For businesses seeking efficient product labeling, top machines include compact DYMO® models for small spaces, high-speed HERMA 500 systems exceeding 100 labels per minute, and GEA PowerPak thermoforming applicators for versatile packaging. Rotary systems with servomotor precision, portable Brady M210 options, semi-automatic Primera AP380 units, and industrial ALritma X powerhouses offer tailored solutions. These ensure accuracy, compliance, and scalability across industries. Exploring further unveils detailed insights into optimizing labeling for specific operational needs.
Key Takeaways
- Compact small-business labelers like DYMO® offer space-saving designs with speeds up to 71 labels per minute.
- High-speed machines, such as HERMA 500, achieve over 200 meters per minute for mass production.
- Thermoforming applicators like GEA PowerPak integrate labeling with eco-friendly materials for varied packaging.
- Rotary systems use servomotors and vision sensors for precise, multi-directional labeling in one pass.
- Portable options like Brady M210 provide lightweight, battery-operated solutions for low-volume tasks.
Compact Small-Business Labeling Solutions
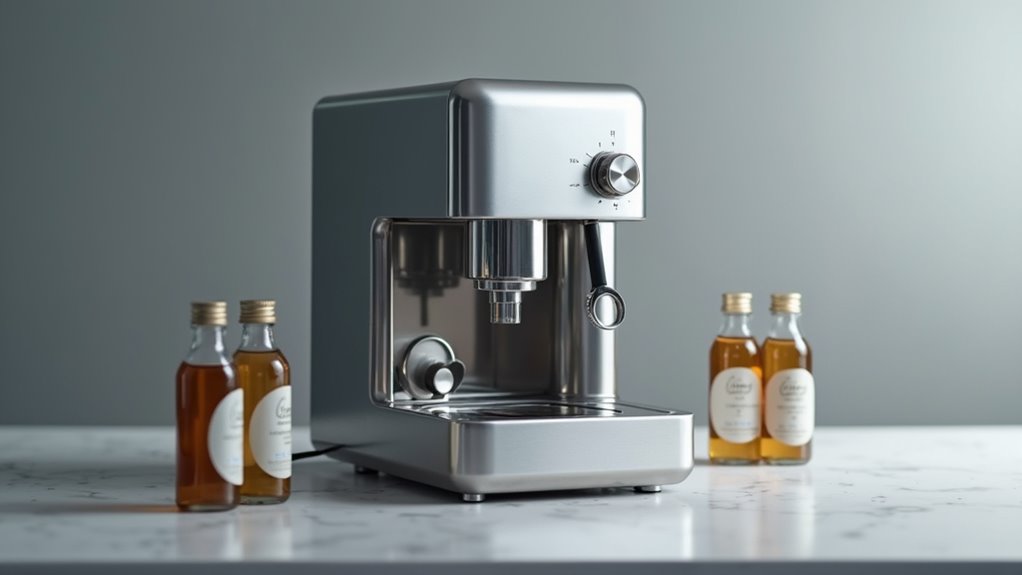
For small businesses operating in confined environments, compact labeling solutions offer a critical balance of functionality and space efficiency. These devices are engineered with a space saving design, ensuring they fit seamlessly into limited workspaces without compromising on performance. The lightweight construction of models like DYMO® label makers further enhances their suitability as ideal deskmates, allowing easy repositioning and minimal clutter in tight office settings.
Analyzing their technical capabilities, DYMO® label makers demonstrate an impressive output capacity, printing up to 71 labels per minute. This efficiency caters to the demands of small-scale operations where quick labeling is essential for inventory management and customer service. The combination of portability and performance in these compact units addresses the spatial constraints faced by small businesses, providing a practical solution without the need for expansive equipment. Such designs ensure operational agility, maintaining productivity in environments where every inch of workspace matters. Additionally, the use of thermal printing technology eliminates the need for ink and toner, reducing ongoing costs for small business owners.
High-Speed Machines for Mass Production
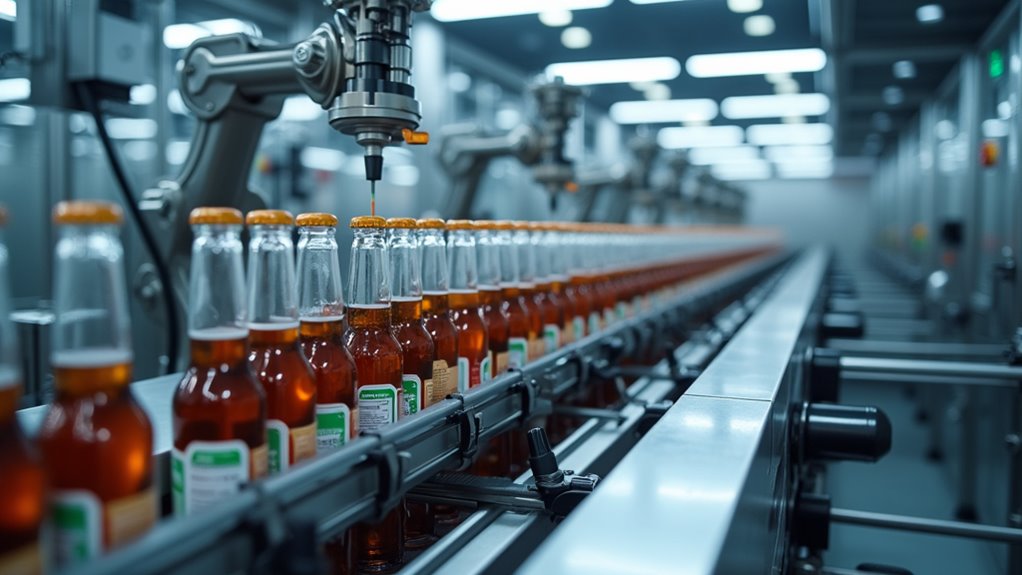
How do industries meet the relentless demands of mass production labeling with precision and efficiency? High-speed labeling machines offer a robust solution, delivering exceptional labeling speed, often ranging from 100 to over 1,000 labels per minute. Models like the HERMA 500 achieve up to 200 meters per minute, synchronizing with product flow for seamless operation. These machines ensure accuracy through advanced controls like photoelectric sensors, adapting to various materials and production volumes with precision.
Equally critical are the diverse interface options, including I/O-Interface, Industrial Ethernet, and touch-screen systems, facilitating integration and user-friendly operation. Such interfaces enable automation, efficient setup, and real-time monitoring, reducing manual intervention. With modular designs and large label roll capacities, downtime is minimized, enhancing operational efficiency. Built for durability and compliance with UL and CSA standards, these machines are indispensable for industries requiring high throughput and reliable performance in mass production environments.
Specialized Thermoforming Packaging Applicators
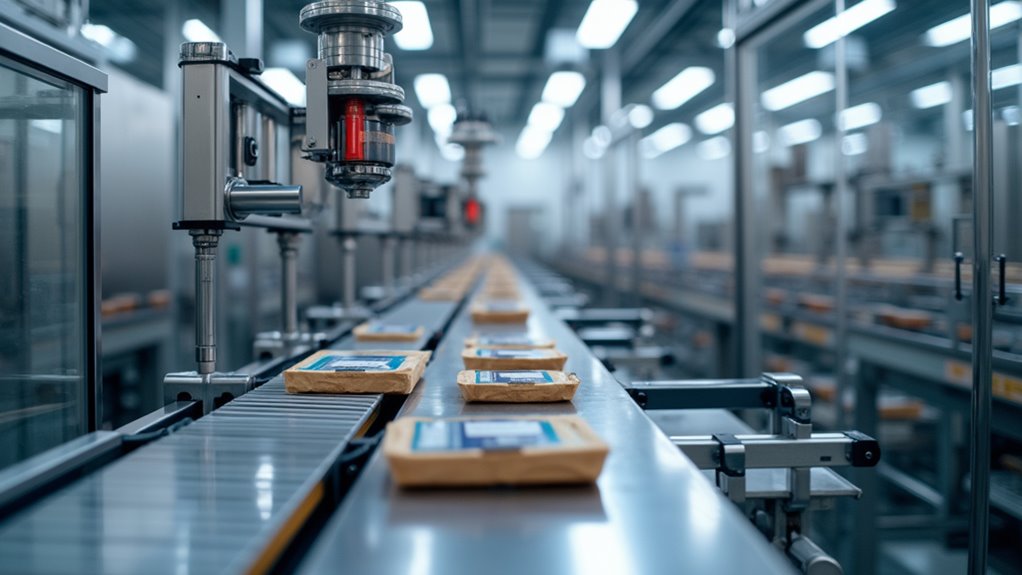
Industries seeking tailored solutions beyond high-speed labeling often turn to specialized thermoforming packaging applicators for integrated forming, sealing, and labeling processes. These systems, such as the GEA PowerPak and Multivac compact thermoformers, offer modular designs with interchangeable components for feeding, heating, and sealing, ensuring adaptability across product sizes with film widths of 240–560 mm. Precision is enhanced by adaptive heating zones and Rockwell Automation controls, minimizing downtime and ensuring consistent packaging quality.
Incorporating eco friendly materials, these applicators support thin-gauge films up to 280 µm for cost efficiency and rigid films up to 700 µm for durability. Integrated labeling features, including top/bottom web film labeling and direct thermal printing, allow for custom printing of high-resolution graphics and barcodes during the forming process. With MAP capabilities for shelf-life extension and energy recovery systems reducing power consumption by approximately 15%, these machines meet stringent global compliance standards like CE/UL and HACCP/GMP.
Rotary Systems for Precise Product Orientation
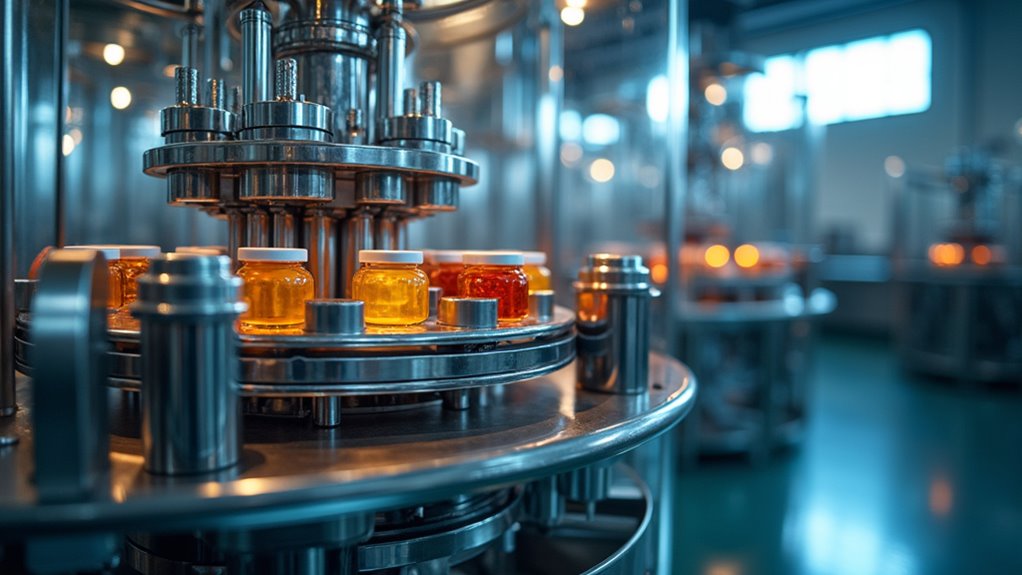
Why settle for inconsistent labeling when precision is paramount? Rotary systems for precise product orientation offer unparalleled accuracy in label application through advanced mechanics and automation. Utilizing rotational movement with fixed angular increments, these systems ensure exact workpiece positioning via servomotor drives and mechanical indexing, minimizing wear and enhancing repeatability. Sensors and vision systems detect and correct misalignments, while actuators reposition items mid-process, maintaining consistency across orientations.
In industries like pharmaceuticals and food and beverage, precision control is critical for regulatory compliance and batch uniformity. Circular platform rotation and adjustable speeds synchronize with production lines, enabling multi-directional labeling in a single pass. With equipment customization, programmable platforms adapt to diverse container shapes, supported by vision-guided actuators and servo-electric drives. This results in reduced labor costs, lower error rates, and minimal maintenance, delivering efficient, high-speed output for businesses seeking reliable labeling solutions.
Portable and Semi-Automatic Labeling Options
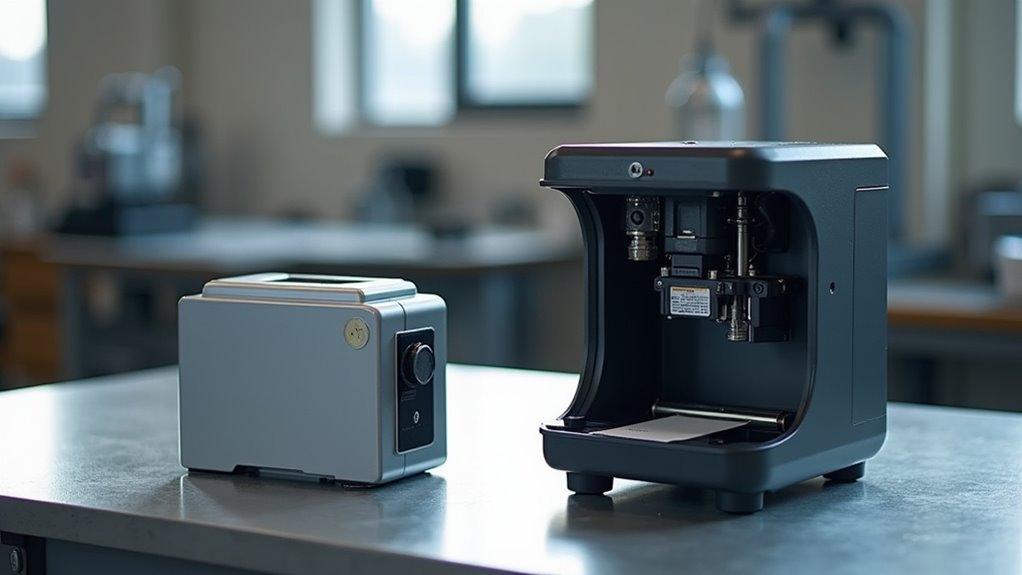
Portable labeling solutions, such as the M210 Handheld Label Maker, offer compact versatility with thermal transfer printing at 203 dpi and a capacity for low-volume tasks up to 100 labels per day. In contrast, semi-automatic systems like the Primera AP380 enhance efficiency by applying up to 1500 labels per hour with dual-label capabilities for cylindrical containers. These technologies address distinct operational needs, balancing mobility and higher throughput for varied labeling applications.
Versatile Portable Solutions
While labeling demands vary across sectors, versatile portable solutions offer a practical balance of mobility and efficiency for diverse applications. These systems, including handheld label makers like the Brady M210 and Brother Handheld Labeller, cater to retail, industrial, and field service needs with lightweight designs and battery-operated functionality. Advanced features such as a streamlined user interface ensure quick setup, while remote monitoring capabilities allow for operational oversight in dynamic environments.
Visualize the impact of these tools through:
- A warehouse worker printing asset tags on-site with the rugged Brady M210.
- A retail clerk crafting promotional QR codes via Brother’s LCD display.
- A field technician labeling cables seamlessly with battery-powered portability.
Their adaptability and precision make them indispensable for varied labeling tasks.
Semi-Automatic Efficiency Gains
As businesses seek to optimize labeling processes without the high costs of full automation, semi-automatic labeling machines emerge as a compelling solution for low-to-mid-volume operations. Valued at $1.43 billion in 2023, this market segment offers cost-effective scalability, achieving up to 30% throughput gains through balanced human-machine workflows. These systems provide customization flexibility, allowing rapid format switching for specialty production in sectors like pharma and food.
Despite requiring manual intervention for tasks such as product placement, semi-automatic machines reduce labor demands and enhance consistency with hybrid dispensing mechanisms. Their lower upfront investment, minimal infrastructure needs, and data-driven adjustments ensure precise operation. Additionally, IoT-enabled monitoring and modular upgrades support long-term efficiency for small-to-medium enterprises navigating variable labeling demands.
Versatile Multi-Position Label Placement Equipment
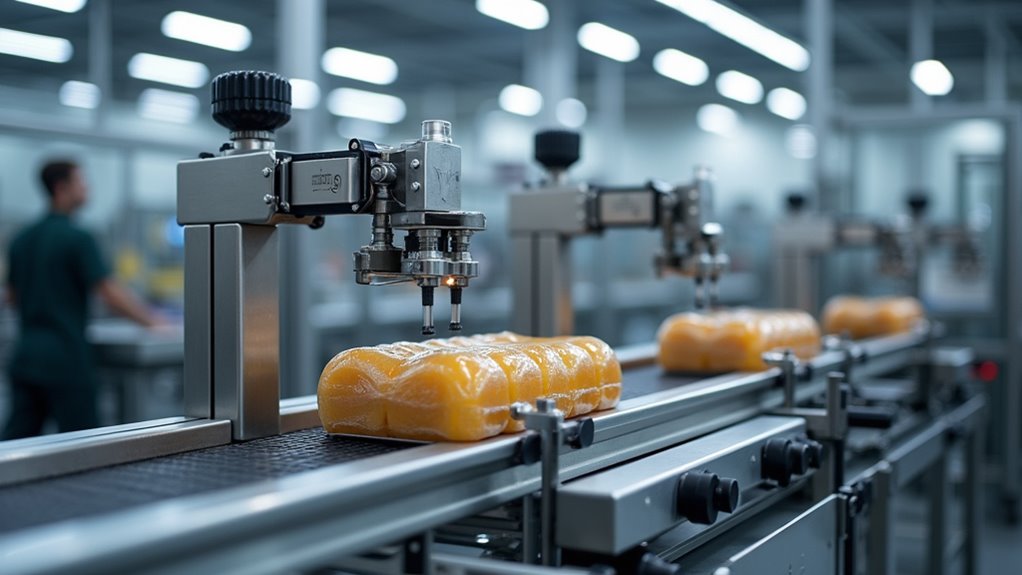
Given the diverse needs of modern packaging lines, versatile multi-position label placement equipment offers a sophisticated solution for applying labels with precision across various product surfaces. These systems incorporate advanced technologies like robotic integration for seamless operation and software customization to adapt to specific labeling requirements. With features such as air blow, tamp, and merge application noses, alongside DAT applicators, they ensure accurate multi-panel labeling on diverse container shapes using adjustable pneumatic modules and 2D/3D vision systems for error detection.
Versatile multi-position label placement equipment delivers precision across diverse product surfaces, integrating advanced robotics and customizable software for seamless, accurate labeling solutions.
Imagine the efficiency of these machines through:
- Air blow systems using vacuum grids to secure labels before precise application.
- Three-panel setups simultaneously labeling leading edges, tops, and sides of moving products.
- Saloon-door-style applicators dispensing labels across conveyor paths with flawless alignment.
Compliance is maintained with 600dpi printers and critical alarm systems, while interchangeable nose assemblies and microprocessor controls enhance flexibility for tailored production needs.
Industrial Powerhouses With Exceptional Throughput
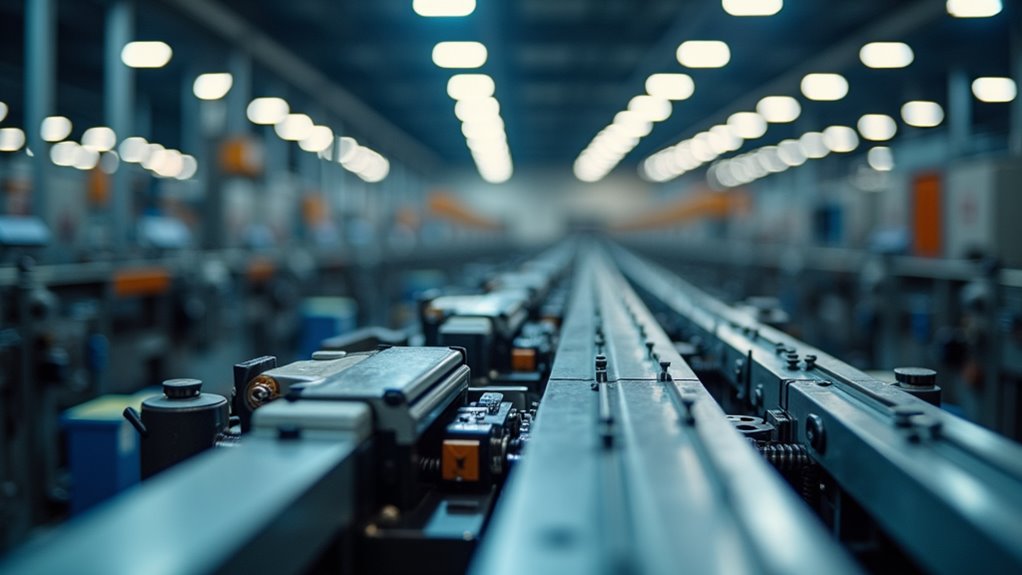
How do industrial labeling machines achieve unparalleled efficiency in high-demand production environments? These industrial powerhouses, such as HERMA Labeling Systems and LabelMill LM3612, are engineered for exceptional throughput, applying over 100 labels per minute with precision across diverse container types like flat, oval, or round. Their advanced PLC systems, including Allen-Bradley controls, and user-friendly touchscreen interfaces ensure seamless operation during 24/7 production cycles. Automation integration plays a critical role, enabling these systems to adapt to various industrial settings and connect via Ethernet or USB for streamlined workflows.
Moreover, high-speed applicators like the ALritma X, with speeds up to 40 meters per minute, support multiple label formats, enhancing versatility. Robust designs prioritize durability, while some systems incorporate sustainability practices by minimizing material waste during operation. Collectively, these features position industrial labeling machines as indispensable assets for businesses aiming to maximize output and maintain precision in competitive markets.