Belt scale systems accurately measure the flow of bulk materials on conveyor belts, integrating load cells and speed sensors to provide real-time data. Essential in mining, agriculture, and construction, they ensure operational efficiency and product quality. Regular maintenance and calibration are critical for optimal functionality. Further exploration reveals their impact on cost efficiency and safety compliance.
Key Points
- Belt scale systems precisely measure bulk material flow on conveyors, integrating weight and speed data for real-time monitoring.
- They include a robust frame, load cells for weight measurement, speed sensors for conveyor velocity, and electronic processors for data integration.
- Critical in industries like mining, construction, and food processing for quality control, inventory management, and operational efficiency.
- Regular calibration and maintenance are essential to maintain accuracy, prevent costly errors, and ensure compliance with industry standards.
- Enhance cost efficiency and safety by reducing waste, minimizing downtime, and supporting risk management efforts in operational environments.
Understanding Belt Scale Systems
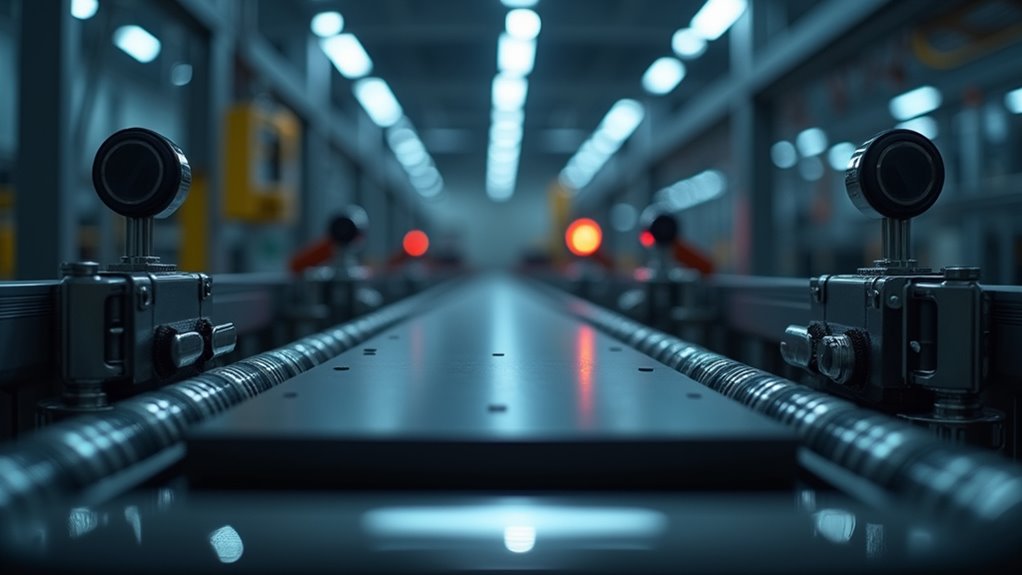
Belt scale systems are integral for accurately measuring the flow of bulk materials across various industries.
Belt scale systems: precise measurement solutions for bulk material flow, essential across industries for enhancing operational efficiency and inventory management.
These systems are designed to accurately weigh materials as they are transported on a conveyor, providing real-time data on flow rate and total weight.
By integrating the dynamics of belt movement with sophisticated flow measurement technology, belt scale systems facilitate optimal operational efficiency and inventory management.
They are indispensable in industries such as mining, construction, and food processing, where precise material flow monitoring is critical for process control and quality assurance.
Comprising a weighbridge structure, load cells, electronic processor, and conveyor speed sensor, belt scale systems calculate material flow using the equation: Weight x Speed = Rate.
Through continuous advancements in technology, belt scale systems deliver unmatched precision in dynamic bulk material weighing, ensuring smooth and efficient operations.
Components and Operating Mechanism
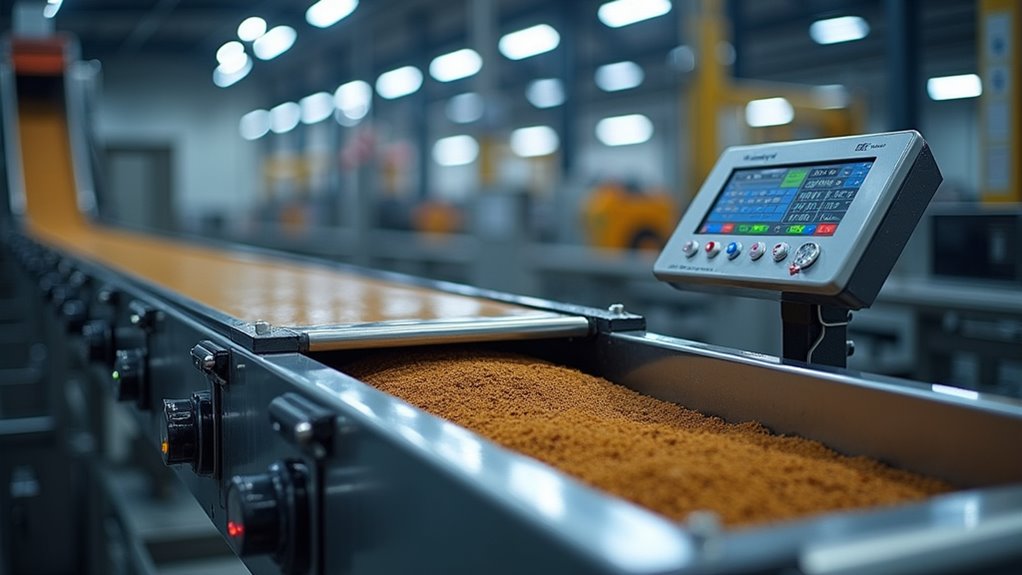
Belt scale systems operate through the seamless integration of core components.
The weighbridge and load cells form the foundation, accurately measuring the weight of materials as they pass over the conveyor. Meanwhile, the speed sensor provides real-time data on conveyor velocity, which, when combined with weight measurements in the integrator, enables precise calculation of material flow rate and total weight. Additionally, regular calibration is necessary to maintain weight accuracy across varying production speeds.
Weighbridge and Load Cells
The weighbridge and load cells are essential components of belt scale systems, providing the structural support and sensing capabilities needed for accurate weight measurement.
The weighbridge design must ensure a robust structure, typically made of steel, to support the conveyor and transmit material weight to the load cells without distortion. Various designs, including single-idler and multi-idler configurations, cater to different application needs.
Load cells, often using strain gauge technology, convert the force of the material’s weight into an electrical signal. Different load cell types, such as parallelogram designs, are selected based on their ability to minimize errors and ensure measurement linearity, critical for accurate weight calculations in bulk material handling operations.
Speed Sensor and Integrator
Integral to the precise operation of belt scale systems are the speed sensor and integrator components, each performing critical roles in the measurement and data processing sequence. The speed sensor accurately measures conveyor belt speed, with types including wheel-driven sensors, proximity sensors, and pulse generators, providing essential data for flow rate calculations.
The integrator processes signals from both load cells and speed sensors to calculate material flow rate and total weight, serving as the system’s central processing unit.
- Speed Sensor Types:
- Wheel-driven sensors make direct contact with the belt.
- Proximity sensors detect targets on rotating components.
- Pulse generators eliminate friction-related wear.
- Integrator Functions:
- Processes weight and speed signals to calculate flow rate.
- Displays real-time operational data.
- Interfaces with control systems and peripheral devices.
- Enables system calibration and diagnostics.
Key Applications Across Various Industries
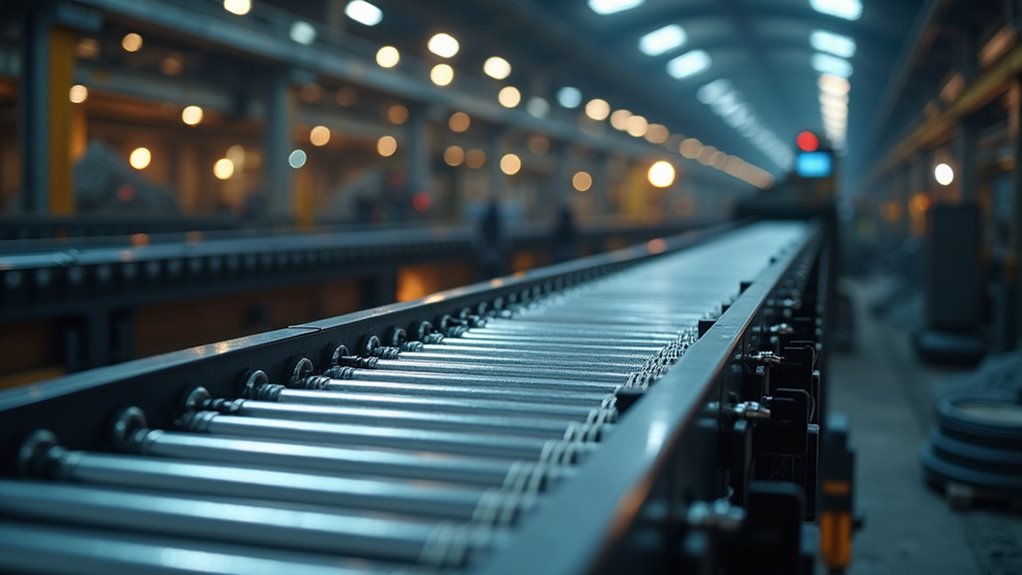
Across various industries, belt scale systems play a pivotal role in enhancing operational efficiency, ensuring product quality, and supporting regulatory compliance.
In sectors such as mining and quarrying, agriculture, construction, food processing, and recycling, these systems monitor and control material flow from extraction to processing. They ensure accurate measurements for sales, inventory management, and quality control, whether handling ores in mining, grains in agriculture, or ingredients in food processing.
By providing accurate, real-time data, belt scale systems aid in stockpile management, optimize production processes, and ensure compliance with industry standards and environmental regulations. This functionality supports both operational excellence and regulatory compliance across diverse industrial sectors.
Benefits of Implementing Belt Scale Systems
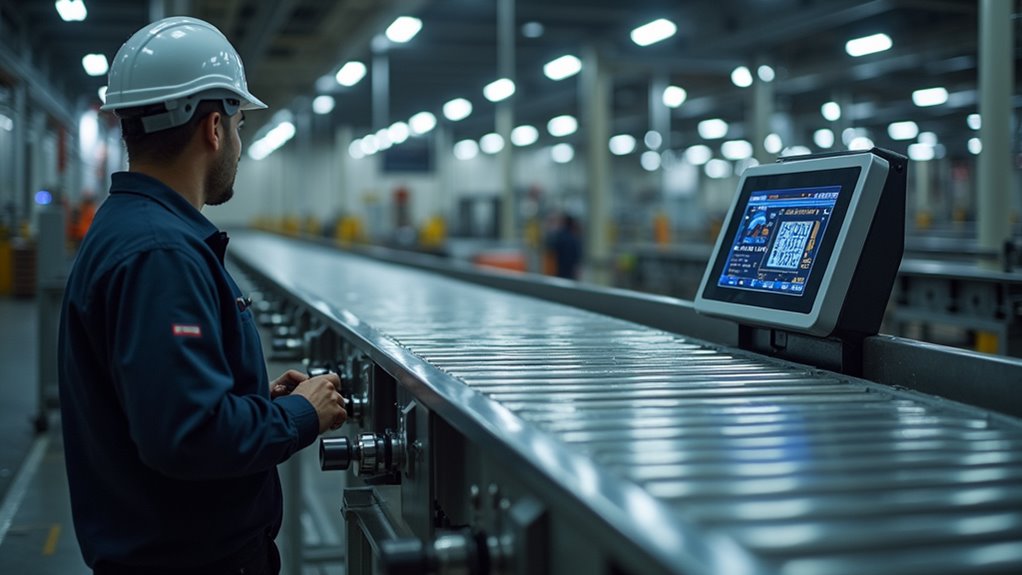
Implementing belt scale systems delivers significant benefits, enhancing operational efficiency across various industries.
These systems provide continuous, real-time data on material flow, enabling precise inventory tracking and production process control.
Key benefits include:
- Enhanced Operational Efficiency: Automates material handling, reduces manual labor, and optimizes conveyor speed, leading to minimal downtime and increased throughput.
- Improved Process and Quality Control: Ensures consistent product quality through precise dosing and blending, maintaining compliance with weight-related standards.
- Significant Cost Savings: Minimizes material loss, reduces labor costs, and prevents equipment damage, resulting in lower operating costs.
- Accurate Inventory Management: Facilitates real-time inventory monitoring, improving stock accounting and supporting advanced production planning, enhancing overall cost efficiency.
Factors Affecting Accuracy and Performance
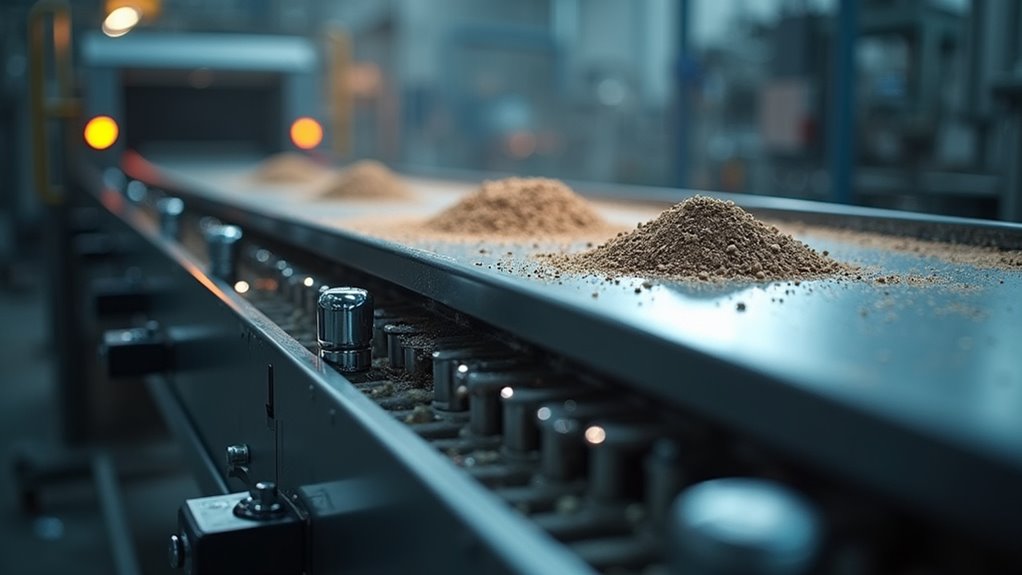
While the benefits of implementing belt scale systems are clear, understanding the factors affecting their accuracy and performance is key to optimizing their use.
Precise idler alignment is essential to prevent measurement errors, as even a fraction of an inch misalignment can cause significant inaccuracies.
Idler alignment is critical for belt scale accuracy; even minor misalignment can lead to significant measurement errors.
Additionally, maintaining consistent belt tension is crucial, as variations can impact weighing accuracy by up to 10 percent.
Proper conveyor condition and structural integrity also play a significant role.
Any deviation from optimal conditions, such as excessive belt sag or structural deflection, can lead to inaccuracies, emphasizing the importance of regular maintenance and calibration for reliable performance.
Maintenance and Calibration for Optimal Operation
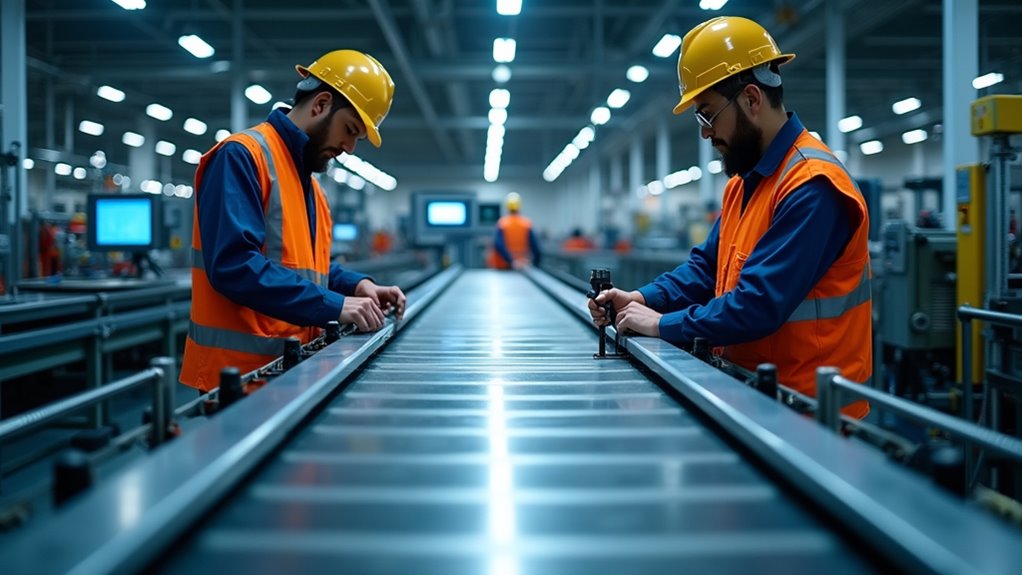
Regular inspection and maintenance of belt scale systems are critical to ensuring continuous accuracy and reliability.
Professional servicing, performed by certified technicians, provides the benefits of advanced diagnostics and precise calibration, essential for maintaining optimal system functionality.
These practices not only extend the operational lifespan of the equipment but also significantly reduce the likelihood of costly downtime and inaccurate measurements.
Importance of Regular Inspections
Regular inspections and calibration are essential for maintaining the optimal functionality of belt scale systems.
Routine checks ensure mechanical reliability by identifying and addressing issues such as debris buildup, component wear, and sensor malfunctions. Consistent calibration ensures accurate weight measurements, critical for efficient operations and product quality.
To maximize system performance and durability, the following practices are recommended:
- Conduct daily inspections to remove debris and check for visible damage or wear on the belt, weighbridge, and idlers.
- Regularly clean and inspect speed sensors to ensure accurate belt speed readings.
- Perform frequent zero calibrations, ideally daily, to account for changes in belt tension.
- Schedule regular monthly calibrations to maintain system accuracy over time.
Benefits of Professional Servicing
Professional maintenance of belt scale systems delivers numerous benefits for sustaining optimal functionality.
Adhering to recommended service frequencies and calibration standards ensures the system consistently provides accurate and reliable weight measurements. This precision is critical for inventory management, production planning, and cost control, preventing costly errors in billing and material ordering.
Regular maintenance also extends equipment lifespan, minimizes downtime, and reduces repair costs by identifying potential issues early.
Furthermore, it ensures compliance with regulatory standards, enhances workplace safety, and optimizes production processes.
Regular professional maintenance and calibration are indispensable for maximizing the efficiency and productivity of belt scale systems.