Belt weighing conveyors are critical for measuring the flow rate of bulk materials, incorporating load cells to convert weight into electrical signals. Accuracy, influenced by calibration and maintenance, meets specific industry standards, with some systems achieving ±0.125% accuracy. Essential in mining, agriculture, and manufacturing, they enhance operational efficiency and product quality. Real-time data integration facilitates comprehensive monitoring and control, supporting various network protocols for extensive data analysis. Technological advancements continue to improve measurement accuracy and material handling capabilities.
Key Takeaways
- Belt weighing conveyors accurately measure material flow rates with load cells and signal processors.
- They offer high accuracy with permissible errors as low as ±0.125% to ±0.25% per OIML R 50 standards.
- Regular calibration and maintenance ensure reliable weight measurements and long system lifespan.
- These systems enhance operational efficiency through real-time data monitoring and integration with control systems.
- Technological advancements continue to improve measurement accuracy, with specialized designs for diverse material handling.
Components and Operating Principles
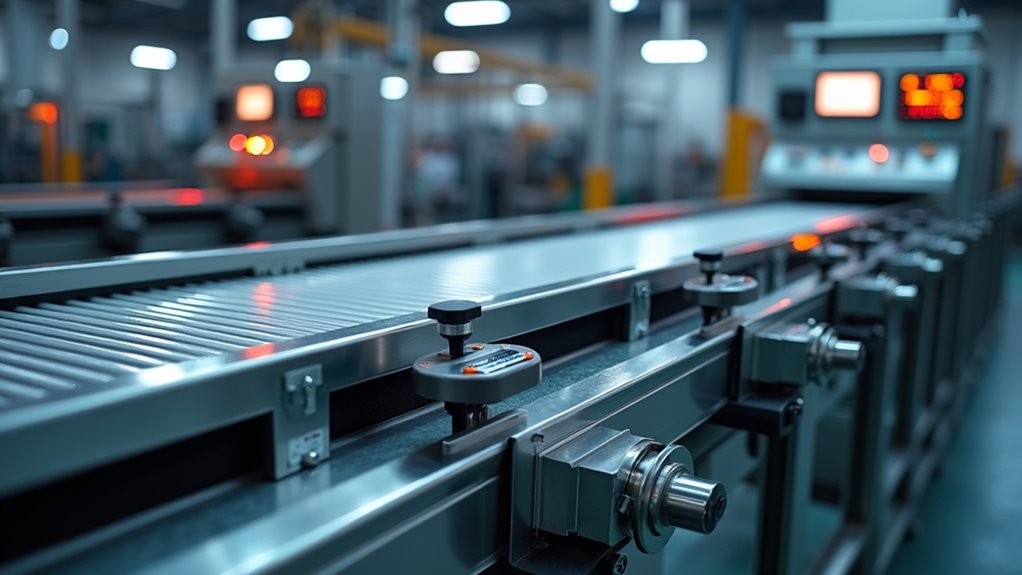
Belt weighing conveyor systems are sophisticated systems designed to measure the flow rate of bulk materials during transport.
At the core of these systems are several design features, including the weighing frame, conveyor belt and material support, and load cells that convert the material’s force into an electrical signal.
The selection of load cell types, such as strain gauge load cells, is critical to ensuring minimal deflection and temperature stability.
Choosing the appropriate load cell type, like strain gauge load cells, is crucial for maintaining minimal deflection and temperature stability in weighing applications.
Integrators process signals from load cells and speed sensors to calculate material flow rates, making these conveyors essential for accurate and continuous weighing in industrial applications.
Multi-idler belt weighing systems are recommended for high accuracy and are commonly used in fertilizer, cement, and power plants, facilitating in-line weighing and saving time and effort.
Accuracy and Calibration
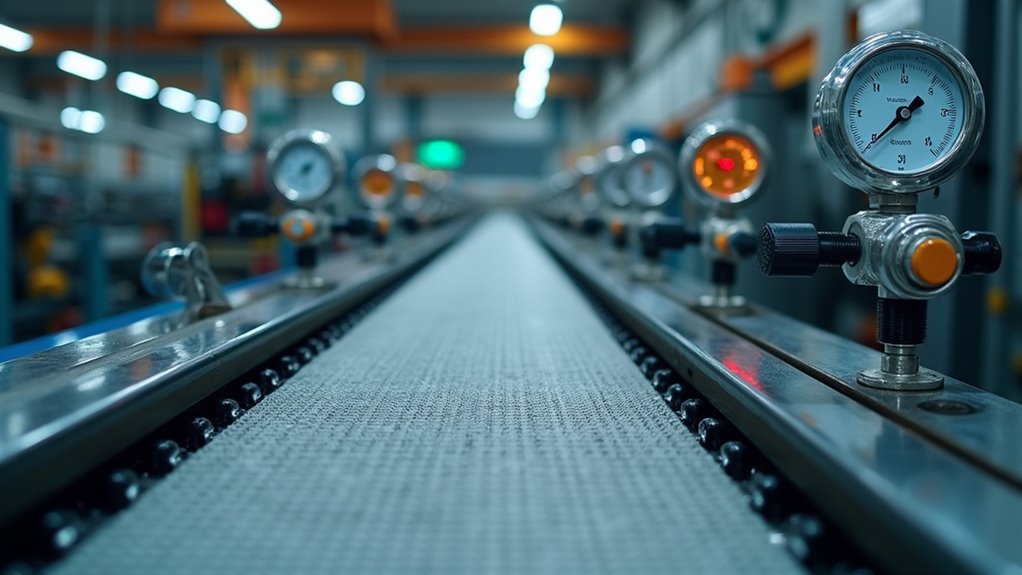
In belt weighing conveyors, accuracy is classified into different categories based on application requirements and industry standards.
Calibration methods, including zero calibration, span calibration, material test calibration, and electronic calibration, are essential for ensuring the accuracy of recorded mass values.
The choice of calibration method and adherence to proper calibration procedures directly impact the reliability of the conveyor’s mass measurements.
Accuracy Classes Explained
Understanding the accuracy classes of belt weighing systems is crucial for selecting the appropriate system based on application requirements. The OIML R 50 standard outlines four accuracy classes: 0.2, 0.5, 1, and 2, each corresponding to the maximum permissible error for automatic weighing.
For instance, Class 0.5 belt scales have an MPE of ±0.25% for initial verification and ±0.5% for in-service verification. In the United States, NTEP certification ensures scales meet NIST Handbook 44 specifications, requiring accuracy within ±0.25% of actual material load.
Accuracy standards are influenced by mechanical components, conveyor design, material characteristics, environmental conditions, and installation quality, all of which can cause measurement variations.
High-accuracy systems, suitable for custody transfer or high-value materials, can achieve accuracies from ±0.125% to ±0.25%, often utilizing multi-idler configurations with advanced load cell technology.
Overview of Calibration Methods
Calibration of belt weighing conveyors is a critical aspect of ensuring accurate and reliable weight measurements during material handling. Various calibration techniques are employed to maintain this accuracy, each serving a specific purpose with recommended frequencies.
Calibration Method | Purpose | Recommended Frequency |
---|---|---|
Zero Calibration | Establish baseline | Daily or shift start |
Span Calibration | Adjust accuracy | Monthly or quarterly |
Material Test Verification | Verify during operation | Semi-annually |
Repeatability Test | Confirm consistency | Before calibration |
The frequency of these calibration methods depends on factors such as environmental conditions and application criticality, emphasizing the need for regular and systematic calibration practices to ensure weighing system integrity.
Applications and Industrial Use
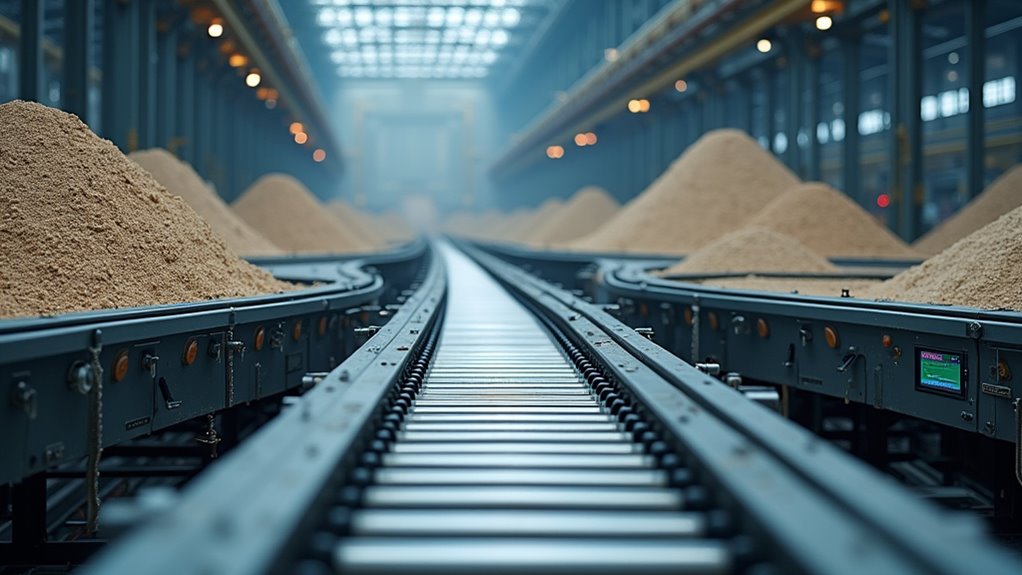
Belt weighing conveyors are widely applied in process control, where they monitor and manage material flow during various stages of production.
They are particularly vital in industries such as mining, agriculture, manufacturing, logistics, and construction to ensure accurate material handling and product quality.
Moreover, these systems are indispensable for load-out operations and invoicing, providing accurate measurements necessary for capacity planning and financial transactions.
Process Control Applications
Process control applications of belt weighing conveyors are integral to industries for optimizing production efficiency and maintaining product quality.
By precisely controlling feed rates, these systems prevent overloading or underfeeding downstream equipment, ensuring stable material flow, which is critical for production efficiency. They are indispensable in blending and mixing operations, where maintaining consistent material ratios per formula is vital for product quality.
Belt weighing conveyors also play a key role in quality control, minimizing material flow variations to ensure final products meet quality standards.
Their integration with automated systems enables real-time process adjustments, further enhancing production efficiency and product quality.
Load-Out and Invoicing
In many industries, load-out and invoicing are critical stages requiring high accuracy.
Belt weighing conveyors facilitate accurate material measurement, essential for efficient logistics and economical transportation. In industries where load-out accuracy is critical, automated systems allow programming of target weights for trucks, railcars, and ships, preventing fines and contract disputes.
For invoicing, “Legal for Trade” certification ensures that belt weighing conveyors meet stringent regulatory standards, with components like NTEP-certified load cells guaranteeing accuracy.
Compliance with international guidelines, such as those from the International Organization of Legal Metrology (OIML), ensures uniformity in weighing system standards, fostering trust through accurate weight-based transactions.
Maintenance and Environmental Considerations
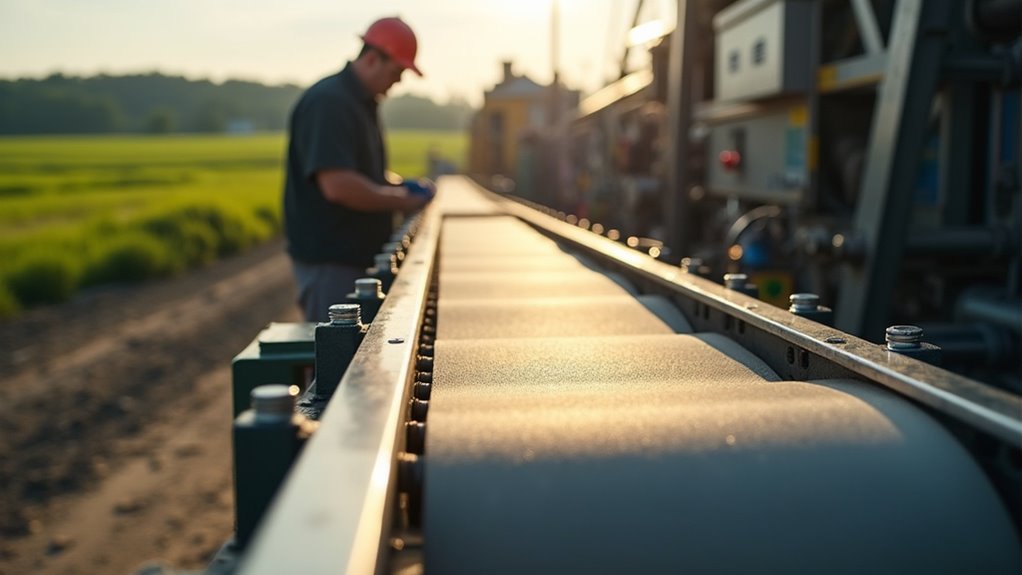
The installation of belt weighing conveyors is critical to their performance, but maintaining these systems and considering environmental factors are equally important to ensure accurate and reliable measurements.
Preventive maintenance and careful consideration of environmental impacts are essential for the long-term reliability of belt weighing conveyors.
- Regular Inspection and Calibration: Routine checks and scheduled calibration maintain accuracy and prevent measurement interference.
- Environmental Protection: Shielding conveyors from extreme temperatures, humidity, and windy conditions is crucial to minimize environmental impacts on accuracy.
- Mechanical Adjustments: Ensuring proper belt tension, alignment, and roller maintenance is necessary to keep conveyors operating within design tolerances, thereby enhancing measurement accuracy.
System Variants and Improvements
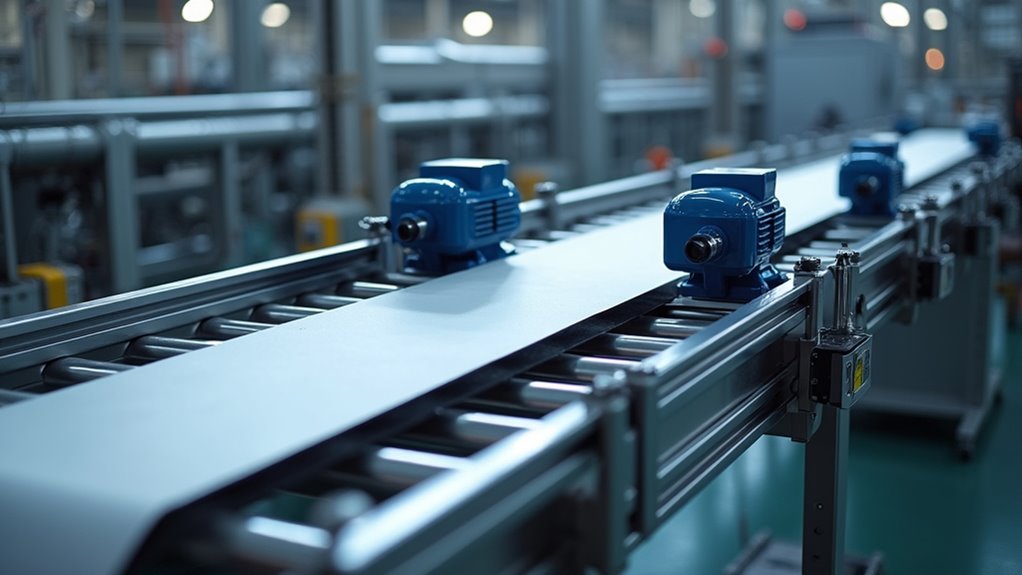
As conveyor systems evolve to meet the diverse needs of various industries, belt weighing technologies also advance, ensuring accurate and efficient measurement of materials during transport.
System variants include the integration of modular flexibility, enabling easier installation and adaptation to different conveyor configurations, such as those with limited space or specialized designs for handling powdered materials.
Improvements in weighing technology also include advanced speed sensors, critical for accurate weight calculations. These sensors, ranging from optical segmented disks to electromagnetic pulse generators, accurately detect conveyor speed, contributing to the overall accuracy of the weighing process. Additionally, the integration of high-speed checkweighers further enhances operational efficiency and regulatory compliance across various sectors.
Data Integration and Real-Time Reporting
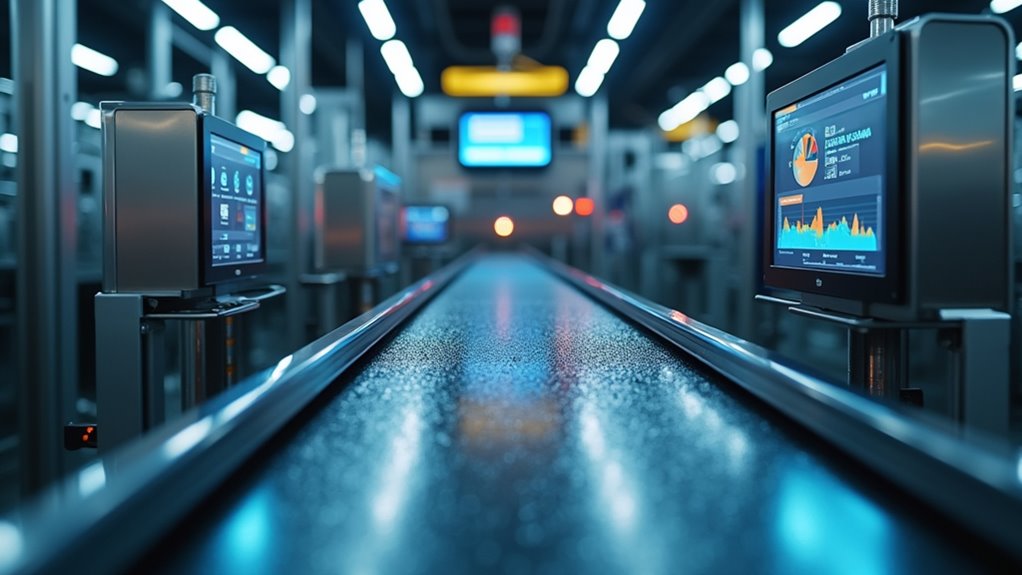
Belt weighing conveyors not only provide continuous real-time data on material flow and weight but also offer a comprehensive suite of monitoring features that enhance operational efficiency.
Belt weighing conveyors: Enhancing efficiency through real-time material flow data, comprehensive monitoring, and seamless operational integration.
These systems are equipped with advanced data integration and reporting features, which are critical for modern industrial operations.
- Data Integration with Control Systems: Belt weighing conveyors seamlessly integrate with PLC or SCADA systems, enabling real-time automated adjustments to production processes based on a continuous stream of accurate weight data.
- Comprehensive Reporting and Data Logging: Detailed reports on material usage and flow rates, along with extensive data logging, support historical analysis and informed decision-making.
- Connectivity and Communication Options: With multiple communication ports and support for various network protocols, these conveyors ensure data accessibility from any internet-connected device, facilitating remote monitoring and control.