A Warehouse Management System (WMS) is specialized software that oversees daily warehouse operations with precision. It optimizes tasks like receiving, inventory tracking, order picking, packing, and shipping through automation and real-time data. By integrating technologies such as barcode scanning and RFID, WMS ensures accurate inventory control and efficient workflow. It also supports performance analytics for data-driven decisions. Exploring further unveils deeper insights into its transformative impact on supply chain efficiency and operational success.
Key Takeaways
- WMS, or Warehouse Management Software, is specialized software for managing daily warehouse operations efficiently.
- It provides real-time inventory visibility to track goods and streamline processes.
- WMS optimizes tasks like receiving, picking, packing, and shipping through automation.
- It enhances accuracy using barcode scanning or RFID for inventory control.
- The software boosts productivity by automating manual tasks and optimizing workflows.
Understanding WMS Warehouse Software
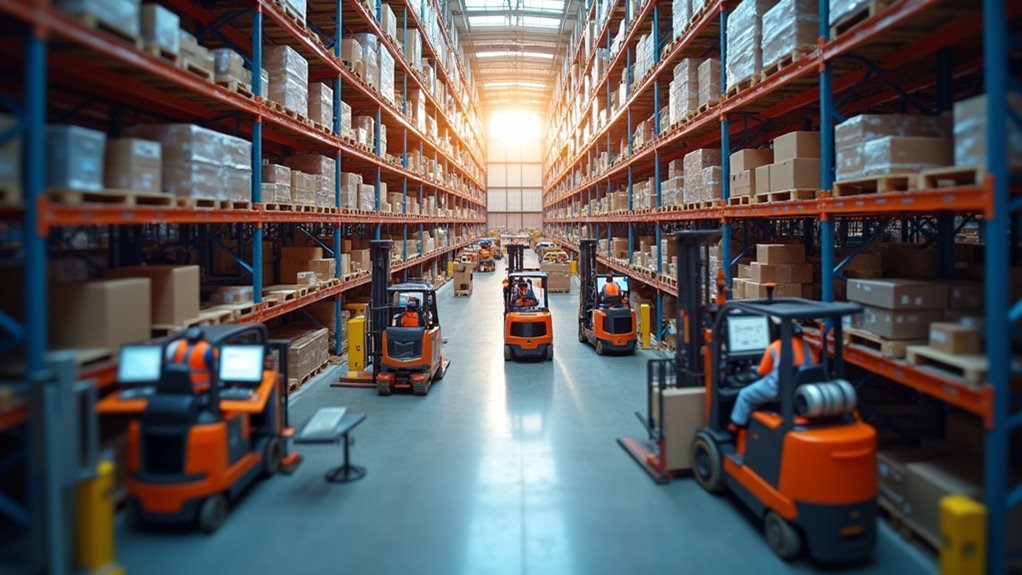
A Warehouse Management System (WMS) is a specialized software solution engineered to oversee and optimize daily warehouse operations. It serves as a critical tool in supply chain management, ensuring efficient movement of goods by providing real-time inventory visibility and streamlining processes. The WMS History traces back to the late 20th century when early systems emerged to address manual inefficiencies in inventory tracking, evolving with technology into sophisticated platforms integrating automation and analytics. By automating key processes, a WMS significantly enhances warehouse efficiency by reducing task time.
Despite its advantages, implementing such systems faces significant Adoption Barriers. High initial costs, especially for standalone or on-premise solutions, deter smaller enterprises. Additionally, the complexity of integration with existing infrastructure poses technical challenges. Resistance to change among staff, coupled with the need for extensive training, further complicates deployment. Overcoming these hurdles requires strategic planning and investment, as the long-term benefits of enhanced efficiency and accuracy often outweigh the initial obstacles in modern warehousing environments.
Core Operations of WMS in Warehouses
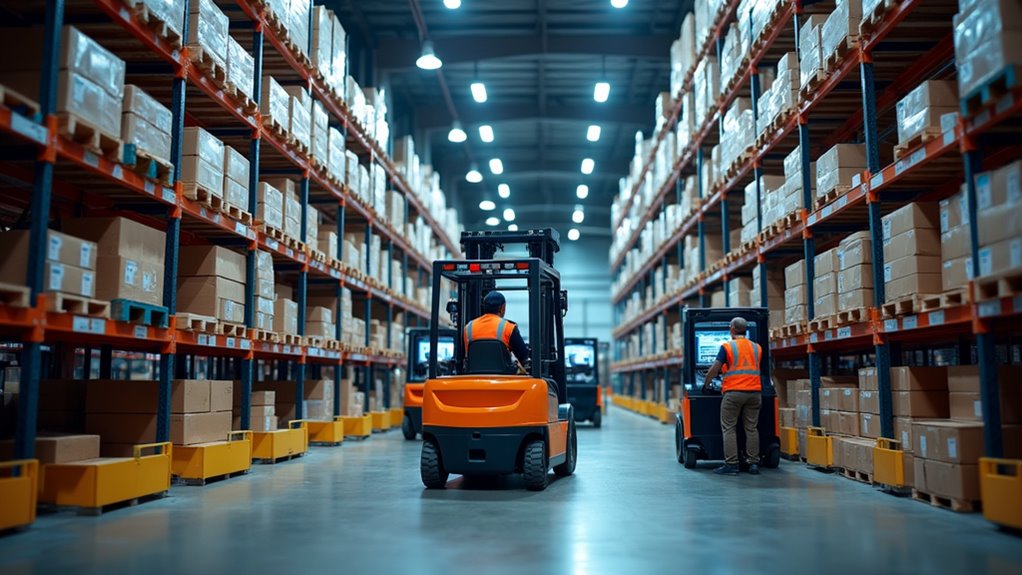
Observers of warehouse management systems will note that beyond the initial challenges of adoption, the true value of WMS lies in its ability to refine and control key operational functions within a warehouse. A WMS optimizes receiving by automating shipment verification and directing Putaway Strategies, using rules based on product attributes and space availability to assign storage locations efficiently. It enhances inventory control with real-time tracking via barcode or RFID, ensuring accuracy through cycle counting and stock rotation methods like FIFO.
Additionally, a WMS streamlines order picking by generating optimized routes and supporting diverse picking methods, minimizing errors through scanning verification. It coordinates packing and shipping by automating label generation and integrating with transportation systems. In Returns Handling, it manages reverse logistics by tracking returned items, guiding disposition decisions, and updating inventory, thereby reducing labor costs and maintaining data precision across operations.
Key Features and Benefits of WMS
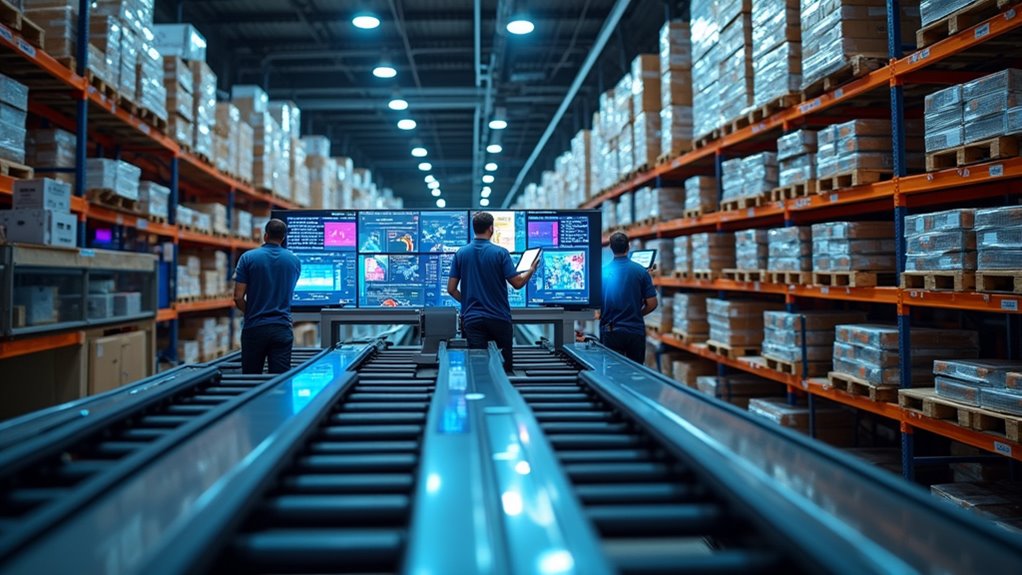
Warehouse Management Systems (WMS) offer a robust suite of features designed to enhance operational efficiency and accuracy across diverse warehouse environments. These systems deliver critical Feature Benefits by optimizing inventory tracking with real-time visibility, ensuring precise stock levels through cycle counting, and reducing errors via barcode scanning. The Efficiency Gains are evident in streamlined order fulfillment, where automated picking and packing processes minimize mis-shipments, and labor management tools optimize task allocation and travel paths, cutting operational costs.
Key highlights of WMS capabilities include:
- Space Optimization: Analyzes warehouse layout to suggest ideal storage, maximizing floor usage.
- Performance Analytics: Provides KPI reports and data-driven insights for strategic decision-making.
- Labor Productivity: Automates manual tasks, boosting worker output and morale.
Through these features, WMS drives significant cost reductions and accuracy improvements, positioning warehouses to meet modern demands with precision and agility.
Types and Integration Options for WMS
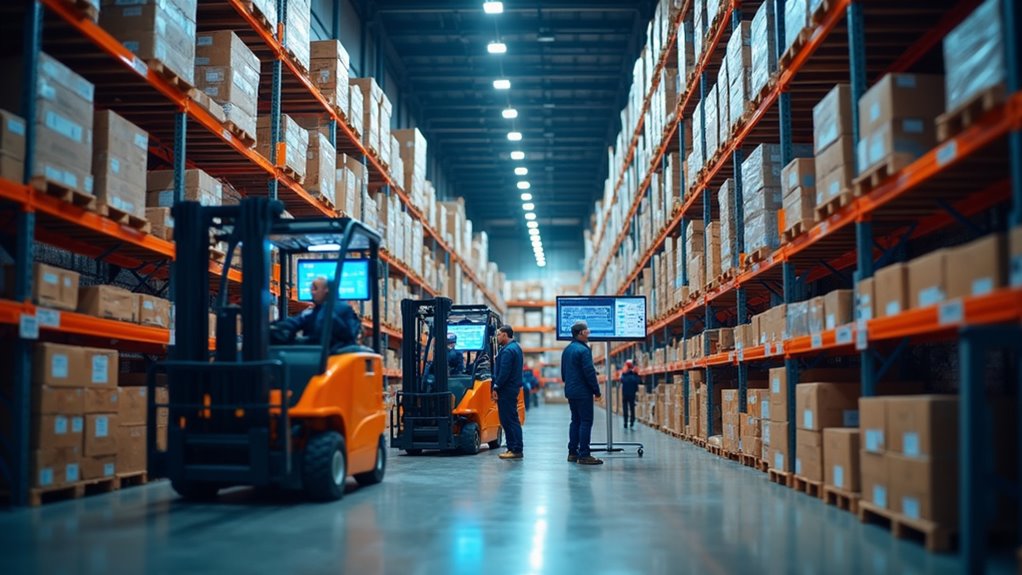
Navigating the landscape of Warehouse Management Systems reveals a diverse array of options tailored to varying operational needs and business scales. WMS solutions are categorized into four types: Standalone, focusing on specialized warehouse operations; SCM Modules, embedding warehouse functions within broader supply chain oversight; ERP Modules, integrating with enterprise-wide processes like finance; and Cloud Types, hosted remotely with scalability and subscription-based access via SaaS models, reducing upfront costs.
On the integration front, WMS employs various Integration Methods to ensure seamless connectivity. APIs, EDI, web services, and direct database links facilitate data exchange with systems like ERP for inventory updates, TMS for shipping optimization, OMS for order fulfillment, and Material Handling Equipment for operational efficiency. These methods enable real-time synchronization across platforms, enhancing visibility and control. Businesses must evaluate WMS types and integration capabilities to align with operational demands and strategic objectives, ensuring robust warehouse management.