Selecting the right labeling machine for bottled water production requires understanding specific needs, ensuring compatibility with bottle sizes, and setting up correctly for precise label application. Carefully prepare the workspace and bottles, including cleaning and drying, to ensure smooth label adhesion. Regular maintenance and quality checks are crucial for consistent results. Learn more to optimize the efficiency and reliability of your labeling process.
Key Points to Remember
- Choose a labeling machine compatible with your bottle sizes, shapes, and label types to ensure accurate labeling.
- Prepare a clean, organized workspace and ensure bottles are thoroughly cleaned and dried for optimal label adhesion.
- Use advanced sensors and systems for precise labeling, enhancing product aesthetics and efficiency.
- Implement maintenance and inspection protocols to identify and resolve labeling issues, maintaining quality control.
- Address common issues and optimize machine performance to maximize productivity and reliability.
Choosing the Right Labeling Machine for Your Needs
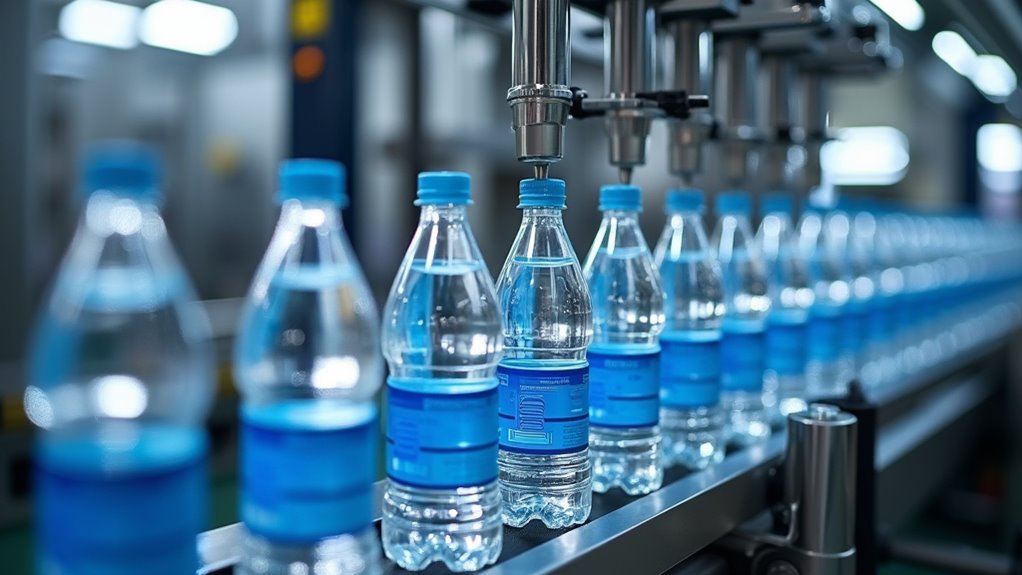
Selecting the appropriate labeling machine for bottled water production is a critical decision based on understanding the specific needs of the operation.
With various machine types, from manual to fully automatic, this choice significantly impacts production speed and efficiency. Manual machines are suitable for small-scale operations but require more labor. Semi-automatic machines offer a balance between manual control and automation, increasing speed while maintaining operator involvement. Automatic machines are ideal for high-volume production, capable of labeling over 300 bottles per minute with minimal operator intervention. In fact, some machines can label up to 500 bottles per minute with precise placement, particularly in high-speed rotary applications.
Machine compatibility with bottle sizes, shapes, and materials, as well as the type of labels used, must also be considered to ensure accurate and consistent labeling. Integration capabilities are crucial for seamless operation within existing production lines, enhancing overall efficiency and reducing downtime.
Preparing the Workspace and Bottles for Labeling
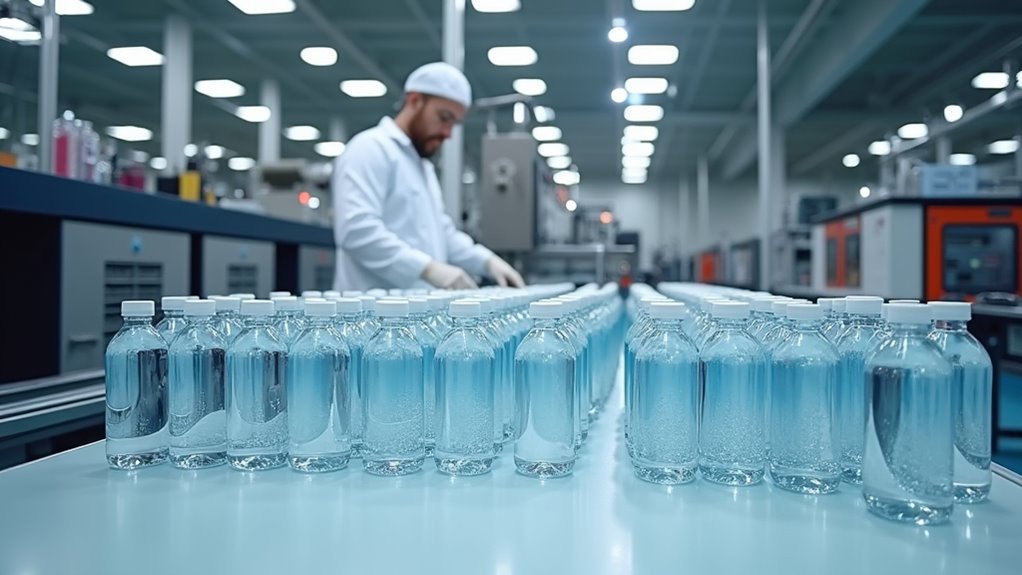
To ensure an efficient and safe labeling process, the workspace must be well-organized with a stable surface for the labeling machine, located near the production line, with adequate lighting and a clean, dust-free environment.
Bottles should undergo thorough cleaning, including an initial soak to remove dirt and old labels, internal cleaning with a bottle brush, and a final rinse to eliminate any detergent or debris.
Drying bottles with specialized equipment like air knives or bottle dryers is critical to prevent moisture-related issues, such as poor label adhesion and bacterial growth, ultimately improving the quality and output of the labeling process. Integrating advanced technology in labeling machines can ensure precise label application across various container shapes.
Essentials for Setting Up the Workspace
Creating an efficient and safe workspace is crucial for the smooth operation of labeling machines for bottled water.
Workplace ergonomics and workflow optimization are essential. The area should have a stable, dedicated surface with sufficient space for materials and finished products.
Proper lighting and a clean environment are necessary for performance and safety. Organize tools and materials to minimize downtime, using storage solutions to reduce clutter.
Implement a streamlined workflow, from bottle input to labeled output, with standardized procedures. Train staff on proper workspace usage to ensure safety and efficiency.
Regularly inspect materials and maintain machines to prevent production disruptions.
Bottle Preparation Guide
Transitioning from workspace setup to the critical steps of bottle preparation, it’s essential to ensure each bottle is properly cleaned, dried, and inspected before labeling.
The process begins with cleaning bottles to remove contaminants, which may involve spraying with a sanitizing solution or soaking in soapy water.
After cleaning, bottles must be thoroughly dried, focusing on areas like under the cap to prevent rust formation.
Next, surface inspection is conducted, checking for defects like cracks and verifying dimensional accuracy to ensure smooth label adhesion and that the final product meets quality standards.
Automated systems and trained personnel can assist in this detailed inspection process.
Setting Up Your Labeling Machine Correctly
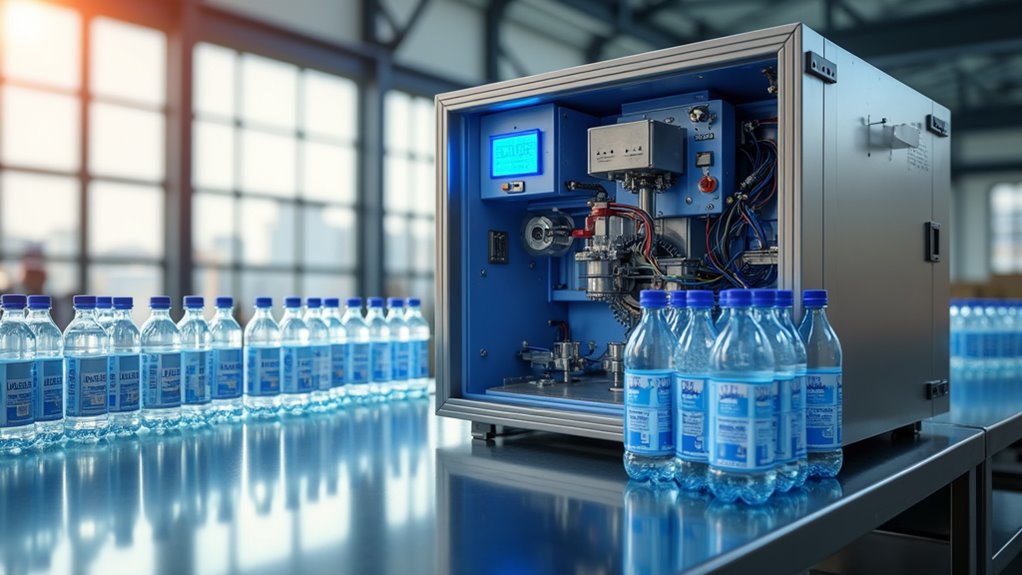
Properly setting up your labeling machine is critical to ensuring smooth and efficient label application for bottled water products. Aligning and calibrating the machine to match bottle and label sizes enhances labeling accuracy. Pre-setup checks on machine stability, environmental conditions, and component integrity are essential for consistent performance. Advanced systems with servo motors and vision sensors also contribute to precise label application.
Key Setup Steps | Purpose | Impact on Accuracy |
---|---|---|
Guide Rail Adjustment | Aligns bottles with the labeling head | Ensures correct label placement |
Labeling Head Height | Matches label position to bottle | Prevents wrinkles and bubbles |
Sensor Configuration | Detects bottles and labels | Triggers precise label application |
Proper setup not only ensures the aesthetic quality of labeled products but also optimizes machine performance, minimizing downtime and material waste.
Step-by-Step Labeling Process Guide
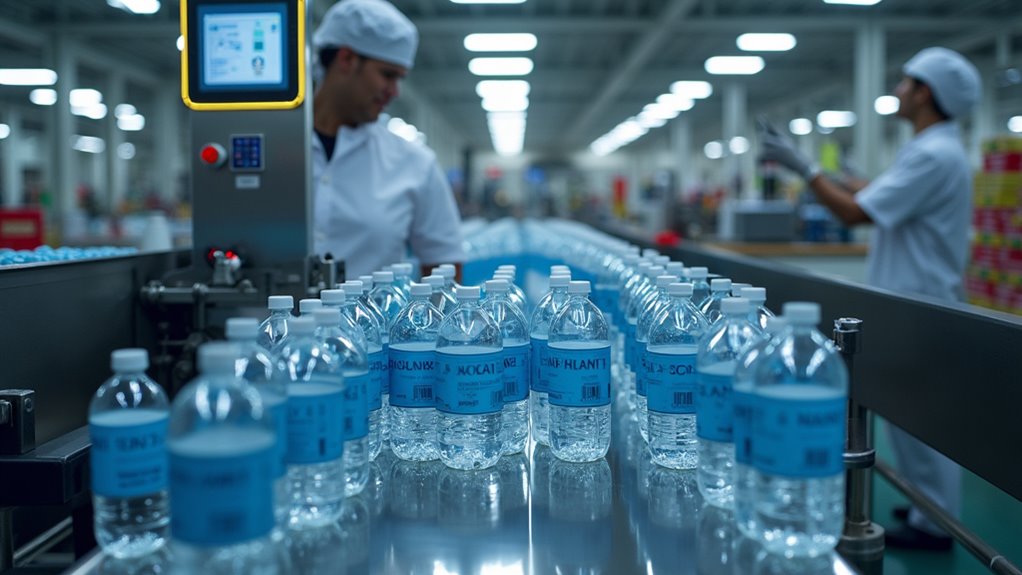
The labeling process begins with thorough preparation, ensuring both bottles and labels are ready for seamless application. This includes loading the label roll into the label feeder, adjusting gaps for stability, and guiding the label through the machine’s path.
Bottles must be cleaned and dried to ensure adhesion and prevent wrinkles or bubbles, which depends on the effectiveness of the chosen adhesive types. Label design must be compatible with the bottle’s shape and material.
After preparation, bottles are placed on the conveyor system, where sensors detect their presence to trigger precise label application. Labels are peeled from their backing and applied smoothly, with a wraparound or pressing system ensuring crease-free and bubble-free adhesion. Additionally, using automatic labeling machines can significantly improve labeling accuracy and efficiency during the process.
Ensuring Quality and Consistency in Label Application
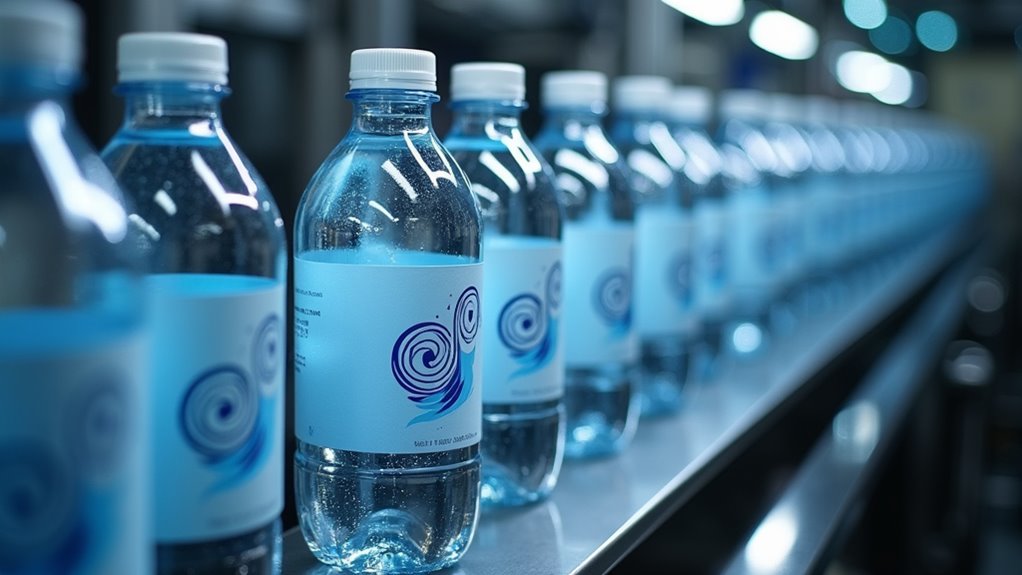
Despite the complexities of the labeling process, ensuring quality and consistency in label application is critical to maintaining a professional appearance and complying with industry standards.
Label integrity is influenced by factors such as container surface integrity, shape consistency, and cleanliness. Adhesive factors like compatibility with container material, resistance to environmental conditions, and proper storage are crucial.
Container surface integrity, shape consistency, and cleanliness significantly impact label adhesion, along with adhesive compatibility, environmental resistance, and proper storage conditions.
Additionally, using suitable label materials, such as flexible films for uneven surfaces, and addressing issues like outgassing from plastics and static buildup during application are essential.
Controlling environmental conditions and minimizing contamination further ensure that labels adhere properly, maintaining product appeal and compliance with industry standards.
Maintaining and Troubleshooting Your Labeling Machine
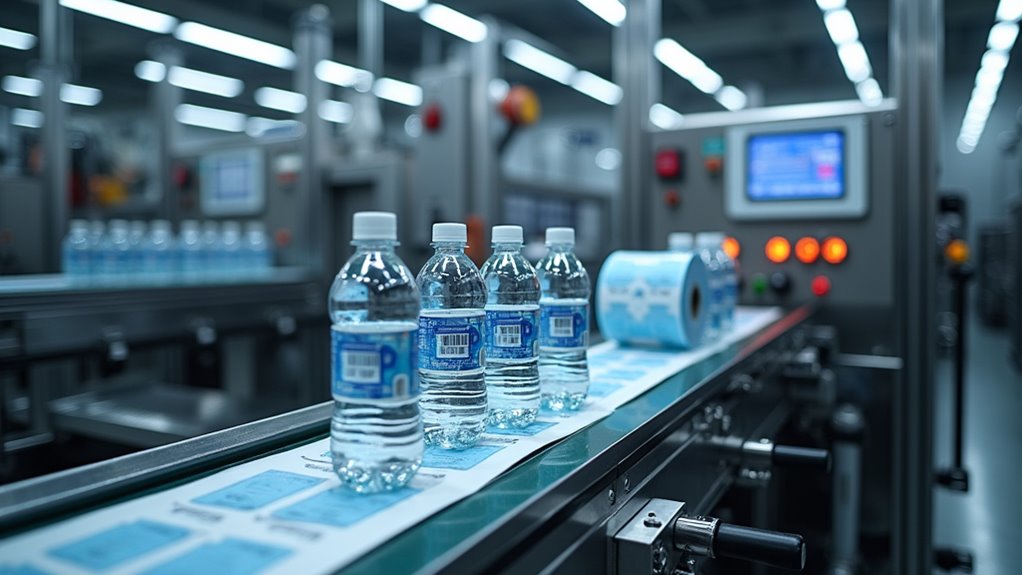
Ensuring optimal performance of the labeling machine is key to guaranteeing consistent label quality on bottled water.
Regular machine maintenance, including cleaning, lubrication, and component inspections, prevents unexpected downtime and extends machine lifespan. By following a preventive maintenance schedule, operators can identify and address potential issues before they become costly repairs.
Troubleshooting tips, such as adjusting label roll tension and checking wear on critical components like rollers and sensors, can help resolve common issues like label misalignment or poor adhesion.
Proper training on maintenance and troubleshooting procedures ensures safe and efficient operation of the labeling machine, thereby enhancing productivity and reliability in the bottled water production line.