For efficient production in 2025, top tube labeling machines excel with cutting-edge features. High-speed innovators achieve 12,000 bottles per hour, while precision-driven solutions ensure +/- 0.4mm accuracy. Versatile systems handle diverse tube types, from plastic to aluminum. Advanced automation integrates with MES for seamless data exchange, and durable designs using SUS304 steel promise longevity. These machines redefine industrial efficiency with smart sensors and servo controls. Explore further to uncover detailed insights on optimizing your production line.
Key Takeaways
- High-speed labeling machine achieving up to 12,000 bottles per hour for maximum efficiency.
- Precision-driven solution with +/- 0.4mm accuracy for flawless label placement.
- Versatile system handling diverse tube types like plastic and aluminum with ease.
- Advanced automation integrating with LIMS/MES for seamless data management.
- Durable design using SUS304 stainless steel for long-term industrial reliability.
High-Speed Labeling Innovator for 2025
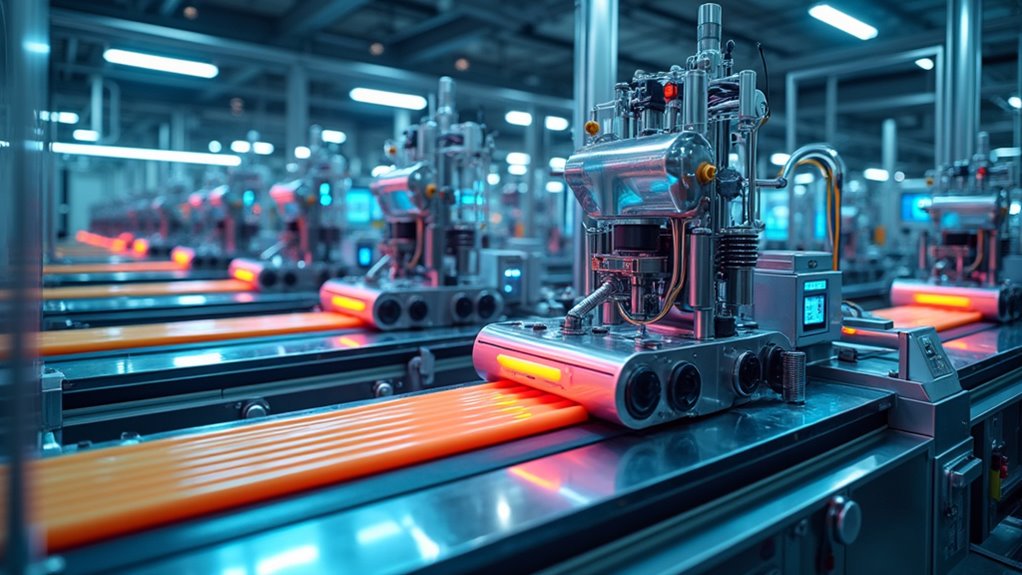
How are tube labeling machines evolving to meet the demands of high-speed production in 2025? As industries push for greater efficiency, manufacturers are integrating Speed Innovations to achieve rates up to 12,000 bottles per hour or 200 products per minute. Automated systems with features like automatic feeding and ejection minimize manual intervention, enhancing operational throughput. Advanced servo motors and clamping belt systems further boost labeling speed while maintaining stability, ensuring seamless operation under intense production demands.
Looking at 2025 Trends, integration with digital platforms like BOBST Connect enables real-time monitoring and data-driven optimization. Microprocessor-based controls and PLC interfaces offer precise process management, while automated sensors for tube detection reduce waste through mechanisms like “no tube – no label.” These technological advancements signify a shift toward smarter, faster systems, positioning tube labeling machines as critical assets in high-speed manufacturing environments, meeting the rigorous expectations of modern production lines. Additionally, automation in these machines optimizes workflows by reducing errors and ensuring compliance with stringent regulatory standards.
Precision-Driven Tube Labeling Solution
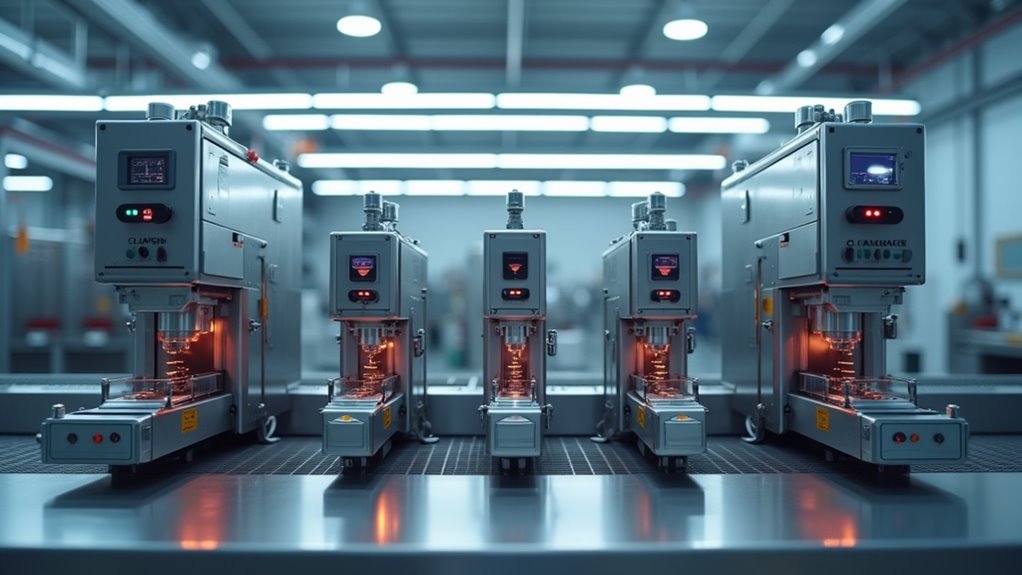
Precision in tube labeling has become a cornerstone for industries such as pharmaceuticals and cosmetics, where exact label placement is non-negotiable. The latest precision-driven tube labeling solutions achieve exceptional accuracy, often down to +/- 0.4mm, using advanced technologies like servo motors and microprocessor-based controls. These systems ensure consistent label positioning through rigorous Precision Calibration, aligning labels with tube features via sophisticated mechanisms.
Central to their performance is Sensor Accuracy, enabled by vision systems and label sensors that detect tube presence and ensure automatic registration. These machines also employ specialized rollers and secondary extrusion mechanisms to secure labels without bubbles or misalignment. Integrated digital control systems, such as PLC and HMI interfaces, allow precise parameter adjustments, while automated quality checks reduce errors. Optional vision inspection verifies label placement and data correctness, ensuring compliance and efficiency in high-stakes production environments with uncompromised accuracy.
Versatile Machine for Diverse Tube Types
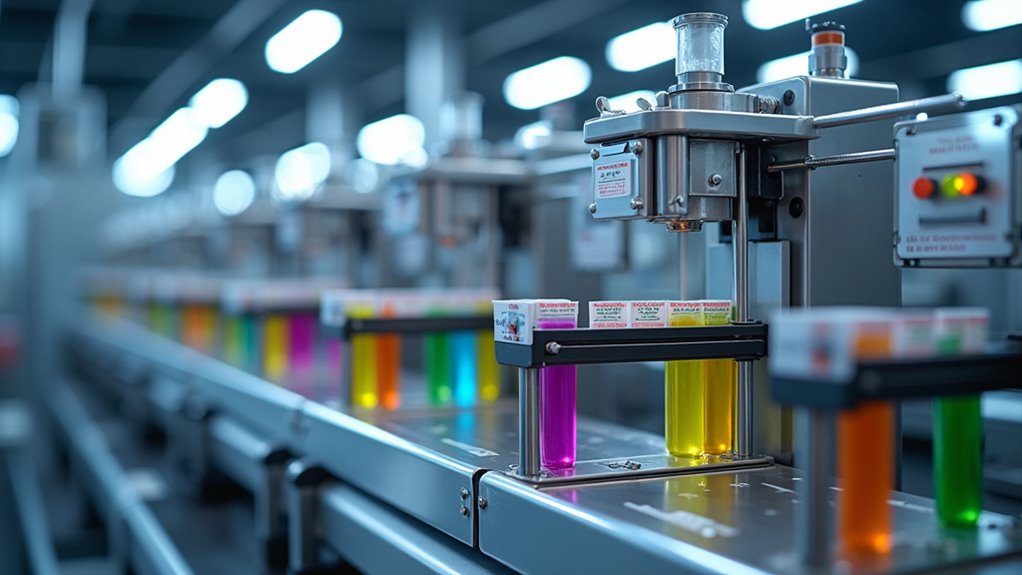
Modern tube labeling machines exhibit remarkable versatility, adeptly accommodating a wide array of tube types and materials to meet diverse industrial demands. These systems excel in handling Material Variety, processing plastic, aluminum, and soft tubes with precision, while their robust construction often incorporates food-grade aluminum and stainless steel for compliance and durability. Additionally, Shape Flexibility is a critical feature, as machines manage cylindrical, conical, and varying tube sizes from 0.5 mL to 50 mL, supported by quick-change mandrels or adjustable guides for efficient transitions.
Modern tube labeling machines showcase incredible versatility, expertly handling diverse materials and shapes to meet varied industrial needs with precision and efficiency.
Visualize the adaptability of these machines through:
- Plastic squeeze tubes gliding smoothly on adjustable conveyors.
- Rigid aluminum tubes aligned for precise 360° label registration.
- Conical containers secured by custom star wheels for accurate labeling.
- Soft tubes handled gently to prevent deformation during operation.
- Diverse tube diameters seamlessly switched in under 10 minutes using modular tooling.
This versatility ensures compatibility across cosmetics, pharmaceutical, and food industries.
Advanced Automation for Seamless Integration
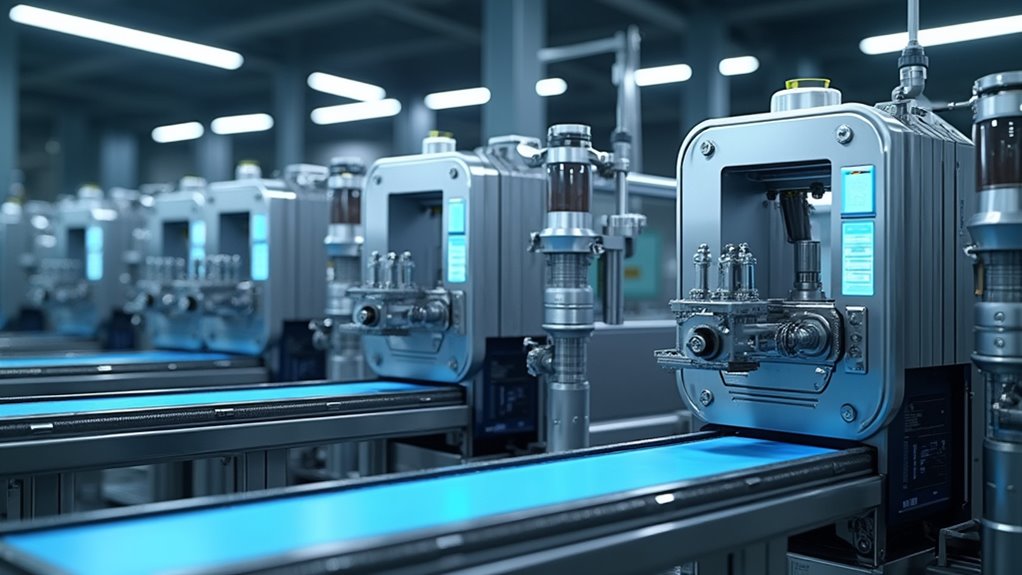
Tube labeling machines are increasingly engineered with advanced automation features to ensure seamless integration into complex production environments. These systems incorporate sophisticated connectivity, such as integration with LIMS or MES, enabling smooth data exchange and synchronization with production equipment like fillers via PLCs. Ethernet connectivity supports Remote Monitoring, allowing operators to oversee operations and troubleshoot issues from afar, enhancing efficiency.
Further, automated Data Logging ensures traceability, often adhering to regulatory standards like 21 CFR Part 11, while smart sensors and vision systems detect tube presence and validate label accuracy. Robotic integration, including compatibility with pick-and-place systems, facilitates hands-free workflows, optimizing throughput in high-volume settings. Real-time data management and HMI controls streamline process synchronization with conveyors, minimizing errors through features like “No Tube – No Label.” Embracing Industry 4.0 principles, these machines offer scalability and digital readiness, ensuring precise, automated labeling within broader manufacturing ecosystems.
Durable System for Long-Term Efficiency
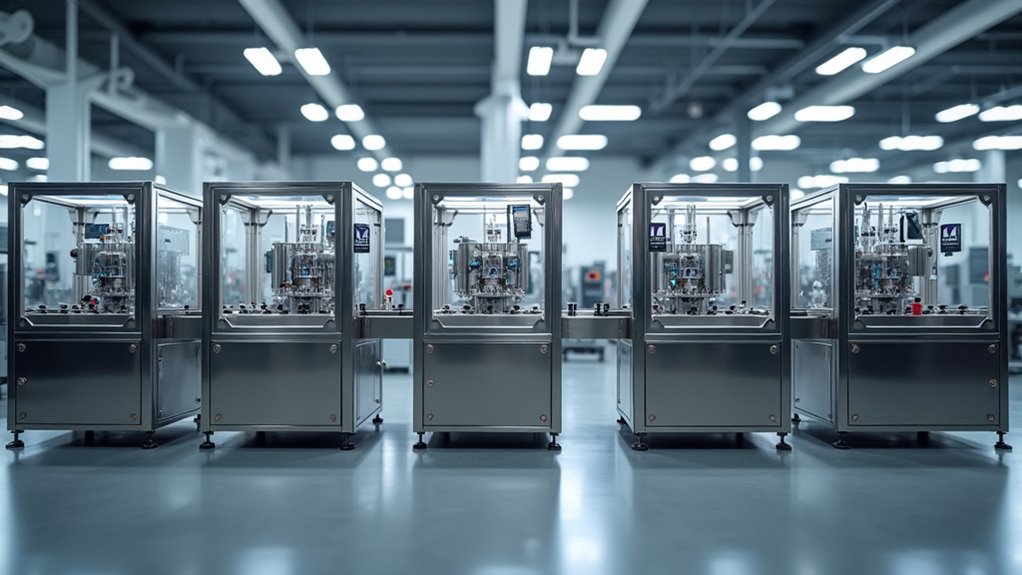
Ensuring long-term efficiency in industrial settings, tube labeling machines are engineered with robust construction to withstand the rigors of continuous operation. Built with durable materials like stainless steel (SUS304) or aluminum alloy, these systems comply with GMP standards, ensuring resilience in harsh environments. Durability Maintenance is critical, involving regular cleaning, lubrication, and inspections of wear parts like belts and seals to prevent downtime. A controlled operational environment and adherence to manufacturer guidelines further enhance longevity.
Efficiency Upgrades often integrate modular components for easy replacement, minimizing disruptions. Visualize the following aspects of these machines:
- Robust stainless steel frames gleaming under factory lights.
- Precision CNC-machined parts interlocking seamlessly during operation.
- Operators conducting meticulous daily checks on rollers and seals.
- Spare parts neatly organized for swift, uninterrupted repairs.
- Calibration tools fine-tuning label placement with exacting accuracy.
Such systematic care and build quality ensure sustained performance and reliability over years.