Conveyor belt scale systems continuously measure the weight and speed of materials on a conveyor to determine flow rate and total weight. They consist of a weighing frame, load cells, and a speed sensor. Load cells convert material weight into electrical signals, while the speed sensor measures conveyor speed. An integrator processes these signals to calculate flow rate and total weight. Various configurations, such as single or multi-idler scales, cater to specific application needs, enhancing operational efficiency and quality control.
Key Points to Remember
- Conveyor belt scales measure material weight and flow speed on conveyors to enhance operational efficiency and quality control.
- Load cells convert mechanical force into electrical signals, processed alongside conveyor speed data to calculate material flow and total weight.
- Speed sensors accurately measure conveyor speed, essential for precise flow rate and total weight measurements.
- The integrator processes signals from load cells and speed sensors to provide real-time data on material flow rate and total weight.
- Accurate calibration and minimization of external influences are critical for ensuring system accuracy and reliability.
Main Components of Belt Scale System
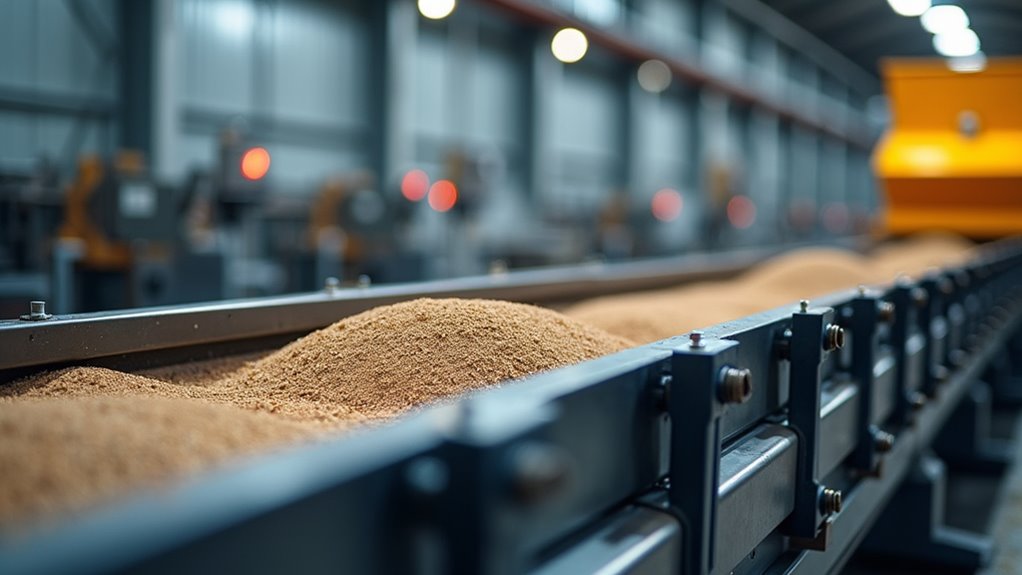
The core components of a conveyor belt scale system are designed to accurately measure the weight of materials as they are transported on a conveyor.
At the heart of the system is the weighing frame, available in configurations such as single, dual, or multi-idler setups to suit various application needs. These frames are built to support idlers and ensure accurate weight transfer to load cells, utilizing advanced strain gauge sensor technology. Load cells play a critical role in converting the force from the material into electrical signals, essential for system accuracy. Collectively, these components form the foundation of a precise and reliable conveyor belt scale system.
Essential for real-time monitoring, the controller/display processes these signals, providing instant data on weight and flow rate, crucial for operational efficiency and quality control.
Weight Measurement Process
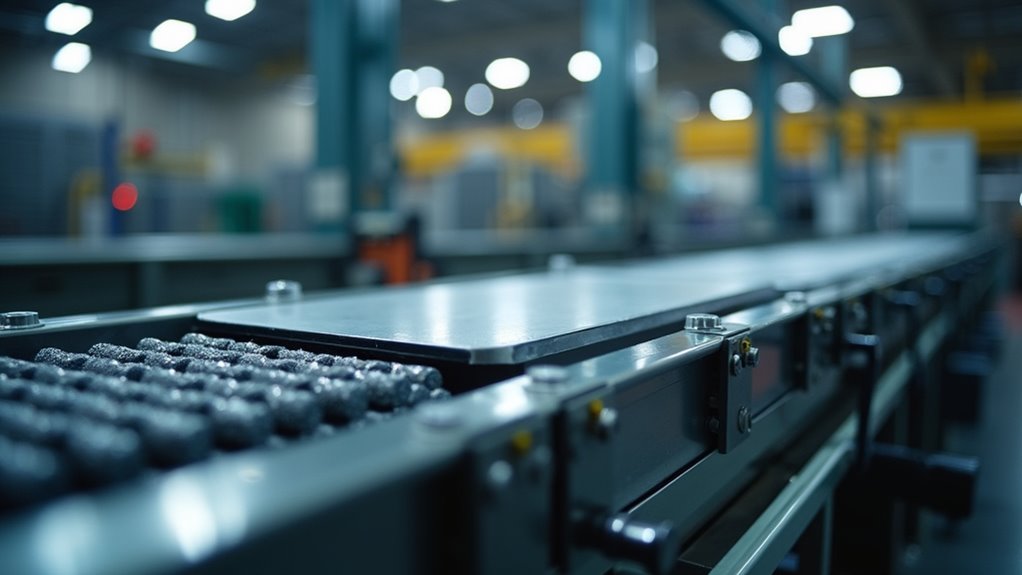
Understanding the core components of a conveyor belt scale system is foundational to grasping its intricate weight measurement process.
Central to this process are the load cells, which act as transducers, converting mechanical force from the material on the conveyor into electrical signals. These signals, proportional to the material’s weight, are transmitted to an integrator.
The integrator processes these electrical signals alongside conveyor speed data, calculating the material flow rate and total weight over time. System accuracy depends on precise calibration and minimizing external influences such as belt tension and environmental conditions, ensuring reliable weight measurements. This process is critical for maintaining compliance with regulatory standards and ensuring product quality across industries.
Role of Speed Sensor
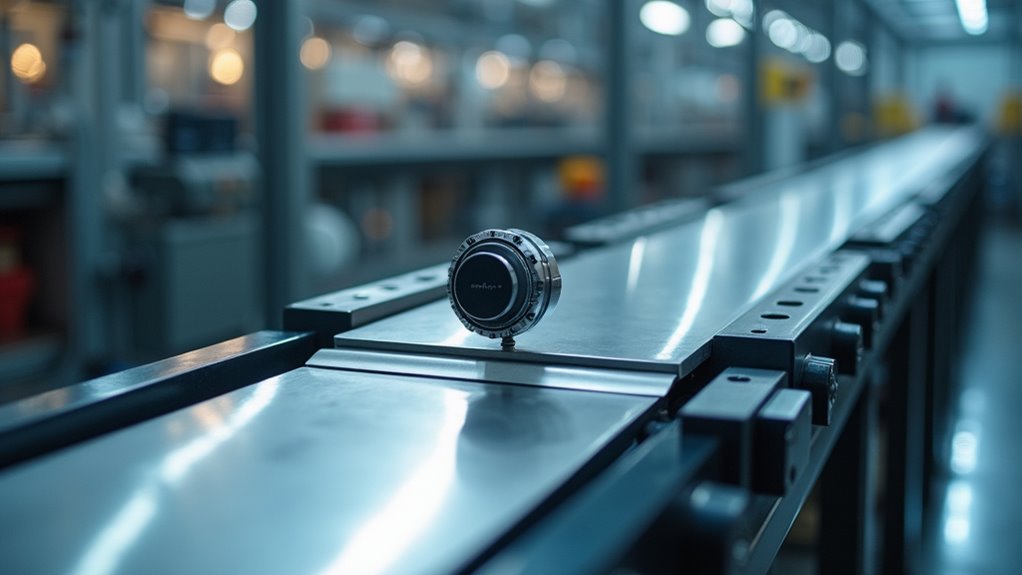
A central element in the operation of a conveyor belt scale system is the speed sensor, a critical component responsible for accurately measuring the conveyor’s speed. The speed sensor’s function is indispensable for ensuring high precision in measuring material flow rate and total mass. It generates signals proportional to the conveyor’s speed, which an integrator uses to calculate flow rate. High-performance systems can handle up to 250 products per minute, maintaining accuracy within ±0.1g, even at high outputs.
Speed Sensor Type | Installation Location |
---|---|
Tachometer/Encoder | Tail Pulley |
Wheel-Driven Sensor | Bend Pulley |
Proximity Sensor | Dedicated Speed Wheel |
Internal Sensor Design | Within Measuring Roller |
Accuracy is affected by factors like belt tension, material buildup, and vibrations, making proper installation and maintenance essential for reliable performance. Additionally, real-time measurement ensures discrepancies can be detected and addressed promptly, contributing to overall operational efficiency.
Integration and Calculation Functions
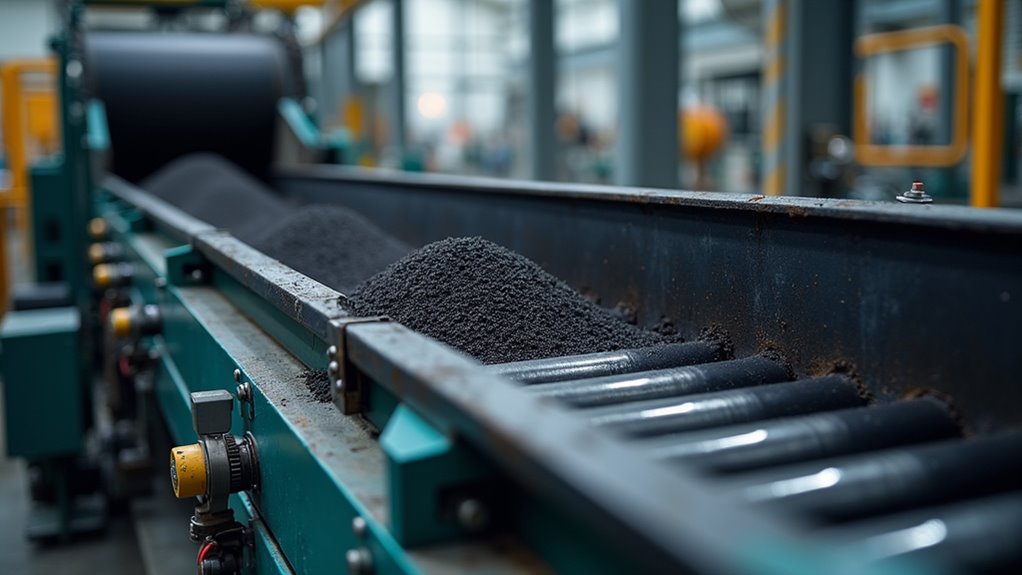
Integral to the operation of a conveyor belt scale system, alongside the speed sensor, is the integrator, a component responsible for processing signals from both the load cells and speed sensor to calculate material flow rate and total mass.
The integrator performs several key functions:
- Signal Processing: Converts electrical signals from load cells and speed sensors into usable data.
- Preliminary Calculation: Determines material flow rate using the formula: Flow Rate = Belt Load × Belt Speed.
- Total Mass: Continuously integrates flow rate over time to calculate total weight.
- Calibration and Accuracy: Manages zero and span calibration for precise measurements.
- Output Generation: Provides data display and outputs for control systems.
The integrator’s accurate signal processing and calibration precision are critical for reliable and accurate material weighing on conveyors.
Types and Configurations of Belt Scales
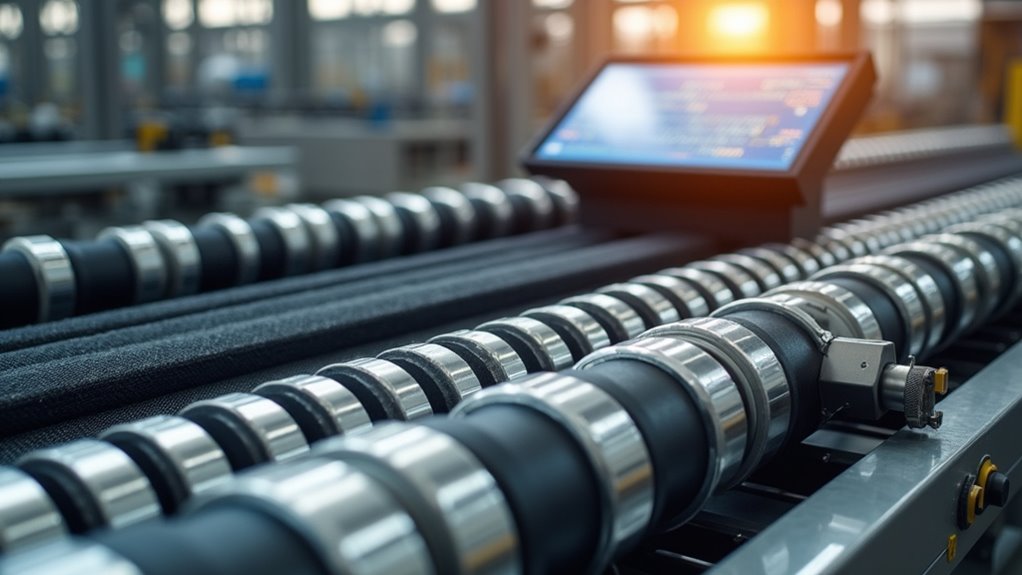
Conveyor belt scales, critical components in material handling systems, come in various types and configurations to suit diverse industrial applications. The choice between single-idler and multi-idler scales is primarily determined by accuracy requirements and application selection.
Single-idler scales, while cost-effective, offer lower accuracy suitable for less expensive products. In contrast, multi-idler scales, with longer weighing platforms, provide the high accuracy needed for high-value products and commercial applications.
Environmental factors also influence scale type selection, with multi-idler designs offering superior stability and adaptability. Specialized designs address specific needs, such as low-density materials or heavy-duty mining environments, showcasing the versatility of conveyor belt scale applications.