- Select an Appropriate Location: The belt scale should be installed on a straight and level section of the production line to ensure accuracy.
- Proper Calibration: Before use, ensure the belt scale is properly calibrated to guarantee accurate measurement results.
- Check System Integrity: Inspect the belt scale components such as the belt, idlers, and sensors to ensure they function correctly and are free from damage.
- Connect to Control Systems: Integrate the belt scale with the control system to ensure seamless operation.
Installing a belt scale requires selecting an optimal location away from feed points and discharge chutes to ensure accurate weight measurements. The conveyor frame must be rigid, with high-quality load cells installed and idlers properly aligned. Proper belt condition and tension are critical, with the scale positioned near the tail end. Environmental factors such as temperature and wind must be considered, and regular calibration and testing are essential. Exploring these tips further reveals the nuances of achieving precise belt scale operation.
Key Takeaways
- Select an optimal location away from feed points and discharge chutes for accurate weight measurements.
- Ensure structural integrity with a rigid frame, high-quality load cells, and proper idler alignment.
- Maintain proper belt condition and tension for accurate belt scale systems.
- Consider environmental factors and isolate vibrations to protect the system from external influences.
- Perform regular calibration and testing to prevent financial losses, production inefficiencies, and safety risks.
Selecting an Optimal Location
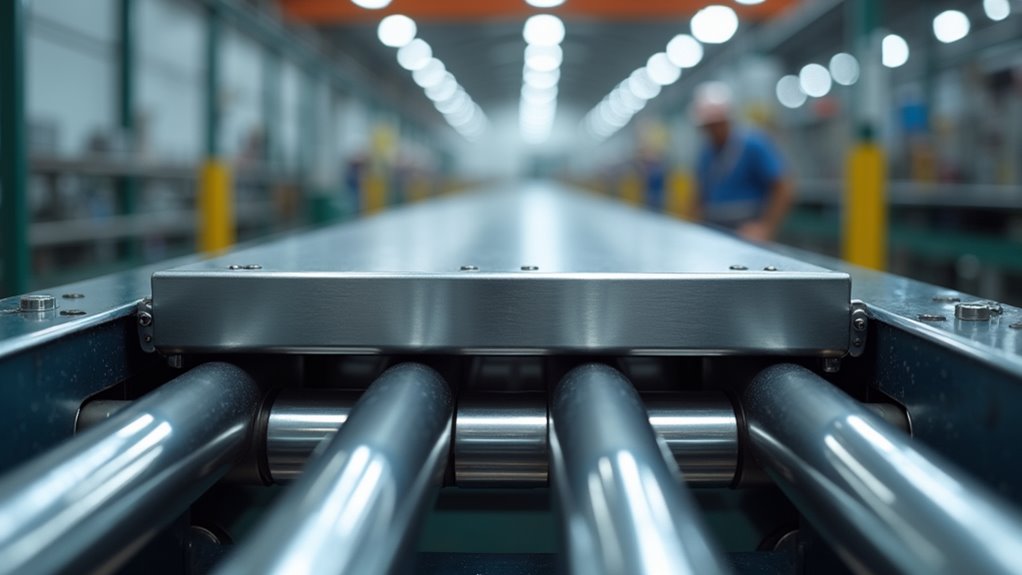
When selecting an optimal location for belt scale installation, it is critical to consider the distance from the feed point to ensure accurate weight measurements.
Avoiding installation near hopper discharge areas is essential to reduce the risk of inaccurate readings due to material turbulence, which can adversely affect scale performance.
A general guideline is to position the scale at a distance of 4 to 5 times the conveyor belt width from the feed section, where the material has fully stabilized on the belt.
Additionally, the scale should be placed at least one to two idler spaces away from the material disturbance stop point to avoid installation challenges that could impact measurement accuracy.
Sloped areas and grade changes should be avoided to maintain measurement accuracy, as they can cause shifts in material flow and weight distribution on the conveyor.
Ensuring Structural and Component Integrity
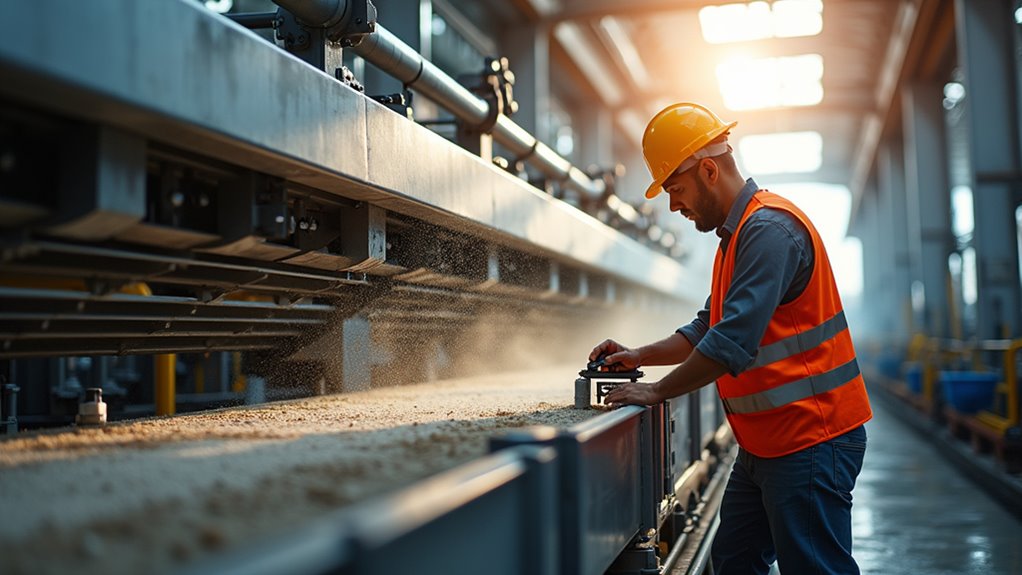
After determining the optimal location for installing the belt scale, the next critical step is ensuring the structural and component integrity of the conveyor system.
The conveyor frame must be rigid and isolated from external forces to prevent deflection that could affect accuracy. Installing high-quality weighing idlers in the weighing area, ensuring they are of the same type and properly aligned using methods like string testing, is essential to maintain a straight conveyor path.
Regular maintenance of load cells is crucial to protect these sensitive components from damage, particularly during welding. Additionally, inspecting speed sensors and maintaining the gravity take-up area ensures consistent and accurate weight data transmission.
Maintaining Proper Belt Condition and Tension
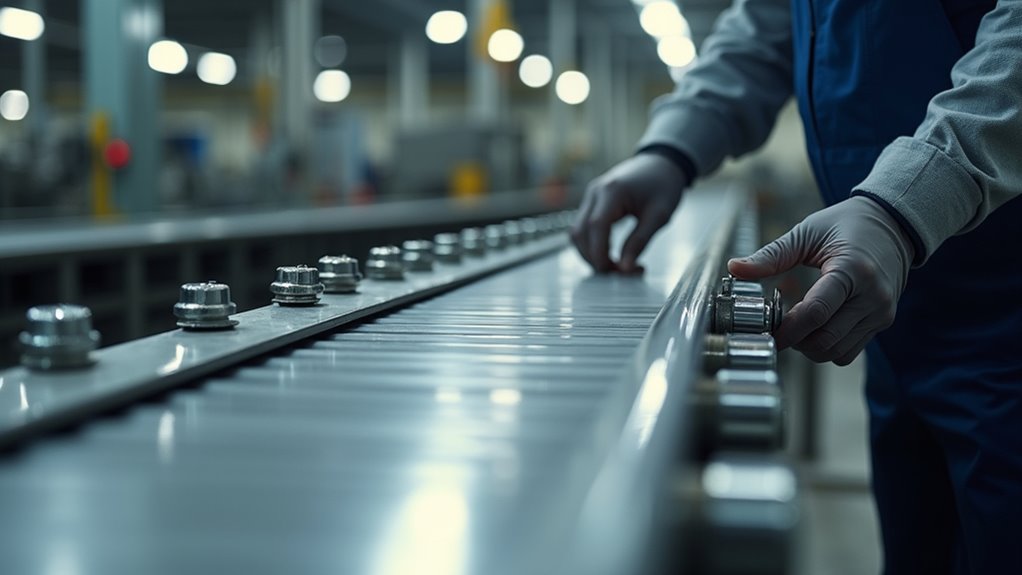
Belt condition and tension are critical factors in ensuring the accuracy of the belt scale system. The belt must have sufficient flexibility to maintain proper contact with all idlers, as an overly stiff belt may lift off the idlers, hindering accurate zero and span calibration.
Variations in belt tension, influenced by factors such as material weight, belt speed, conveyor length, and lift height, must be minimized. Positioning the scale near the tail end, where tension variation is lowest, and using a gravity tension system to maintain consistent, uniform tension are recommended practices.
Maintaining optimal belt condition and stable tension is essential for accurate weight measurements and overall system performance.
Considering Environmental and External Factors
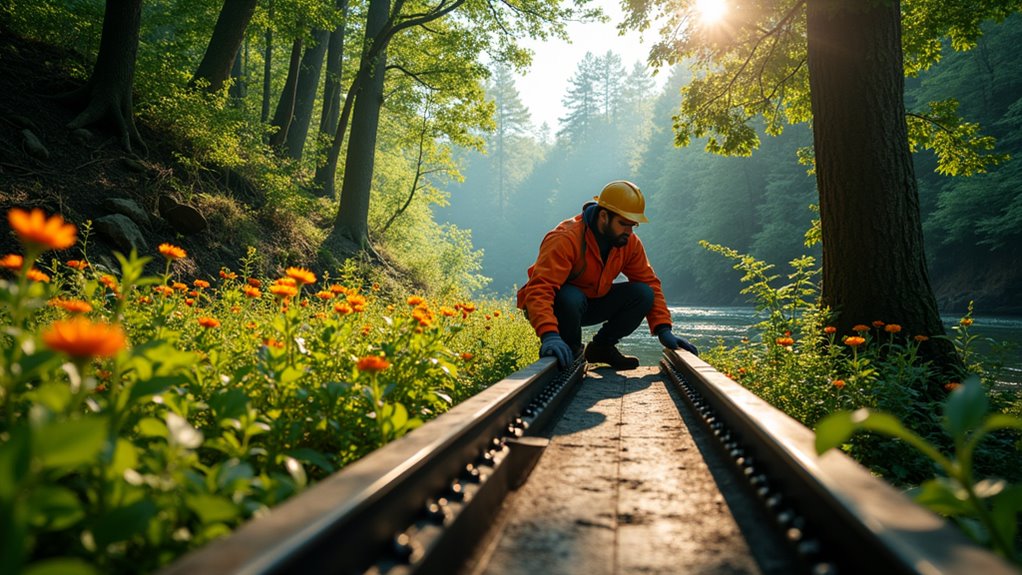
Beyond the critical aspects of maintaining proper belt condition and tension, addressing environmental and external factors is essential to achieving optimal belt scale system performance and accuracy.
Installations exposed to temperature variations require temperature-stable strain gauge load cells and can benefit from temperature sensors for real-time data integration.
Addressing temperature variations with stable strain gauge load cells and integrating real-time data from temperature sensors for installations exposed to varying conditions.
Windshields or protective enclosures safeguard against weather influences. Vibration isolation is critical, including mounting scales near support structures and using rubber or neoprene mounts for integrators, especially in mobile applications.
Regular cleaning and belt scrapers minimize the impact of dust and debris on scale accuracy.
Performing Regular Calibration and Testing
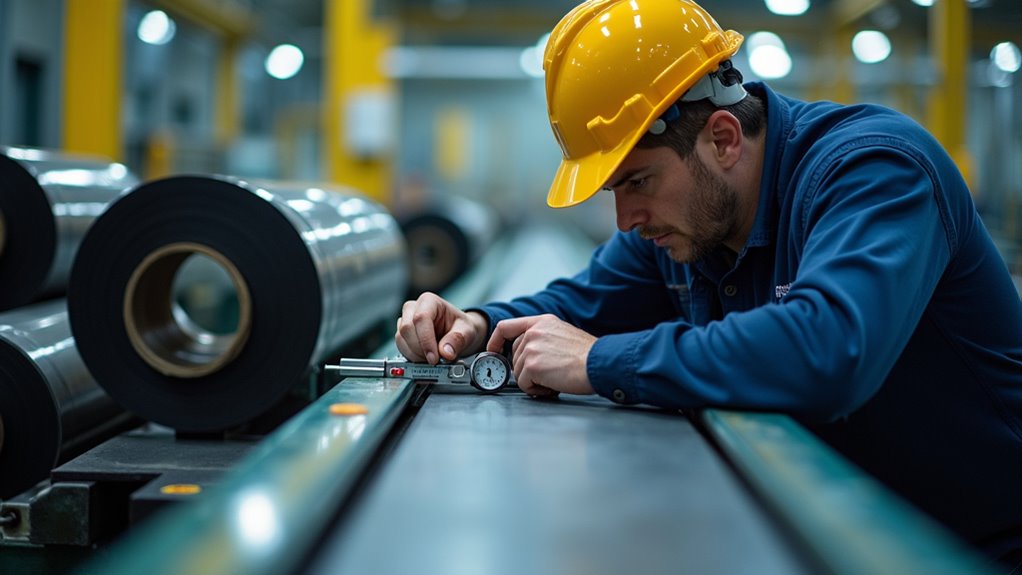
While the initial installation and setup of the belt scale system are critical, ongoing calibration and testing processes are equally vital to ensuring sustained accuracy and performance.
Calibration adjusts the scale system to address deviations, including zero and span calibration to maintain accuracy. Daily zero calibration, performed by running the conveyor empty, is recommended, with an emphasis on achieving a stable, operational zero through consecutive tests.
Regular calibration is essential to prevent financial losses, production inefficiencies, and safety risks. Testing methods and calibration frequency should be tailored to the conveyor system’s specific operational requirements, considering any mechanical changes that may affect scale performance.