Continuous belt weighers operate by integrating load cells, speed sensors, and data processing units to measure the weight and flow rate of materials on a conveyor. Load cells support the weighbridge, capturing material weight, while speed sensors monitor conveyor velocity. An integrator processes these inputs to calculate real-time flow rates and total weight. Proper installation and regular calibration are essential for maintaining accuracy. Understanding these components and their interactions provides the foundation for efficient scale operation and management.
Key Takeaways
- Continuous belt weighers measure material flow rates and total weight on conveyors for bulk material handling.
- Load cells convert weight into electrical signals, supporting conveyor rollers for accurate weight measurement.
- Speed sensors monitor conveyor velocity, essential for determining flow rates and total weight.
- An integrator processes data from sensors, calculating and displaying material flow rates and total weight.
- Regular calibration, zero adjustments, and span checks are critical for maintaining measurement accuracy over time.
Truck Scales and Load Cells
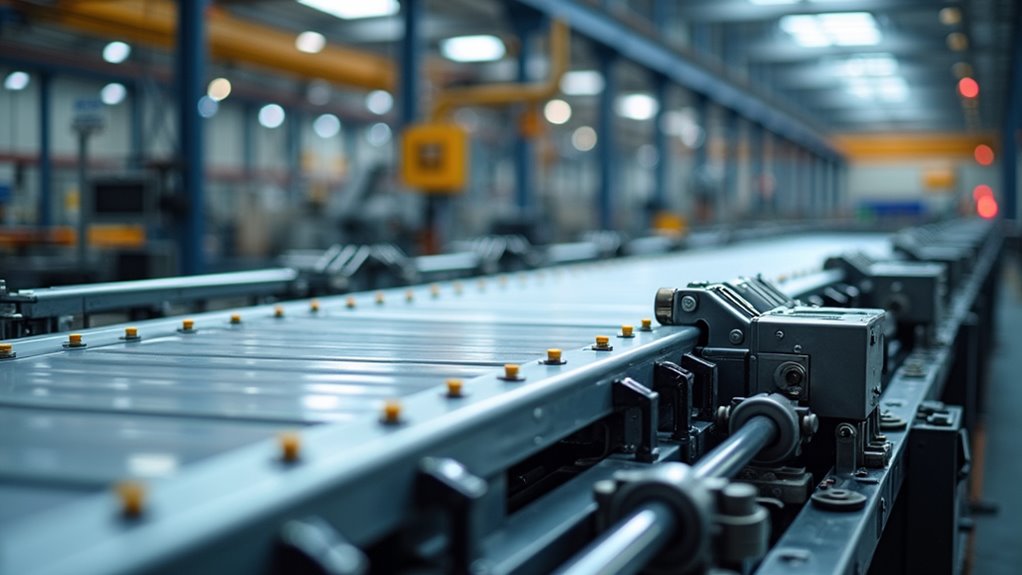
Truck scales are a critical component in conveyor belt weighing systems, providing the structural framework that supports one or more conveyor rollers and transfers material weight to load cells.
Robust truck scale designs prevent vibration and spillage, with some featuring pass-through frames to avoid material trapping. Multi-roller weighbridges increase measurement time, improving accuracy. Proper installation is essential to ensure accurate weight measurement and avoid potential issues.
Weighbridge design ensures stability and precision, with features like pass-through frames and multi-roller configurations enhancing accuracy by preventing material trapping and increasing measurement time.
Installation location is critical, requiring a rigid conveyor section with constant belt tension.
Various load cell types, including shear beam, bending beam, single-point, and S-type, are used based on application requirements. Specialized load cells like LVDT and pancake designs are selected for specific constraints such as light loads or space limitations.
Speed Sensors and Conveyor Velocity
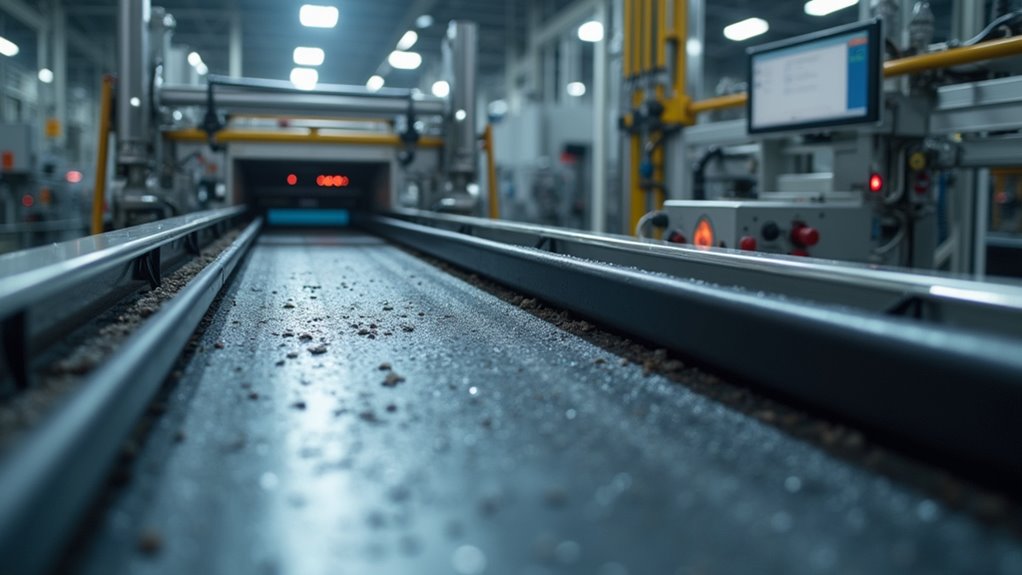
Integrated into the precise operation of belt weighers, speed sensors perform the critical task of accurately monitoring conveyor velocity.
They provide essential data for determining flow rates and totals by measuring conveyor speed fluctuations. Sensors convert rotational motion into electrical signals processed by the integrator.
Different sensor types are used, including:
- Tachometers, which measure the rotational speed of pulleys.
- Proximity sensors, which detect metallic targets on rotating components.
- Wheel-driven sensors, which use a wheel in contact with the conveyor to measure speed.
Measurement accuracy can be affected by factors like belt slippage, material buildup, and environmental conditions, which must be mitigated to ensure precise weighing.
Integrator and Data Processing
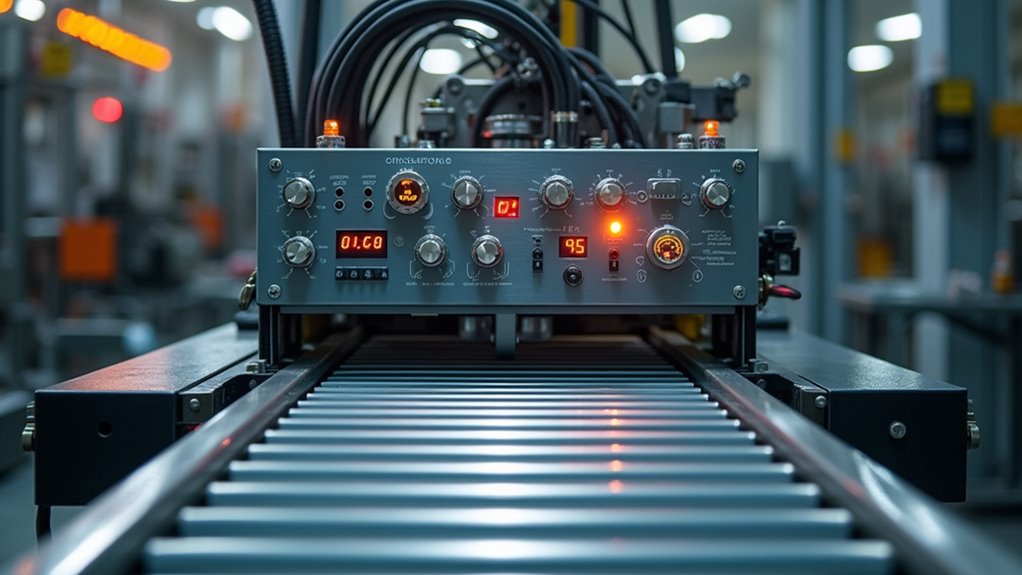
Serving as the brain of the belt weigher system, the integrator plays a pivotal role in processing and managing data from various sensors. It uses advanced microprocessor-based technology to calculate instantaneous material flow rates and cumulative total weight by integrating signals from load cells and speed sensors.
Intelligent signal filtering techniques eliminate mechanical vibrations, ensuring optimal performance. Utilizing high-resolution display technology, the integrator provides a comprehensive interface for operators to view and manage production data, including flow rates, total weight, and belt speed.
With support for various communication protocols, it enables seamless system integration and data management to enhance operational efficiency.
Calibration and Maintaining Accuracy
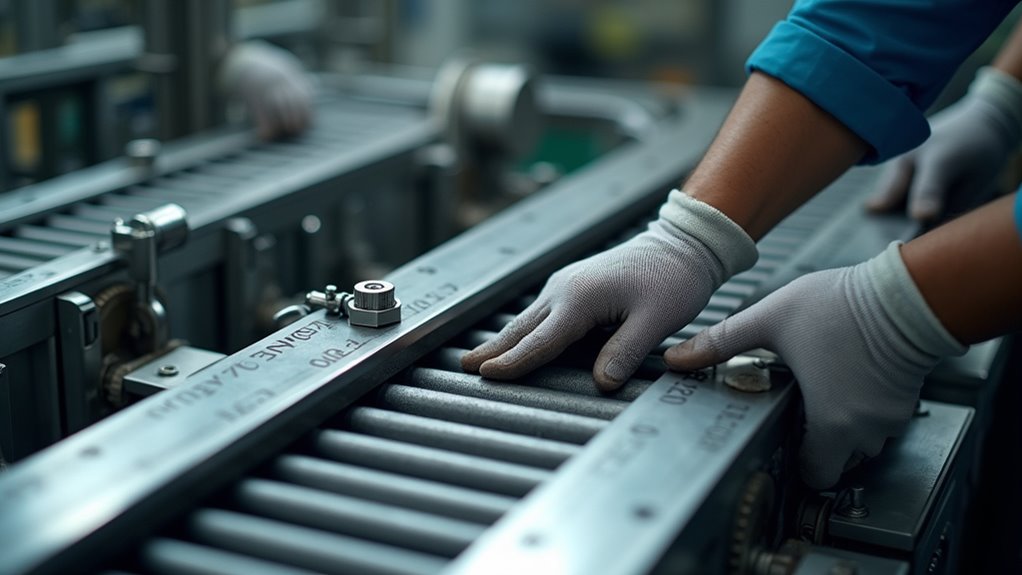
The calibration frequency of continuous belt weighers depends on several factors to ensure measurement accuracy:
- Zero Calibration: Performed daily, with a minimum recommendation of weekly, to adjust for the conveyor’s tare weight.
- Span Calibration: Conducted monthly to maintain system accuracy, using reference standards like test weights or chains.
- Maintenance Trigger Factors: Recalibration is necessary after any conveyor system maintenance or lubrication, as these actions can alter baseline measurements.
Accuracy checks through regular calibration are critical for reliable continuous belt weigher operation.
Specific intervals between calibrations can be adjusted based on statistical data, allowing for extended periods if deviation errors remain within acceptable limits.
Installation Considerations and Environmental Impact

While calibration ensures the ongoing accuracy of continuous belt weighers, the installation process and environmental factors play a crucial role in establishing the foundation for precise weight measurements.
The installation location must be carefully selected to minimize measurement errors. It should be positioned away from material loading points and conveyor curves, with the scale placed near the tail end where belt tension is most stable.
Choosing the correct installation location is critical to minimizing measurement errors, with the scale placed near the tail end to ensure stable belt tension.
The conveyor structure must be rigid, with rollers in the weighing area properly aligned and maintained. Environmental influences such as vibrations, weather, and extreme temperatures must also be mitigated.
The production and operation of conveyor systems have a significant environmental impact, consuming considerable energy and resources. End-of-life management and conveyor belt recycling are critical to minimizing their environmental footprint.