Ensure the accuracy of belt scale measurements by properly preparing the scale, performing zero and span calibration, and verifying accuracy through material testing. Regular maintenance and recalibration are critical for long-term reliability. Dive deeper to master the intricacies of effectively calibrating your belt scale.
Key Points
- Inspect and prepare the conveyor scale by cleaning, aligning, and ensuring proper operation before calibration.
- Perform daily zero calibration with an empty conveyor to establish a reliable baseline.
- Use certified weights for span calibration to ensure accurate measurements across the scale’s full range.
- Verify calibration accuracy through material testing and load simulation, comparing results with certified scales.
- Schedule regular maintenance and periodic calibration to maintain long-term accuracy and reliability.
Preparing Your Scale for Calibration
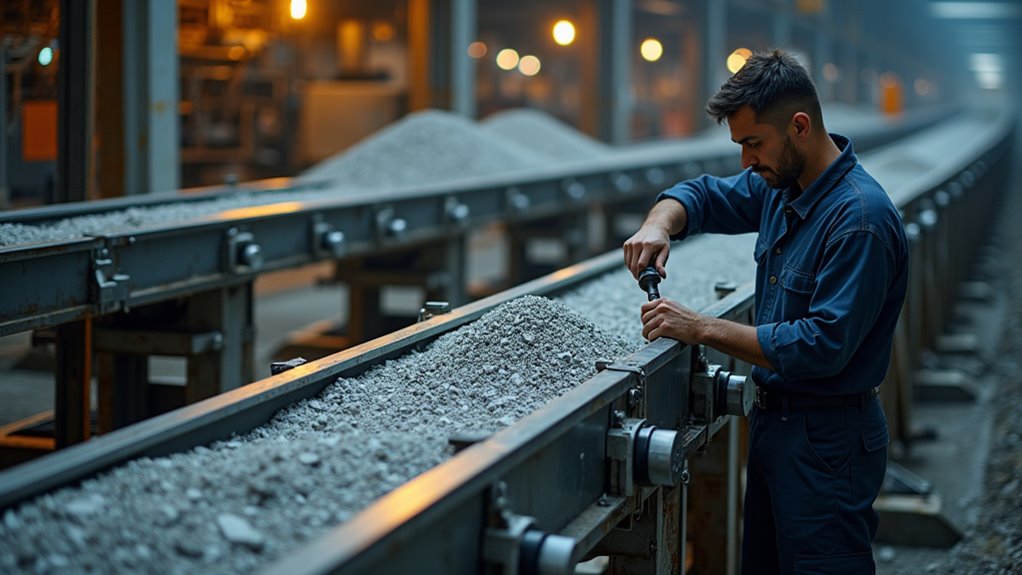
Before calibrating your belt scale, conduct a thorough inspection and cleaning process to ensure accuracy.
Begin with a comprehensive conveyor scale inspection, assessing belt wear, ensuring weigh idlers rotate freely, and adjusting scrapers and plows if necessary. High-speed handling ensures accuracy, which is critical during calibration.
Proper cleaning is essential; remove any debris or buildup from the speed sensor that could affect its readings.
Verify structural integrity and alignment, checking for obstructions under the frame and confirming that all mounting bolts are securely fastened.
This preparation phase includes ensuring operational readiness by running the conveyor empty for a warm-up period, typically 20-30 minutes, and verifying that the scale operates within its rated capacity to prevent inaccuracies during calibration.
Mass standards must be carefully selected and prepared, ensuring they are certified and in proper condition for accurate calibration.
Performing Zero Calibration
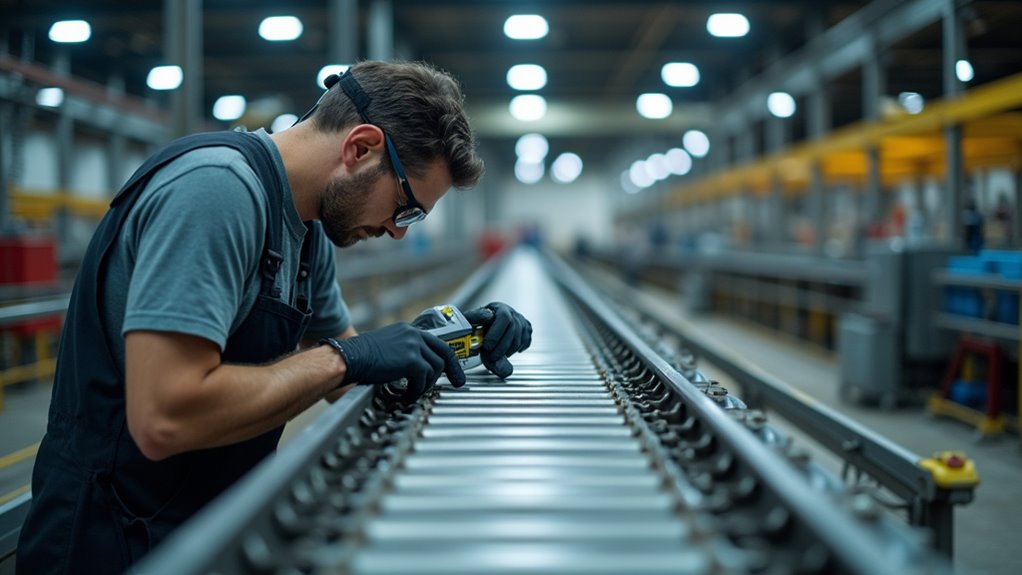
To establish an accurate baseline for precise weight measurement, zero calibration is performed on the belt scale, ensuring it reads zero when the conveyor is empty, thus accounting only for the material being transported. This process is critical to eliminating any residual load or drift that could affect the scale’s accuracy.
Zero calibration should be performed daily or even at the start of each shift to verify that load cells and indicators do not register weight on an empty scale. It is typically applied at the beginning of each shift in manufacturing plants to ensure correct settings before production starts.
Regular zero calibration is vital for maintaining reliable and consistent weight measurements throughout the belt scale’s operation.
Conducting Span Calibration
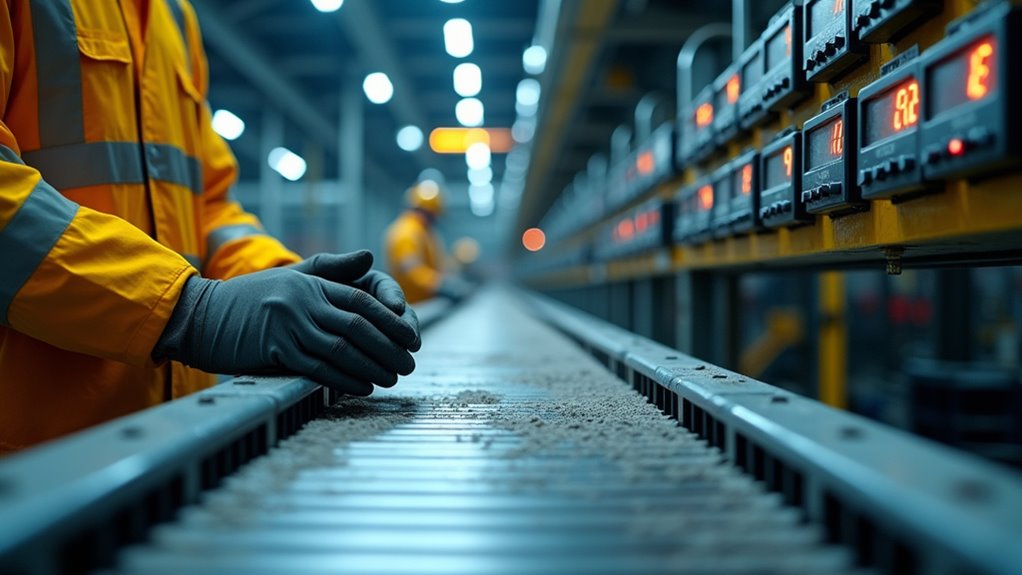
Performing span calibration on a belt scale is a critical process that ensures the scale accurately measures known weights across its full operating range. This involves using specific span calibration techniques and tools to adjust the scale’s response to a given weight.
Common techniques include static weight calibration, where certified weights are placed on the weighbridge, and test chain calibration, simulating a dynamic load using a weighted chain. Electronic and digital calibration provide less physically demanding alternatives, relying on load cell data and resetting default values.
Regardless of the method, span calibration is essential for maintaining the belt scale’s accuracy over time.
Verifying Calibration Accuracy
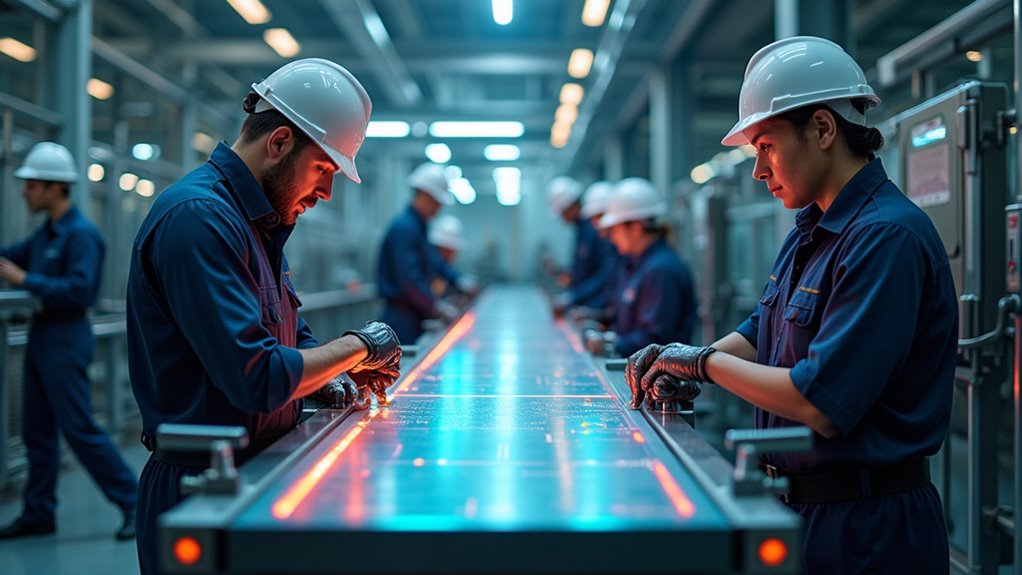
After completing span calibration, the next critical step in the calibration process is verifying the belt scale’s accuracy. This is done through material testing, which involves weighing a known quantity of material on a certified static scale and comparing the readings.
The sample should be substantial, ideally running for at least 10 minutes at 50% of the scale’s capacity. Simulated load tests, including static weights and test chains, are used to monitor performance between material tests. These tests should be conducted within 12 hours of material testing to establish a correlation factor.
Accuracy is further ensured by maintaining proper idler alignment, belt tension, and structural integrity, while installing the scale away from vibration sources.
Regular Maintenance and Calibration Schedule
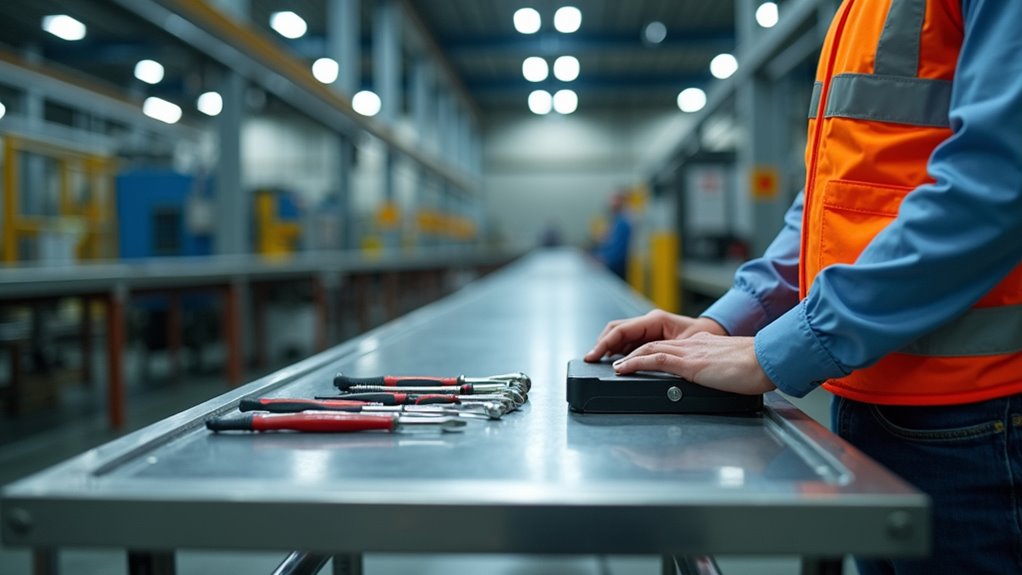
Regular maintenance and calibration are essential components for ensuring the ongoing accuracy and reliability of belt scales in material handling systems. The frequency of maintenance and the importance of inspections cannot be overstated, as they directly impact the performance and longevity of the equipment.
Adhering to a structured maintenance plan helps identify and address issues before they become significant problems. Key aspects include:
- Daily zero tests to monitor repeatability.
- Weekly or daily zero calibration, especially after initial installation.
- Monthly span calibration to maintain accuracy.
- Post-maintenance calibration following any work on the conveyor system.
This rigorous approach ensures the belt scale remains within operational limits, guaranteeing consistent and accurate measurements.