For businesses seeking top bottle labeling machines in 2025, options include high-volume automatic labelers for 1000+ labels per minute, versatile semi-automatic machines for small batches with ±0.2mm precision, precision rotary systems for multi-side labeling, compact benchtop models for startups, advanced shrink sleeve applicators for unique designs, flexible front-back labelers for diverse containers, and smart integrated solutions with traceability via QR codes. Explore further to uncover detailed insights on optimizing your production needs.
Key Takeaways
- High-volume rotary systems label up to 1000 labels per minute for large-scale production.
- Semi-automatic machines offer precision of ±0.2mm for small batch versatility.
- Benchtop models provide portability and compact design for limited workspaces.
- Advanced applicators handle irregular shapes with servo motor accuracy of ±1mm.
- Smart integrated solutions ensure traceability with QR codes and compliance features.
Leading Automatic Labeler for High-Volume Production
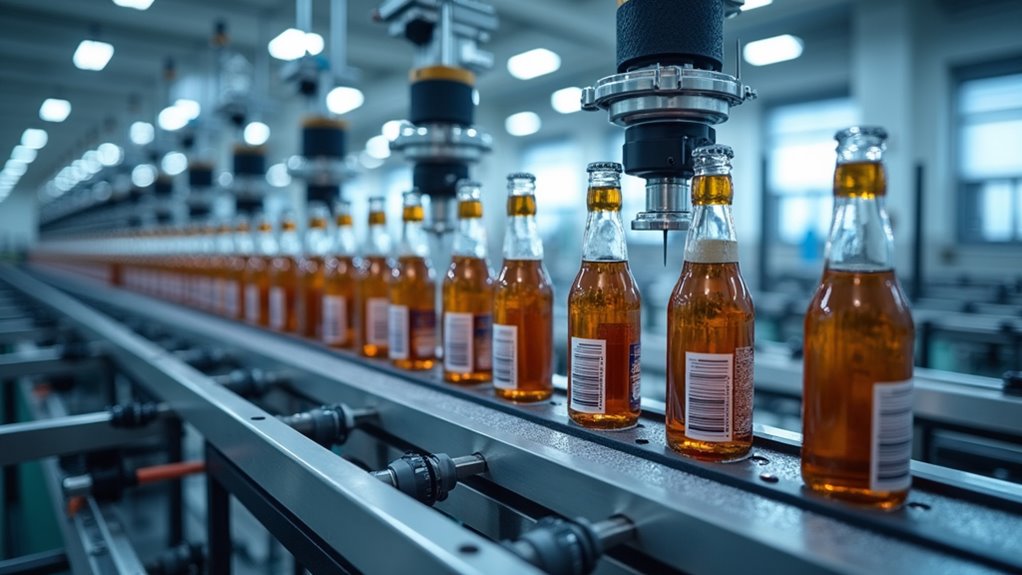
The realm of high-volume production demands equipment capable of relentless performance, and leading automatic labelers meet this challenge with exceptional efficiency. Engineered for continuous 24/7 operation, these machines achieve impressive speeds of 100 to over 1000 labels per minute, ensuring high speed durability in demanding environments. Their robust construction, often featuring stainless steel frames, withstands rigorous use while maintaining precision in label placement for brand consistency and compliance.
Integral to their design is conveyor integration, allowing seamless operation with adjustable speeds to synchronize with production lines. Advanced control systems, such as microprocessors and PLCs, paired with servo-driven applicators, ensure accurate synchronization and label alignment via optical fiber sensors. Models like rotary and inline labelers from manufacturers such as Quadrel and Krones cater to diverse container shapes, enhancing throughput. Additionally, these machines offer flexibility to handle various bottle types, including glass, plastic, and metal diverse bottle materials. This automation reduces labor costs, minimizes errors, and boosts production efficiency in high-volume settings.
Versatile Semi-Automatic Machine for Small Batches
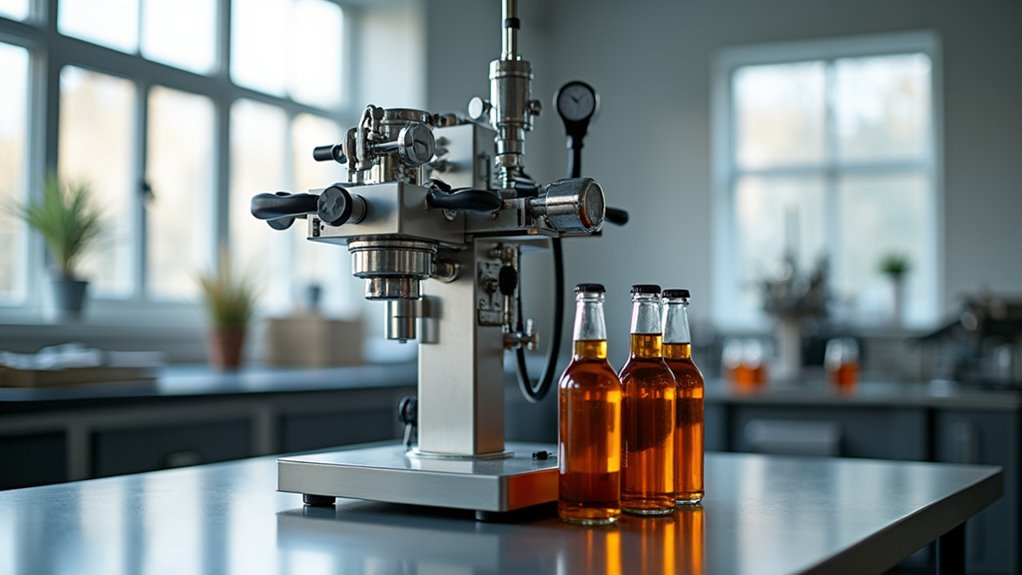
Semi-automatic bottle labeling machines offer significant advantages for businesses managing small to medium production runs, providing ideal batch flexibility to accommodate diverse product lines. These systems balance efficiency with operator involvement, featuring user-friendly controls and quick setup processes that simplify operation and reduce training needs. Their design ensures adaptability, allowing seamless transitions between different container sizes and label types with minimal downtime.
Ideal Batch Flexibility
For businesses managing small to medium production runs, versatile semi-automatic bottle labeling machines offer an optimal solution for batch flexibility. These machines provide Scalable Flexibility, accommodating diverse container shapes—round, square, oval—and materials like glass, plastic, and metal, with adjustable mechanisms for varying dimensions (15mm-150mm diameters, 20mm-250mm heights). Their Adaptive Systems handle multiple label types, including self-adhesive and wrap-around, with precision placement (±0.2mm to ±0.5mm). Designed for operational versatility, they support frequent batch changes through tool-less adjustments and modular setups, minimizing downtime. Cost-effective for startups, they reduce labor expenses compared to manual methods while ensuring accuracy. Ideal for moderate volumes, these systems bridge manual and automatic processes, offering customization without sacrificing consistency in dynamic production environments.
Easy Operator Use
Versatile semi-automatic bottle labeling machines prioritize operator ease through intuitive design and streamlined functionality. These machines feature user-friendly interfaces with touchscreens or minimal buttons, ensuring quick learning and minimal training. Operator Comfort is enhanced by simplified adjustments for bottle sizes and foot pedal initiation, reducing physical strain during small batch operations.
Feedback Systems, such as smart sensors, provide real-time data on label application accuracy, minimizing errors. The table below highlights key operational aspects:
Feature | Benefit |
---|---|
Intuitive Controls | Reduces training time |
Adjustable Mechanisms | Adapts to various bottle dimensions |
Sensor Integration | Ensures precise labeling |
Designed for durability and easy maintenance, these machines optimize efficiency while maintaining operator oversight through manual placement and removal tasks.
Precision Rotary System for Multi-Side Labeling
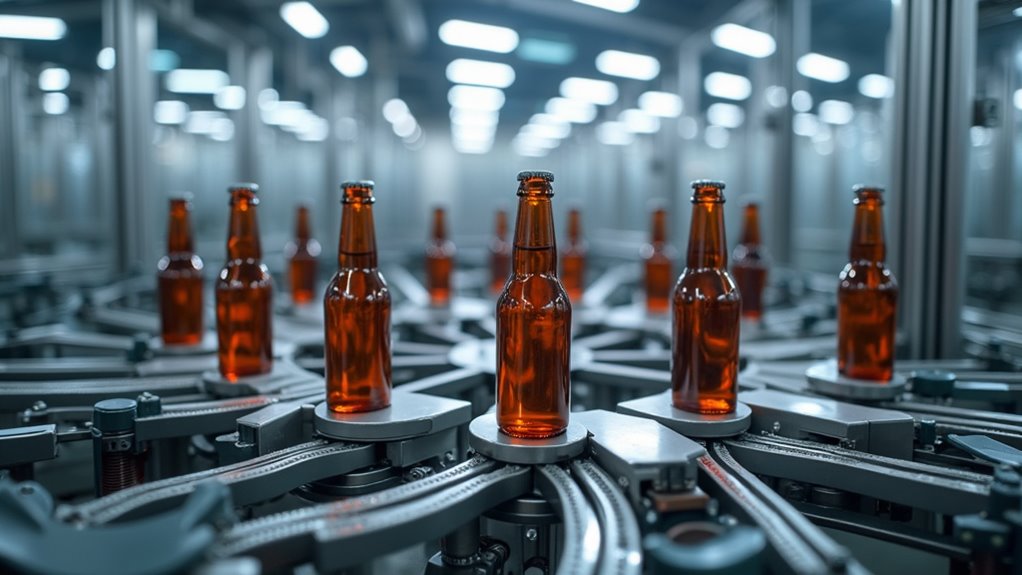
Precision rotary systems for multi-side labeling represent a pinnacle of engineering in bottle labeling technology, designed to meet the demands of high-speed and high-accuracy applications. These systems utilize rotating platforms to achieve rates up to 500 products per minute, ensuring precise label placement with accuracy between ±0.04 mm and ±0.3 mm. Advanced Servo Motors enable exact positioning with minimal variability, while Cam Systems provide mechanical control for consistent rotation, particularly for complex container shapes.
Such systems excel in applying multiple labels—front, back, neck, or wrap-around—simultaneously or sequentially on diverse bottle types, including round, square, and irregular forms. Containers are secured between a bottle plate and centering bell, allowing controlled rotation for multi-side access. Sensors ensure accurate alignment, minimizing skewing. Ideal for high-volume industries like food, beverage, and pharmaceuticals, these rotary systems offer versatility, handling various materials and label types with continuous motion for superior throughput.
Compact Benchtop Option for Startups
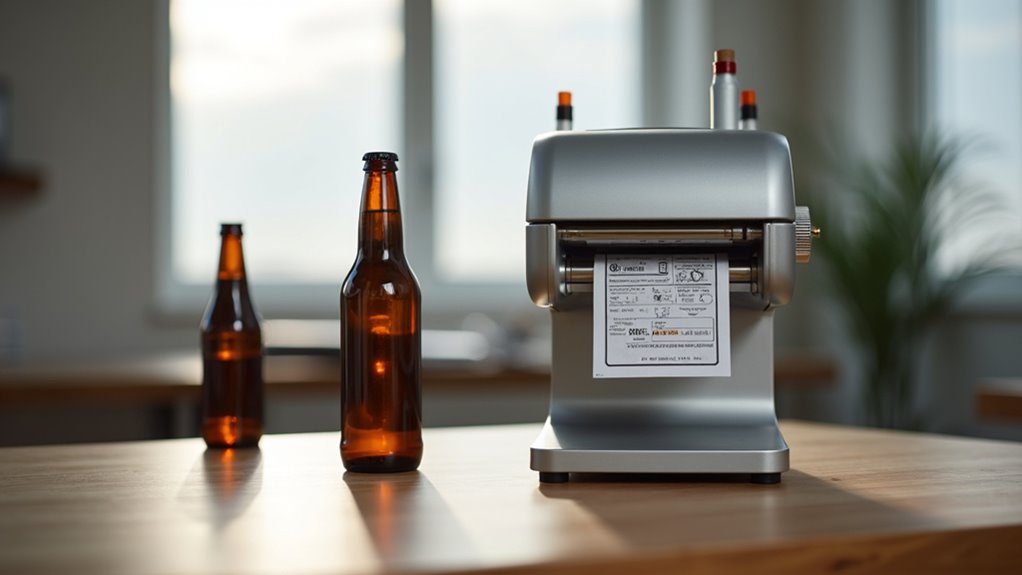
Compact benchtop labeling machines present an affordable solution for startups, offering a cost-effective entry into automated labeling without the expense of larger systems. Their design prioritizes easy operation, with straightforward setups and minimal training requirements, enabling quick integration into existing workflows. Additionally, their small footprint ensures compatibility with limited workspace environments, fitting seamlessly on benches or packing stations.
Affordable Startup Solution
For startups and small businesses entering the market, affordable labeling solutions like compact benchtop machines offer a practical entry point into efficient production. These devices, often priced under $1,000 for manual models like Zap Labeler at $449, provide significant Cost Benefits by reducing labor expenses through faster labeling—up to 10 times quicker than hand application. Funding Strategies can include allocating minimal capital for such low-cost equipment, ensuring scalability with trade-in options like BenchMATE’s 80% program.
Key advantages for startups include:
- Low Initial Investment: Manual units range from $449 to $1,400, fitting tight budgets.
- Compact Design: Tabletop models (e.g., BenchMATE at 52cm x 34cm) save space.
- Versatility: Handles various round containers (15mm-180mm diameters) for diverse products.
Easy Operation Design
Startups often find that the affordability of compact benchtop labeling machines pairs seamlessly with their straightforward operation, making them an ideal choice for businesses with limited resources and experience. These machines feature an Ergonomic Design, with intuitive touchscreens and minimal buttons like footswitches, ensuring minimal training for inexperienced users. Microprocessor-driven controls enable automation, while digital displays provide clear settings and counters for precision.
Operational simplicity is enhanced by quick setup, tool-less adjustments, and automatic label gap sensors for accuracy. Automated Alerts notify users of potential issues, preventing misaligned labels. With basic operation modes and simplified label loading, these machines support startups by reducing skill requirements and boosting efficiency through thoughtful, user-friendly engineering.
Small Space Fit
Businesses operating within constrained environments benefit significantly from the compact footprint of benchtop labeling machines, designed to occupy minimal workspace. These units, often as small as 12 x 16 inches, enable Space Optimization for startups in limited factory or home setups. Their lightweight build, starting at 13 lbs, ensures portability, while Vertical Placement on benches eliminates the need for expansive floor areas.
Key advantages for small spaces include:
- Minimal Footprint: Models like LabelOn™ Benchtop (24″L x 16″W) fit tight workstations.
- Integrated Design: Combines label holder and applicator into one compact unit.
- Stability Features: Rubber feet or clamping options secure devices without permanent setups.
Such designs cater to startups, balancing efficiency and spatial constraints with precision and cost-effectiveness.
Advanced Shrink Sleeve Applicator for Unique Designs
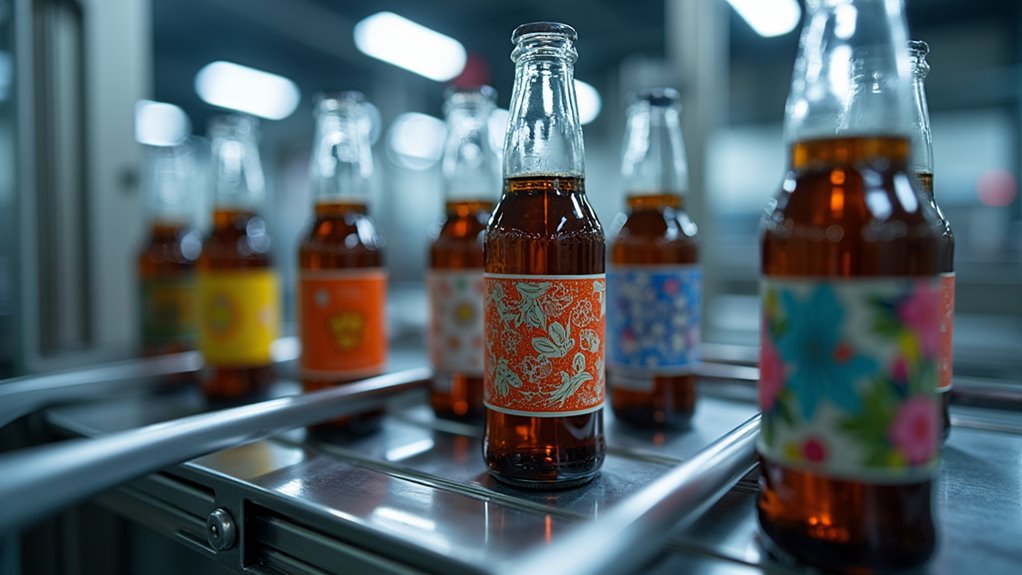
Innovative advancements in packaging technology have led to the development of advanced shrink sleeve applicators, specifically engineered for unique and intricate designs on diverse container shapes. These systems excel in Shape Handling, adeptly managing irregular and non-round containers through mechanisms like in-feed screws and orientation systems. Their Film Conforming capability ensures tight, distortion-free application, with shrink tunnels—steam or hot air—delivering uniform heat distribution for a sleek finish on complex curves and contours.
Equipped with servo motor control and PLC systems, these applicators achieve precision at high speeds, processing 60 to 800 containers per minute. They support 360-degree branding with vibrant, specialized inks and thin gauge films down to 25 microns. Mandrel-style application and quick changeovers enhance efficiency across glass, plastic, and metal containers. With trends toward sustainable materials and smart automation, these machines represent a cutting-edge solution for impactful, tailored packaging designs in 2025.
Flexible Front and Back Labeler for Diverse Containers
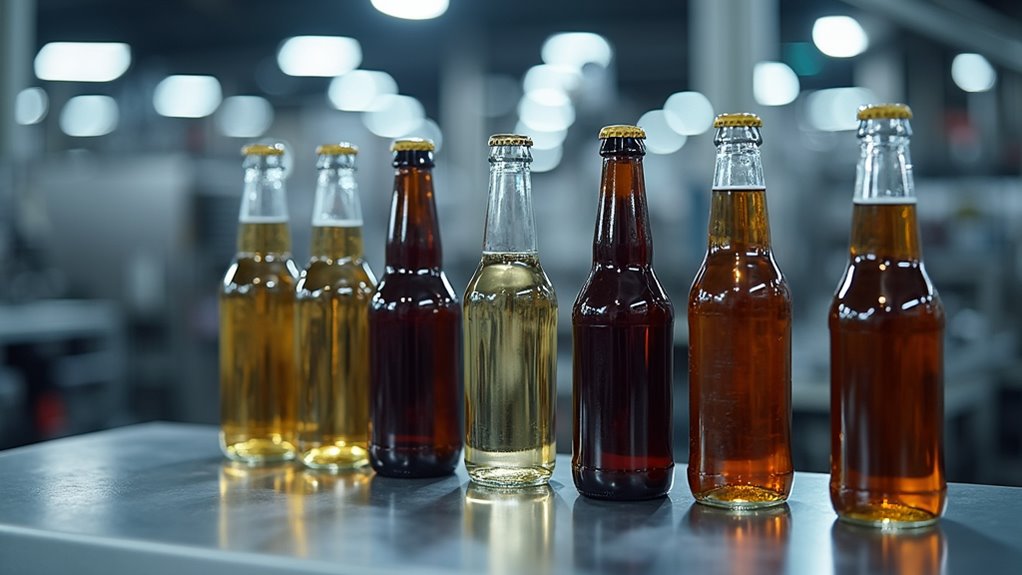
Building on the advancements in shrink sleeve technology, attention now shifts to the capabilities of flexible front and back labelers designed for diverse containers. These machines excel in handling a wide array of shapes—oval, rectangular, square, and round—while adeptly managing Protruding Surfaces and Recessed Handling challenges. They apply labels to both front and back sides simultaneously with synchronized heads, ensuring precision within +/- 1mm using servo motors and touchscreen HMIs.
Operational efficiency is notable, with speeds reaching up to 300 bpm and features like quick changeovers minimizing downtime. Their modular design integrates seamlessly into existing lines and supports various industries, from food to pharmaceuticals. Consider these key benefits:
- Shape Versatility: Accommodates irregular containers with ease.
- Labeling Accuracy: Ensures consistent placement on complex surfaces.
- High Throughput: Boosts production with rapid, automated processes.
Such adaptability makes these labelers indispensable for businesses with diverse container needs.
Smart Integrated Solution With Traceability Features
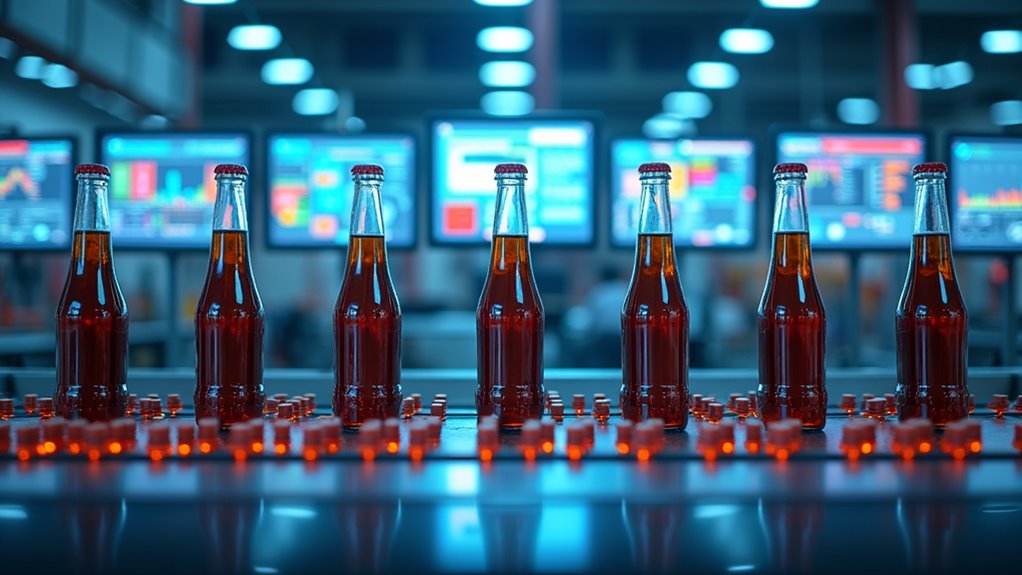
A significant advancement in bottle labeling technology emerges with smart integrated solutions that incorporate traceability features. These systems seamlessly integrate with existing packaging lines and connect to ERP or MES platforms, enabling centralized management through dedicated software. They assign unique identifiers to bottles, supporting real-time supply tracking across the chain while ensuring compliance with regulations like FMD.
Data analytics plays a critical role, as real-time data collection enhances decision-making and visibility, reducing recall costs by up to 50%. Smart technologies like QR codes and RFID tags store detailed product information and combat counterfeiting. Vision systems further ensure quality via code verification and automated rejection of errors.
Feature | Benefit | Technology Used |
---|---|---|
Traceability | Real-time supply tracking | QR Codes, RFID |
Data Management | Enhanced data analytics | Centralized Software |
Quality Control | Error reduction | Vision Systems |