Tecweigh WY15, Rice Lake 221DB, and Thermo Scientific Ramsey Series 14 are among the top belt scale load cell models, offering high-precision weighing with accuracies within ±0.125%. Siemens Milltronics MSI/MMI and Thayer Scale LC-137/174 employ advanced technologies like parallelogram-style load cells and Force Measurement Suspension Systems (FMSS) for error isolation. These models cater to diverse applications, including mining and food processing, ensuring stability and reliability across environments. Further exploration reveals specific features enhancing their performance.
Key Takeaways
- Tecweigh WY15 offers single-idler precision with ±1/2% accuracy in approved installations using temperature-compensated load cells.
- Rice Lake 221DB is engineered for medium to heavy loads, featuring a dual-arm structure and external mounting for accuracy and ease of maintenance.
- Thermo Scientific Ramsey Series 14 provides high-precision weighing with ±0.125% accuracy, complying with global standards for various industrial applications.
- Siemens Milltronics MSI/MMI incorporates patented parallelogram-style load cells, offering exceptional accuracy and repeatability under uneven loading conditions.
- Thayer Scale LC-137 and LC-174 utilize dual-technology (LVDT and strain gauge) for precise and durable performance across different force capacities.
Tecweigh WY15: Precision in Single-Idler Design
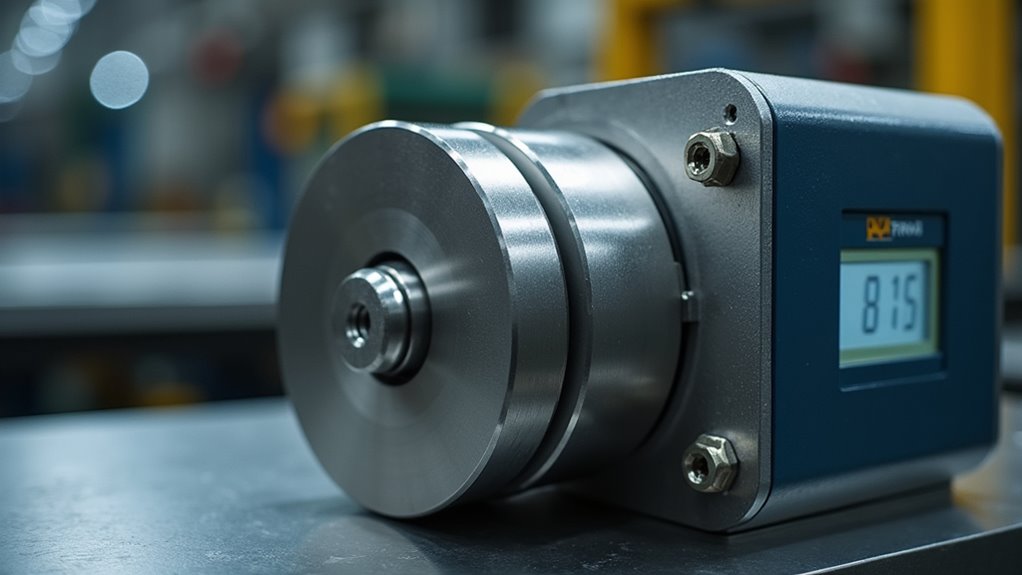
The Tecweigh WY15 belt scale load cell embodies precision in a single-idler design, tailored for weighing materials on conveyor belts with a stated accuracy of ± 1/2% in installations approved by the factory.
This model leverages single idler efficiency by incorporating two NTEP-approved, temperature-compensated bending-beam load cells that ensure accurate measurements across varying conveyor loads. Real-time measurement and verification processes are crucial in ensuring that the WY15 maintains consistent weight accuracy during operation.
The WY15’s design eliminates vulnerable components such as knife edges and bearings, enhancing its durability and reliability in diverse industrial environments. Dynamic range of calibration capabilities offered by companies like Arvus Calibration ensures that equipment like the WY15 can be maintained to provide consistent accuracy and performance.
Its rugged, weather-tight construction further supports its suitability for applications ranging from mining to food processing, underscoring the load cell advantages inherent in its design.
Rice Lake 221DB: The Master Belt Scale for Medium to Heavy Loads
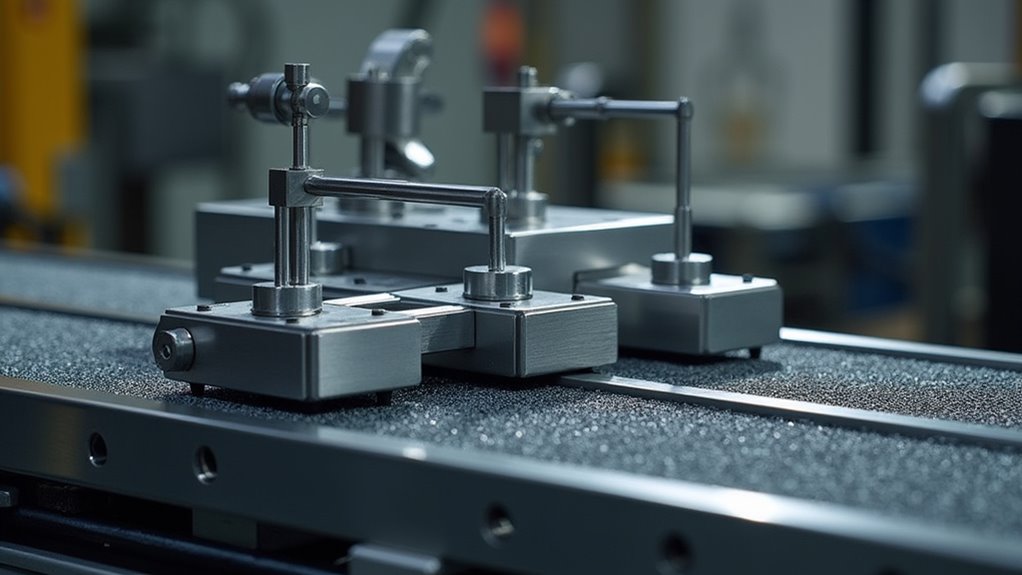
Rice Lake’s 221DB master belt scale stands out in the realm of medium to heavy load weighing with its robust construction and adaptability. Engineered for loads up to 3,300 tons per hour, it features a dual-arm structure with friction-free pivots, ensuring accurate and repeatable measurements.
The external mounting simplifies installation and maintenance, requiring minimal modifications to existing conveyor structures. With conveyor compatibility ranging from 18 to 72 inches in width and options for durable materials including powder-coated mild steel, galvanized, or stainless steel, the 221DB offers versatility across various industry segments. Its design facilitates straightforward assembly and integration into conveyor systems, making it an optimal choice for dynamic weighing applications in bulk material handling.
Thermo Scientific Ramsey Series 14: High-Accuracy Weighing With Global Certifications
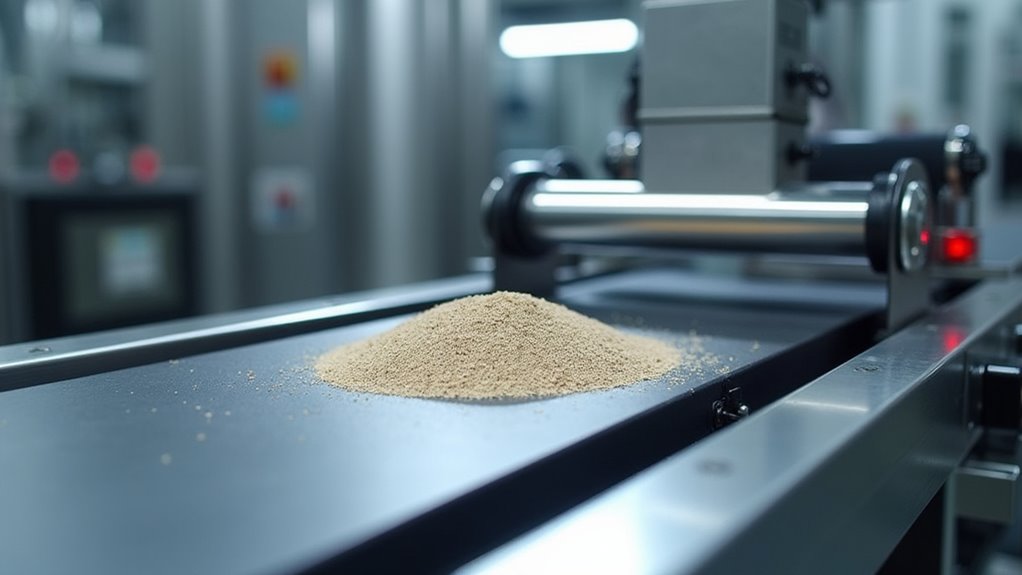
The Thermo Scientific Ramsey Series 14 belt scale system is engineered for high-precision weighing applications, offering an accuracy of ±0.125% which is crucial for basis-of-payment and custody transfer operations requiring government and regulatory certifications.
The system’s weighbridge, constructed from structural steel tubing, features a pivotless design that enhances durability and minimizes maintenance needs.
This series is recognized globally for its performance in loadout, inventory monitoring, and fee-holder situations where certified accuracy is paramount, demonstrating its compliance with stringent industry standards.
Precision and Certification
Designed for applications where precision is paramount, the Thermo Scientific Ramsey Series 14 belt scale system offers high-accuracy weighing with global certifications, ideal for basis-of-payment transactions and inventory monitoring.
The system’s accuracy is guaranteed within ±0.125% of the test load, with repeatability ensured to 0.1% through rigorous calibration methodologies and accuracy assessment protocols.
This precision is upheld across a wide range of flow rates, from 25% to 100% of the scale’s calibrated capacity, making it suitable for diverse industrial applications.
- Certified globally, including NTEP, OIML, and EEC Class 0.5 standards, ensuring compliance with international trade and legal metrology requirements.
- Incorporates advanced technology such as the Ramsey 61-12N belt speed sensor and Ramsey Flex integrator, enhancing measurement stability and reliability.
- Supported by over 60 years of experience in high-accuracy belt scale design, offering unparalleled performance in loadout and inventory monitoring applications.
Weighbridge Design
Integral to the Thermo Scientific Ramsey Series 14 belt scale system is its weighbridge, featuring a suspension-type design configurable with two, three, or four idlers.
Constructed with rigid structural steel tubing, the weighbridge ensures durability and maintains alignment, enhancing weighbridge efficiency. This full-floating, unitized assembly operates without pivots or moving parts, bolstering the suspension system’s longevity.
The design includes four environmentally-sealed precision strain gauge load cells applied in tension. Factory pre-assembled with checkrods, the weighbridge allows for quick field installation.
Suitable for conveyor belt widths from 457 to 2,134 mm, the system requires minimal clearance above the belt line, streamlining installation and operation.
Regulatory Compliance
Beyond its robust mechanical design, the Thermo Scientific Ramsey Series 14 belt scale system distinguishes itself through extensive regulatory compliance, holding key certifications necessary for global deployment. The system navigates complex regulatory frameworks and compliance challenges with certifications including NTEP, OIML, and EEC standards. This ensures its acceptance and reliability in high-accuracy applications worldwide.
- NTEP Certification: Conformance under the National Type Evaluation Program (NTEP) facilitates use in the United States, meeting stringent accuracy requirements.
- OIML and EEC Standards: Compliance with OIML and EEC Class 0.5 or Class I standards enables deployment across international markets, affirming its precision.
- Comprehensive Approvals: cCSAus, CE, and pending certifications like SIL-2, Tick Mark, GOST, and ATEX underscore its versatility and safety for global applications.
Siemens Milltronics MSI/MMI: Innovative Design for Varied Applications
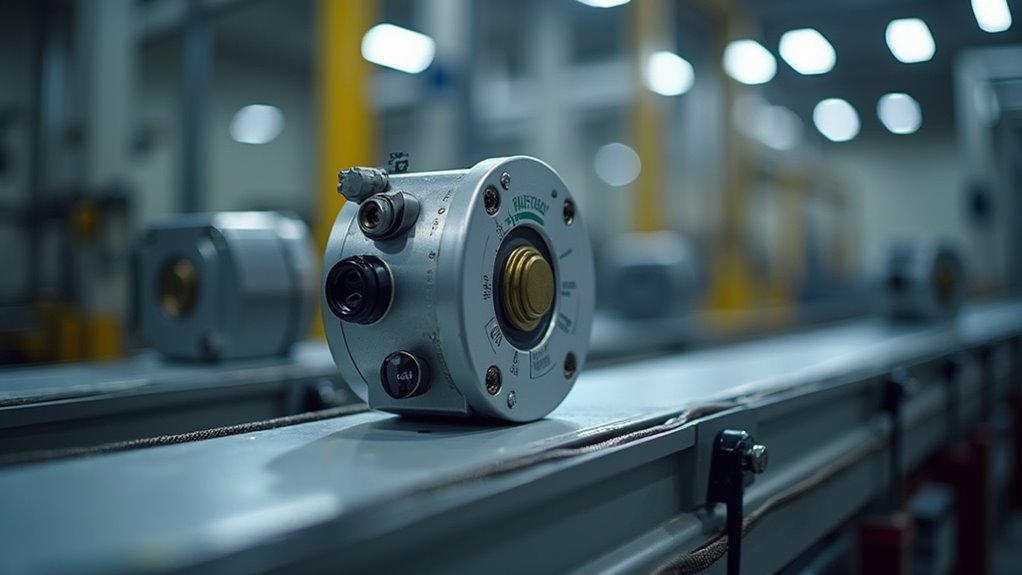
The Siemens Milltronics MSI and MMI belt scales exemplify innovative design principles tailored for a broad spectrum of industrial applications.
The MSI, a heavy-duty single idler belt scale, and the MMI, a high-accuracy multi-idler system, incorporate advanced load cell developments to ensure precise weight measurement across varied industries.
Featuring a patented parallelogram-style load cell design, these belt scale innovations provide rapid response to vertical forces, enabling exceptional accuracy and repeatability even under challenging conditions such as uneven loading and high belt speeds.
With applications spanning mining, power generation, food processing, and chemical industries, the MSI and MMI offer robust, reliable solutions for critical process and load-out control.
Thayer Scale LC-137 and LC-174: Dual Technologies for Enhanced Precision
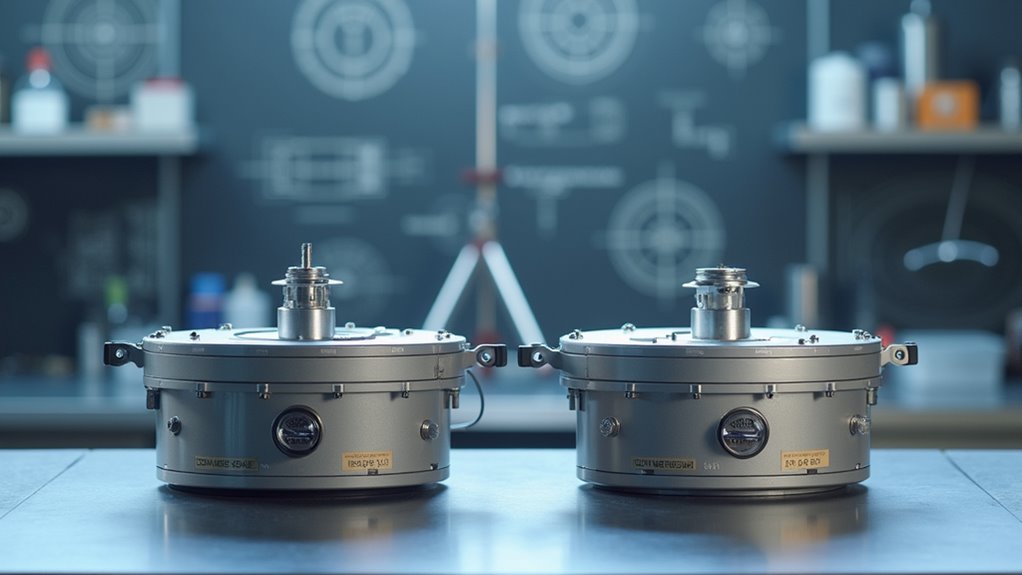
Thayer Scale’s LC-137 and LC-174 load cells employ a dual-technology approach to enhance precision in weight measurement for belt scales, leveraging the innovative Force Measurement Suspension System (FMSS).
This system facilitates the selection of either LVDT or strain gauge technology, with the LC-137 LVDT load cell offering exceptional precision and durability for light loading applications, and the LC-174 strain gauge load cell providing NTEP-approved reliability across a wide range of force capacities.
The FMSS technology ensures the isolation of error-inducing forces, enabling both load cells to deliver accurate and reliable performance in diverse operational environments. Additionally, these load cells are built to maintain weight accuracy within a margin of +/-20g at 2 Sigma, ensuring compliance with stringent industry standards.
LVDT Load Cell Benefits
While LVDT technology is renowned for its precision in measurement, Thayer Scale’s LC-137 and LC-174 load cells offer dual technologies that harness these benefits for enhanced performance.
The LC-137, utilizing LVDT advantages, provides a non-contact method for converting linear motion into electrical signals, ensuring high accuracy and repeatability. This technology is especially beneficial in harsh industrial environments due to its robust construction and resistance to mechanical wear.
- Infinite resolution allows for precise measurement of small displacements.
- The absence of physical contact between core and coil eliminates degradation of accuracy over time.
- Dual-technology options cater to a wide spectrum of application requirements, offering both LVDT and strain gauge load cells to optimize performance.
NTEP-Approved Strain Gauge
NTEP-approved strain gauge load cells, LC-137 and LC-174, offered by Thayer Scale, embody dual technologies tailored for precise weight measurement in diverse industrial applications. These load cells represent a significant innovation in the field of strain gauge applications, providing versatility and accuracy across a broad spectrum of industrial needs.
Feature | LC-137 (LVDT) | LC-174 (Strain Gauge) |
---|---|---|
Technology | Tension-style force | “S” beam strain gauge |
Force Ranges | 5 to 465 pounds | 25 to 2,000 pounds |
Overload Protection | 200% of rated output | 1.5% of rated output |
Certification | High precision | NTEP-approved |
Unique Feature | 15-year guarantee | Interchangeability |
Force Measurement Suspension System
In the realm of industrial weighing, the Force Measurement Suspension System (FMSS) stands out as a revolutionary approach, integrating dual technologies to enhance precision in belt scale loadcells. It employs a mechanical structure that filters force vectors, allowing only vertical forces to reach the load cell.
This system is compatible with both the LC-137 LVDT and LC-174 strain gauge load cells, offering flexibility to match application requirements.
- Utilizes an active mechanical structure to isolate and transmit only vertical load forces, enhancing measurement accuracy.
- Compatible with both LVDT and strain gauge technologies, providing a versatile solution for various application needs.
- Eliminates the impact of extraneous forces such as belt tension and friction, ensuring reliable and consistent measurements.
Tecweigh WY10: Rugged Reliability for Extreme Conditions
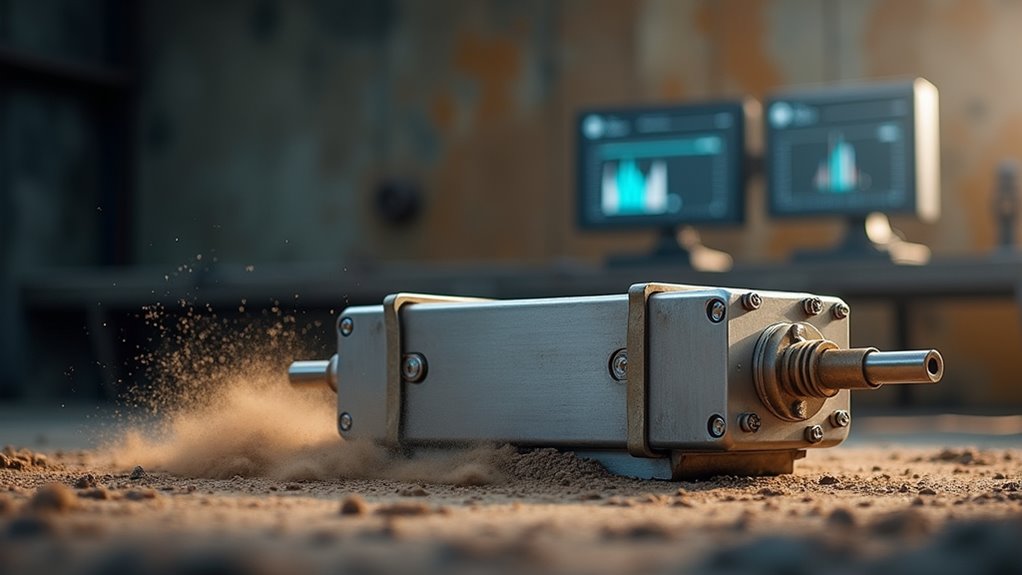
The Tecweigh WY10 belt scale is engineered for rugged reliability, capable of enduring the most extreme industrial environments.
Its robust, one-piece welded construction ensures weather-tight protection against dust, dirt, and harsh weather, while its rugged steel carriage offers durability in tough conditions.
Utilizing LVDT load sensors, it provides accurate weight measurement (±1/2% in single idler configuration) and is resistant to overloading and lightning damage.
Designed for high flow rates, the WY10 maintains performance in the harshest settings, though care should be taken in extreme cold to prevent ice buildup.
Features like self-storing calibration weights and a user-friendly processor enhance its reliability and ease of use.
Multi-Idler Weigh Bridges: Enhancing Accuracy Through Extended Measurement

Multi-idler weigh bridges increase the time material spends on the scale, enhancing measurement accuracy.
The configuration of multiple idlers provides a more stable platform, reducing the impact of external influences and improving data quality.
This extended and stable measurement directly contributes to higher precision in weight calculations. Additionally, this method ensures compliance with actual content regulations by minimizing the risk of weight discrepancies in industrial applications.
Time-on-Scale Impact
As material handling systems evolve, the significance of time-on-scale impact becomes increasingly apparent, particularly in the context of multi-idler weigh bridges. Time adjustments and measurement techniques are critical for enhancing the accuracy of weight measurements.
- Retention Time Extension: Expanding the weighbridge with multiple idlers increases the duration material remains on the scale, allowing for more precise data acquisition.
- Enhanced Data Sampling: Longer retention times facilitate the collection of a greater number of measurements, contributing to a more representative analysis of the material load.
- Accuracy Optimization: By adjusting the time material spends on the scale through multi-idler configurations, systems can achieve higher accuracy standards, crucial for high-speed or precision-dependent applications.
The direct relationship between weighbridge length and measurement precision underscores the importance of time-on-scale impact in the development of advanced belt scale loadcells.
Idler Configuration Benefits
While single-idler scales offer a basic level of accuracy in weight measurement, multi-idler weigh bridges significantly enhance precision by extending the duration of measurement.
This extended measurement period, facilitated by the increased number of idlers, allows for the gathering of more data points, which in turn helps to average out variations in material loading. The accuracy of weight measurements generally improves with each additional weigh idler incorporated into the system.
Proper idler spacing and alignment are crucial; misalignment, particularly between the last conveyor idler and the first weighbridge idler, can significantly impact accuracy.
Ensuring equal spacing between idlers minimizes belt sag and maintains optimal belt tension, thereby reducing potential weighing errors.
Parallelogram-Style Load Cells: Siemens Milltronics’ Approach to High Accuracy
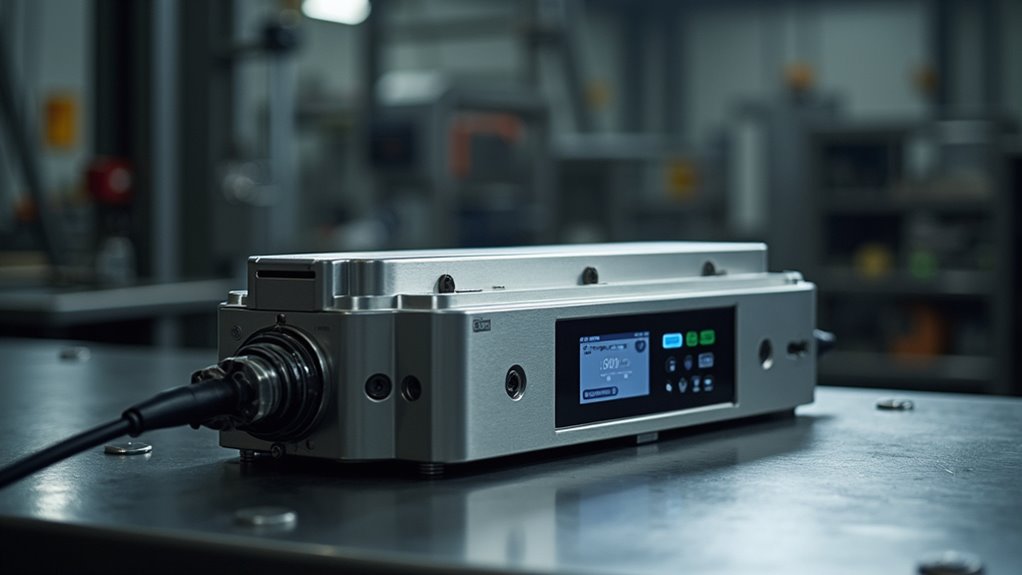
Parallelogram-style load cells, as developed by Siemens Milltronics, represent a significant advancement in high-accuracy weight measurement for belt scales. Their patented design effectively isolates vertical forces, ignoring horizontal forces such as belt tension and friction, which is crucial for maintaining accuracy in dynamic loading environments.
- Design Innovation: The unique geometry of the parallelogram ensures that only the vertical component of force is measured, enhancing precision.
- Material Integrity: Constructed from robust stainless steel, these load cells offer durability and corrosion resistance, suitable for harsh industrial settings.
- System Integration: When paired with advanced integrators like the Milltronics BW500, these load cells facilitate precise calibration and load cell balancing, further enhancing measurement accuracy.
This approach to load cell design and calibration underscores Siemens Milltronics’ commitment to providing reliable and high-precision weight measurement solutions in conveyor belt scale applications.
Force Measurement Suspension Systems: Thayer’s Solution to Error Isolation
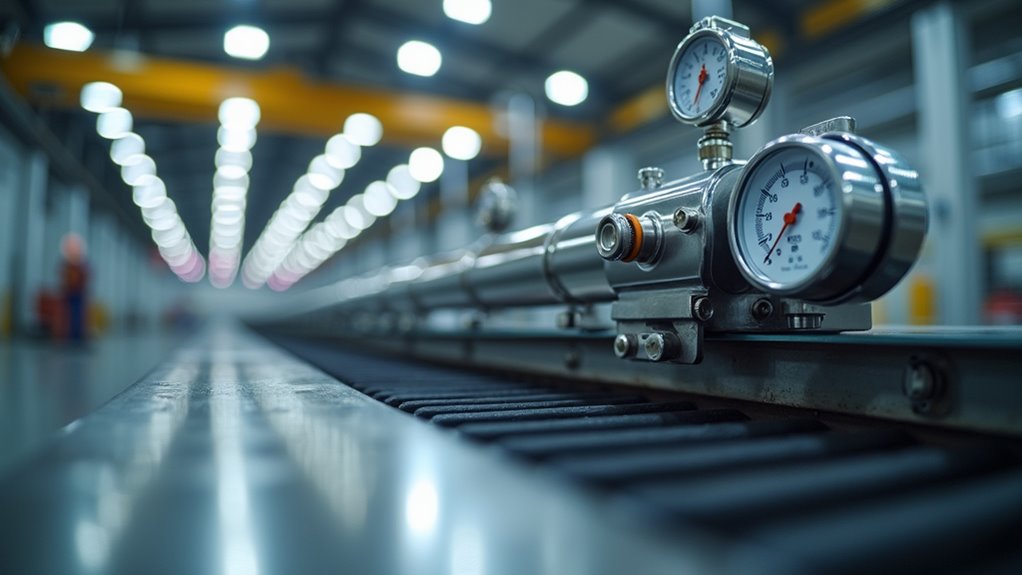
Thayer Scale’s force measurement suspension systems offer a sophisticated approach to error isolation in belt scale load cell measurements by effectively filtering out undesirable forces through a combination of mechanical design principles.
These systems function as force filters, discriminating between net load forces and extraneous forces. Utilizing force discrimination techniques and vibration filtering methods, they counteract horizontal force vectors and isolate vertical load forces.
The design includes mass counterbalancing to enhance signal clarity and patented “Rocking Flexure” suspension to minimize rotational hysteresis. This ensures immunity to external variances and structural shifts, providing a stable and precise measurement of material weight, thus enhancing the overall accuracy of weight measurements in industrial applications.
Temperature-Compensated Load Cells: Ensuring Stability Across Environments
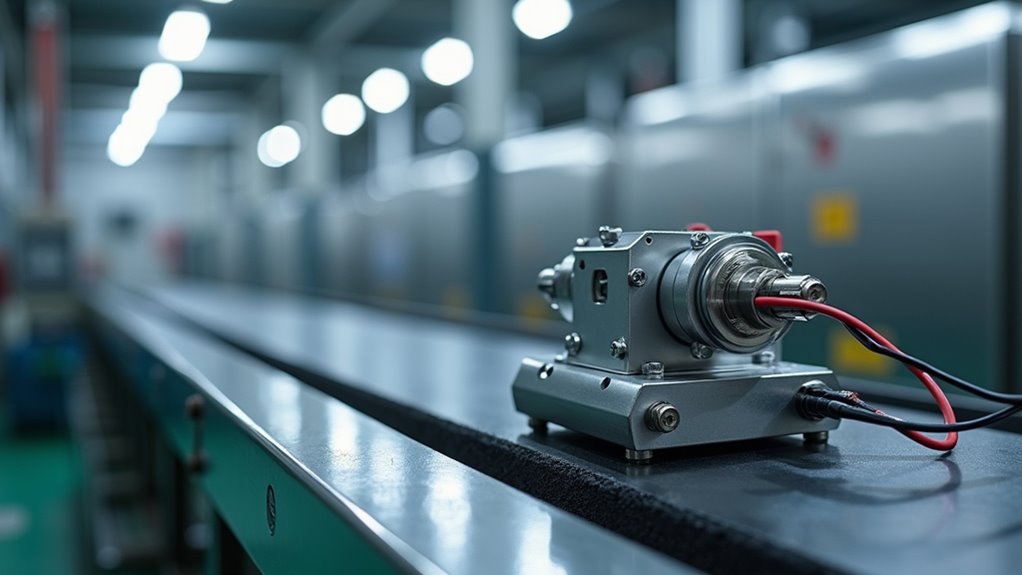
Moving beyond the intricacies of force measurement suspension systems, we enter the realm of temperature-compensated load cells, a critical aspect ensuring measurement stability across diverse environments.
Temperature fluctuations induce changes in load cell materials, leading to measurement errors such as zero drift and sensitivity drift. To mitigate these errors and ensure temperature stability, the following strategies are employed:
- Utilizing materials with low thermal expansion coefficients
- Incorporating temperature compensation circuits within the load cell
- Implementing software algorithms to adjust readings based on temperature variations