Calibrating a belt scale involves understanding its components, preparing the conveyor, and performing zero and span adjustments. Material tests verify accuracy, while repeatability ensures consistent measurements. Regular calibration, including zero and span settings as well as material tests, maintains accuracy. Certified weights or chains are essential for span calibration, and comparison with static scales verifies operational accuracy. Ensuring reliability and accuracy through consistent checks is critical, with daily zero calibrations and monthly span calibrations recommended, hinting at the detailed processes involved.
Key Takeaways
- Prepare the conveyor by ensuring it is clean, tensioned, and aligned before starting calibration.
- Perform zero calibration daily or at the start of each shift to establish an accurate measurement baseline.
- Conduct span calibration monthly to ensure accuracy across the full operating range.
- Verify accuracy through material tests, comparing belt scale measurements with certified static scales.
- Ensure repeatability and accuracy through consistent checks, addressing mechanical issues before adjusting for accuracy.
Understanding Belt Scale Components
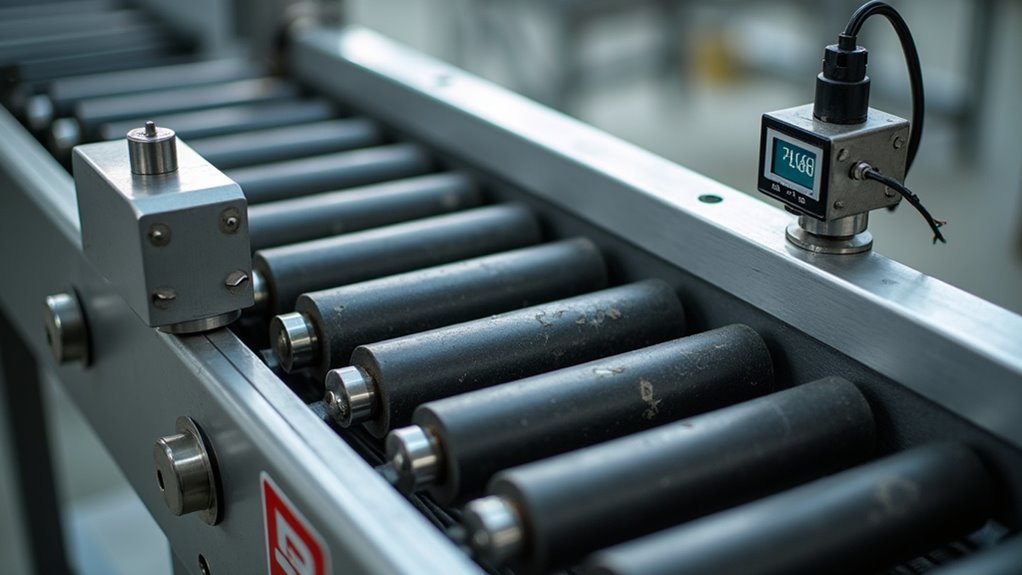
The accuracy and reliability of a belt scale system depend on the precise operation and integration of its core components.
Load cells are critical in this system, functioning to convert the mechanical force from the material weight on the conveyor into a quantifiable electrical signal.
Load cells play a pivotal role in the belt scale system, converting the material weight on the conveyor into a quantifiable electrical signal, ensuring accurate measurements.
Strain gauge sensors, embedded within load cells, are crucial by detecting the applied force and generating an electrical signal proportional to that force.
This signal is then processed by the integrator, which, when combined with data from the speed sensor, calculates the flow rate and cumulative total weight of the material.
The integration of a speed sensor is vital as it provides accurate data on the conveyor’s speed, a key factor in determining the material flow rate.
Thus, the functionality of load cells and the role of strain gauge sensors are fundamental to ensuring the accuracy of belt scale measurements.
Preparing for Calibration
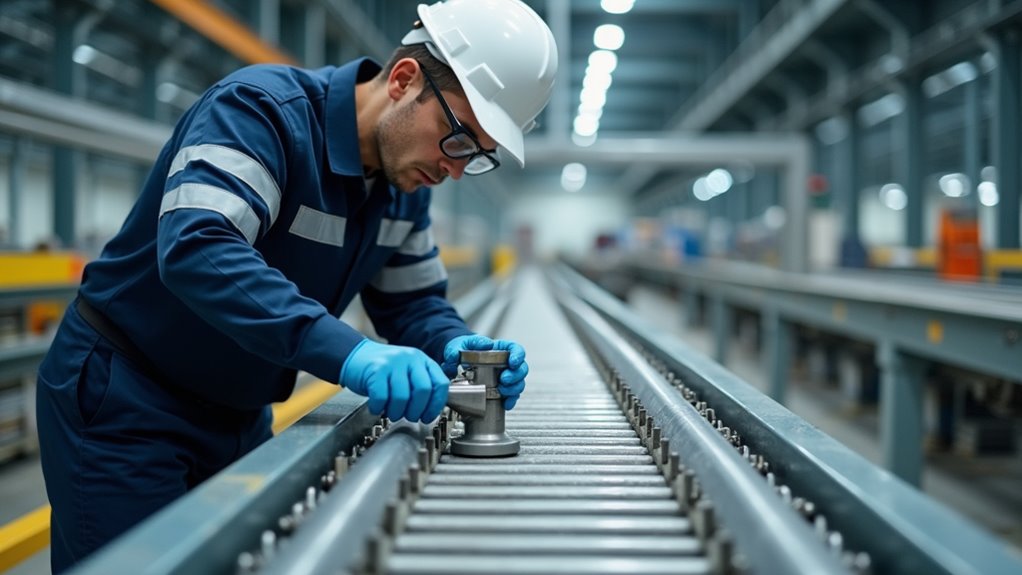
The calibration preparation process demands a meticulous approach to ensure the accuracy of the belt scale system. A pre-calibration checklist is crucial for systematically assessing the conveyor’s condition, including inspecting the belt, idlers, and mechanical components.
Safety measures must be strictly adhered to, with all power sources locked out and only authorized personnel conducting the calibration. The use of certified scales or test chains is mandatory, and the manufacturer’s service manual must be consulted for model-specific procedures.
Ensuring the conveyor is conditioned, properly tensioned, and aligned is essential before proceeding with calibration to achieve accurate and reliable weighing results.
Performing Zero and Span Calibration
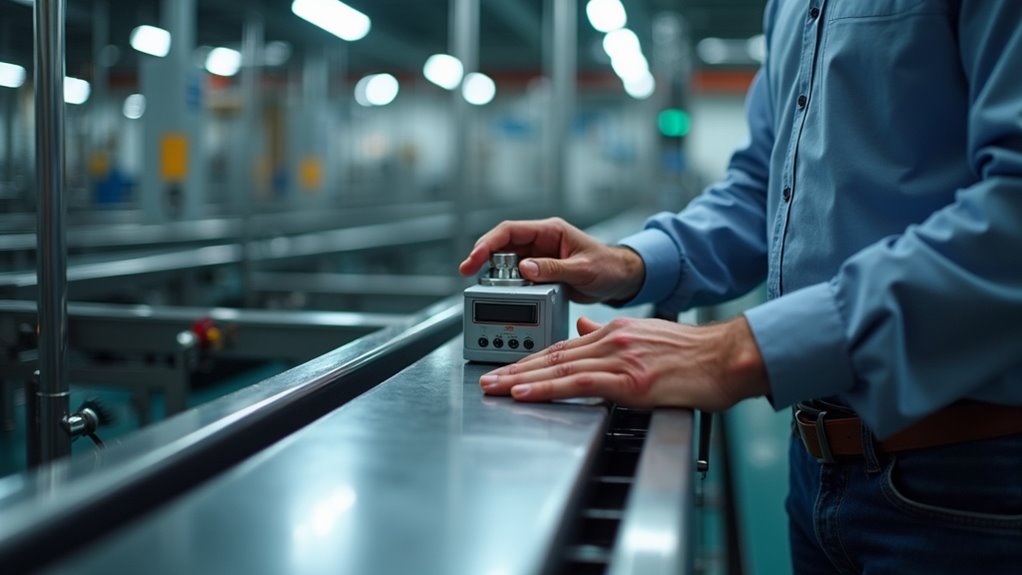
Initiating zero calibration lays the foundation for accurate weight measurements in the conveyor system. This process, recommended daily or at the start of each shift, involves running the conveyor empty to establish a baseline weight. Changes in belt tension, temperature, or material buildup require frequent zero adjustments to maintain system accuracy.
Calibration Type | Frequency | Procedure | Importance |
---|---|---|---|
Zero Calibration | Daily or per shift | Run empty conveyor, measure weight | Establishes baseline |
Span Calibration | Monthly | Use certified test weights or chains | Ensures full-range accuracy |
Span calibration complements zero calibration, using certified test weights or chains to verify the scale’s accuracy across its operating range, typically performed monthly.
Conducting Material Test Calibration
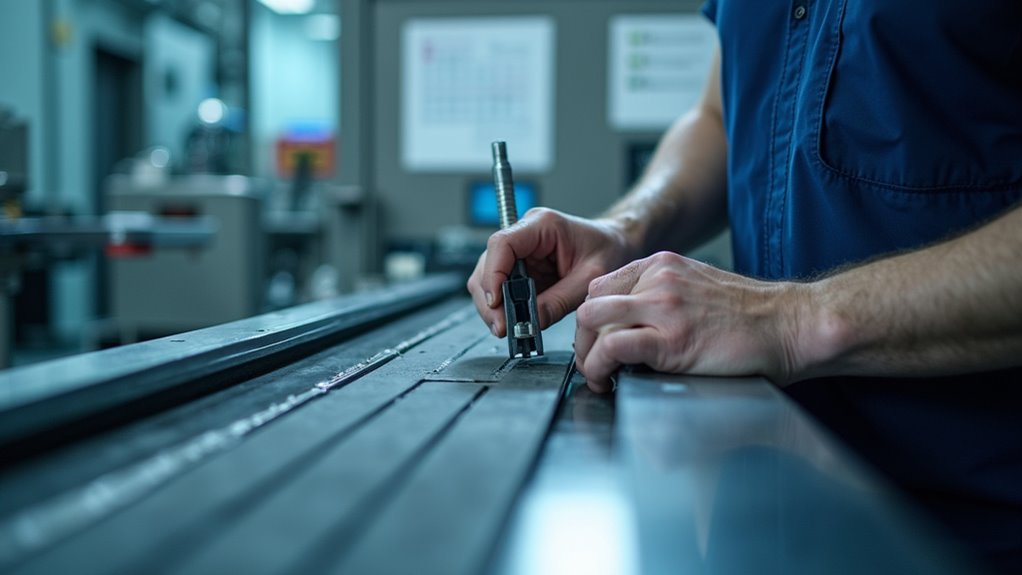
Validating the accuracy of a belt scale through material test calibration is essential to ensure precise weight measurements in operational environments. This process involves comparing the weight recorded by the belt scale with a certified static scale, using specific test methods to handle and evaluate materials.
Pre-test preparations include verifying the accuracy of the reference scale and inspecting the conveyor and idlers for any issues that could affect test reliability. Material handling during testing requires careful sampling and feeding materials into the conveyor system under normal operating conditions.
The test execution involves running at least three material samples through the scale, recording initial and final readings from the totalizing integrator, and making necessary adjustments to the scale’s integrator based on the results. This meticulous approach ensures the belt scale’s performance is validated under real-world conditions, providing confidence in measurement accuracy.
Ensuring Repeatability and Accuracy Through Testing
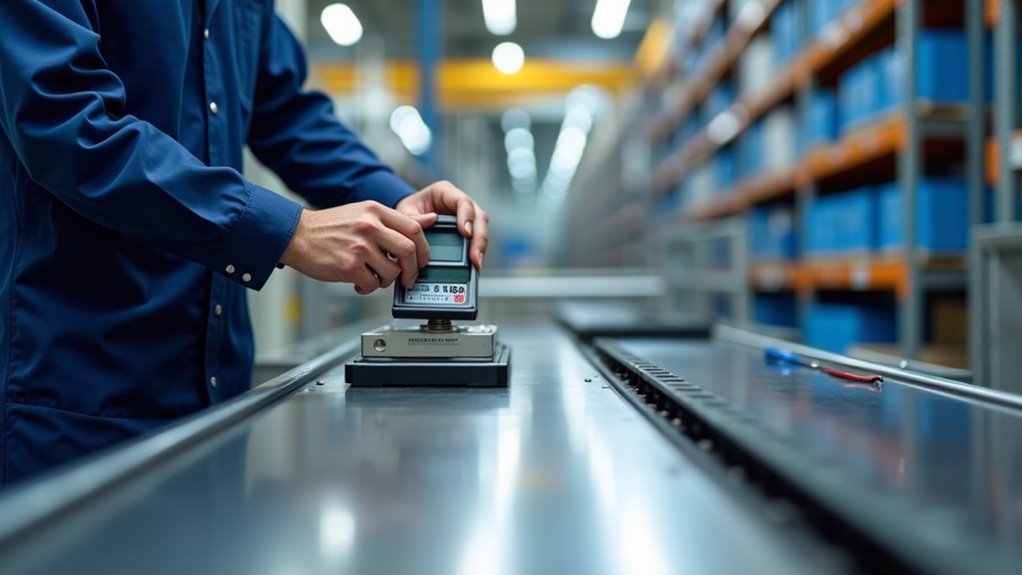
To ensure the integrity of weight measurements in industrial applications, focusing on the repeatability and accuracy of belt scales through rigorous testing is essential. Repeatability, defined as the ability of the belt scale to produce consistent results under identical conditions, is a prerequisite for accuracy, which is the ability to match the true measurement, requiring consistency. Test consistency is critical for assessing measurement reliability and identifying any mechanical issues that need resolution before accuracy can be adjusted.
Repeatability | Accuracy |
---|---|
Consistent results under identical conditions | Matches the true measurement |
Prerequisite for accuracy | Achieved after repeatability is established |
Assessed through initial tests | Adjusted after repeatability is established |
Zero calibration tests establish a baseline by measuring the weight of an empty conveyor, which should be performed daily or weekly to ensure ongoing reliability.