Warehouse Management System (WMS) software is a digital tool designed to optimize warehouse operations. It manages inventory, tracks goods, and coordinates daily tasks with precision. WMS provides real-time visibility into stock levels, supports barcode scanning, and integrates with other systems like ERP for seamless data flow. This technology enhances efficiency, reduces errors, and lowers operational costs through automation. For those seeking deeper insights, exploring further will uncover additional benefits and functionalities of WMS solutions.
Key Takeaways
- WMS software is a digital tool that optimizes warehouse operations from inventory entry to exit.
- It provides real-time visibility into stock levels and locations for efficient management.
- WMS supports barcode scanning and RFID for accurate inventory tracking.
- It enhances productivity by automating tasks like picking and task allocation.
- WMS integrates with ERP and TMS for seamless supply chain operations.
Understanding Warehouse Management Systems
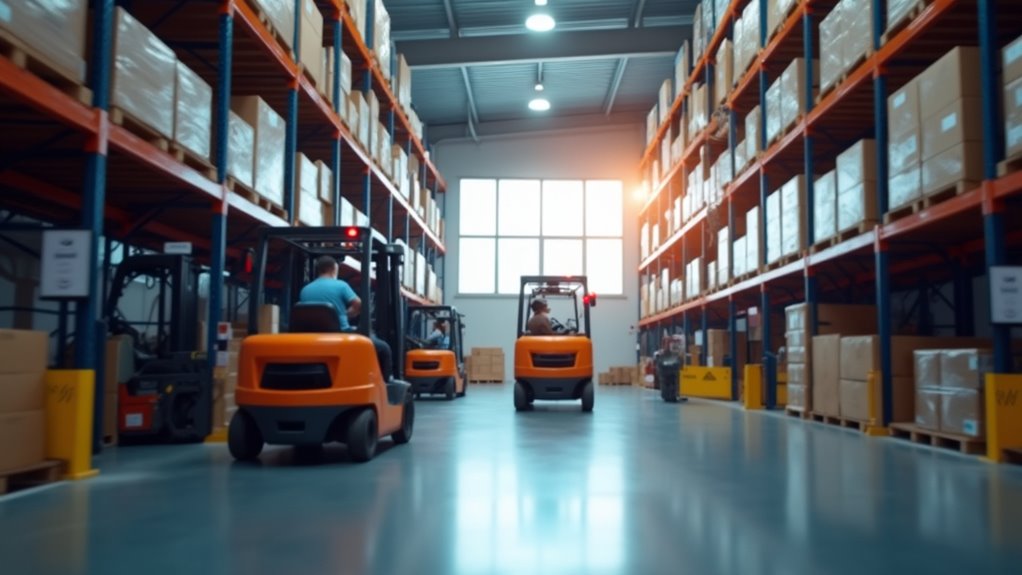
While warehouses are critical hubs in the supply chain, their efficiency hinges on sophisticated tools like Warehouse Management Systems (WMS). These software applications manage daily operations in warehouses and distribution centers, overseeing processes from goods entry to exit. Their primary purpose is to optimize workflows, ensuring materials move cost-effectively and efficiently, linking physical inventory to digital records as a backbone of supply chain management. Additionally, WMS provides real-time inventory data to support quick decision-making and maintain accuracy in stock levels.
Delving into WMS History, these systems emerged in the late 20th century as basic inventory tracking tools, evolving with technology into comprehensive platforms addressing modern warehousing complexities. Today, they are indispensable for businesses facing high volumes and diverse SKUs. Looking at Emerging Trends, WMS solutions are increasingly adopting cloud-based models for scalability and integrating with robotics and augmented reality to enhance operational precision. This evolution reflects the growing demand for real-time data and adaptability in dynamic supply chain environments.
Core Features of WMS Solutions
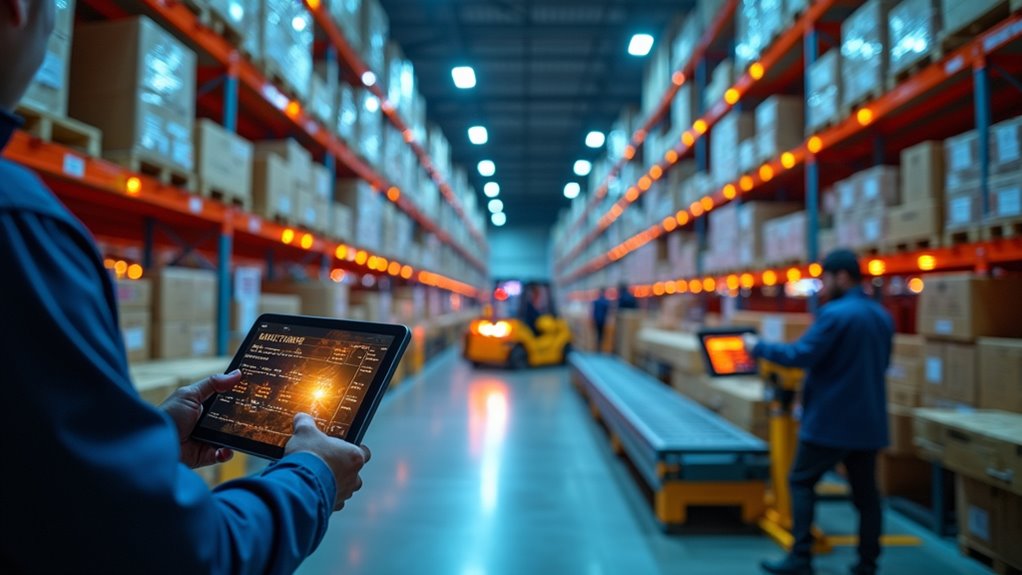
A robust Warehouse Management System (WMS) is defined by its core features, which streamline warehouse operations with precision and efficiency. Central to these is Inventory Tracking, offering real-time visibility into stock levels, locations, and status. It supports automated updates, barcode scanning, and RFID integration to ensure accuracy and prevent discrepancies through cycle counting and detailed tracking of SKUs, batches, and expiration dates.
Another critical component is Order Fulfillment, which optimizes outbound logistics through systematic order management and execution. WMS solutions facilitate various picking strategies like wave and zone picking, while automating task assignments and optimizing routes for efficiency. They also manage packing operations and support value-added services such as kitting and labeling. Additionally, features like inbound receiving, putaway rules, shipping automation, yard management, labor tracking, and system integration with ERP and TMS platforms ensure a cohesive operational framework, enhancing overall warehouse functionality.
Benefits of Implementing WMS Technology
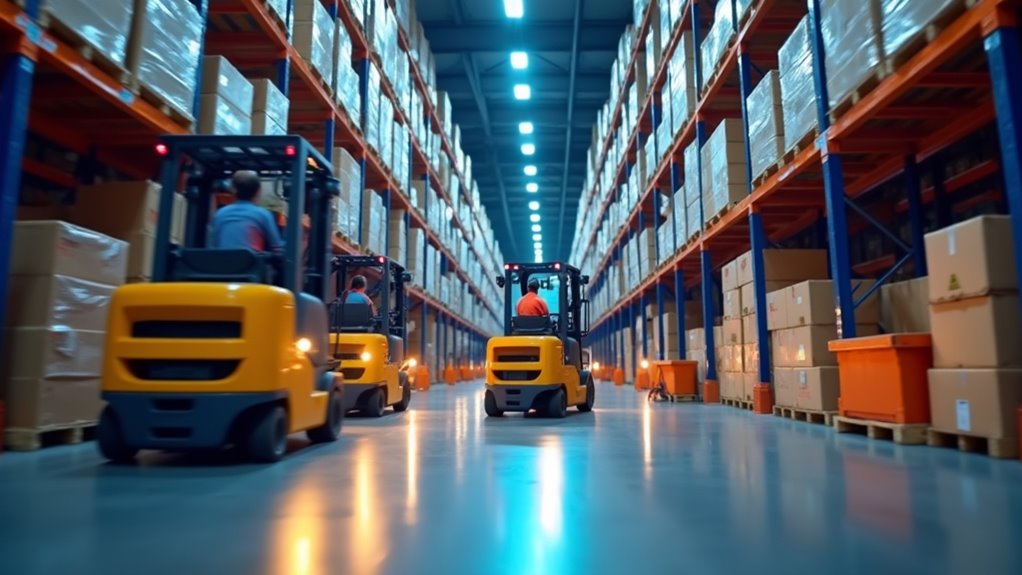
Implementing Warehouse Management System (WMS) technology delivers transformative advantages for organizations seeking to optimize warehouse operations. By leveraging real-time data and automation, WMS ensures precise inventory tracking, minimizing errors and enhancing visibility into stock levels and movements. This accuracy supports better demand forecasting and traceability, reducing stockouts and overstocking risks.
Operationally, WMS drives a significant Productivity Boost by automating tasks like picking and shipping, optimizing workflows, and reducing travel time through advanced picking strategies. This results in higher throughput and order accuracy. Additionally, WMS contributes to Cost Reduction by cutting labor expenses through efficient task allocation and minimizing errors that lead to returns or write-offs. Optimized space utilization and reduced inventory carrying costs further enhance savings, with studies indicating operational cost decreases of 20-35%. Moreover, real-time analytics enable data-driven decisions, identifying bottlenecks and improving labor management for sustained efficiency gains.
Exploring Different Types of WMS Platforms
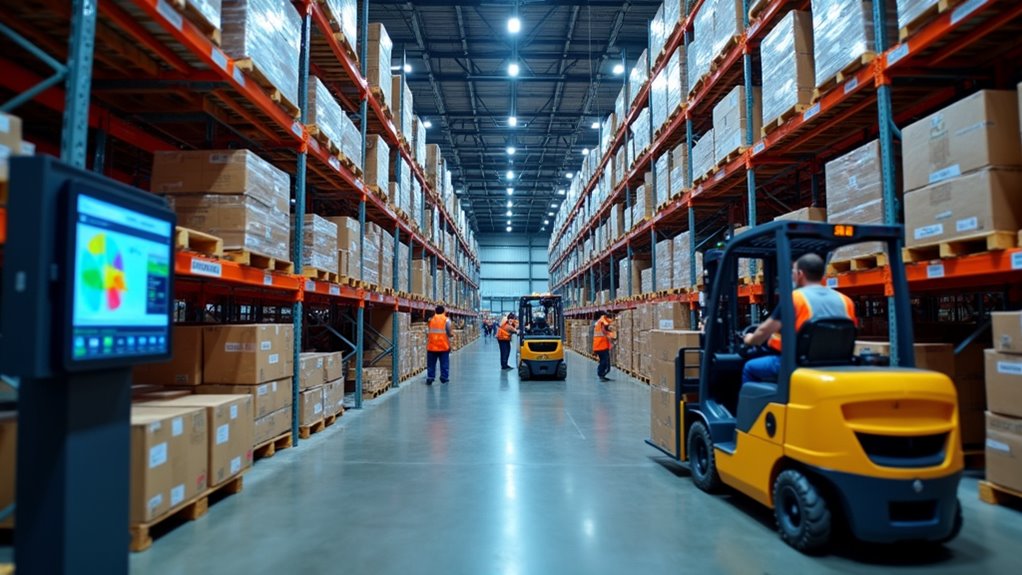
Various Warehouse Management System (WMS) platforms cater to diverse organizational needs, offering distinct functionalities and deployment models. In a Types Comparison, standalone WMS solutions focus on specialized warehouse functions, ideal for SMBs, while integrated WMS modules within ERP or SCM systems ensure seamless data flow across business operations. Cloud-based WMS offers scalability and lower initial costs via a subscription model, contrasting with on-premise WMS, which provides greater control but demands significant upfront investment and maintenance.
Additionally, tiered WMS platforms vary by complexity, from basic Tier 3 systems for single warehouses to robust Tier 1 solutions for intricate networks. Reflecting on Platform History, early WMS systems were predominantly on-premise, evolving over time to include cloud and integrated options to meet modern scalability and connectivity demands. Each type serves specific operational scales and budgets, requiring careful evaluation to align with organizational objectives and infrastructure capabilities.