Belt weigh feeders are advanced devices that precisely control the flow of bulk materials by integrating a conveyor belt with a weighing system. They incorporate components such as weighbridges, speed sensors, and load cells to deliver accurate material dosing. Operating on the principle of continuous weight measurement, they adjust conveyor speed in real-time to maintain the desired flow rate, crucial for industries like mining and cement production. Understanding their components and operational fine-tuning reveals their pivotal role in enhancing industrial efficiency.
Key Points
- Belt weigh feeders are critical for measuring and controlling the flow rate of bulk materials in industries like mining and cement production.
- They integrate a conveyor belt with a weighing system, including load cells for accurate weight measurement and speed sensors for flow rate calculation.
- Key components include a weighbridge, speed sensor, mechanical weighing frame, load cells, and conveyor rollers designed to minimize weighing errors.
- Operational efficiency is achieved through continuous weight-based feeding, real-time monitoring, and adjustments to ensure consistent material flow and product quality.
- Benefits include precise material dosing and blending, improved product quality, process automation, and significant cost savings.
Understanding Belt Weigh Feeders
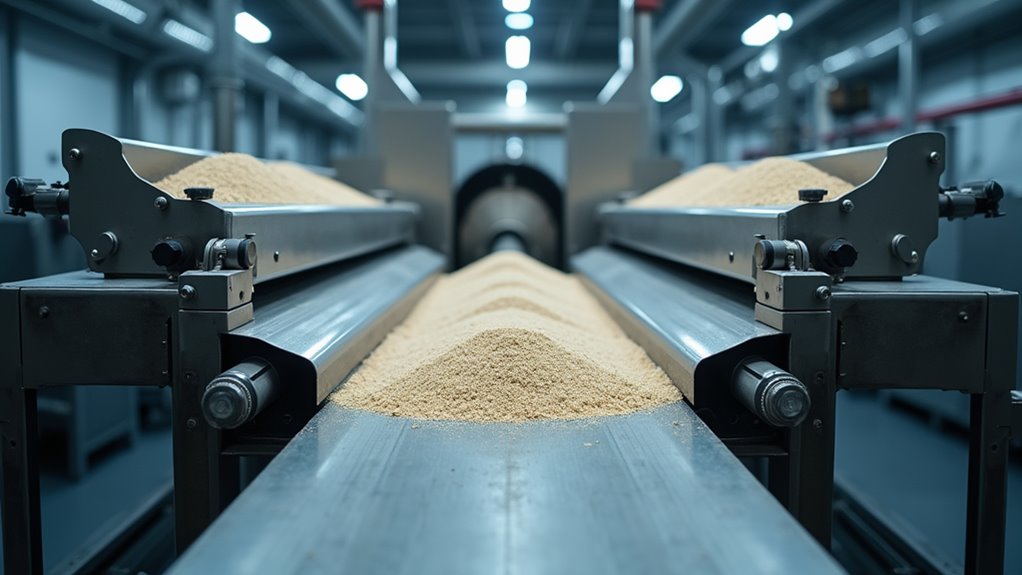
Belt weigh feeders are sophisticated devices designed to precisely control the flow rate of bulk materials in various industrial applications.
Their design integrates a conveyor belt with a weighing system, typically incorporating load cells, to accurately measure and regulate the volume of material transported.
The feeder’s design is customized to match the specific material properties it will handle, such as density, particle size, and flow characteristics, ensuring optimal performance and reliability.
The customized design of belt weigh feeders ensures optimal performance and reliability by matching specific material properties, including density, particle size, and flow characteristics.
Through continuous monitoring and adjustment of conveyor speed, belt weigh feeders maintain a consistent and accurate feed rate, essential for downstream processes requiring precise material dosing or blending.
In industries like mining and cement production, the use of belt weigh feeders is critical for maintaining product quality and optimizing production efficiency.
Key Components of a Belt Weigh Feeder
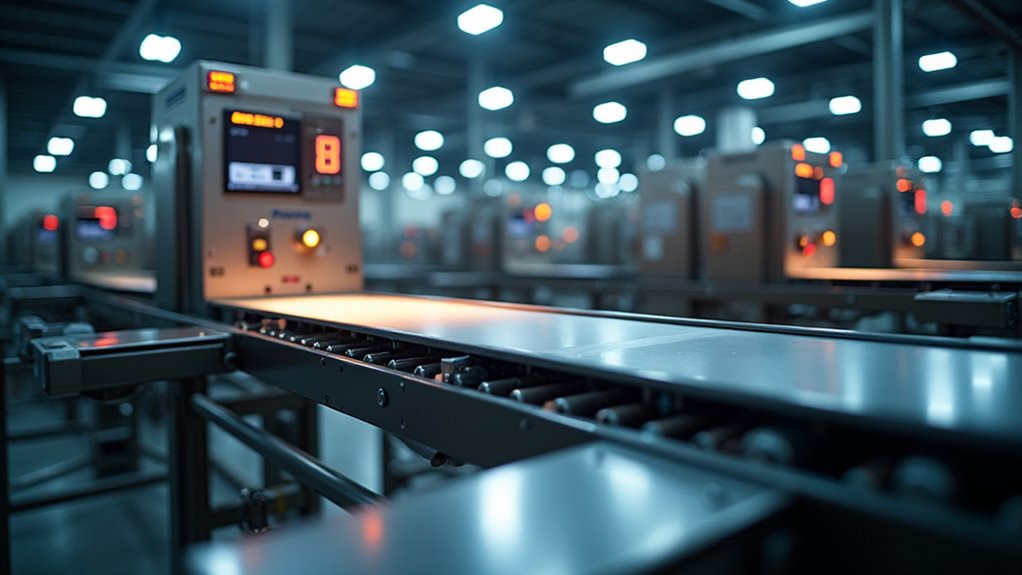
The weighbridge is a critical component of a belt weigh feeder, providing the structural support necessary for accurate weight measurement.
It is isolated from the main conveyor frame to ensure that only the weight of the material on the belt is measured.
The speed sensor, typically a high-precision rotary encoder, accurately measures the conveyor’s speed, which is crucial for determining the material flow rate.
Mechanical Weighbridge
Integral to the accuracy of a belt weigh feeder, the weighbridge consists of several mechanical components that work in unison to ensure precise continuous weighing of bulk materials.
The weighbridge frame design is critical, requiring a robust structure to support weighing rollers and load cells without deflection. Load cells, typically strain gauge types, are mounted beneath the frame, converting the force of the material’s weight into an electrical signal, requiring precise calibration for accurate weight measurement.
Weighing rollers, or idlers, within the frame are precision-machined to minimize vibrations, while the conveyor belt must maintain consistent tension to prevent weighing errors.
Speed Sensor Functionality
A critical element, the speed sensor plays a pivotal role in determining the mass flow rate in a belt weigh feeder system. It measures the velocity of the conveyor belt, providing essential data for calculating material flow.
Sensor calibration ensures accurate speed measurement, which, when combined with weight data from load cells, allows the system to precisely calculate the mass flow rate.
- Direct coupling to the tail pulley or return roller is common for accurate speed detection.
- Drag arm sensors with friction wheels provide an alternative method for precise speed measurement.
- Proximity-type sensors can be used with a rotating disc or wheel for reliable speed readings.
- Incremental encoders provide high-frequency pulses to enhance accuracy.
Proper calibration and maintenance of the speed sensor are critical for determining a stable and reliable mass flow rate.
Operating Principles of Belt Weigh Feeders
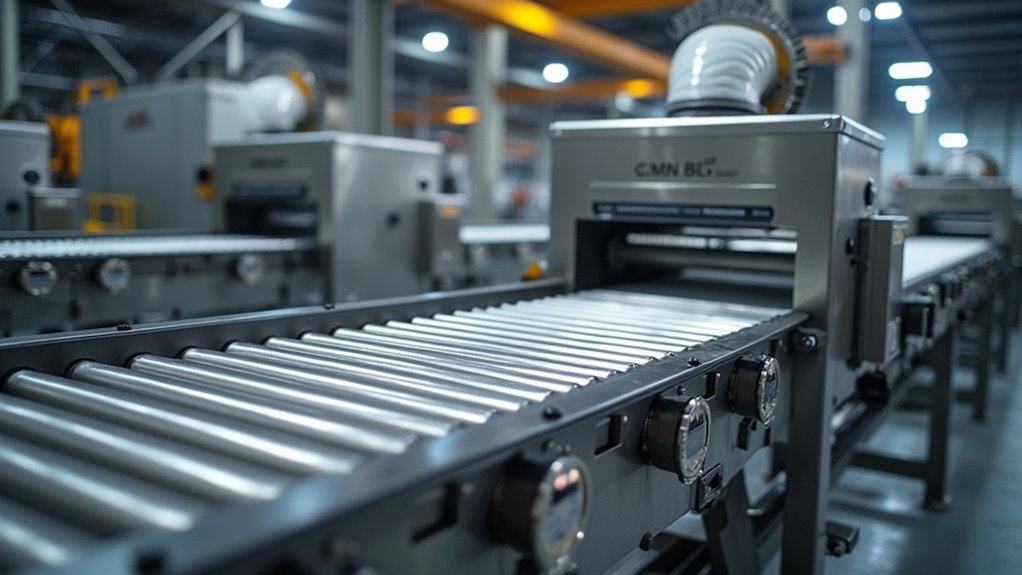
Belt weigh feeders operate on the fundamental principle of continuous weight-based feeding, accurately measuring and controlling the flow rate of bulk materials as they move along the conveyor.
This is achieved through a sophisticated integration of a weighing system, speed sensor, and controller. The load cells, critical for precise weight measurement, require regular maintenance and calibration to ensure they provide accurate data.
The system continuously calculates the mass flow rate by integrating weight measurements from the load cells with conveyor speed data. This real-time monitoring enables immediate adjustments to the conveyor speed to maintain the desired flow rate, ensuring a consistent and reliable material feed.
Applications Across Industries
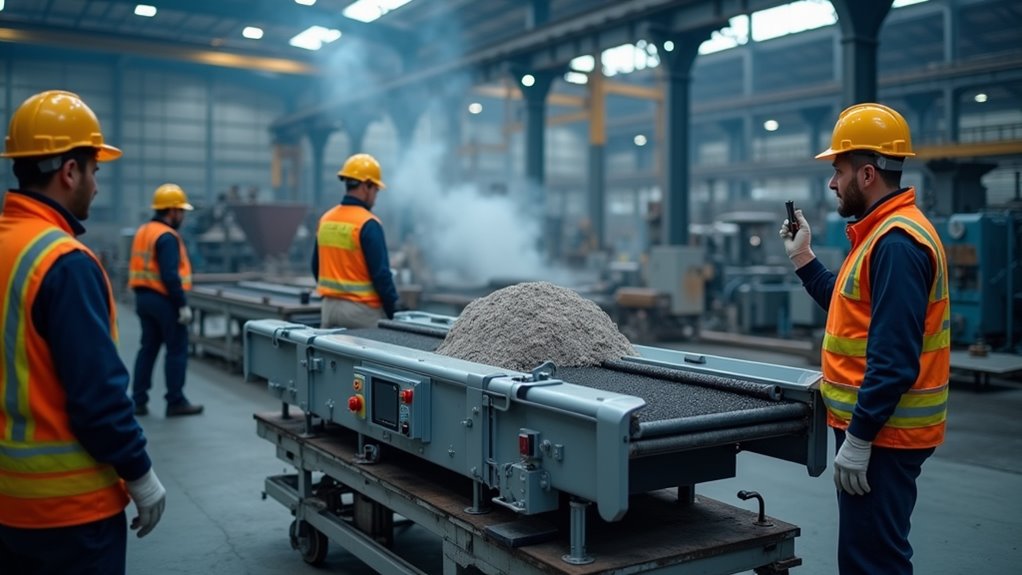
Belt weigh feeders are indispensable in numerous industries, including cement production, where they are often referred to as the “heart of the plant” due to their role in accurately dosing raw materials to ensure consistent product quality.
In the mining industry, these feeders are critical for controlling the flow of minerals and ores to processing equipment, enhancing efficiency and reducing waste by ensuring precise material feeding.
Additionally, in food processing, belt weigh feeders are used to precisely dispense ingredients for products like cereals, pet food, and baked goods, meeting stringent quality standards and contributing to enhanced production process efficiency.
Use in the Cement Industry
In the cement industry, belt weigh feeders play a critical role in ensuring accurate material dosing and process control at various stages of production.
These feeders are essential for managing the flow of raw materials, additives, and fuels throughout the cement production process.
- Controlling the feed of raw materials like limestone and clay to maintain a consistent formulation.
- Precisely dosing expensive additives to reduce waste and maintain final product quality.
- Regulating the flow of raw materials and fuel into kilns for stable operation and optimal efficiency.
- Managing the extraction and transport of hot clinker using specialized weigh feeders.
- Proportioning clinker and additives before final grinding to control mill load and cement properties.
Precision in Mining
Though often overlooked, belt weigh feeders play a pivotal role in the precision and efficiency of mining operations across various industries.
These systems ensure a continuous and uniform flow of bulk materials, optimizing the performance of equipment like crushers and ball mills. By accurately measuring and controlling the material flow rate through variable speed operation, belt weigh feeders maintain consistent output, eliminating fluctuations in feed rates that could lead to production issues or material waste.
This precise control is essential for inventory management, enabling accurate production monitoring and optimizing stock levels. Furthermore, in blending and dosing operations, belt weigh feeders ensure consistent mixture quality, guaranteeing the quality of the final product.
Through such precise material handling, mining efficiency is significantly improved.
Enhancing Food Processing
Food processing industries leverage belt weigh feeders to achieve unparalleled precision in ingredient blending and recipe management, ensuring consistent product composition and compliance with stringent quality standards.
These feeders enable:
- Optimized material use through precise measurement and control of material flow.
- Enhanced production sustainability by reducing material waste and improving process efficiency.
- Gentle handling of fragile products, minimizing degradation of items like cereals and snacks.
- Improved dosing, bagging, and packaging processes with weight-controlled feeding and high-accuracy proportioning.
- Versatility in handling a wide range of food products, from flours and pastes to candies and coffee.
The integration of belt weigh feeders in food processing not only supports quality maintenance but also enhances the sustainability of production processes.
Benefits of Using Belt Weigh Feeders
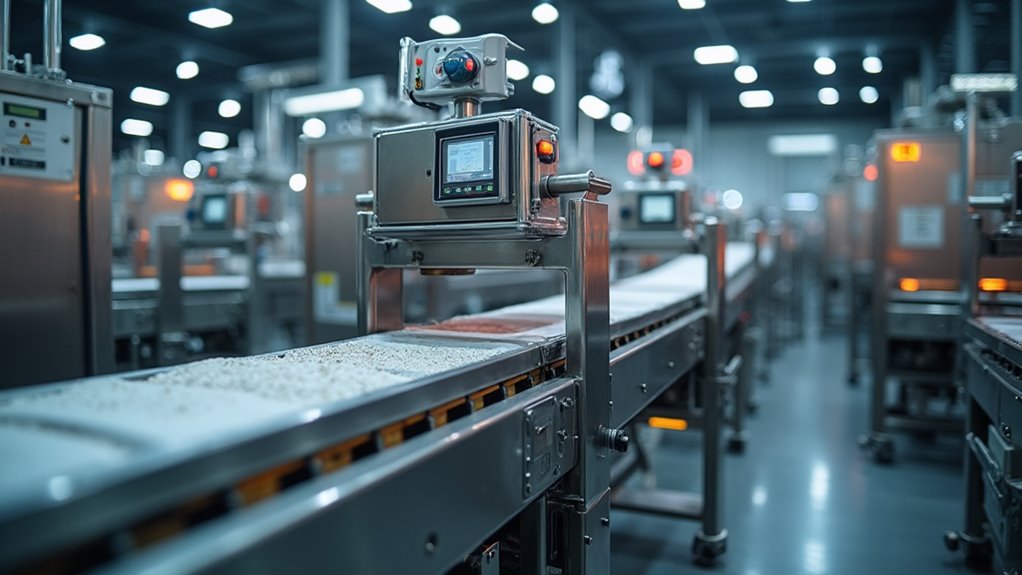
Belt weigh feeders offer numerous advantages across various industries, ensuring precise dosing and blending of raw materials. They enhance product quality by maintaining consistency and minimizing variations, critical for meeting standards in food, pharmaceutical, and chemical sectors.
Operationally, they increase efficiency by automating the feeding process, optimizing conveyor speed, and minimizing downtime, streamlining production and supply chain operations. Significant cost savings are achieved through reduced waste, lower energy consumption, and decreased labor costs.
Inventory management is improved through real-time data on material consumption, enabling proactive inventory control and efficient logistics. Additionally, integrating high-speed checkweighers enhances the accuracy and compliance of feeder systems in fast-paced production environments.
These feeders are versatile, handling a wide range of materials gently and adapting to various feed rates and configurations, including hygienic and dust-tight designs, with installation considerations and maintenance practices tailored to specific industry needs.
Ensuring Accuracy and Control in Material Flow
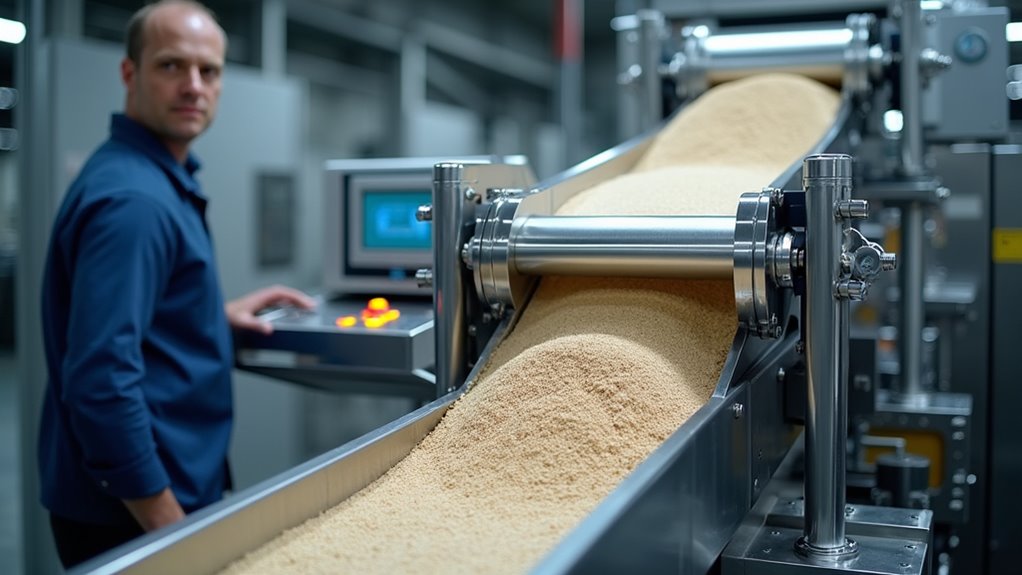
Accuracy and control in material flow are fundamental to the operational efficiency of belt weigh feeders, directly impacting the quality and efficiency of industrial processes. Advanced calibration techniques and data integrity maintenance are critical for precise feeding.
Core components and systems contributing to this accuracy include:
- Weighbridge Alignment: Ensures stable and accurate weight measurements by minimizing external forces.
- Load Cell Technology: Provides precise weight data using advanced load cells.
- Speed Sensors: Monitor and control belt speed with high-resolution devices, ensuring consistent material flow.
- Controller Processing: Integrates weight and speed data to calculate and adjust flow rates in real-time.
- Mechanical Stability: Features like consistent belt tension and structural integrity support long-term accuracy and reliability.
These elements work in synergy to ensure that belt weigh feeders maintain high levels of accuracy and control, essential for optimizing industrial processes.