For businesses seeking top sticker labeling machines in 2025, consider the NCT 21200 for high-volume efficiency, CED TB100 for versatile self-adhesive labeling, PBTB 160 for precise fully automatic operation at 120–130 bottles per minute, PA7100 for industrial print-and-apply reliability, HERMA 362E for high-speed side labeling up to 200 products per minute, HERMA 152E for wrap-around cylindrical labeling, and other innovative solutions. Explore further to uncover detailed insights into optimizing your production needs.
Key Takeaways
- NCT 21200 offers high-performance self-adhesive labeling for high-volume environments with consistent application.
- PBTB 160 labels 120–130 bottles per minute with ±0.5mm accuracy using photoelectric sensors.
- PA7100 provides high-speed labeling with servo-controlled technology, reducing maintenance costs.
- HERMA 362E achieves 200 products per minute for two-side labeling of various shapes.
- HERMA 152E excels in wrap-around labeling for cylindrical items at 100 products per minute.
NCT 21200 Automatic Sticker Labeling Machine Overview
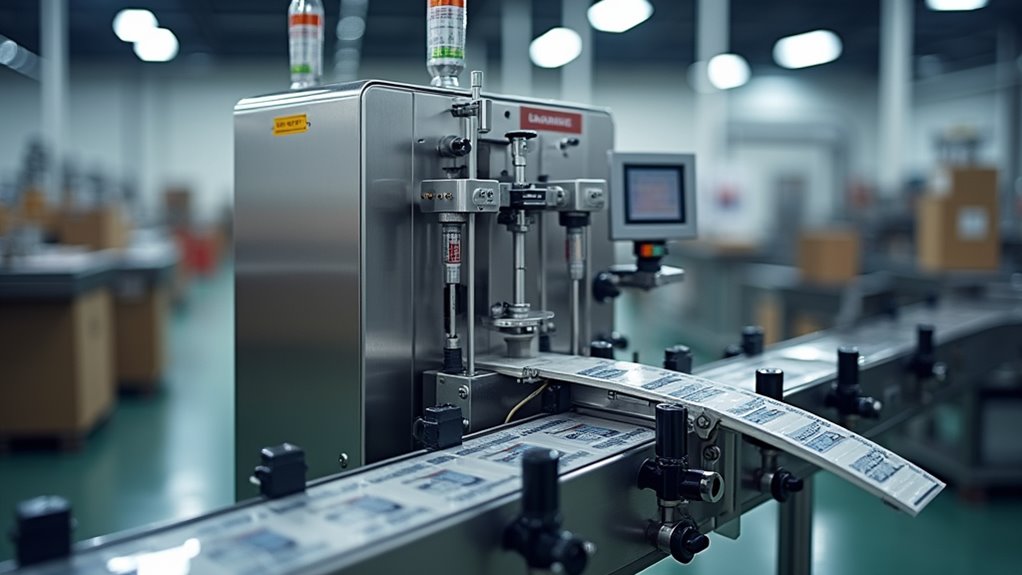
As the demand for efficient packaging solutions continues to grow, the NCT 21200 Automatic Sticker Labeling Machine stands out as a cutting-edge tool designed for high-performance labeling. This advanced equipment offers self-adhesive labeling capability, ensuring seamless automation for various packaging needs. Its precision-engineered design supports consistent label application, optimizing production efficiency in high-volume environments. Manufactured by iPharMachine, with over 30 years of experience, this machine exemplifies innovative labeling technology in its design and functionality.
A critical aspect of sustaining its performance lies in labeling machine maintenance. Regular upkeep, including cleaning and calibration, prevents downtime and extends the machine’s operational lifespan. Equally important is label material selection, as the choice of adhesive and substrate impacts adhesion quality and compatibility with different surfaces. The NCT 21200 accommodates a range of materials, but selecting the appropriate type ensures optimal results and minimizes errors during application. By prioritizing maintenance and material considerations, users can leverage this machine’s capabilities to meet stringent industry standards and achieve reliable, high-quality labeling outcomes.
CED TB100 Self-Adhesive Bottle Labeling Machine Features
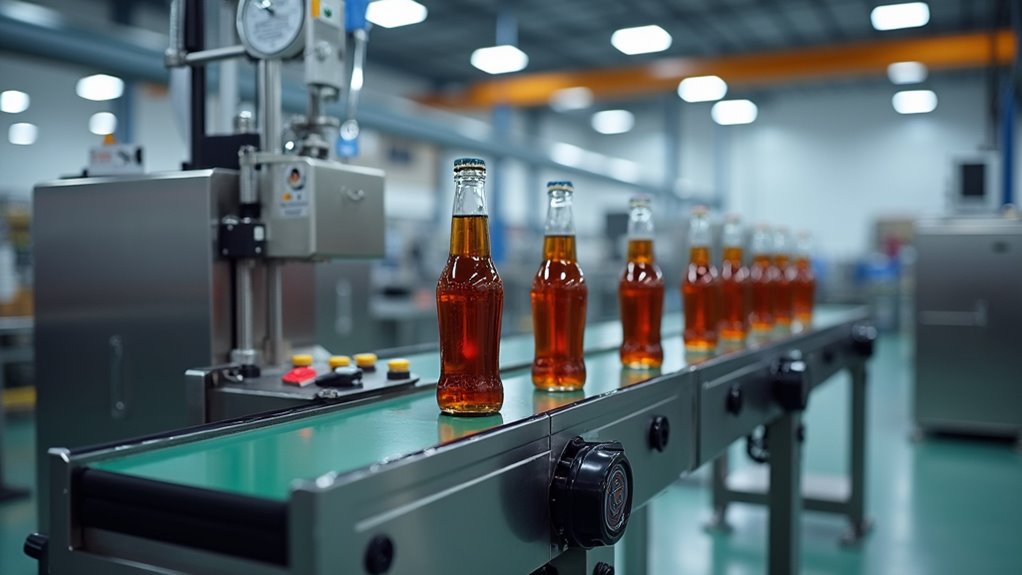
Building on the advancements in automated labeling technology, the CED TB100 Self-Adhesive Bottle Labeling Machine emerges as a robust solution tailored for precision and versatility in bottle labeling applications. Designed for efficiency, it operates at a capacity of 30 to 120 bottles per minute, supported by a 150W power supply and 0.6MPa air pressure. Its dimensions (1650x800x900mm) ensure seamless integration into production setups across pharmaceutical, cosmetic, and food industries.
The machine excels in handling round bottles (15ml to 500ml) with adjustable sensors for varying diameters, supporting both transparent and opaque labels. Features like tension-based label movement and photoelectric sensors ensure consistent placement and sticker durability. Additionally, customizable label lengths (20–200mm) enable label personalization for diverse branding needs. Its modular design simplifies maintenance, while automated peeling and pressing mechanisms enhance fixation accuracy, complemented by durable, wear-resistant components for long-term reliability.
PBTB 160 Fully Automatic Sticker Labeler Highlights
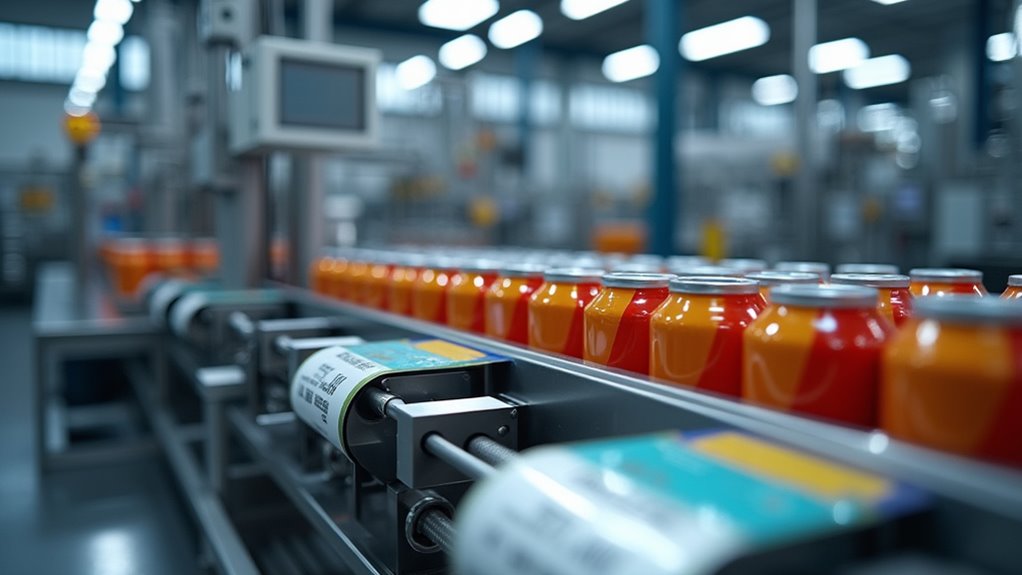
The PBTB 160 Fully Automatic Sticker Labeler stands out as a high-performance solution for modern bottling operations, delivering exceptional speed and precision. Capable of labeling 120–130 bottles per minute, it handles containers of 30–110mm diameter and 30–200mm height with remarkable labeling efficiency. Its ±0.5mm accuracy, aided by photoelectric sensors and tamp-blow techniques, ensures consistent placement on varied surfaces, while a customizable labeling head adapts to diverse container shapes.
Technically robust, the machine operates on AC220V single-phase voltage, weighs 250–300kg, and complies with GMP standards for regulated industries. Machine durability is evident in its secure mechanical components and low noise operation, complemented by safety measures protecting operators during high-speed tasks. Seamless integration into packaging lines, user-friendly maintenance, and minimal air consumption of 0.2 m³/h enhance its operational value. With SIEMENS HMI touch screen control, it offers precision and reliability for modern production demands.
PA7100 Industrial Print & Apply Labeling System Benefits
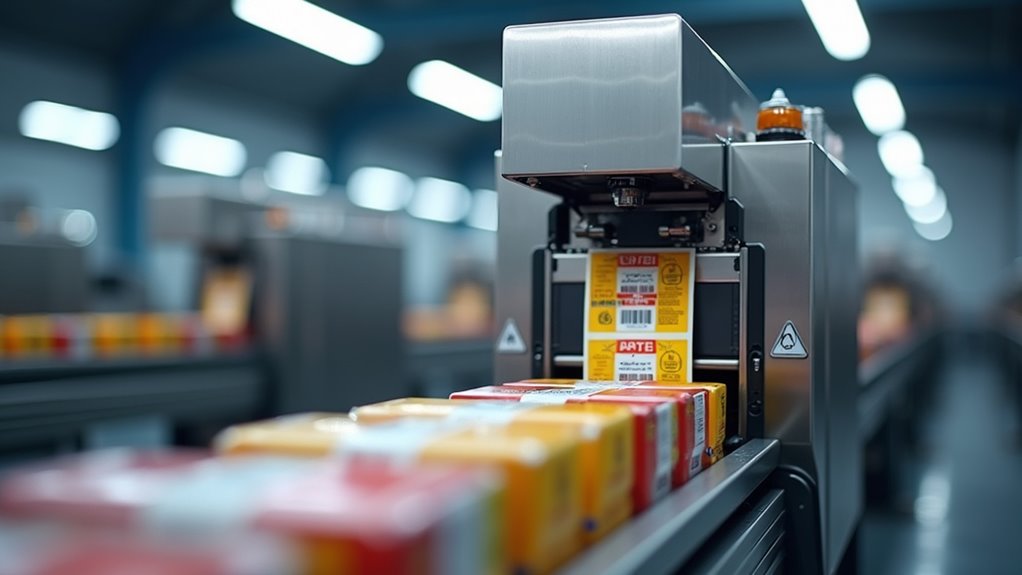
The PA7100 Industrial Print & Apply Labeling System offers exceptional high-speed label application, leveraging servo-controlled dispensing technology to maintain rapid throughput with minimal downtime in demanding production settings. Its cost-saving servo design eliminates the need for pneumatic components, reducing mechanical wear and lowering maintenance expenses over time. Additionally, the system’s reliable adhesion technology, supported by smart sensing auto-adjusting controls, ensures precise label placement and consistent bonding across diverse packaging formats.
High-Speed Label Application
While efficiency remains paramount in modern manufacturing, the PA7100 Industrial Print & Apply Labeling System excels in delivering high-speed label application without compromising accuracy. Designed for rapid production environments, this system integrates servo-controlled label dispensing to ensure precision label placement, even at elevated speeds. Its smart sensing auto-adjusting controls detect and compensate for motion inconsistencies, maintaining consistent alignment across various labeling materials.
This technology minimizes errors, enhancing throughput for diverse industries. Additionally, the system’s robust design supports seamless operation with minimal machine maintenance, reducing downtime and operational costs. By prioritizing speed and reliability, the PA7100 meets the demands of high-volume labeling tasks, offering a solution that balances performance with precision in fast-paced production lines.
Cost-Saving Servo Design
Numerous advancements in the PA7100 Industrial Print & Apply Labeling System underscore its cost-saving servo design, particularly through the integration of brushless servo motors. These motors ensure precision label placement with ±0.5mm accuracy at high speeds, while reducing mechanical wear due to frictionless operation. Their all-electric nature eliminates compressed air needs, optimizing energy use and delivering sustainability benefits by minimizing resource consumption.
Further enhancing efficiency, the system’s digital integration allows centralized control via HH-4000 handheld or remote PC interfaces for real-time adjustments. Self-calibrating sensors and proactive diagnostics reduce maintenance, while adaptive power usage cuts operational costs. Combined with material waste reduction through precise application, the PA7100 offers a technically advanced solution for cost-effective labeling in industrial environments.
Reliable Adhesion Technology
Several critical features define the reliable adhesion technology of the PA7100 Industrial Print & Apply Labeling System, ensuring consistent performance in demanding industrial settings. Its advanced adhesion control, with an integrated sensor system and tension management, guarantees adhesion durability by preventing skewing during high-speed operations. This precision enhances label longevity, even in harsh conditions like 10-85% humidity and 5°C to 40°C temperatures.
The system’s military-grade certifications further validate its reliability. Below is a technical overview of key adhesion factors:
Feature | Specification |
---|---|
Humidity Tolerance | 10-85% RH (non-condensing) |
Temperature Range | 5°C to 40°C |
Tension Management | Prevents skewing |
Such specifications ensure unwavering performance, making the PA7100 ideal for industrial labeling needs with sustained label integrity.
HERMA 362E Side Labeling Machine Capabilities
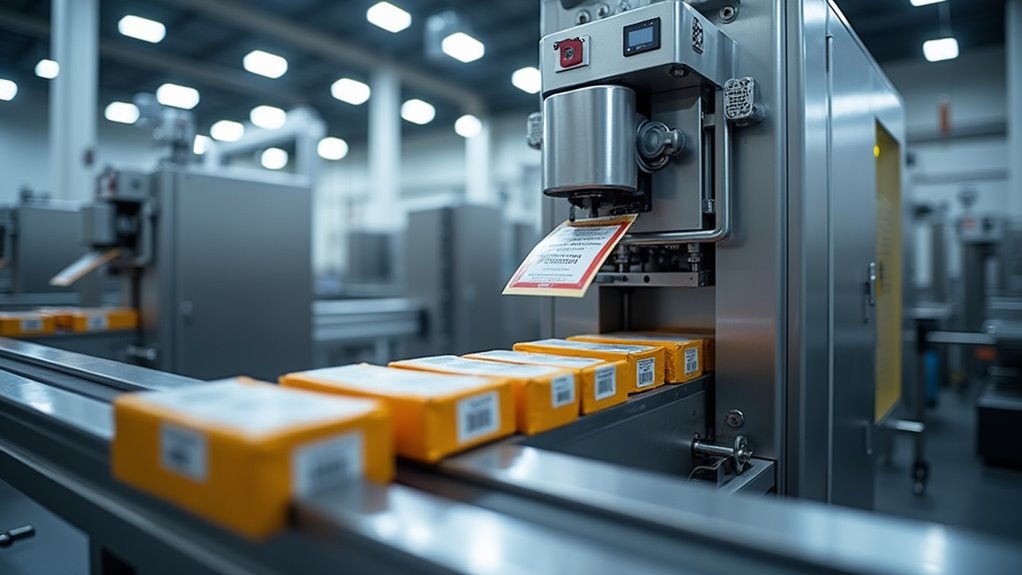
How does the HERMA 362E Side Labeling Machine stand out in high-speed production environments? This advanced system achieves labeling speeds of up to 200 products per minute, leveraging dual HERMA 500 applicators for seamless, continuous operation. It excels in two-side labeling for rectangular and cylindrical products, ensuring output consistency even under demanding conditions. The machine supports product customization by accommodating diverse dimensions (30–200 x 30–120 x 30–300 mm) and guarantees label durability through precise application and integrated quality checks.
Its compact, space-efficient design features an enclosed stainless-steel base for stability and handwheels with digital indicators for exact adjustments. The HERMA 362E also offers a PLC control panel for intuitive operation and automatic ejection of failed labels, enhancing reliability. With modular components and configurations like the Economy model or tamper-evident variant, it integrates effortlessly into varied production lines, delivering precision and efficiency.
HERMA 152E Wrap-Around Labeler Specifications
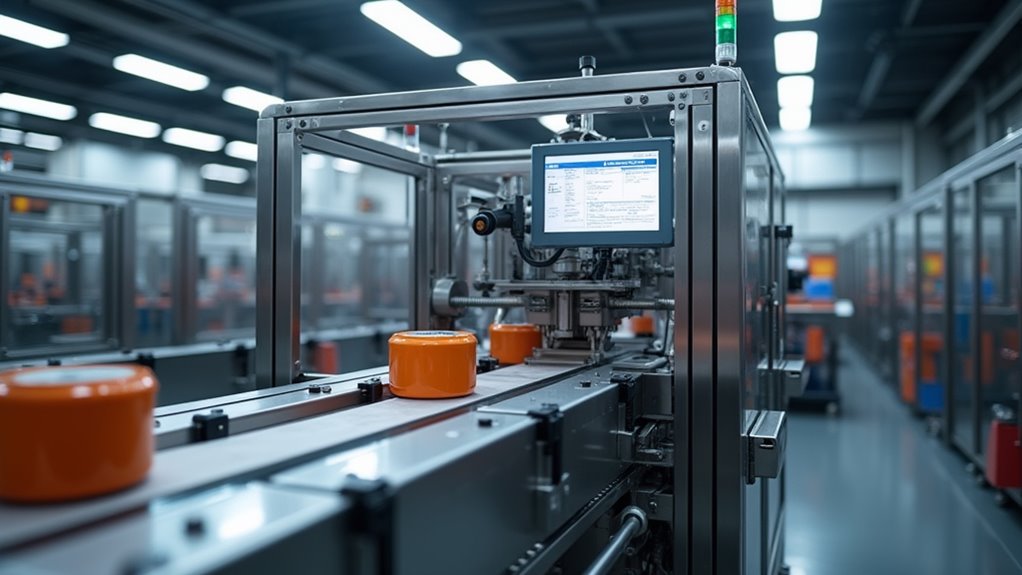
While high-speed labeling demands precision and adaptability, the HERMA 152E Wrap-Around Labeler meets these challenges with specialized specifications for cylindrical products. Designed for vials, bottles, cans, and jars, it handles diameters from 1.27 cm to 10.16 cm and heights up to 250 mm, supporting industries like pharmaceuticals and food/beverage. Its belt variant processes 100 products per minute without format sets, while the prism variant offers 90 products per minute with enhanced precision.
The machine excels in product customization, accommodating label widths of 15–240 mm and lengths of 30–315 mm, alongside optional integrations like variable data printing and code verification. Its ergonomic design ensures a compact footprint, tool-free adjustments, and a linear setup that simplifies format changes. Additionally, a gentle ejection mechanism for defective items and serialization-ready modules underscore its compliance with strict standards, optimizing efficiency and reliability in high-throughput environments.
Choosing the Right Labeling Machine for Your Needs
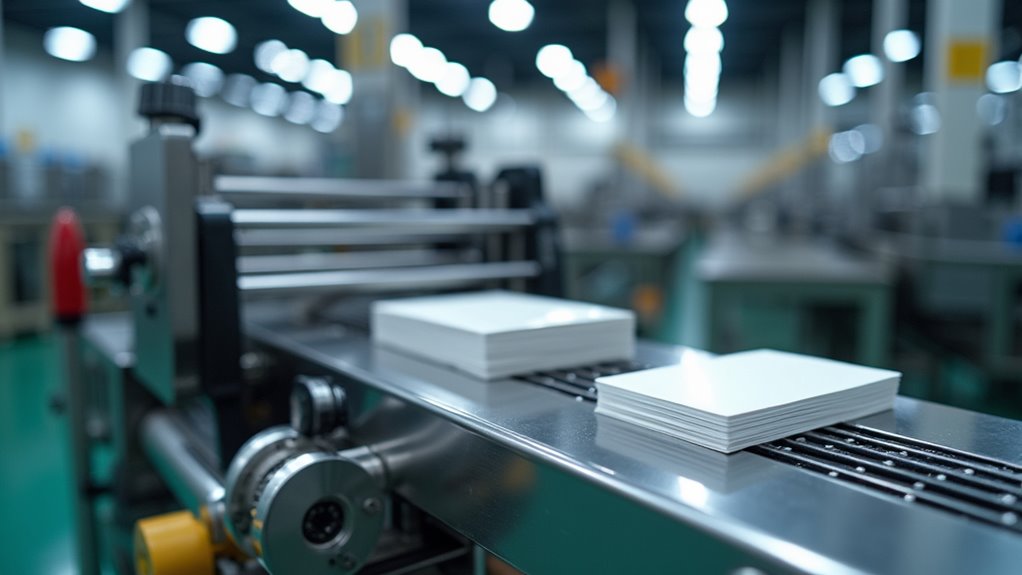
Many factors influence the selection of an appropriate labeling machine to meet specific operational demands. Key considerations include the type of label application method, such as flat labeling for versatile, low-volume operations or wrap-around labeling for full 360° coverage on cylindrical products like bottles. Material compatibility is critical, ensuring the machine handles specific substrates and adhesives without degradation or misalignment during application. Side labeling, often integrated with conveyors, supports high-throughput environments, while corner labeling offers precision for tamper-evident needs with ±1mm accuracy.
Additionally, operator safety must be prioritized, with machines featuring protective guards and emergency stop mechanisms to mitigate risks during operation. Assessing production volume, product variety, and integration with existing systems further refines the choice. By systematically evaluating these parameters, businesses can identify a labeling solution that aligns with operational efficiency, regulatory compliance, and long-term scalability in a competitive 2025 market landscape.