non-stop labeling enhancing efficiency. Advanced options, including serialization and Faulty Label Reconciliation Systems, minimize waste. Built for durability with safety interlocks and touchscreen HMIs, these labelers excel in high-volume, multi-shift operations, meeting intricate labeling demands with precision.
Efficient Top and Bottom Labeler for Flat Surfaces
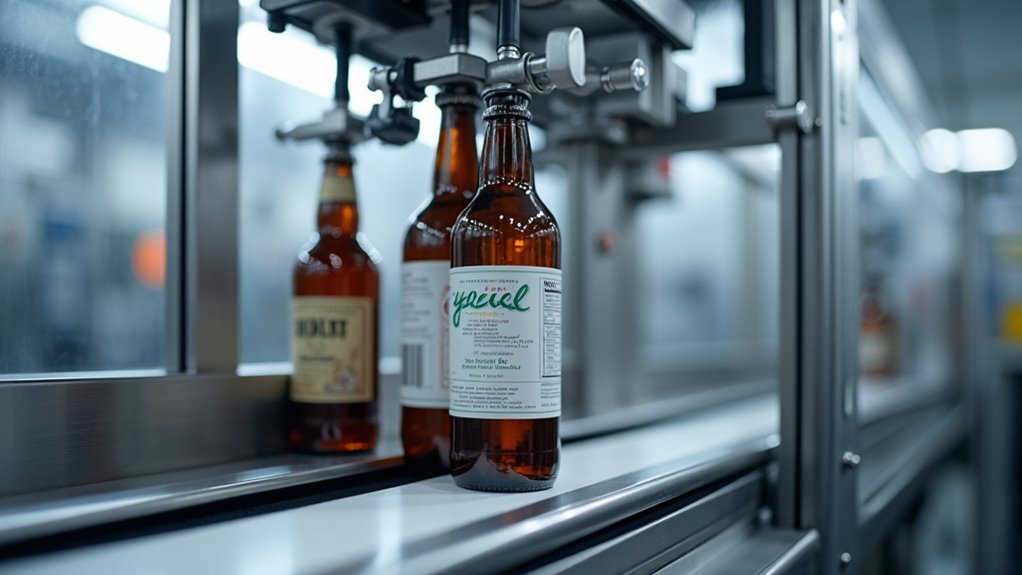
Efficient top and bottom labelers represent a specialized solution for applying labels to flat surfaces of products with precision and speed. These machines utilize dual labeling heads to simultaneously apply labels to both sides of items like boxes, trays, and clamshells, achieving accuracy within +/- 0.5mm to 1mm. Their design often incorporates Split Conveyors with adjustable gaps to accommodate diverse product sizes while enabling bottom label placement, alongside Hugger Belts that provide gentle stability for items during transport, particularly those with irregular shapes.
Built with durable materials like S304 stainless steel, these labelers feature adjustable components and PLC controls for seamless product changeovers and parameter storage. Capable of speeds up to 300 products per minute, they enhance productivity by reducing handling time. Serving industries such as food, pharmaceuticals, and electronics, they ensure consistent label placement, improving quality control and operational efficiency in automated production lines.
Advanced Pressure-Sensitive Labeler for Diverse Materials
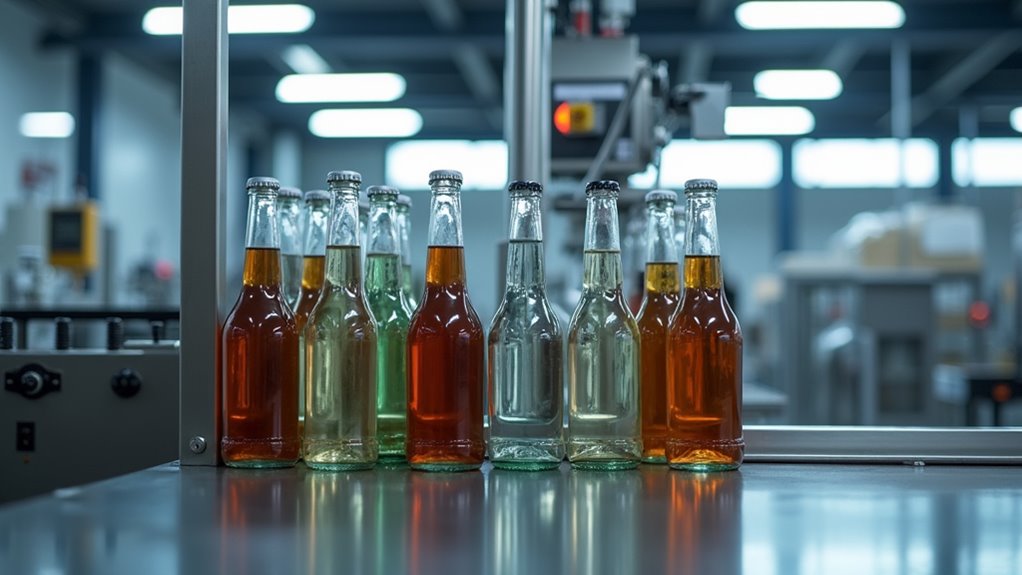
Advanced pressure-sensitive labelers offer a sophisticated solution for applying pre-glued labels to a wide range of products with minimal pressure, ensuring secure adhesion without the need for heat, water, or solvents. These machines utilize an adhesive backing that bonds to surfaces like glass, plastic, metal, and wood upon contact, accommodating diverse container shapes such as cylindrical, square, and irregular forms. Labels, fed from rolls, are precisely placed using advanced sensors and variable speed conveyors, achieving high-speed outputs up to 1200ppm in in-line systems.
Their versatility extends to specialized applications, including Degassing Applicators for coffee packaging and Eco Adhesives for sustainable options like wash-off labels on recyclable cans. With configurations for front/back, wraparound, and tamper-evident labeling, these systems ensure accuracy and efficiency. Integration with production lines, quick changeovers, and automation capabilities further optimize throughput, making them indispensable for varied industrial and consumer goods applications.
Innovative Shrink Sleeve Applicator for Full-Body Branding
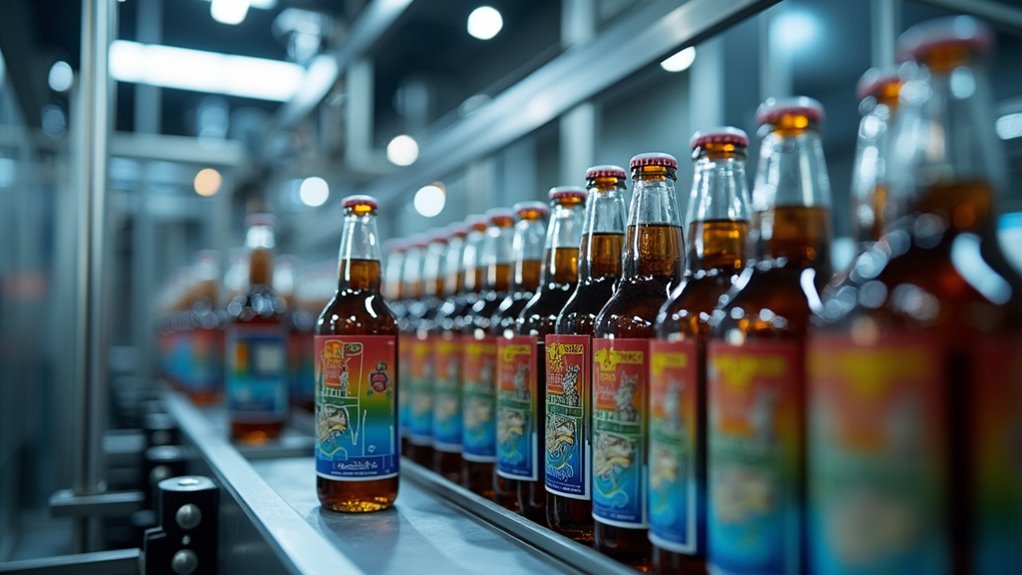
Precision in branding reaches new heights with innovative shrink sleeve applicators designed for full-body container coverage. These systems deliver 360-degree graphics with vibrant, high-resolution designs, maximizing surface area for impactful branding on diverse container shapes. Leveraging Mandrel Innovation, the applicators ensure precise sleeve placement, while advanced servo controls enhance operational accuracy at speeds up to 800 units per minute.
The application process integrates a sophisticated Heat Tunnel, shrinking sleeves to conform seamlessly using steam or hot air options for distortion-free results. Below is a concise overview of key features:
Feature | Benefit |
---|---|
Mandrel Innovation | Ensures precise sleeve application |
Heat Tunnel Technology | Provides uniform shrinkage |
High-Speed Capability | Supports up to 800 units/minute |
These machines offer durability with moisture-resistant materials and tamper-evident options, while enabling cost savings through stock container use and sustainable film choices for modern businesses.
Specialized Tube Labeler for Precision and Speed

Specialized tube labelers are engineered to deliver exceptional performance in high-speed tube labeling, achieving rates of hundreds to thousands of units per hour depending on the configuration. These machines incorporate precision application technology, utilizing advanced components like servo motors and optical sensors to ensure label placement accuracy within ±0.5mm to ±1mm. Such meticulous design supports consistent, professional results, meeting the stringent demands of industries like pharmaceuticals and cosmetics.
High-Speed Tube Labeling
High-speed tube labeling machines represent a critical advancement in automated packaging, designed to meet the rigorous demands of modern production environments. These systems achieve remarkable speeds, labeling up to 1800 vials per hour, significantly enhancing production efficiency over manual methods. They incorporate automation to eliminate human error, reduce labor costs, and minimize downtime with durable industrial components.
Equipped with advanced sensors and PLCs, these machines ensure precise label placement on diverse tube materials and shapes. Below is a snapshot of their capabilities:
Feature | Benefit | Example |
---|---|---|
Speed | High throughput | Up to 1800 vials/hour |
Automation | Reduces errors | Consistent labeling |
Tube Handling | Versatile compatibility | Various diameters |
Control Systems | Precision operation | Touchscreen panels |
Precision Application Technology
Building on the advancements in high-speed tube labeling, attention now shifts to the sophisticated realm of precision application technology in specialized tube labelers. These systems employ cutting-edge mechanisms like Laser Calibration to ensure exact tube positioning and alignment, minimizing errors such as wrinkling or misalignment. Advanced sensors and vision inspection systems, paired with precision dispensing, synchronize label release with tube movement for flawless application. Additionally, Haptic Feedback technology provides real-time tactile data to operators or control systems, enhancing adjustment accuracy for varying tube dimensions. Automated handling and customized holders further reduce human error, while sophisticated control systems maintain consistency. Such precision not only elevates brand presentation but also boosts efficiency by minimizing waste and rework in production lines.