Checkweighers are vital in the food industry for ensuring product weight accuracy and regulatory compliance with standards like FDA and EU directives. They enhance quality assurance, reduce waste by minimizing overfill, and boost consumer trust through consistent product reliability. Advanced sensor technologies, such as FlashCell™, achieve precision at speeds up to 800 pieces per minute. They support production efficiency, data traceability, and diverse product adaptability. Explore further to uncover deeper insights into their transformative impact.
Key Takeaways
- Checkweighers ensure food product weight accuracy, meeting strict regulatory standards like FDA and EU directives.
- They prevent overfill and underfill, reducing waste and protecting consumer trust in the food industry.
- High-speed models process up to 800 pieces per minute with precision using advanced technologies like FlashCell™.
- Integration with ERP systems provides real-time data for compliance, traceability, and quality control.
- Multimodal systems combine checkweighing with contaminant detection, enhancing food safety and compliance.
Critical Role in Quality Assurance
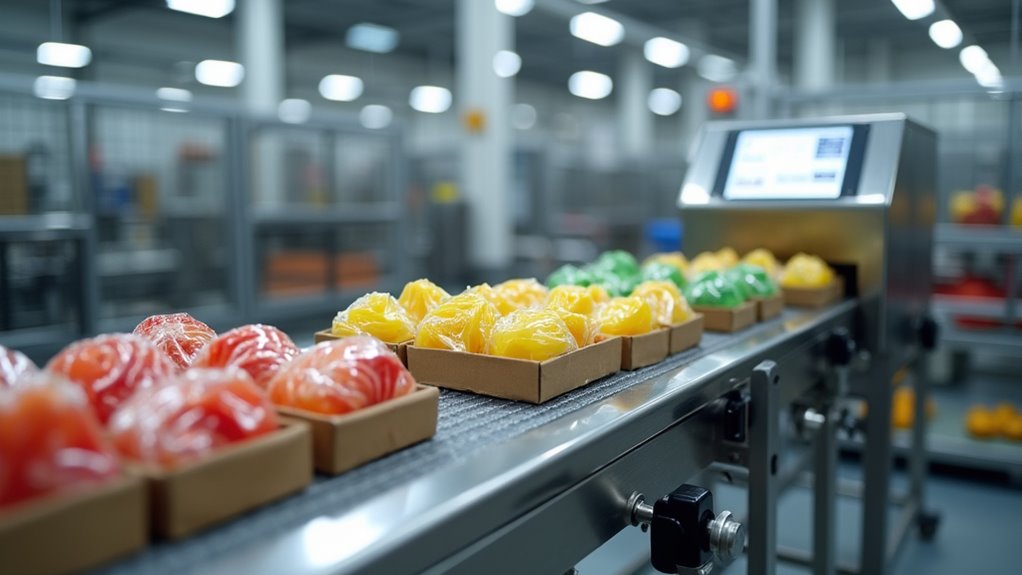
Checkweighers play a pivotal role in quality assurance within the food industry by ensuring product weight accuracy through real-time measurement and verification during production. These high-precision systems maintain fill quantities within strict tolerance ranges, employing statistical control to minimize deviations across batches. By reducing underfilling and overfilling, they curb material waste and ensure consistent output, even in specialized applications like vintage packaging, where aesthetic and weight precision are critical.
In artisanal manufacturing, where small-scale production demands exacting standards, checkweighers provide indispensable support by achieving tight production tolerances. Their ability to detect and address weight discrepancies in real time enhances product reliability without compromising the unique character of handcrafted goods. Furthermore, the technology minimizes costly errors, ensuring that packaging weights remain uniform across shifts. This analytical precision fortifies quality assurance, safeguarding brand integrity while optimizing resources in diverse food production environments. Additionally, checkweighers support compliance with weights and measures regulations globally, reinforcing trust and accountability in the supply chain.
Ensuring Regulatory Compliance
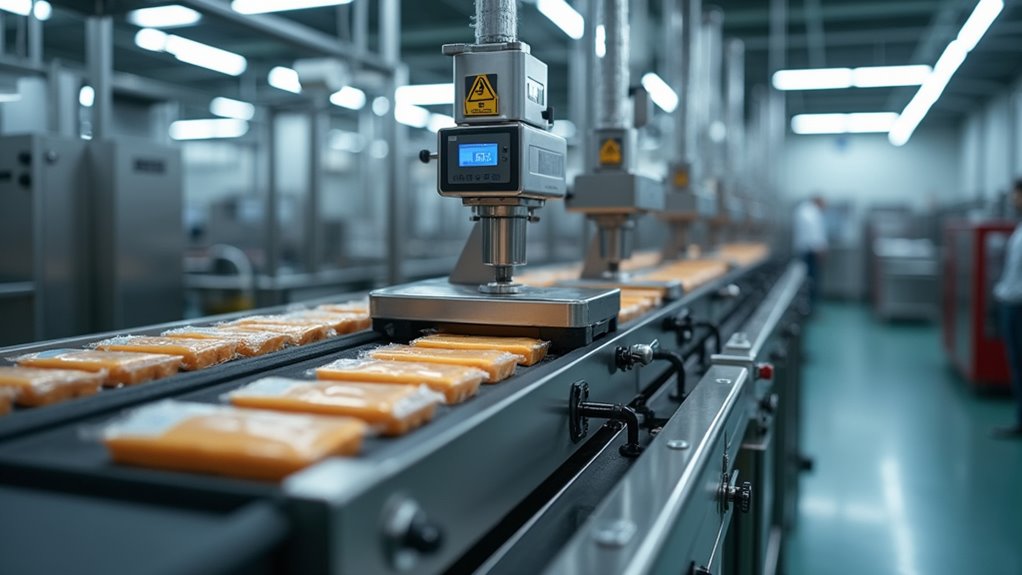
Checkweighers play a critical role in meeting legal standards by ensuring that food products adhere to varying global weight regulations and tolerance thresholds. They help manufacturers avoid costly penalties by preventing non-compliance issues such as underfilling or label discrepancies that could result in fines or reputational harm. Additionally, these systems support audit traceability through precise documentation of weight data and calibration records, facilitating regulatory inspections and accountability.
Meeting Legal Standards
In the highly regulated food industry, adherence to legal standards for weight accuracy is paramount to ensure consumer trust and avoid penalties. Checkweighers play a critical role in meeting stringent requirements like the Weights and Measures Acts, FDA regulations, and EU Directive on Repackaging by providing real-time weight validation and enforcing Tolerable Negative Error limits. These systems, often equipped with calibration protocols and automated rejection mechanisms, ensure compliance with the Average Weight System across batches.
Beyond functionality, checkweighers indirectly support packaging aesthetics by maintaining consistent product weights, aligning with marketing strategies that emphasize reliability. Integration with ERP systems and audit-ready data logs further streamlines compliance monitoring, while adherence to BRCGS and SQF certifications facilitates international trade through harmonized measurement protocols.
Avoiding Costly Penalties
Regulatory adherence in the food industry extends beyond meeting legal standards to directly safeguarding against severe financial and operational repercussions. Non-compliance can incur fines up to $500,000, product seizures, and facility suspensions, while misleading vintage packaging or inconsistent seasonal flavors may trigger penalties under the FDA-mandated weight standards or EU Repackaging Directive. Such violations also risk long-term reputational damage and revenue loss.
Key risks of non-compliance include:
- Financial Burden: Fines, retailer fees, and litigation costs for underweight products.
- Operational Halts: Facility suspensions or import alerts disrupting production.
- Market Impact: Mandatory recalls damaging consumer trust in products like seasonal flavors.
Checkweighers ensure precision, mitigating these costly penalties through accurate weight verification and regulatory alignment.
Supporting Audit Traceability
How can food industry stakeholders ensure seamless compliance during stringent regulatory audits? Checkweighers play a pivotal role in supporting audit traceability by automating data collection and ensuring data integrity. These systems capture real-time weight measurements and production statistics, generating digital documentation with timestamps and operator signatures for paperless audits. This traceable, electronic reporting aligns with global standards like FSMA and EU food safety protocols, facilitating quick retrieval of batch-specific data during inspections.
Moreover, configurable software integrates retailer-specific codes of practice, while system checks and staff training uphold data accuracy. By maintaining accessible, dated records, checkweighers provide audit-ready evidence, minimizing discrepancies and ensuring regulatory alignment across territories. Such precision in documentation fortifies compliance under rigorous scrutiny.
Enhancing Production Efficiency
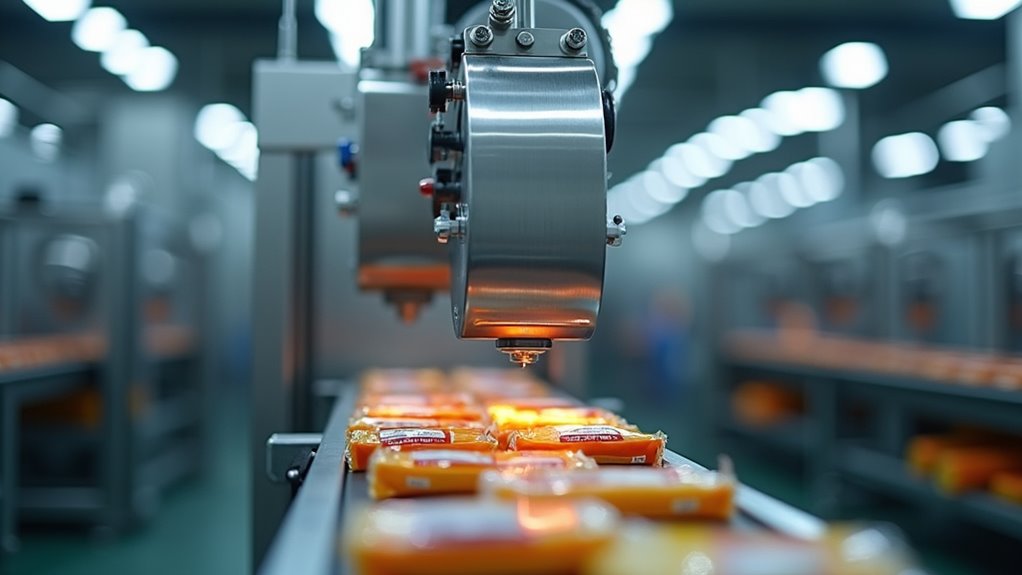
While modern food production demands relentless speed and accuracy, checkweighers stand as critical tools for enhancing efficiency on the production line. These systems leverage automation scalability to adapt to varying production rates and package sizes, ensuring consistent throughput without sacrificing packaging precision. High-speed performance, processing up to 250 pieces per minute with accuracy of ±0.05 grams, integrates seamlessly with existing lines, while real-time rejection mechanisms eliminate non-conforming items instantly.
Key efficiency benefits include:
- Dynamic Calibration: Algorithms adjust fill levels mid-production, optimizing material use and maintaining compliance.
- Conveyor Synchronization: Adjustable belt speeds balance throughput with precise measurements, preventing bottlenecks.
- Data-Driven Insights: Real-time analytics log weight trends and equipment metrics, enabling proactive process improvements.
Through automated weight inspection and precision-driven adjustments, checkweighers minimize human error and ensure operational consistency. Their integration with quality control systems further streamlines workflows, reinforcing their role in modern food manufacturing efficiency.
Reducing Product Waste
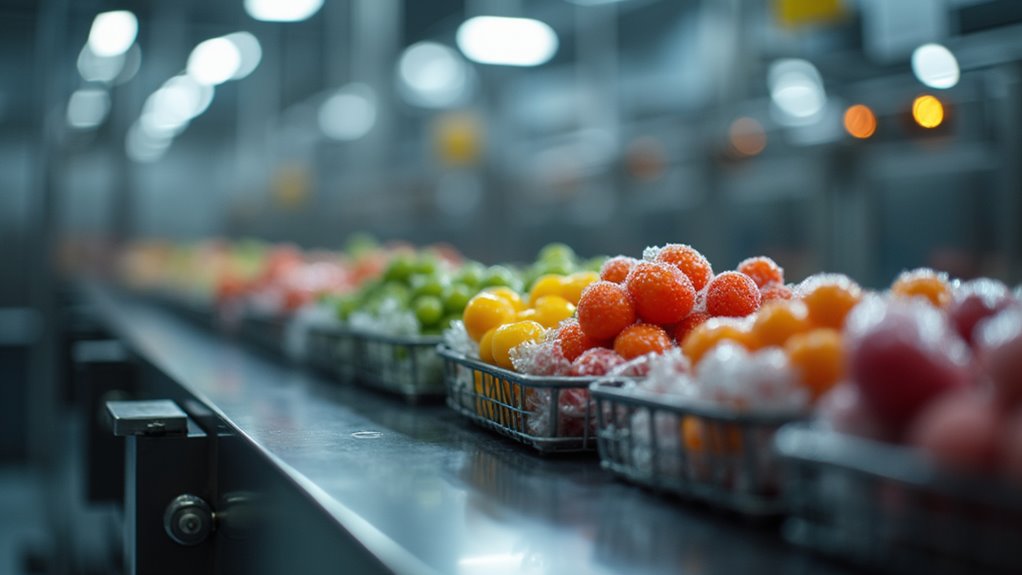
Checkweighers play a critical role in reducing product waste by minimizing overfill losses through precise weight control, ensuring that excess product giveaway is curtailed. They also prevent underfill issues by detecting and rejecting packages that fail to meet minimum weight standards, thus avoiding customer dissatisfaction and regulatory penalties. Additionally, these systems optimize resource use by providing data for process adjustments, enabling manufacturers to balance efficiency with waste reduction.
Minimizing Overfill Losses
Why do food manufacturers face significant losses from overfilled packages? Overfilling results in product giveaway, where excess material is used beyond the labeled weight, directly impacting profit margins. Checkweighers mitigate this by providing real-time monitoring and precise measurements, detecting discrepancies instantly to prevent costly waste. With high-speed processing, they ensure accuracy at scale, while automated adjustments recalibrate fillers to minimize variations.
Key benefits of checkweighers include:
- Cost Reduction: Minimized giveaway preserves inventory, optimizing resource allocation.
- Efficiency Gains: Small weight adjustments yield substantial savings in high-volume production.
- Environmental Impact: Reduced overfill lowers excess packaging and raw material waste.
Through laboratory-grade precision, checkweighers safeguard compliance and enhance production tolerances, ensuring efficient inventory use and significant cost savings.
Preventing Underfill Issues
How can food manufacturers safeguard against the risks of underfilled packages that lead to product waste and customer dissatisfaction? Checkweighers play a critical role in detecting underweight packages, which often indicate filling equipment malfunctions or calibration errors. By providing continuous weight monitoring, these systems enable real-time adjustments to maintain precise fill levels, ensuring packaging aesthetics remain intact and consumer trust is preserved.
Moreover, checkweighers identify inconsistencies in multi-component systems, such as trayed frozen foods, ensuring volumetric filling accuracy through weight verification. Real-time feedback pinpoints specific production line segments causing underfills, preventing waste and maintaining flavor consistency across batches. This analytical approach not only reduces product loss but also upholds regulatory compliance by preventing underfilled packages from reaching the market.
Optimizing Resource Use
What drives efficiency in food manufacturing when it comes to minimizing waste? Checkweighers play a pivotal role by providing precision measurement, reducing product giveaway, and optimizing fill levels to curtail material overuse. They enable real-time monitoring, aligning with lean manufacturing to divert excess supply and minimize rework costs, thus supporting sustainability goals.
Key benefits of checkweighers in resource optimization include:
- Precision Control: Ensures consistent weights, preserving packaging aesthetics by avoiding overfill or underfill issues.
- Waste Reduction: Facilitates recycling (97% of food waste) and donation through accurate tracking.
- Operational Efficiency: Reduces labor costs with automation, bolstered by employee training for effective system use.
This analytical approach ensures tighter inventory control and measurable waste reduction in food production processes.
Supporting Consumer Trust
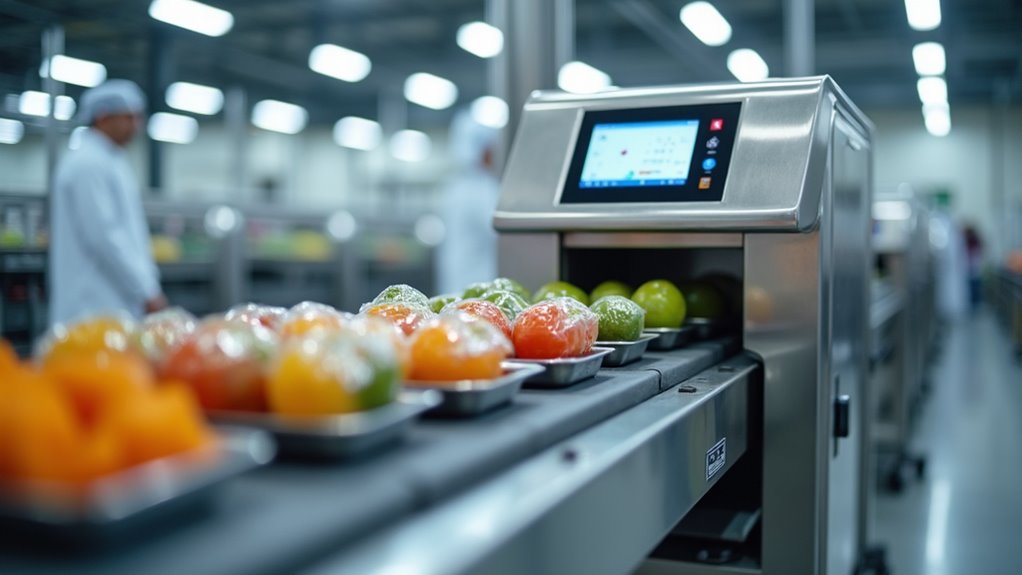
In the food industry, maintaining consumer trust is paramount, and checkweighers play a critical role in this endeavor. These precision instruments ensure that every product meets the declared weight, preventing underfilled items from reaching the market. By enforcing precise compliance with weight regulations, checkweighers protect manufacturers from legal penalties and fraud allegations, which could severely damage brand reputation. This accuracy reassures consumers that they receive the quantity promised on the label, fostering confidence in the product’s integrity.
Beyond weight accuracy, checkweighers contribute to consistent quality control, aligning with consumer expectations for reliability. While aspects like packaging aesthetics and packaging variety—key in attracting diverse customer preferences—are vital, the fundamental assurance of correct product weight underpins trust. Checkweighers thus serve as a technical safeguard, ensuring that each item upholds the manufacturer’s commitment to fairness and transparency, solidifying consumer loyalty through dependable standards.
Integration With Automated Systems
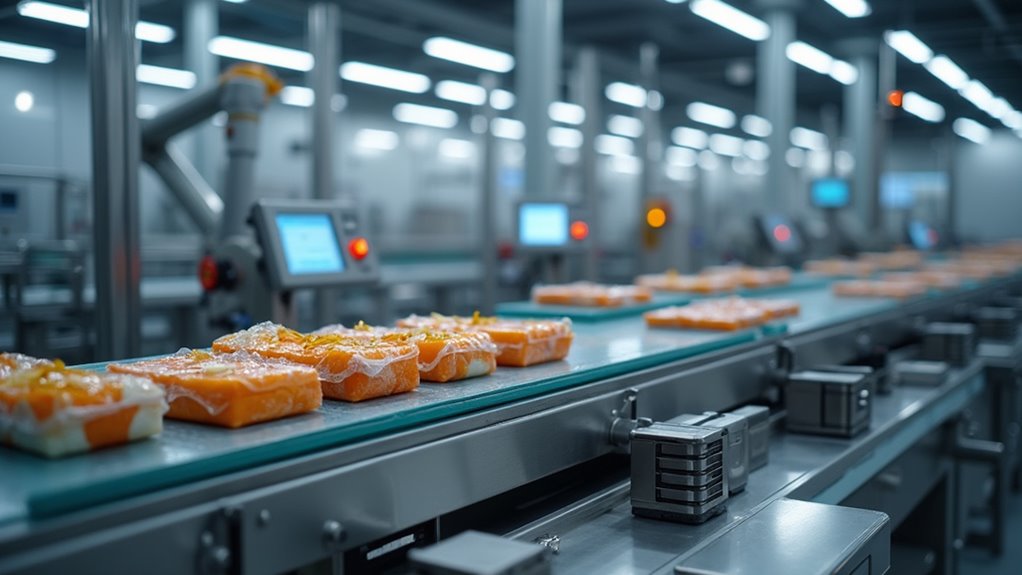
Checkweighers in the food industry demonstrate advanced integration with automated systems by ensuring seamless production line synchronization through precise alignment with conveyors and packaging equipment. They facilitate real-time data sharing via standardized protocols, enabling instant communication with ERP and quality management systems for accurate monitoring and decision-making. Additionally, their error-free process automation is achieved through dynamic transport systems and automatic reject mechanisms, minimizing manual intervention and enhancing operational reliability.
Seamless Production Line Sync
While modern food production demands efficiency and precision, seamless integration of checkweighers with automated systems ensures uninterrupted workflow across complex production lines. These systems leverage conveyor reliability to transport products smoothly, while star wheel adjustments maintain optimal spacing for accurate weighing. Modular designs and intuitive interfaces further enable compatibility with existing setups, minimizing disruptions.
Key aspects of this integration include:
- Belt Synchronization: Multiple belts coordinate product flow through weighing and separation, ensuring consistent operation.
- High-Speed Handling: Advanced models process over 200 products per minute, supporting ultra-high throughput with precision.
- Dynamic Adjustments: Centralized controls allow real-time modifications to speed and spacing for diverse products.
Such technical synergy optimizes production efficiency, maintaining accuracy across multilane, continuous operations without compromising system interoperability.
Real-Time Data Sharing
Modern food production systems rely heavily on the ability of checkweighers to facilitate real-time data sharing, ensuring a cohesive link with automated processes across the production environment. Through smart sensor integration, checkweighers continuously monitor product weights and transmit critical data to centralized systems, enabling immediate detection of deviations. This connectivity, often achieved via wireless data transfer, supports seamless integration with conveyors, robotics, and production management software. Ethernet or USB options further enhance data exchange with quality management systems, aligning with Industry 4.0 standards for smart factory ecosystems. Such real-time synchronization allows remote monitoring of multiple lines, optimizing oversight. By bridging operational components, checkweighers ensure precise data flow, fostering efficiency and responsiveness in dynamic food production settings.
Error-Free Process Automation
As automation becomes central to food production, the integration of checkweighers with automated systems ensures error-free operations across complex manufacturing lines. These systems synchronize with conveyor belt feeding and packaging machinery, maintaining production speed while adapting to varying line configurations in wet or dry environments. Real-time rejection mechanisms, like pneumatic systems and diverting channels, swiftly remove non-compliant items with minimal downtime.
Key integration benefits include:
- Seamless Flow: Direct compatibility with conveyors ensures consistent product throughput.
- Precision Rejection: Automated air jets enhance accuracy in removing defective items.
- System Reliability: Regular mechanical calibration guarantees optimal performance.
Such precision demands thorough operator training to manage integration and troubleshoot issues, ensuring sustained efficiency and compliance in high-speed food production environments.
Advanced Sensor Technology
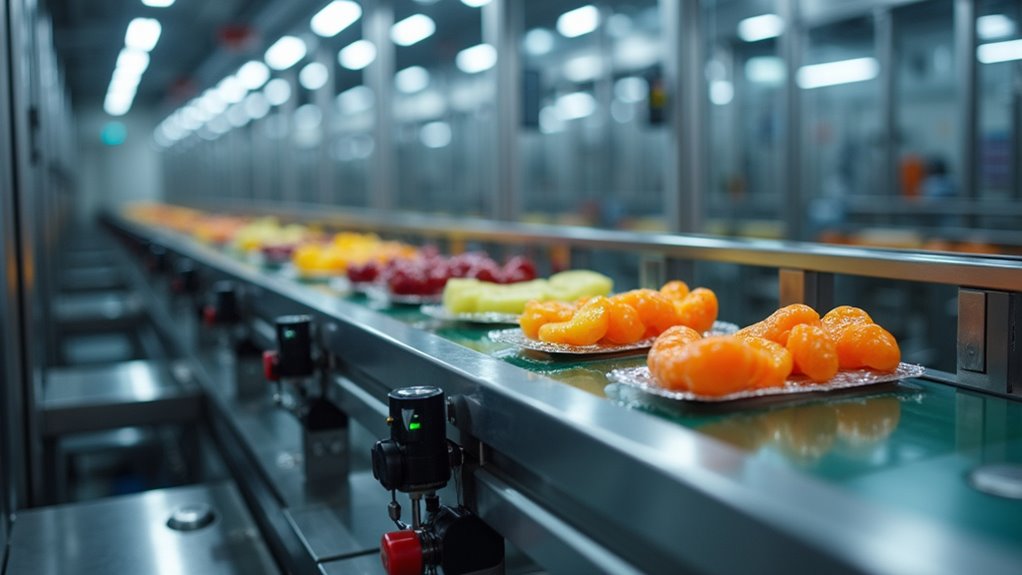
How have checkweighers in the food industry achieved such remarkable precision and efficiency? Advanced sensor technology, including sensor miniaturization and refined calibration techniques, plays a pivotal role. Electromagnetic Force Reduction (EMFR) sensors, like FlashCell™, ensure accuracy at speeds up to 800 pieces per minute, minimizing vibration for consistent results. Hygienic-grade sensors, rated IP69K, endure harsh sanitation cycles in dairy and meat processing, using corrosion-resistant materials to maintain uptime.
Further, multimodal sensor integration combines checkweighers with X-ray and metal detection, optimizing contaminant control in compact systems. Real-time data processing, supported by dynamic algorithms, logs deviations and ensures compliance through detailed batch reports. Below is a snapshot of key sensor advancements:
Sensor Type | Key Feature |
---|---|
EMFR (FlashCell™) | Precision at 800 PPM |
Inductive/Capacitive | IP69K hygiene standards |
Hygienic-Grade | Chemical resistance |
Multimodal Integration | Contaminant detection combo |
High-Speed Weight Verification
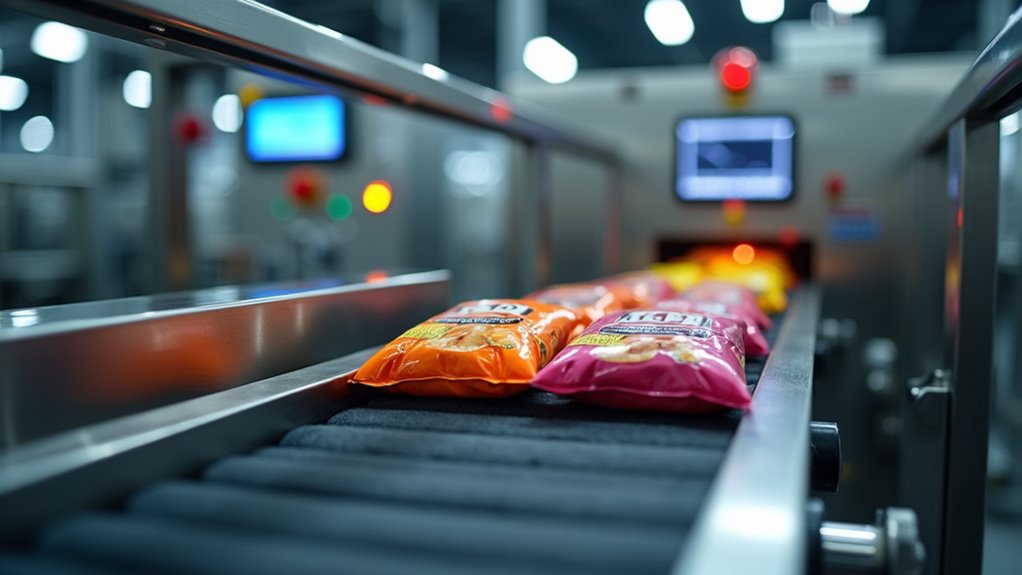
Why is speed so critical in food production lines? In the fast-paced food industry, high-speed weight verification ensures that production keeps pace with demand without sacrificing quality. Checkweighers perform real-time weight calibration to detect deviations, operating at conveyor speeds up to 120m/min, as seen in models like Easyweigh. They maintain precision with ±0.1g accuracy, even at throughputs of 650 units/min in high-performance systems like HC-A, using technologies such as electromagnetic force restoration (EMFR).
Key insights into high-speed checkweighers include:
- Rapid Throughput: Handling up to 250-650 units/min, they support high-volume lines without bottlenecks.
- Versatile Adaptation: Designed for diverse products, from fragile items to complex packaging, ensuring consistent verification.
- Automated Rejection: Mechanisms like air jets swiftly remove non-compliant items, maintaining batch integrity.
Such systems minimize downtime, ensuring continuous operation while meeting strict regulatory standards in dynamic food manufacturing environments.
Data Logging for Traceability
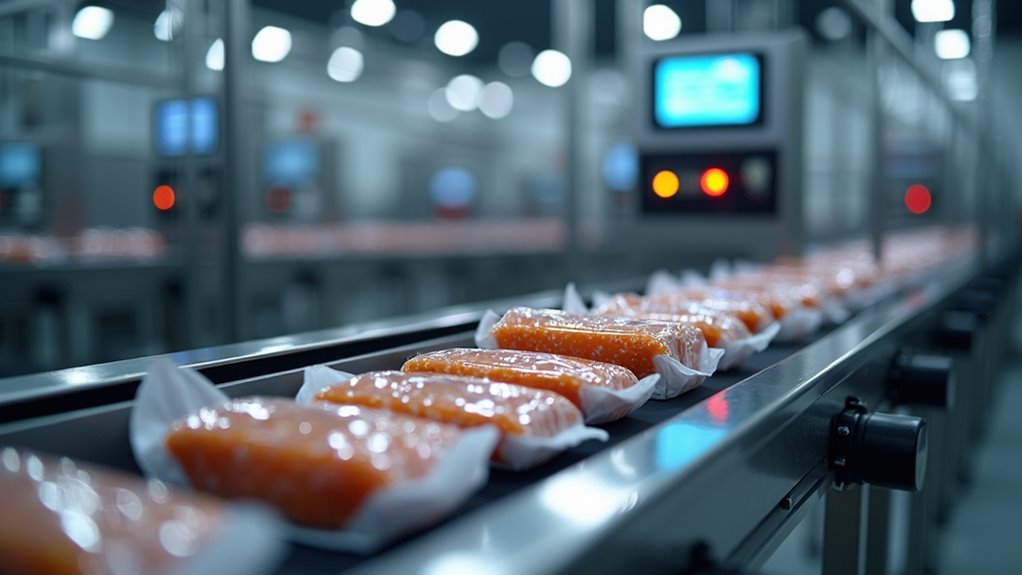
In the realm of food production, data logging for traceability stands as a critical function of modern checkweighers, ensuring accountability and transparency across the supply chain. These systems employ software-driven traceability to automatically log weight data with timestamps, capturing 100% of production metrics for audit-ready documentation. Integration with ERP platforms and batch-specific tracking links individual weights to manufacturing origins, supporting rapid recall execution and regulatory compliance with tamper-proof records.
Beyond core logging, checkweighers facilitate real-time data monitoring through statistical tools and intuitive dashboards, flagging anomalies for immediate action. This capability aligns with Environmental Monitoring by correlating weight deviations to external factors, while also aiding Maintenance Scheduling by identifying equipment performance trends. Exportable reports and historical visibility further enhance compliance with FDA or EU standards, enabling precise identification of defective batches and preventive analysis to minimize giveaway, all while maintaining operational integrity across food production lines.
Adapting to Diverse Product Needs
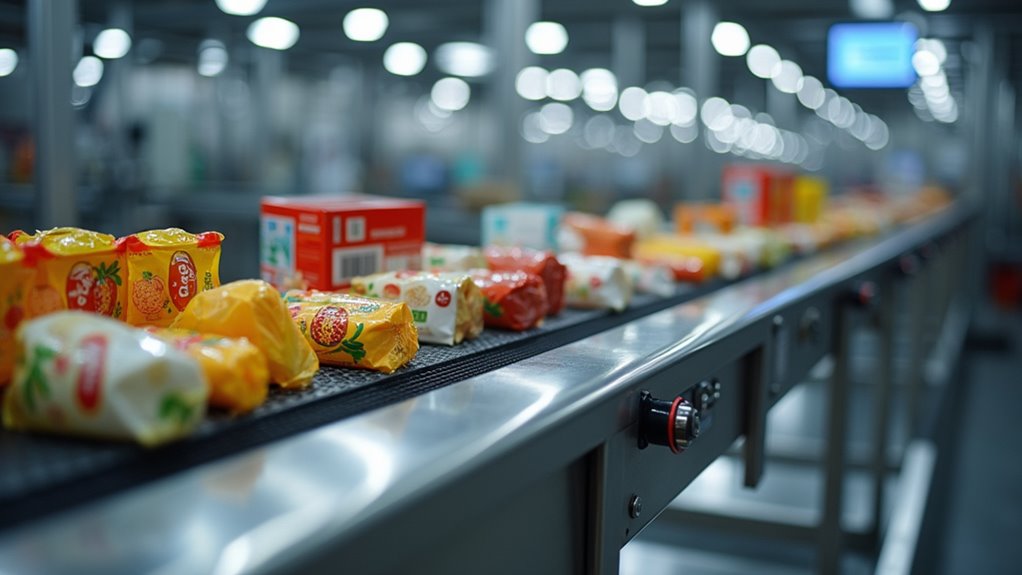
While food production encompasses a wide array of items, checkweighers demonstrate remarkable adaptability to diverse product needs through versatile product handling capabilities. These systems are engineered to process goods across varied sizes, shapes, and weights, ensuring precision in weight verification regardless of product type. This flexibility is critical in high-throughput environments where different items are handled on the same line, maintaining efficiency and compliance with regulatory standards.
To highlight their adaptability, consider the following technical aspects of checkweighers:
- Adjusting Settings: Operators can fine-tune parameters to accommodate specific product dimensions and weight ranges, ensuring accurate measurements.
- Product Customization: Tailored configurations allow seamless integration for unique packaging or material types, optimizing performance.
- Dynamic Processing: Advanced algorithms adapt to varying product characteristics in real-time, minimizing errors.
This capacity for adjusting settings and enabling product customization ensures checkweighers meet the stringent demands of diverse food industry applications with analytical precision.